悬架设计之对标开发初期
悬架对标开发有很多方面,包括K&C测试,主观评测,客观测量,数据制作,其中数据制作又分为系统数据制作和零部件数据制作,本文先说一些数据制作方面的内容和注意事项。
数据 制作主要是通过扫描仪器将悬架系统和零部件通过逆向扫描, 建立点云,然后在输入CAD软件进行点云处理。下图是通过点云扫描对某车型的经固件进行逆向,可以看出生成的CAD曲面和点云的误差非常小,一般的制作保持在0.1mm一下都可以接受的。
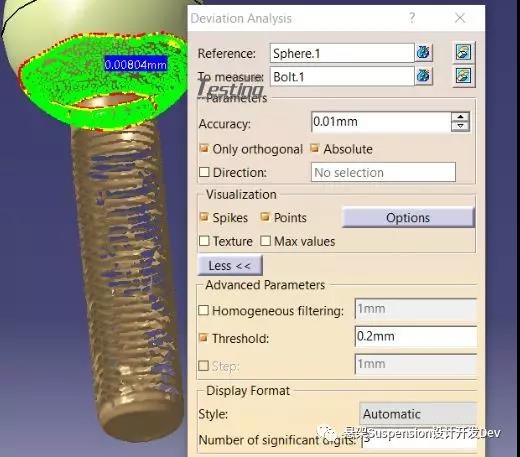
系统数据制作:
系统数据制作主要是用于研究和记录悬架系统方面的问题。一辆标杆车在拆(xi)解(sheng)前,都需要规划好, 这样才会事半功倍。
拆解前主要考虑和记录如下问题:
1,姿态问题
a,)是否需要扫描满载姿态
b,)是否需要扫描空载姿态
c,)是否需要扫描设计姿态
d,)别的系统是否还有特殊需求?
一般空载姿态肯定扫描,用于考虑整车造型等问题。然后就是考虑设计姿态的扫描,因为设计姿态不同的主机厂会有不同的考虑,如果2up状态(仅前排两个人),3up状态(前排两个人,后排一个(此人做中间or坐标or右边?)),还有4up状态的 。满载状态就是车辆满负荷状态。
以上描述省略了如下假设:
1,油箱状态,90%还是满油?
2,行李重量
以上只讨论五座的SUV和轿车,对于大型SUV和MPV不在以上考虑范围。
姿态扫描除了用于确认悬架位置,对于后期悬架硬点的校核和确认也起到非常重要的作用。原因主要在于如下:
1,后期零部件模型逆向过程会有误差,尤其是衬套,弹簧等性能件误差很大。
2,零部件误差导致后期悬架系统模型装配时误差。
3,由于CAD软件中不考虑衬套等的变形,所以CAD软件中的模型和实际车辆的姿态位置也会有很大误差。
4,姿态扫描过程,可以通过对部分或许多零部件特征进行捕捉,这部分特征也可以用于悬架硬点的提取的校核。
比较有意思的就是球销球心点的提取了,比如麦弗逊悬架摆臂球销球心,可以通过扫描球销轴和球销基座,然后通过拟合两个零部件的轴线进行计算球心。
此种方法也可以用于零部件的球心位置拟合。
零部件数据制作
零部件数据制作主要用于后期图纸的制作,释放给供应商进行开模和零部件尺寸精度管控。在进行零部件逆向时需要考虑以下问题
1,零部件的配合尺寸
2,零部件的连接关系
3,零部件主要特征尺寸
4,零部件逆向精度
5,子系统逆向需求
等
一般零部件在逆向时,由于工作量大,会有几个甚至十几个CAD工程师进行逆向,如果配合尺寸没有整理清楚,就会有配合零件配合尺寸不匹配的问题,如开档与对手件之间的问题,解决方法就是需要有经验的系统工程师进行判定。零部件的连接关系如果不对也会出现后期一系列零部件制作问题。如焊缝位置和长度,由于CAD工程师对产品了解较少, 此方面也需要产品工程师进行协助。零部件主要特征尺寸说起来比较抽象,比如制动卡钳两个安装孔之间的距离,三代轴承内外法兰面之间的距离等,一般都会取整。零部件逆向精度自不用说,结构件0.1mm以内是肯定的,性能件会放松要求,因为刚度低,易变型。有些子系统也有逆向需求,如角膜块系统,减震器系统,前桥模块系统。
以上是关于系统逆向和零部件逆向的部分总结,这两者之前还有很多工作需要处理,如力矩测量记录,接口尺寸定义等。
- 下一篇:悬架开发初期之硬点确认
- 上一篇:通过悬架调校改善轮毂电机车辆的平顺性及操控性研究
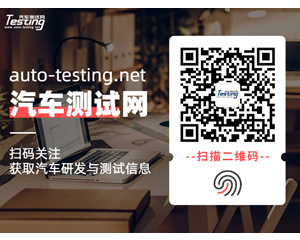
最新资讯
-
商用车及工程机械行业专场:NVH 及语音音频
2025-08-01 17:12
-
理想i8和重卡对撞测试引争议,东风柳汽发声
2025-08-01 15:52
-
艾德克斯IT-N2100 系列太阳能阵列模拟器
2025-08-01 15:43
-
ITECH重磅发布IT2705直流电源分析仪,重构
2025-08-01 15:34
-
现代汽车新一代混合动力系统:以技术革新引
2025-08-01 15:32