基于VPG的某商用车载荷谱研究
本文转自数字仿真论坛
基于VPG的某商用车载荷谱研究
崔震,张克强,聂梦龙,王乾勋
(浙江飞碟汽车制造有限公司五征分公司,山东 日照 276800)
【摘要】以某商用车为研究对象,采用特征线模型缩聚技术,建立整车刚柔耦合模型,大幅提升整车多体模型的计算效率。基于虚拟试验场技术仿真分析得到虚拟载荷数据,同时对样车进行实际耐久试验场测试,获取测试载荷谱数据用于仿真模型的修正和精度对标。基于损伤一致原则,将仿真载荷向测试载荷等效迭代,得到路面等效系数,从而保证基于虚拟载荷谱的结构疲劳性能分析与实际失效模式的一致性,为商用车从零部件到整车级疲劳耐久分析、减少试验中的可靠性问题、缩短研发时间、降低研发成本打下基础。
【关键词】商用车,VPG,刚柔耦合,等效迭代
引言
在汽车开发过程的性能预测中,零部件直至整车的疲劳耐久性能预测分析十分重要,避免或者减少在可靠性试验中出现零部件疲劳损坏,从而可以有效降低研发成本、缩短研发周期。进行疲劳耐久分析的基础是首先获取结构的载荷历程数据,传统的获取方法是试验场采集,包括车辆拆解、安装传感器、装车发车、试验场路试及数据处理等,获得载荷谱。采集过程耗时长且对数采设备精度要求高,如果前期载荷通道规划不合理、通道有遗漏,就必须重复上述过程。尤其对于商用车载重大、路况复杂安全隐患多等,增加了载荷谱采集的难度。并且载荷谱采集必须在物理样车上进行,这就延长了车型的研发周期,降低了高效响应市场需求的能力。
基于虚拟路面和整车多体动力学模型的联合仿真可以预测虚拟试验场环境下的整车载荷,这一技术称为虚拟试验场技术,即Virtual Proving Ground,简称为VPG[1,2],目前在乘用车方面应用居多,而商用车载荷工况复杂应用较少。
基于VPG技术,将商用车载荷谱获取的方式从基于实车测量转到基于虚拟试验场的仿真计算,为零部件、子系统到整车前期开发设计阶段的疲劳分析提供信号输入,在研发前期实现开展商用车结构疲劳耐久分析[3]。解决测试耗时费力和关键位置难以测量的缺点,通过疲劳损伤等效方法得到的载荷谱在应用于虚拟计算中得到的疲劳性能与试验保持一致,能够更准确的预测汽车及其零部件的疲劳性能。为企业快速研发高质量、高可靠性产品,快速抢占市场提供了关键的技术基础。
1整车多体动力学建模
1.1 整车参数介绍
所研究的某商用车整车及悬架相关设计参数如表1所示。前、后悬架均为钢板弹簧,整备质量3.15吨,设计满载质量5吨。
表1 整车基本参数
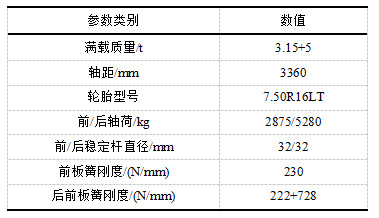
1.2 刚柔耦合模型
在大量的模型对标工作中发现,柔性体能够更好的反应真实测试数据[4]。因此,首先建立整车刚柔耦合模型,柔性体包括车架、前后桥、转向节,如图1所示。柔性体的生成在有限元软件Hypermesh中利用特征线法缩减技术,相比传统方法,柔性文件缩小近十倍,使仿真效率得到大幅提升。柔性体车架模型如图2所示。
轮胎采用完全非线性的FTire模型,其频率可达120~150Hz,对于轮胎的稳态性能具有足够的精度[5]。
板簧采用三连杆模型建模方法,根据空满载簧上质量、弧高及载荷变化等,调整板簧刚度曲线在整个弧高变化过程(自由状态-空载-拐点-满载-压平状态)与理论设计要求一致。仿真与理论刚度曲线如图3所示。
载重信息通过简化模型测算获得。首先根据平板货箱尺寸利用CAD软件建立六面体实体模型,然后通过实体体积和载重 (包括货箱) 质量计算出密度并赋予实体模型。测量出惯量信息,结果如表2所示,载重 (包括货箱) 采用集中质量模拟,赋予质量及惯量信息,通过6个衬套与车架连接,并调整质心位置来匹配实车前、后轴荷。
其他部件包括驾驶室、动力总成、减振器、稳定杆及油箱等附件。
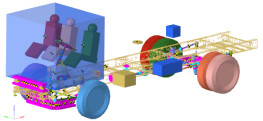
图1 整车刚柔耦合模型
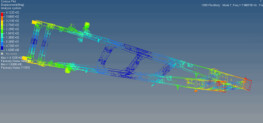
图2 柔性体车架
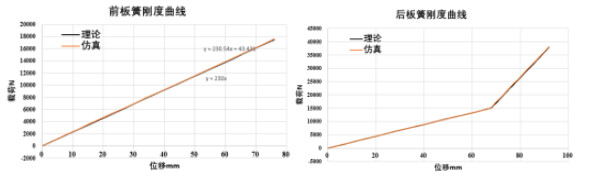
图3 前、后板簧刚度调试
表2 载重参数
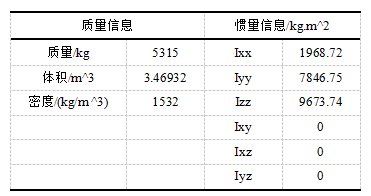
2 试验场载荷采集
对某试验场耐久坏路进行载荷采集,用以虚拟试验场仿真对标。试验场载荷采集按照如图4所示流程。
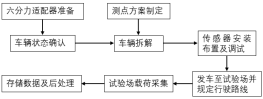
图4 试验场载荷采集流程图
2.1 载荷通道说明
本次测试的载荷通道包括轮心力、减振器位移、车架加速度等。还包括GPS通道,测量车速用以计算行驶路面长度。
用于信号采集的传感器有,六分力传感器,采集各路面条件下车轮部位承受的全部载荷;拉线位移传感器,测量路试过程减振器位移变化和车身悬置垂向位移变化;压电式加速度传感器,测量车架、轮心附近等位置的3方向加速度。如图5所示为测量减振器位移和轮心加速度的传感器布置图。

图5 减振器位移和轮心加速度测量
2.2 试验路面说明
试验场载荷采集路面如表3所示。
表3 试验路线
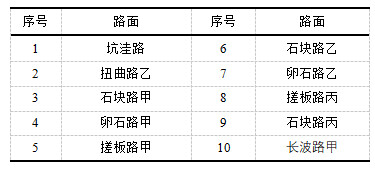
3 VPG仿真
进行虚拟试验场仿真分析,导入路面文件,设置车速与试验一致。依次运行10条与试验对应的虚拟路面。
3.1 路面长度确定
试验中由于驾驶等外界因素导致车速并非完全匀速,仿真中车速也会有偏差。因此,为了弥补车速导致的载荷差异,在对标过程中的原则是保证仿真与试验的行驶长度一致。
例如,对轮心力通道按照路面进行切分,排除过渡路,载荷按路面切分如图6所示;然后将GPS中的车速通道按照切分时间区间求积分,得到各路面行驶长度。
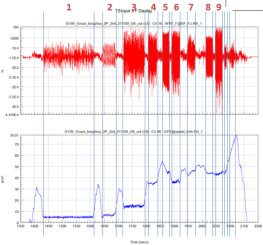
图6 载荷切分及长度计算
3.2 仿真载荷后处理
仿真载荷通道多,需要重复运行不同虚拟路面,载荷数据众多、处理耗时且繁琐。因此,借助编程工具可快速高效完成后处理工作。
在软件后处理界面一次性导出所有载荷通道数据,再借助编程工具对数据进行批量处理。得到与试验长度一致的各路面仿真数据,例如石块路乙的左前轮心力试验和仿真数据如图7所示。

图7 石块路乙左前轮心力试验和仿真数据
4 等效计算
在整车多体动力学模型的建立过程中,有些参数难以测试得到,例如衬套扭转刚度等,只能按照经验值;另外,虚拟路面扫描时由于精度问题或者实际路面损耗等,都可能造成仿真载荷与实际测量有偏差。
由于各种无法预测的因素可能导致仿真与试验载荷存在较大差异,而模型精度很难继续提升,或者需要花费巨大精力。为了解决此问题,提出一种载荷等效方法。
基于损伤一致原则利用遗传算法,将仿真各载荷通道矩阵向试验载荷矩阵优化,迭代计算路面等效系数,以此获得更接近实际的载荷谱。
4.1 通道筛选
仿真时整车上的任意位置都可设置载荷输出,而试验时由于空间限制,某些位置不方便布置传感器。所以,等效的通道筛选需要根据试验来确定。
筛选之前需要对载荷数据做漂移、偏置、毛刺和极性等检查处理。检查完成后对仿真和试验数据做初步的对比分析,包括幅值统计、雨流、损伤和PSD等,剔除信号异常或者差异较大的通道,卵石路的前轮心力载荷特征如图8所示。其中损伤为相关性分析的主要对象,其他载荷特征为辅助检测对象。筛选出的通道包括轮心力、轮心加速度、减振器位移、驾驶室悬置位移、悬置加速度、车架加速度和货箱加速度等,共计62个通道,如图10所示。
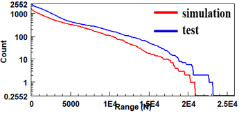
(a)雨流计数
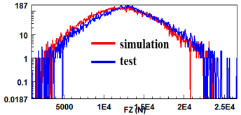
(b)幅值统计
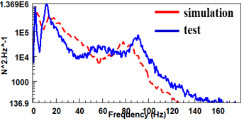
(c)PSD
图8 卵石路前轮心力载荷特征
4.2 伪损伤计算
伪损伤计算按照图9所示,其中设置SN曲线斜率为-3,截距为5000。仿真通道按照路面分别计算;试验通道按照合成路面计算。仿真损伤为的矩阵,试验损伤为的矩阵。
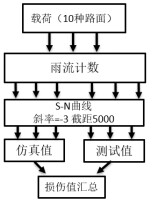
图9 伪损伤计算说明
4.3 多目标优化迭代
基于遗传算法的多目标优化原理,运用公式(1)计算等效系数,

式中,Xmn为仿真损伤矩阵即变量矩阵,Ym为试验损伤矩阵即目标矩阵,γn为路面等效系数矩阵即求解矩阵。
设置解为大于零的整数,经过迭代计算得到最优系数矩阵。等效后的仿真损伤之和与试验损伤的复现比为1.19,各通道的复现比均在1附近,如图10所示,说明等效结果能够很好的反映实测信号。
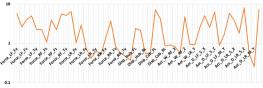
图10 各通道损伤复现比
将各路面的通道载荷在时域上乘以相对应的等效系数,然后按路面顺序串联输出仿真结果,等效串联后的左前轮心如图11所示。除了参与等效的通道外,其他通道载荷按照同样的等效系数输出,即可得到整车的所有通道载荷谱。
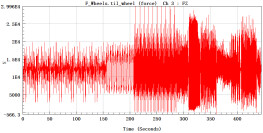
图11 等效后左前轮心力
5 结 论
基于VPG技术并运用柔性体缩减方法搭建商用车整车级刚柔耦合模型,使仿真计算效率大幅提升。通过虚拟载荷与试验载荷对比分析,优化提升模型精度,建立了商用车虚拟载荷获取能力,从而可以在商用车项目研发前期使用虚拟载荷谱进行各零部件、子系统、系统、整车级的疲劳性能预测分析。
基于损伤一致原则,运用遗传算法的多目标优化原理,对变量仿真载荷向目标试验载荷优化迭代,得到路面等效系数。建立了一种载荷等效方法,按照此等效方法可以获取整车所有位置的载荷谱,并且更接近实车测试值,为高精度的疲劳仿真分析建立了基础,进一步提升企业设计研发整车产品的可靠性和质量。
参考文献
[1] 陈宁. 基于VPG白噪声滤波模型在四轴车体系统驾驶室的平顺性研究[J]. 陕西科技大学学报, 2018, 36 (3): 138-145, 166.
[2] 张朝军. 基于VPG技术的整车强度工况BIP虚拟仿真[C]. 第十五届中国CAE工程分析技术年会论文集.
[3] 葛文韬. 基于实测道路谱的纯电动轻卡电池包支架动态载荷仿真及疲劳分析[J]. 振动与冲击, 2020, 9 (39): 267-273.
[4] 王登峰. 车架弹性对重型载货汽车行驶平顺性的影响[J]. 农业机械学报, 2010, 12 (41): 7-12.
[5] 严金霞. FTire模型的建立方法研究[J]. 汽车技术, 2011 (10): 13-16.
作者简介:宋磊(1992— ),男,山东日照人,硕士研究生,浙江飞碟汽车研究院CAE工程师。主要从事多体动力学方向,整车载荷分解等工作。
本文转自数字仿真论坛
- 下一篇:浅析最新自动驾驶视觉技术路线
- 上一篇:商用电动车用永磁同步电机电磁振动噪声削弱方法
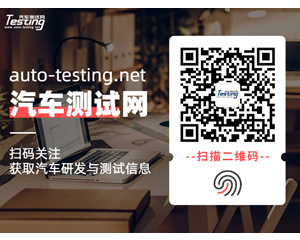
最新资讯
-
新一代扭矩测量 – T110/T100HBK - Hotting
2025-07-15 10:38
-
分布式自动化测试技术
2025-07-15 10:37
-
电动汽车高压连接器的接触电阻、保持力与插
2025-07-15 10:36
-
2025年中国汽车上半场落幕 车企都不好过
2025-07-15 10:36
-
首次开展多场景连续动态测试 | IVISTA中国
2025-07-14 14:44