整车行驶可靠性与室内道路模拟试验技术方法研究
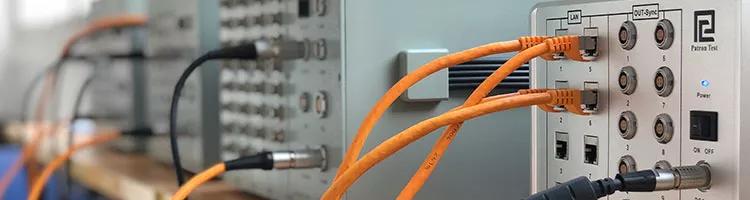
关键词:军用整车 可靠性 道路模拟 数据裁剪 路谱
引言
各种新车型从设计开发到稳定生产及整车改进都要经过各类型的试验,其中行驶可靠性试验是考核整车底盘及上装设备可靠性的关键试验,在相关的国标及国军标中均有相应规定[1-2]。各类汽车行驶可靠性考核一般是通过实际道路行驶试验或汽车试验场试验进行考核[3]。
道路行驶可靠性试验是将汽车按实际使用条件行驶至规定的里程,考核车辆行驶过程中底盘及上装设备的可靠性能。行驶试验对各种路面的里程、对炎热、寒冷和高原等地区的试验时间均有规定。由于是在实际外场路面行驶几千公里至上万公里,道路行驶试验会存在实际路面条件难以控制、环境条件复杂、试验周期长及保密性无法保证等问题[4]。汽车试验场是试验汽车的专用场地,由可进行平顺性、可靠性和耐久性试验的高速环形路、石块路、搓板路和其他典型路段组成,有坡道、弯道、尘灰室、盐水池、淋水室和试验涉水性能的水池以及试验转向特性用的圆形场地等。相比于道路试验,试车场试验可有效解决路面条件及保密性等问题。但对于专用特种军用车辆,需建设相应的试验场路面,投资巨大费用较高[5]。
室内道路模拟是一种重要的可靠性、耐久性试验方法,通过数字计算机技术和液压伺服技术能在实验室室内模拟复现车辆实际行驶时的振动环境,精确再现车辆行驶过程中各种运动状态及受载荷激励情况,可节省大量人力物力[6-7]。由于道路模拟试验在室内进行,能更好的进行保密控制,同时因道路模拟试验系统运行时重复性好,当试验车辆出现故障时,通过路谱重复运行,有利于故障复现与验证。目前国内军用整车及类似产品开发设计或改装,都是采用传统的道路试验方法,在开发的初期,没有时间和条件进行车辆及上装设备整车级的试验。上装设备电子元器件和电子设备作为设备进行过振动等环境可靠性测试,但系统集成为车载上装设备后,其可靠性工作环境与设备级振动环境不一致,导致每次道路试验时都会出现大量问题,严重制约了军用整车的进一步发展提升。
针对军用整车行驶可靠性存在的问题,本文采用一种以军用整车短时外场道路试验结合室内道路模拟试验对其行驶可靠性进行考核的方法。该方法通过先将军用整车在外场进行短时短距离的外场行驶试验,采集样车外场道路行驶时底盘结构及上装设备振动应变响应信号,对响应信号进行分析、压缩、裁剪以获得道路谱数据,再在道路模拟系统上通过对整车设备结构的损伤效果进行对比验证,验证该车型等效道路载荷谱,最终加载等效的道路载荷谱至道路模拟系统台架上对整车的行驶可靠性进行等效考核。
室内道路模拟系统的驱动动力有电动和液压两种类型,由于液压驱动式道路模拟系统推力大、费用低、性能优良,因此应用较电动式更为广泛[8]。本文军用整车试验用的道路模拟系统为液压式,如图1所示,主要由液压泵及驱动电机、液压油源、液压缸、电液伺服阀、数据采集及控制系统等设备组成。
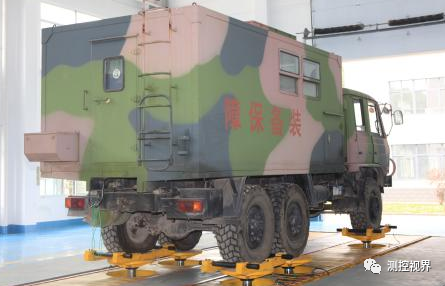
该道路模拟试验系统属于轮胎耦合式系统,总共六个作动器,单个作动器推力最大推力13吨,频率范围0.1-50Hz,振幅350mm,轴头最大垂向速度2m/s,路谱迭代精度(时域)优于5%。该系统可用于3轴及以下、最大整车重量12吨的通用型军用整车。
2、 路谱数据采集系统
路谱数据采集系统具体设备清单如表1所示,相应的整车道路模拟试验流程如图2所示。
表1 路谱数据采集系统设备清单
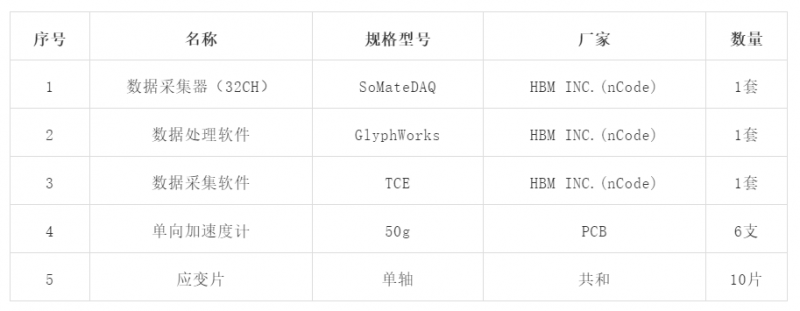
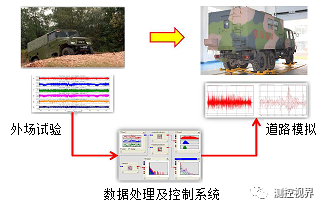
某军用整车外场试验场地跑道符合GJB219B附录D的规定,外场实物图如图3所示,该环形跑道一圈周长为约为0.8Km。在保证安全的前提下,按《XXX军用整车试验大纲的要求》以30Km/h左右车速行驶,完成数据采集。试验时,样车要稳住车速,然后匀速驶过试验路段,记录各加速度传感器及应力应变信号。
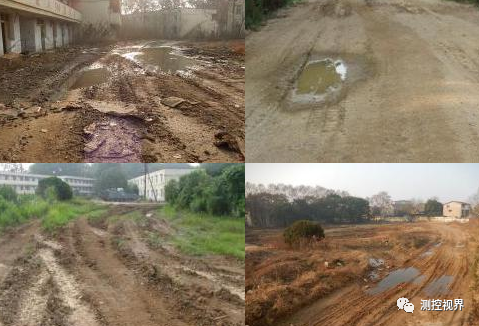
2、路谱采集
根据外场行驶试验时样车结构及上装设备特性,采集16通道原始信号,其中10通道应变监测底盘关键部位,4通道轴头加速度信号,2通道上装设备加速度信号,其中某振动和某应变测点如图4所示。
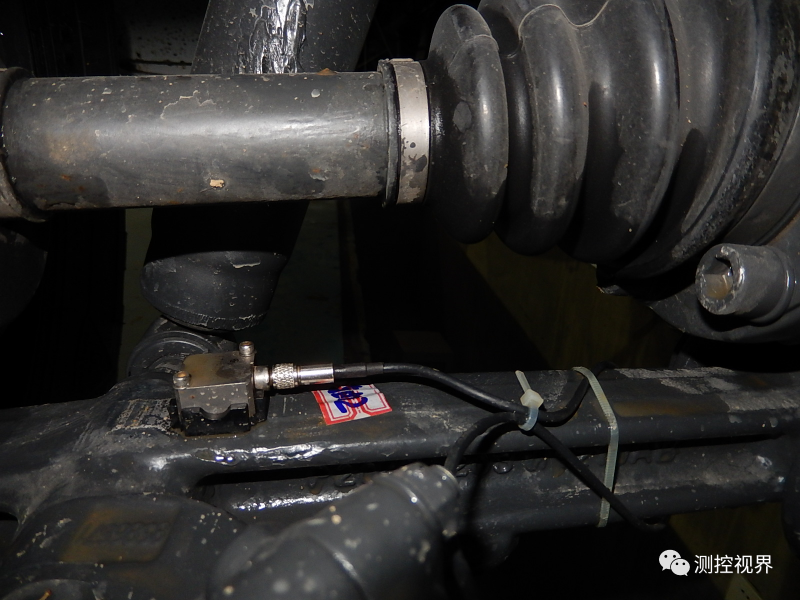
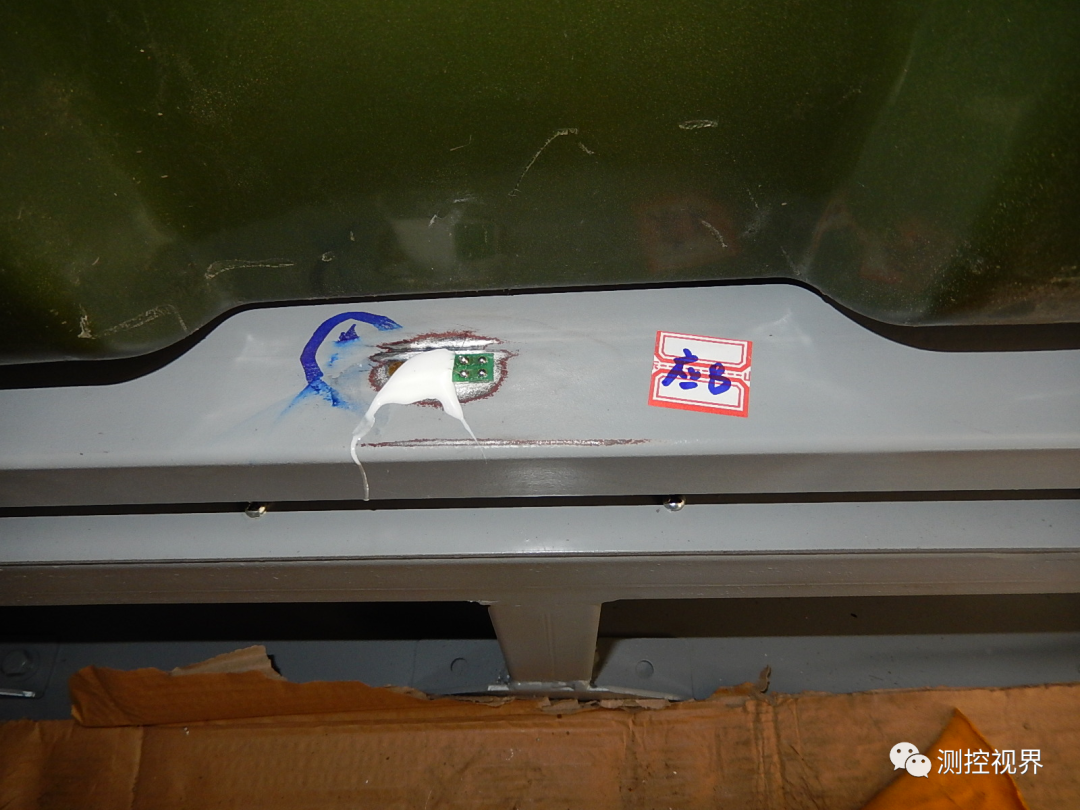
该军用整车绕环形跑道行驶一周,行驶距离0.8Km,共采集119s振动、应变信号,各信号的时间历程曲线分别如图5-7所示。
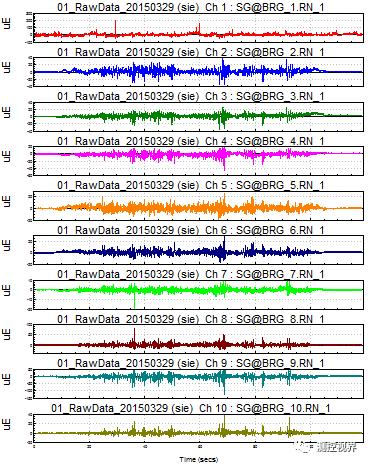
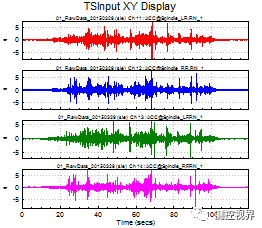
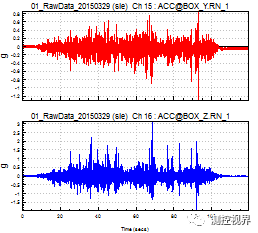
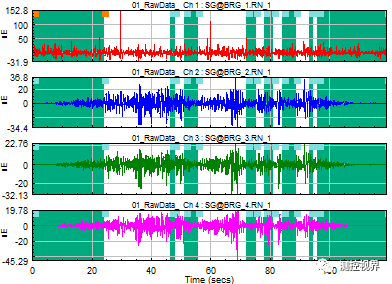
如图8所示,绿色阴影标记片段为没有损伤贡献或损伤贡献较小的可裁剪部分。数据裁剪后,原始119s信号数据压缩为54s。以通道1测点应变信号为例,对前后的信号进行频域成分对比如图9所示。
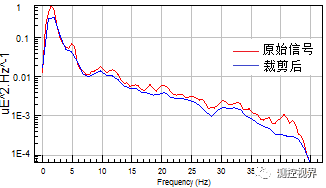
由上图可知前后应变信号频率成分及幅值没有发生明显变化,说明裁剪后信号能有效反映行驶时的载荷环境条件。
用上述54s的4个轴头裁剪后的路谱数据,作为道路模拟系统台架迭代目标,通过台架闭环控制策略在时域上复现该加速度信号。以通道11的轴头加速度为例,控制系统迭代后道路模拟台架上的加速度响应及目标信号对比如图10所示。
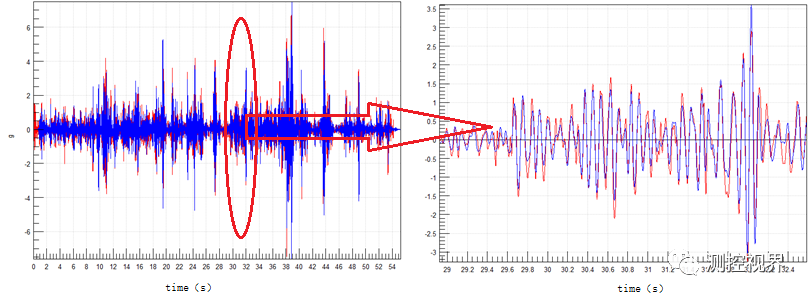
由上图可知,迭代后的响应加速度与目标加速度值能很好重合,说明闭环控制系统精度高。如图11所示,迭代后的4通道轴头加速度信号的RMS(有效值)与目标信号RMS的比值均在91%以上,说明台架可精确复现样车实际行驶时的振动环境条件。
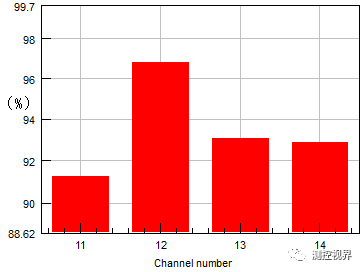
2、 道路模拟试验损伤效果验证
道路模拟台架以4通道轴头加速度为迭代目标,闭环控制系统能精确控制台架对样车施加路谱振动环境条件。为评估道路模拟系统台架及实际路面行驶在相同振动环境条件下,样车的损伤效果是否一致,对比分析实际行驶试验时与道路模拟试验时样机底盘各测点的应力应变损伤水平。由于篇幅有限,仅以底盘通道5-6应变测点及上装设备通道15振动测点为例,进行功率谱密度对比如图12-14所示。
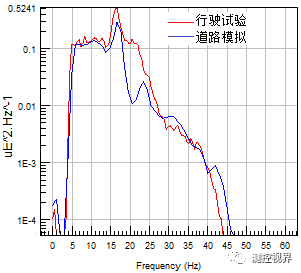
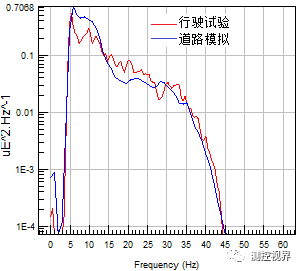
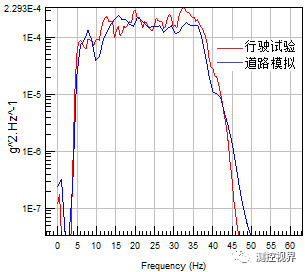
由上图12-14可知,道路模拟试验和行驶试验各测点的频率成分及幅值大小一致,偏差较小。可见道路模拟试验时各测点的响应信号与外场行驶试验时各测点目标信号得到了精确的复现,即行驶试验对样车的损伤效果与道路模拟时对样车的损伤效果一致,54s的道路模拟试验的考核效果可等效为外场119s(0.8Km)的行驶可靠性试验,因此对于10000Km可靠性里程,按传统道路行驶试验方法需50天左右才可完成可靠性试验,而采用道路模拟台架仅需运行187.5小时(1周左右)即可达到可靠性试验考核的目的。
本文通过典型路面的外场行驶试验,采集样车底盘结构及上装设备振动应变响应信号,并进行数据裁剪以获得路谱数据,再以该路谱数据为输入,通过道路模拟试验对样车进行激励加载,结果表明道路模拟试验对样车损伤效果与外场行驶试验效果一致。最终该方法可将该军用整车10000Km(约50天)外场行驶可靠性试验缩短为室内道路模拟系统台架上187.5小时(1周)的试验,加速了该类型军用整车的研发速度,缩短研发周期,节省研发费用,且能更好的进行保密控制。但由于室内道路模拟试验并不能复现整车外场试验的高低温、淋雨日晒吹风等环境条件及发动机工作的激励载荷,采用道路模拟试验如何复现该类环境条件及载荷需要进一步的研究,如采用一定比例的外场行驶试验及室内道路模拟试验进行行驶可靠性考核可作为后续的研究方向之一。
- 下一篇:智能化才是行业变革下半场的核心
- 上一篇:车内VOCs的来源及改善方法
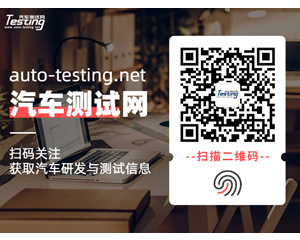
最新资讯
-
商用车及工程机械行业专场:NVH 及语音音频
2025-08-01 17:12
-
理想i8和重卡对撞测试引争议,东风柳汽发声
2025-08-01 15:52
-
艾德克斯IT-N2100 系列太阳能阵列模拟器
2025-08-01 15:43
-
ITECH重磅发布IT2705直流电源分析仪,重构
2025-08-01 15:34
-
现代汽车新一代混合动力系统:以技术革新引
2025-08-01 15:32