汽车零部件疲劳载荷相关性分析
由于路面载荷预测量只有在样车之后才能进行,在当今逐渐缩短开发周期的情况下,往往在路面载荷测量之前,耐久性设计就开始进行,这需要工程师在整车开发早期就找到替代载荷,因此在当今汽车工业开发过程中越来越依赖于多体动力学模型预测车辆载荷,结合有限元分析软件进行疲劳仿真分析,较好的解决在新车型开发初期或对现有车型的设计验证,故载荷的准确性至关重要。
本文借助悬架系统中简单二力杆连接点处的试验载荷与通过多体仿真分析获得相同零部件的载荷进行相关性分析,验证多体动力学模型的准确性,保证汽车零部件载荷精度,确保耐久性分析的准确性。
1 零部件标定
2 道路载荷谱采集
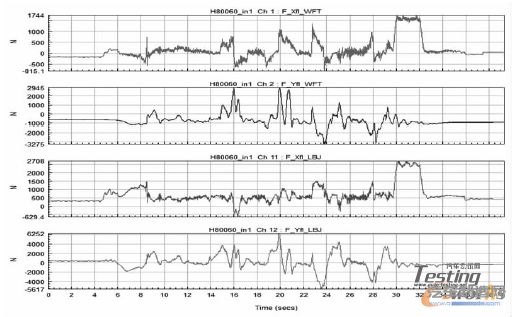
3 多体动力学仿真分析
在MSC.Adams中创建悬架刚柔耦合动力学仿真分析模型,要求模型状态与整车试验状态一致、坐标系一致、参数一致,以便后续进行相关性分析。本文将摆臂、副车架、稳定杆处理成柔性体,所有衬套均赋予非线性刚度特性曲线,采用轮心六分力进行激励仿真,仿真分析得到悬架中各个零部件的载荷谱,具体模型如图2所示。
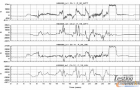
3.2 仿真分析结果
提取各个零部件连接点处的载荷(包括FX、FY、FZ、MX、MY、MZ)、位移、加速度等信息,以下摆臂球销处的载荷为例,具体如图3所示。
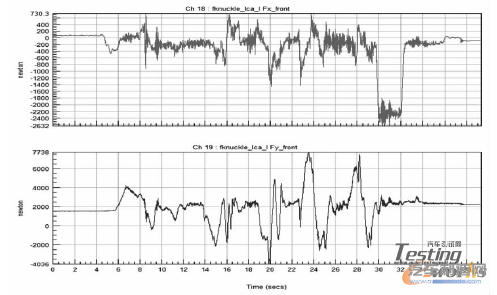
4 相关性分析
对试验与仿真数据进行对比,由于载荷谱的数据点较多,无法实现试验与仿真数据的完全一致性。故本文主要是通过功率谱、雨流计数、程对计数、穿级计数、伪损伤(相对损伤)进行对比分析,并自动生成报告,具体结果如图4所示。
通过S-N曲线可以知道损伤与载荷之间存在一定的关系,若损伤一致零部件的寿命也是一致,本文采用K=5进行相对损伤计算,结合图4和图5可知,损伤相差15%,载荷相差大约3%左右(德国部分企业认为K=5时,自损伤与载荷大概成5倍关系)。而程对计数与穿级计数,试验与仿真数据的曲线形状一致即可,若存在上下偏移是零部件的预载所导致(因为在进行道路载荷谱采集工作时,将整车中所有传感器清零,故零部件的试验载荷未包含预载)。
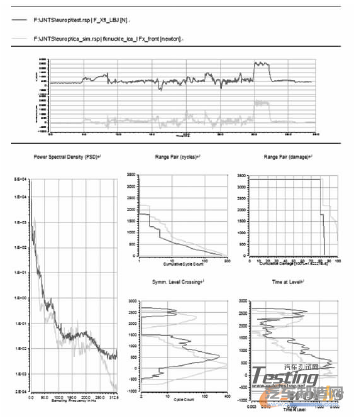
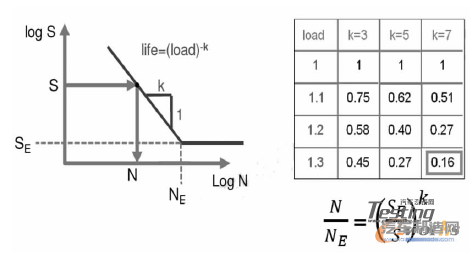
5 结论
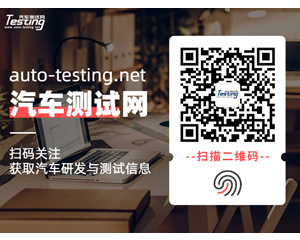
最新资讯
-
2025 汽车测试及质量监控博览会(中国)盛
2025-08-29 13:28
-
达安中心全景环视系统测试能力全新升级,筑
2025-08-26 19:28
-
ATE展会倒计时:迷你研讨会
2025-08-26 19:26
-
在竞技环境下,奇石乐先进测量技术亦能提供
2025-08-26 10:24
-
从创新的赛车六分力传感器到海量数据的高效
2025-08-26 10:21