技术快报 | 整车热管理系统(TMS)的控制策略开发技术及平台
车载控制系统控制策略的开发,不管是采用敏捷模式、前后溯源逐步迭推模式,还是分层式、主从式,多是通过“V”字型开发流程采用模型化的开发方法(MBD, Model based development)来完成。
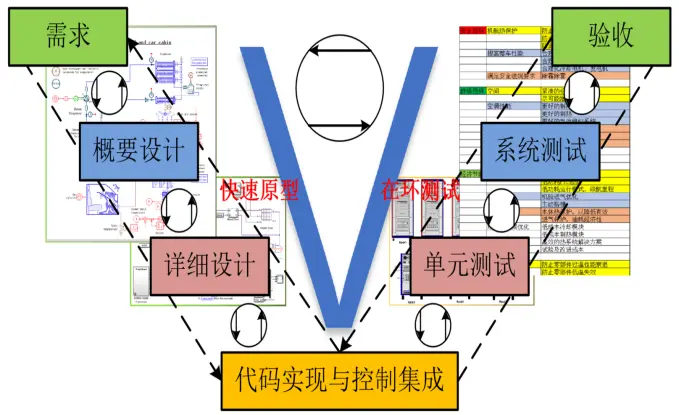
“V”字型开发流程图
针对这一开发流程,中汽中心工程院风洞中心建立了整车热系统功能性能对标测试分析、系统构型、系统功能性能仿真、控制快速原型、系统标定、系统仿真测试分析(在建)、关键零部件及系统实际环境测试分析等全流程关键节点的开发能力。
整车热系统功能、性能对标测试分析
作为产品需求分析、市场定位分析的重要环节,对标(Benchmark)测试是常用手段。根据行业里对整车热系统控制对标测试分析的需要,风洞中心开发团队已经掌握了各种情况下的CAN、LIN通讯协议的解析能力,还具备了外加测试通道实测相应性能数据的能力。基于此,开发团队具备了新能源汽车热系统及动力总成系统能耗测试并对测试数据进行自动分析计算的能力和分析整车热系统控制的功能、性能并得到Benchmark解析报告的能力(能量流可自动计算分解到续航工况下的每一个循环的每一个器件)。
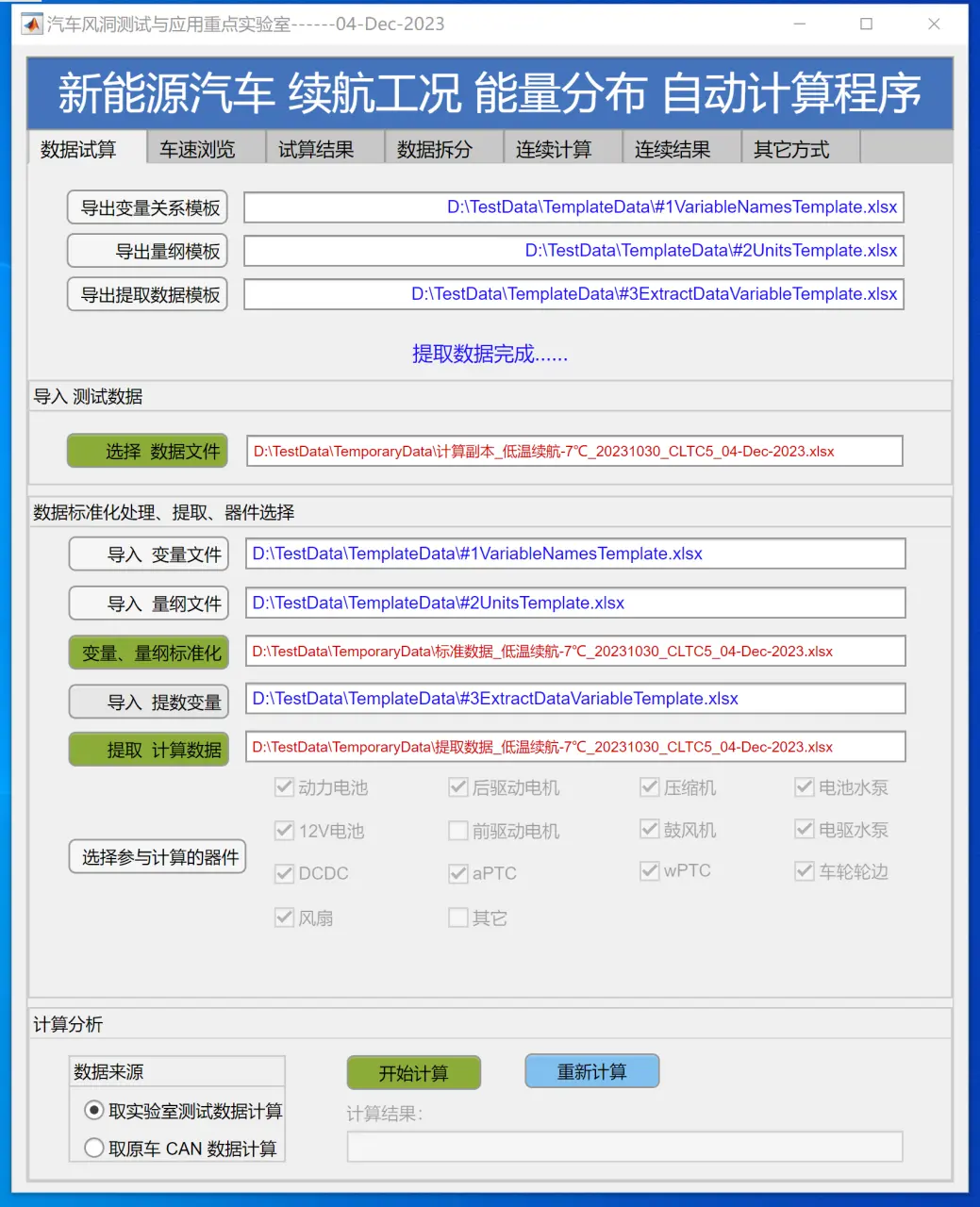
计算程序界面
整车热系统构型
根据待开发整车的设计空间布局、电池电驱系统的配置及其性能标准、乘员舱的制冷和制热需求、主动及被动冷却和余热利用的工作模式,以及参照Benchmark测试数据库的数据或对比数据,进行热系统总布置的设计构建符合要求的热系统构型。
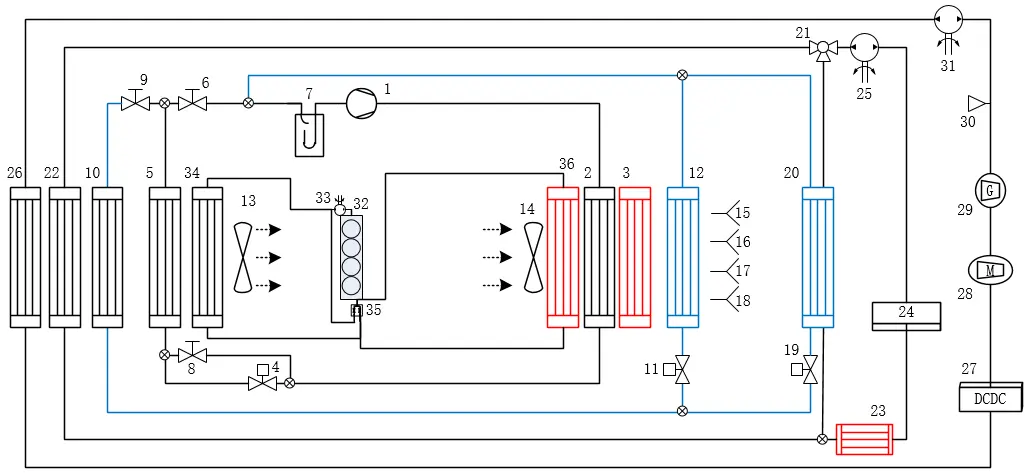
构建某一混动车型TMS构型图
首先根据整车热系统构型与性能要求,进行系统内关键零部件的选型和功能性能验证,其次依据性能仿真的结果对当前的热系统可开展多种分析优化工作。分析优化的工作包括但不限于:系统工作风险与热害分析、性能性能与零部件热害防护的折中优化、不同模式不同工况与不同负荷下能耗分析与能耗耗散分析、总布置与流道和工作模式的优化、系统性能与成本的折中优化,各零部件之间的关联协调与控制逻辑设计等。
系统功能、系统性能仿真
针对各类热系统构型,基于Simulink + Amesim建立相应的模型,对系统和系统中的部件的功能和性能进行仿真和虚拟验证。可实现热系统中执行部件如电动压缩机、各类阀、水泵、PTC、鼓风机和风门电机等各种的动作是否到位,是否满足相应的实时响应要求,结合实验数据进行软标定。在系统性能模型中,分析性能是否满足设定要求,各种散热器(包含冷凝器、蒸发器、液液板换)性能是否满足设计要求,并在实际工况模型中进行必要的优化。在系统性能验证中还可验证升降温响应、冷却水流量、制冷剂充量、压缩机转速、压缩机功耗限值、水泵控制方式、风扇控制方式、鼓风机控制方式、舱内温湿度控制是否满足人体舒适区间要求、电池水热系统是否满足其工作温度区间要求等。必要时,可仿真出不同性能的工作模式,节能模式、舒适模式、常规模式与极限模式。
结合热系统控制与原型需求、温度分布区间与分布均匀性需求,对热系统构型做必要的优化,提出策略原型逻辑框图。
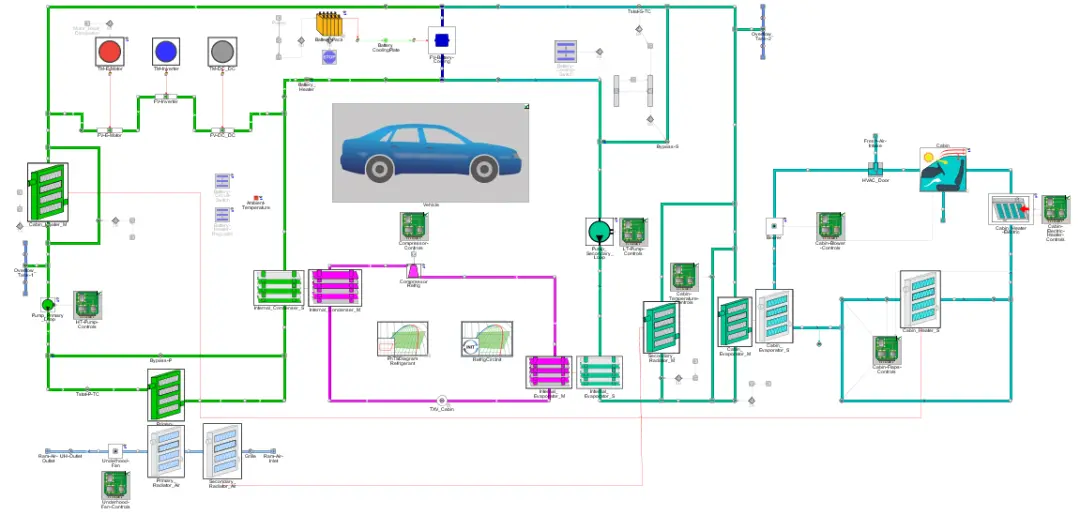
热系统性能仿真模型图
控制快速原型
基于1D性能仿真优化后的构型,结合热系统构型和控制策略原型逻辑图,选用热系统中相应的部件如电动压缩机、电子膨胀阀、鼓风机、PTC等部件,制作或选取相应的管道、流道等器件,在选取合适的实时控制器和IO端口后便可便捷地将热管理的控制程序下载编译到实时控制器中,快速构建起目标的快速控制原型(RCPs,Rapid Control Prototype system)。
在没有生产出车载级的热管理系统控制单元时,可采用快速原型的方式将快速将TMS驱动起来。在快速原型的方案中,选取适当算力的原型控制器代替车载的实时控制器;选取配置功能丰富的接口代替嵌入式系统接入热系统中的真实器件。本方案可验证热系统的控制策略是否满足设计;验证控制系统是否可靠;验证TMS中零部件的性能,最终将验证后的系统信息和系统中软硬件的指标作为硬件开发的输入对车载级TMS控制单元的开发起到指导作用。该RCPs,具有丰富的周边IO接口,依据热系统构型的需要,可灵活配置,已经开发了一套运行通验证的原型软件,针对其它不同TMS构型,只需要调整接口、替换控制逻辑模块“CaculateSub”,进行适当的配置即可运行控制。
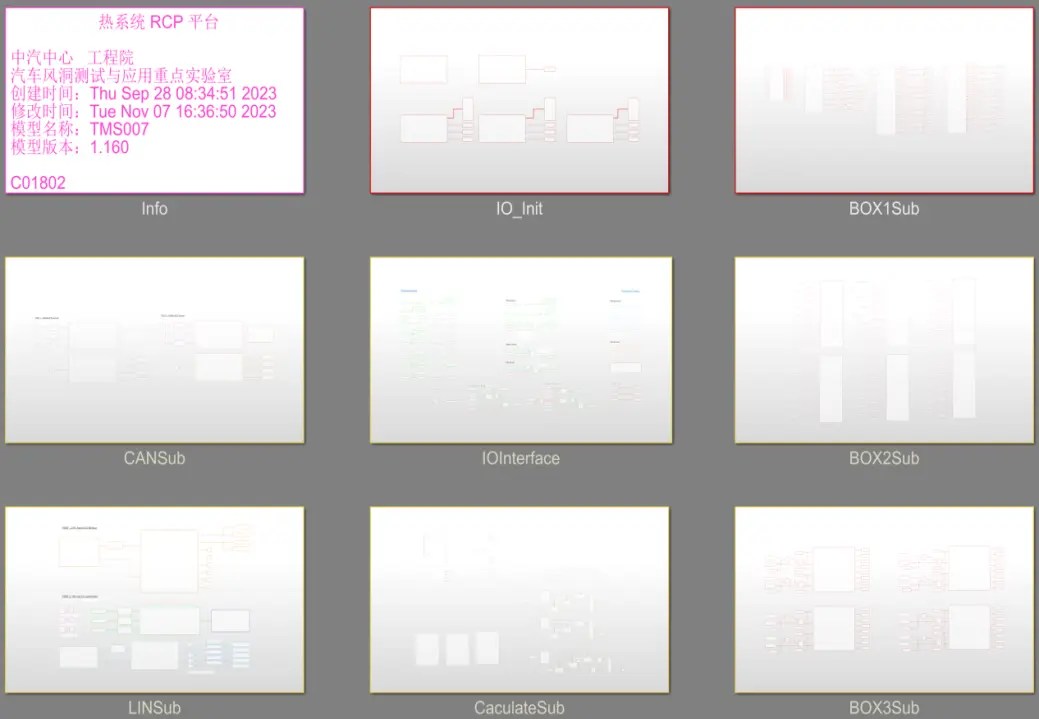
热系统RCP模型图(软接口底层驱动及控制程序)
基于RCPs可直接运行在Simlink、C、C++开发的模型程序,验证并优化调整控制策略,同时软件模型可轻松实现反复修改、模块化复用和封装、更换底层驱动等方式针对不同控制器重新编译下载,这都极大地便利了控制策略的实行和TMS系统软件的开发。基于这一特点便于在开发的前期或半实物状态和真实环境下反复研究、配置系统,减少了开发的费用,提高了开发的效率。
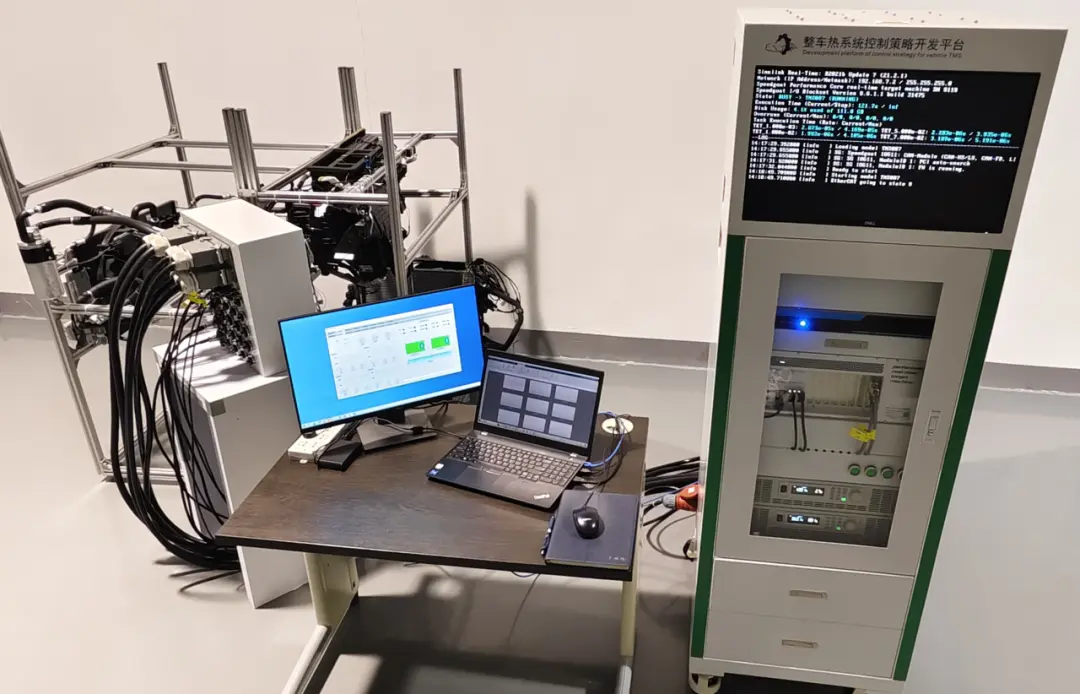
热系统RCP系统图(硬件系统)
基于RCPs可实施TMS零部件的标定工作和零部件性能验证工作。TMS中的温度、压力、阳光和空气质量传感器、出风口工作段和风门位置的标定可通过RCPs来实现。TMS中电动压缩机、PTC、鼓风机、风扇和水泵等执行部件的功能性能要控制指令(开关指令、PWM波、LIN控或CAN控物理值)之间的关系可通过RCPs来验证。TMS中各部件的性能和功能验证如,运行能力、NVH特性测试、PTC功耗测试、制热量测试和水泵功耗等测试都可通过零部件的在环测试实现。以上对于零部件的验证,在开发的前期实现合适的零部件替代,提高零部件在热系统的性价比。
基于以上工作构建出适合整车的热系统,必要时进行操作运行界面虚拟开发和测试监控界面开发,如下图示:
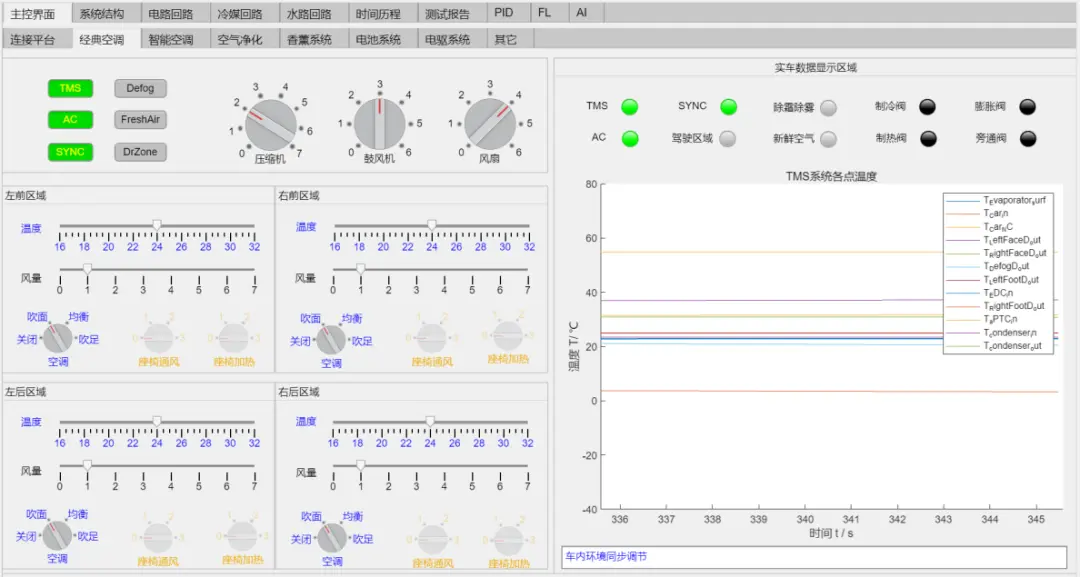
热系统RCP模型图(操作运行界面)
除零部件的测试验证外,RCPs可完成控制仿真之后的真实器件系统级控制的实现、系统级的标定,也在车载ECU未开发出来时代替完成hil测试、实现对整车级的TMS控制,完成整车级的标定工作;可完成TMS零部件、系统在台架、系统在整车的电能耗测试、工作效率测试,结合环境实验室可实施TMS零部件、系统在台架、系统在整车的工作状态的热害测试等。
风洞中心为行业开发的RCPs,基于真实器件,既可对TMS中的任一器件实施实时的控制,即任何一台风门电机、电控压缩机、电子风扇、电动鼓风机、电动水泵、PTC、电子膨胀阀等单独实施控制,完成零部件的控制相关测试与验证;也可对TMS系统在台架状态以及在整车状态实施系统级控制,完成台架在环境实验和整车在环境实验;还可对车载其它真实执行器件实施控制,如任何一扇车门及其玻璃的升降控制、后视镜的动作控制、座椅加热与通风控制、座椅姿态调节、主动格栅(AGS)的动作控制、刮水器电机的控制、玻璃清洁喷水系统控制、转向电机控制、气囊点爆控制、安全带预紧控制等几乎所有的车身电子、舒适电子的快速原型控制。实现TMS、车身电子与整车的同步开发、验证。
至此,基于该TMS控制开发平台(含物理构型和原型控制的平台硬件和软件模型,可满足热系统控制需求实时运行),既可完成热系统控制策略的开发服务,也可单独向行业提供热系统及其零部件的标定、测试验证服务;基于该开发平台技术,实施各种热系统自主控制对标测试与验证测试,完成控制方案开发验证,直至最终交付成套的整车热系统方案和技术。
作 者:于镒隆
来 源:汽车风洞测试与应用重点实验室
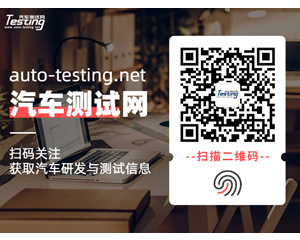
最新资讯
-
商用车及工程机械行业专场:NVH 及语音音频
2025-08-01 17:12
-
理想i8和重卡对撞测试引争议,东风柳汽发声
2025-08-01 15:52
-
艾德克斯IT-N2100 系列太阳能阵列模拟器
2025-08-01 15:43
-
ITECH重磅发布IT2705直流电源分析仪,重构
2025-08-01 15:34
-
现代汽车新一代混合动力系统:以技术革新引
2025-08-01 15:32