基于模组加热的新能源汽车火灾试验研究
文章来源:应急管理部天津消防研究所
0 引言
发展新能源汽车是我国应对国家能源战略需求、实现 2060 年碳中和目标的重大战略选择。截止 2021 年,我国新能源汽车产销量连续 6 年位居全球第一,累计推广数已达 550 余万辆。同时,新能源汽车保有量仍保持上升趋势,国务院2020 年发布了《新能源汽车产业发展规划(2021—2035 年)》提出:到 2025 年,我国新能源汽车销售量达到汽车新车 销售总量的 20%;汽车工程学会发布了《节能与新能源汽车技术路线图 2.0》,预计 2035 年国内新能源汽车保有量将超 过 1 亿辆。然而,随着新能源汽车产销量飞速提升、技术快速发展,新能源汽车起火现象也逐渐频发。据应急管理部统 计数据,2021 年新能源汽车着火事故超过 1000 起。新能源汽车火灾蔓延速度较快,火灾危害大,引发全行业及社会密切 关注,起火问题严重制约了产业快速、健康可持续发展。
动力电池是新能源汽车能源系统的核心,其在全气候环境下动力电池工作性能和安全性随时间动态演变,是导致新 能源汽车出现起火问题的关键诱因。然而目前动力电池热失控触发机理尚不明确,诱因繁多,无预兆突发性热失控难以 复现,这些问题制约了动力电池应急管理系统的设计,同时也导致新能源汽车火灾消防难等问题。研究新能源汽车火灾 事故复现,探究电池系统内部热蔓延、热扩散过程,指导高安全电池系统设计与过火后消防应急管理设计,查清火灾事 故的原因,是目前新能源汽车安全管理的重要研究内容。
单明新等则在 2015 年首次对敞开空间电池爆炸强度进行了直接测量,2018 年—2021 年,清华大学欧阳明高院士 团队长期从事动力电池热失控相关研究,为分析热失控可能触发方式、内部触发机理、热扩散机制等奠定了理论基础。2021 年,Yang 等最先研究了热失控后的碳氧化物(特别是一氧化碳)的逸散,并建立了基于 CO 浓度的热失控预测模 型。2021 年,王青松教授等研究了热失控时的泄压阀开启导致的喷发和燃烧等现象,并针对 811 体系电池和 18650 电 池分别展开了研究。2021 年,王芳等首次研究了高比能电池在低 SOC 下的热失控行为,并认为隔膜的相变反应是该条 件下热失控的主要影响因素。目前,大部分针对锂离子电池热失控的研究均针对单体电池热失控机理、热失控行为及特 征等,针对系统级或整车级的热失控研究不充分,缺乏电池热失控时整车级的燃烧试验数据,对于整车级的火灾和 烟气蔓延、致灾危害和致灾前后数据特征变化仍需开展深入研究。
本文建设了新能源汽车整车级热失控试验平台,基于电池包内单个模组外部加热方法开展了整车级热失控试验,探 究了电池热蔓延、热扩散路径,分析了整车级热失控的数据特征,为设计火灾车消防系统、安全电池系统设计以及灾害 事故调查提供参考。
1 试验平台建设与热失控触发方式
1.1 试验平台设计
为探究新能源汽车动力系统失效过程及特征,本文基于前期建立的新能源汽车整车级热失控试验平台开展整车燃 烧试验。试验平台可采集电池组电压、温度、烟气等数据信息,同时布置多组摄像头、红外热像仪等实时记录电池组内、 外热失控触发与火灾蔓延过程,以及整车温度场分布等信息。试验台布置简图如图 1 所示,其中电压传感器、温度传感 器、烟气传感器为特制设备,可满足电池组内高温环境下的数据与信号采集;其他设备等为标准采集设备,具体设备种 类与型号见表 1。
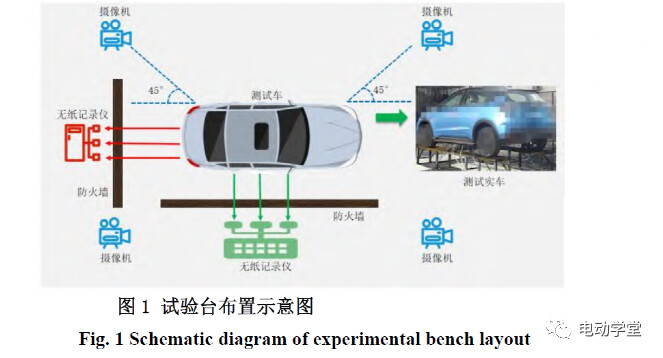
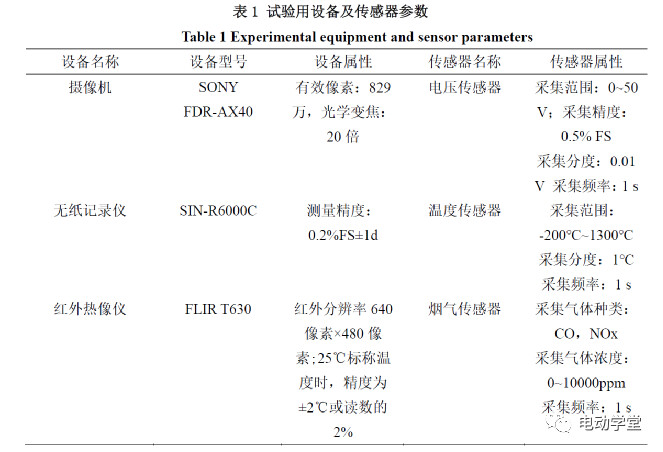
为对比分析火焰传播与扩散路径,选用四个摄像机布置在车身四角方向上,可实现全景摄像信息采集以分析火焰在 车身上的传播路径。此外,车身内驾驶员座位上布置了烟气传感器,用于检测烟气进入乘员舱内的时间与烟气扩散速率。
1.2 传感器布置方式
在本次试验过程中,在电池包中共布置 22 个热电偶。在热电偶布置前,将电池包上盖打开后在内部布置热电偶,采 用绝缘胶带与铝箔胶带对各热电偶进行固定与绝缘处理。然后将热电偶连接线沿电池包上盖与箱体结合处依次甩出,并 打胶密封以保持电池包完整结构与气密性。在试验过程中采用无纸记录仪记录热电偶采样温度值,采样间隔为 1s,热电 偶承受温度超过 1000℃。电池组系统内电压传感器与温度传感器布置方式如图 2 所示。
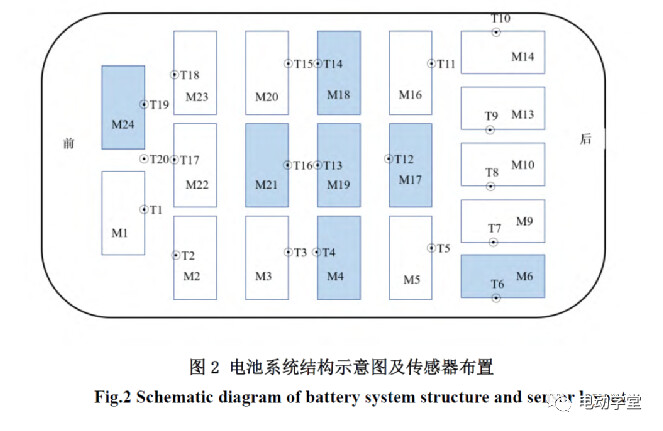
本次测试选取的动力电池组内模组排布如下:电池组前部为单层模组连接,后部为双层式模组叠放式连接,图中的M7/M8/M11/M12/M15 号模组分别位于 M6/M9/M10/M13/M14 号模组下方,故而在图中并未标明,每个模组内有 12 个电 池单体。图中标红的部位为温度传感器布置位置,其中 6/7/8/9/10 号温度传感器布置在了双层模组的侧壁上。图中标色的M4/M6/M17/M18/M21/M24 模组为布置了电压传感器的模组。除 M20/M21/M22 号模组布置在了电池箱体表面外,其他温 度传感器均布置在电池模组的侧壁中央。被加热模组为 M18 模组,因此 22/23 号传感器检测的是被加热模组附件电池包 外壳温度,可分析电池组内热失控发展速度与过程。特别的,由于温度传感器仅能布置在电池模组表面,因此其检测到 的温度不代表电池核心/平均温度,且由于热失控触发方式为表面加热,18 号模组表面的温度传感器采集温度可能偏高。
1.3 热失控触发方式
本试验中动力电池热失控触发方式为外部加热触发。通过在 18 号模组表面布置加热膜,在试验开始时通过对加热膜 进行供电,持续加热电池模组直至触发热失控。为了提高电池热失控速度,根据模组不同面的面积大小,本试验中共使 用两个 1000 W 和一个 800W 的加热膜分别贴在被加热模组两个长壁面处和模组底部,提高电池温升速度。试验开始前, 温度传感器、电压传感器、加热膜供电线均被引出至电池组外,而后重新密封电池组以模拟内部封闭环境。所有线束均 无重叠,以减少对电池组密封性的影响。
2 整车级热失控数据分析
2.1 温度数据及特征分析
为本次试验采集的动力电池包内各模组温度分布。图中绘制数据经过清洗,剔除了部分无效值。所用的无纸记录仪 温度测量范围为-200℃~1300℃,然而在实际测试过程中,部分采样点温度达到 1300℃,为采样设备上限值,实际温度可 能高于 1300℃。另一方面,在实际的电池包热失控过程中,一般情况下电池组表面温度(传感器测量温度)大约在 400-1000℃左右,而部分采样点温度超过 1300℃,应是采样线烧损、传感器故障等导致。在本次试验中,在剔除掉温度 故障数据点后,无明显的异常温度值出现,少部分突然出现的温升可能与电池模组热失控喷发的高温气液混合物导致。同时在本次内加热试验中,发生热失控的各模组温度变化与动力电池的一般热失控温度演化过程相似,除 M18 号模组因 表面被加热外,其他模组在发生热失控前大多有短暂的自产热与引发阶段,随后才出现突然的温度升高现象。大部分动 力电池模组在发生热失控过程中均保持相似的温升曲线,总体保持在发生热失控之前温度升至热失控自产热温度 T1,而 后温度保持在一定范围内引发热失控,温度快速上升至最高温度而后下降。但对于每个模组而言,由于每个模组内有 12 个电池单体构成,其热失控自产热阶段保持时间不同,加上热蔓延路径的差异,少部分模组可能长达数分钟,也有模组 在几十秒左右后即进入热失控引发阶段。
一般情况下,动力电池热失控过程需依次经历多种副反应过程。在热失控自产热阶段,电极表面的 SEI 膜会逐 渐发生分解并放出热量,从而维持电池组温度保持。随着 SEI 膜分解加剧,电池内部结构被破坏,导致石墨负极与电解 液直接发生反应,并引发热失控。在热失控引发阶段中,电池组温度快速上升,同时内部材料、结构等被破坏,正极 材料发生分解、电解液发生分解,电池内短路发生造成快速自产热,到最后电解液燃烧,核心温度剧烈上升。
以开始加热的 9 时 10 分 00 秒为计时零点,所有的温度、烟气和电压分析均以此为计时 0 秒,1900 秒左右时电池包 内出现异响,随后电池包内向外冒出烟气,1963 秒时模组内 18 号模组的温度测试点 T13 出现了近 70℃的上升,随后周 围的测温点也迅速出现了不同程度的温升。
因为本试验研究中的测温点布置在模组之上,模组内单体的热失控表征出的温度特征、电压特征没有那么明显,一 个模组内单体热失控后可能会对邻近模组的测温点也有升温的影响。从事故后拆解得到的电池包残体现象表明,M1、M2、 M3、M20、M22、M23 和 M24 这些电池模组受损情况较小,整体形状保持完整;从温度数据分析,这几个模组总体的温 度分布较低,模组表面后期温度在约为 300℃左右。温度分析结果与痕迹分析结果吻合,表明这些模组受损较轻,为后期 火烧所致,见图 3。
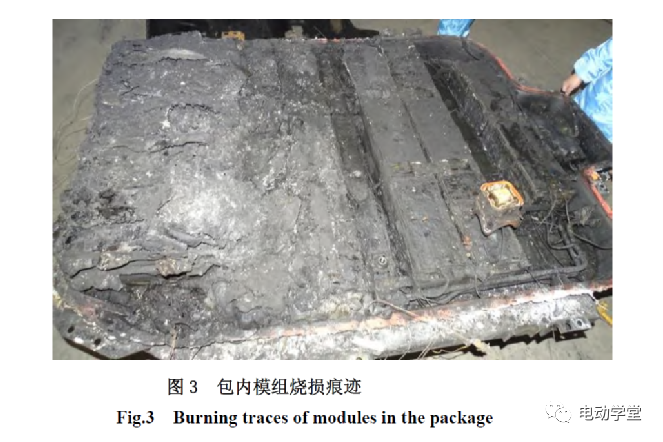
如图 4 所示,为 M5、M6、M9、M10 号模组上布置的热电偶采集温度值。该四个模组表面温度在最早模组出现热失 控后温度维持在高值,M5 与 M6 模组在后期出现了温度的上升,说明火势后期蔓延到两个模组时受热发生热失控,温度 快速上升。
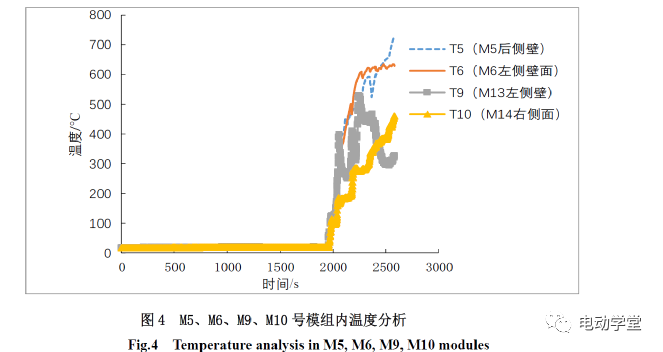
如图 5 所示,为 M18-M21 号模组上布置的热电偶采集温度值。其中,M18 为被加热模组,其表面温度最先升高至 较高水平;然而在试验过程中曾多次下电并重启,因此其表面温度曲线存在多次上升和下降阶段。同时,其表面温度在 被加热时约 600℃左右,然而并不代表其内部核心温度,因此热失控并没有在最开始时发生,而是在加热一段时间后。在 1860 秒左右,表面温度缓慢上升,此时推测为热失控自产热阶段,内部 SEI 分解反应已开始进行,而在 1963 秒左右其表面温度迅速升高,此时表面电池内部已发生剧烈的热失控副反应。在 18 号模组热失控触发后,其喷射的高温气液混合物也迅速加热临近模组,导致其他模组表面也存在快速温升,冷却后又迅速下降,并在一段时间之后重新上升,表明这些 模组已发生热扩散。
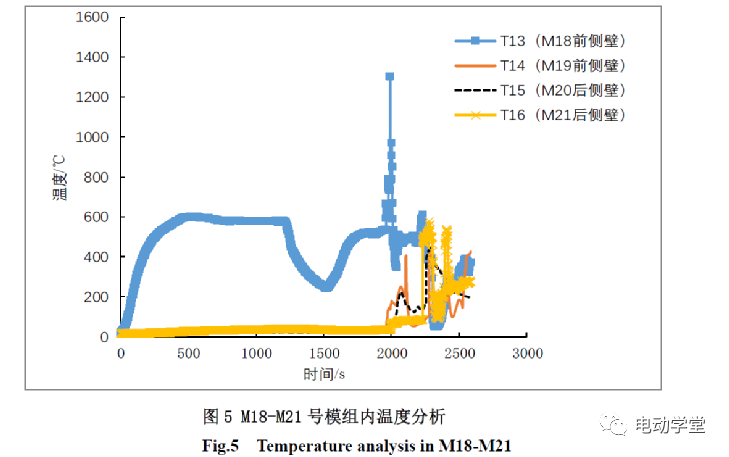
如图 6 所示,为 M22-M24 模组上布置的热电偶采集温度值。图中温度数据表明,模组在热失控前存在一次较快的温 升和冷却,这一过程疑似其他模组发生热失控产生的高温喷发物导致的温升。而在这一阶段过后,几个模组温度缓慢上 升,但没有出现明显发生热失控的过程。根据电池拆解试验结果,这些模组的热失控可能发生在数据记录仪停止工作后。
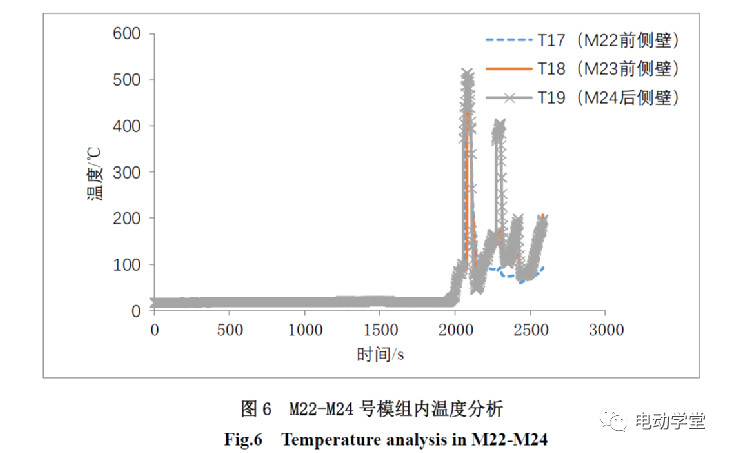
2.2 电压数据分析
图 7 为在热失控发生前,主要模组的电压分布趋势。最先发生热失控的 M18 号模组,在电压恢复过程中突然存在较 明显的电压下降过程,这一过程持续时间约为 10min,同时电压下降幅度为 40mV 左右,这一过程表明在电池模组发生热 失控前存在较明显的电压特征,随着加热内部电池反应,电池电压值的下降明显,可指导后续热失控预警算法设计以及 事故车辆后台数据特征的捕捉。
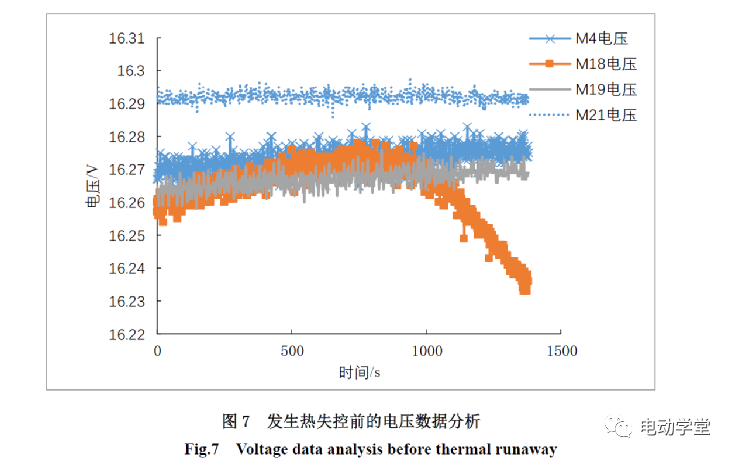
图 8 为 M18 号模组电压下降过程,在发生热失控前电压缓慢下降,而后在某一点发生电压突降,幅值为 4V 左右, 表明模组内有单体发生了内短路,对外电压为 0V。而后电压继续缓慢下降,并又一次发生突降,幅值为 4V 左右,此时 模组内继续有单体失控电压降为 0。而后电压保持并又发生突降,幅值较大,单体数据接近 0,模组内剩余的单体相继传 导发生了热失控。而总电压无明显变化,在电池组内部温升上升后通讯线断开,无电压信号采集。
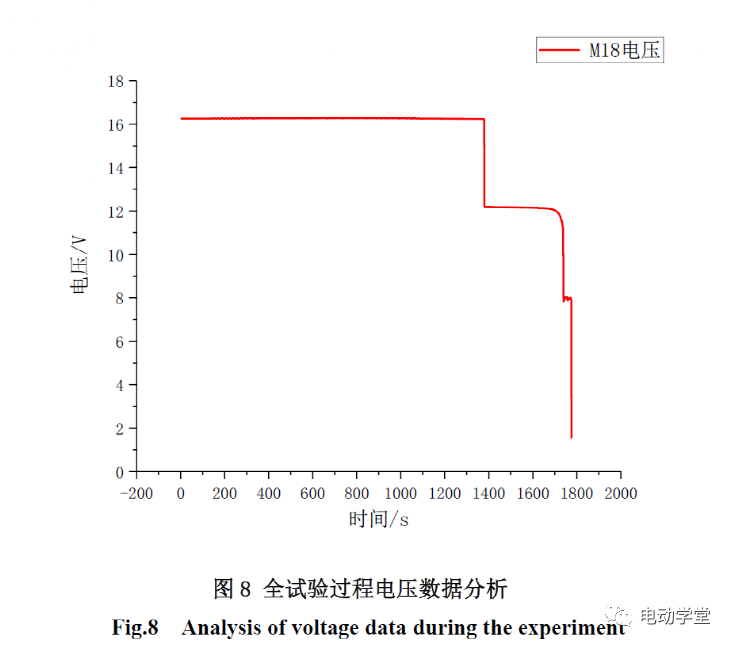
2.3 其他数据分析
如图 9 所示,为本次试验中采集的烟气数据。整体数据在电池包发生热失控前几乎无数据监测,而后在 1932 秒左右 监测到包括一氧化碳与硫氧化物的烟气数据,这个时间点与布置在驾驶室内的摄像头捕捉到烟气进入驾驶室的时间几乎 同步,30 秒左右一氧化碳浓度迅速上升达到传感器检测峰值,超过了 12000ppm,硫氧化物浓度随着热失控的发生也超过 了 2500ppm,达到了危及乘员生命安全的浓度水平。自电池包内出现异响到与冒烟后到乘员舱内可检测到一氧化碳烟气, 共经历近 3 分钟左右时间,表明热失控蔓延速度较快,同时烟气进入乘员舱速度也较快。此时的致灾危害主要集中在驾 驶室内烟气对于乘员的危害,底盘电池包周围火焰对于周围人与环境的危害。
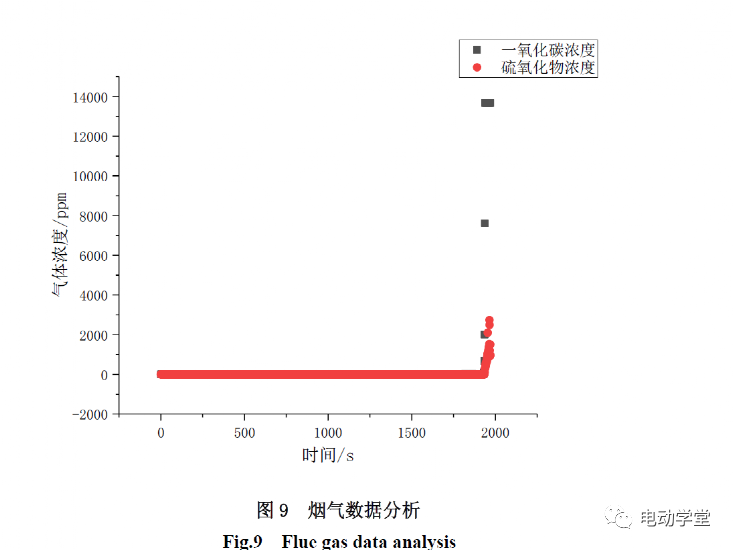
2.4 电池组热蔓延路径分析
根据电池组内温度、电压分布数据、烧损形态,可以大致推测电池组内各个电池模组发生热失控与燃烧蔓延顺序。如表2 所示,基于电池组首个温度峰值、电压的早期电压降、烧损形态与最早加热触发的事实,确认18 号电池模组为首个发生热失控的电池模组。而后基于后续的有效温度阶跃,推测与18 号模组最邻近的M4、M17、M19、M21 模组相继发生热失控。第三批次是相邻近的M5、M6、M13、M14 模组。M1、M2、M3、M20、M22、M23、M24 模组距离18 号电池模组较远,拆解后发现该模组形态保持较完好,其与核心触发模组间间距离较大,导致喷发物导致的高温不足以引发其发生热失控,因此电池包内模组发生热失控的先后顺序与最早加热模组及蔓延路径方向有很大关系。
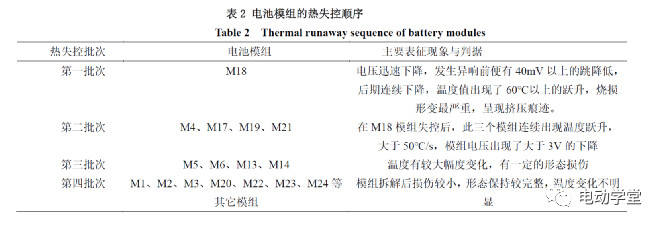
3 结论
本文借助已有的新能源汽车整车级热失控试验平台,通过人为加热触发电池热失控方式探究动力电池热失控后蔓延 及扩散过程,针对某辆新能源汽车开展了热失控试验测试,通过在电池组内部埋设加热膜对某个电池模组持续加热以触 发热失控,并持续采集电池组内电压、温度、烟气等信号,并探究整车级热失控破坏程度及致灾危害,以及烟气与火在 电池包内、车体内的蔓延路径,为指导新能源汽车安全系统优化设计以及事故调查的数据分析提供参考。
(1)在电池模组加热过程中,前期电池内模组内单体温度不断升高,在热失控发生后有一个温度突升的过程,而且 影响到电池包内其它模组,瞬间可蹿升 300℃以上,部分测温点的突升与火焰在包内的蔓延和电池失控后喷溅物的滴落有关。
(2)热失控发生后,火势沿包内的空隙(密封条、泄压口)向底盘、车身处进一步蔓延,部分热烟气通过底盘的空 隙进入到驾驶室内部。从电池有异响到驾驶室内 CO 浓度达到峰值超过 12000ppm,只有不到 2 分钟时间,在此期间硫氧 化物的浓度最高达到了 2734ppm。
(3)电池模组发生热失控前存在较明显的电压下降特征,下降幅度在 50mV 左右,可指导后续热失控预警算法设计 以及事故车辆后台数据特征的捕捉。模组的电压呈现阶梯状下降,与模组内的单体先后热失控后的电压变化有关。
(4)电池包内的模组失控顺序基本与包内的热传递路径一致,最先加热的模组首先失控,其次是紧邻加热模组的几 个模组,然后向远处扩散。电池包内的模组变形痕迹也可以与此相对应。
- 下一篇:自动紧急制动系统AEBS中欧法规解读
- 上一篇:浅析最新自动驾驶视觉技术路线
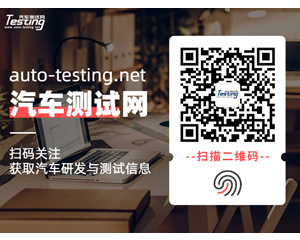
最新资讯
-
打破营销内卷:小红书以“车生活场景”重塑
2025-09-01 19:18
-
2025汽车测试展回顾:你错过的研华科技亮点
2025-09-01 10:58
-
又一 40 亿级别电池项目,落户芜湖!
2025-09-01 10:58
-
深信科创完成A轮融资,引爆合成数据范式革
2025-08-31 08:30
-
雅迅智联自研全域地图解决方案,破解车企出
2025-08-31 08:28