汽车声学包装开发的轻量化策略
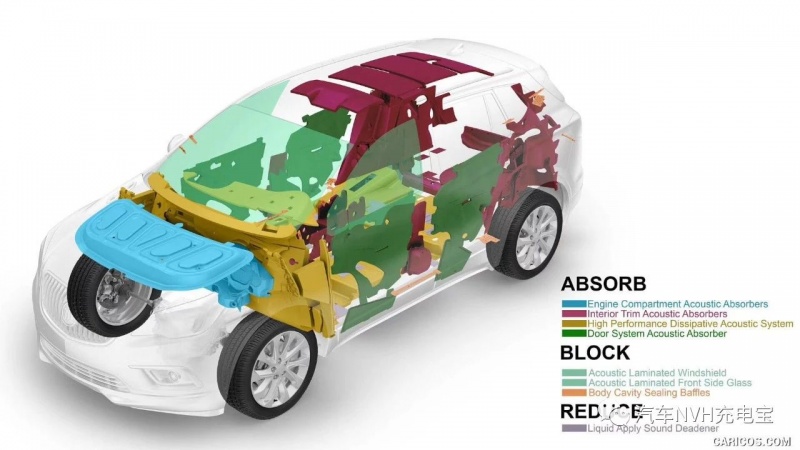
汽车的轻量化一直是产品研发永恒追求的目标;对于传统汽车而言,汽车轻量化技术由于可有效减少污染物和降低碳排放,研究表明,汽车质量每下降10%,油耗下降约8%,排放下降约4%,节能减排效果非常可观!对于新能源汽车,轻量化的效益更是不言而言,能够有效提高续航里程,缓解用户的里程焦虑。
由于车身在整车重量占比最大,所以主要的减重目标就是在它身上,目前重点的发展方向是高强度钢、铝合金、镁合金或塑料等新材料的技术应用。比如奥迪A8和特斯拉电动车就采用了全铝车身,其他主机厂都花大力气在轻量化研发上下功夫。
当然作为车身上一个重要的声学降噪套装——声学包装,也能为整车减重贡献一部分,虽然不多,也是能抠一点是一点的。据我们统计的结果,大部分汽车的声学包装重量一般在20-30kg,如果能降低10%,那也是3kg的贡献。不同的重量对应不同级别的性能,性能与重量之间的比值也是衡量声学包设计水平的一个指标。如何高效的利用每一克重量,发挥最大的的降噪效果也是一个重要的研究课题。
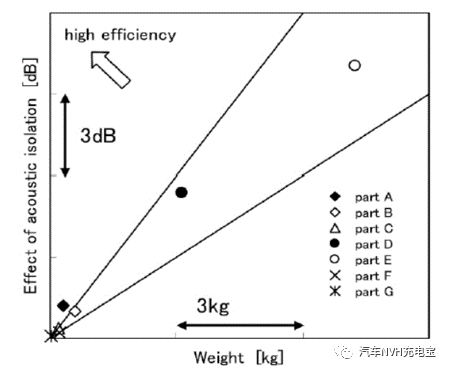
下面就以三个方面来介绍下如何进行汽车的声学包装轻量化设计。
· 声学包装设计轻量化的数学解释
· 轻量化设计的思路和策略
· 电动汽车的轻量化设计
声学包装设计轻量化的数学解释
根据隔声理论,零件的隔声量跟单位面积质量成正相关,满足质量定律(mass law):单位面积质量增加一倍,其隔音量增加6dB。对于双层板,增加的斜率会更高,增加12-18dB。
STL=20log(m*f)-42.5 m-单位面积质量;f-频率
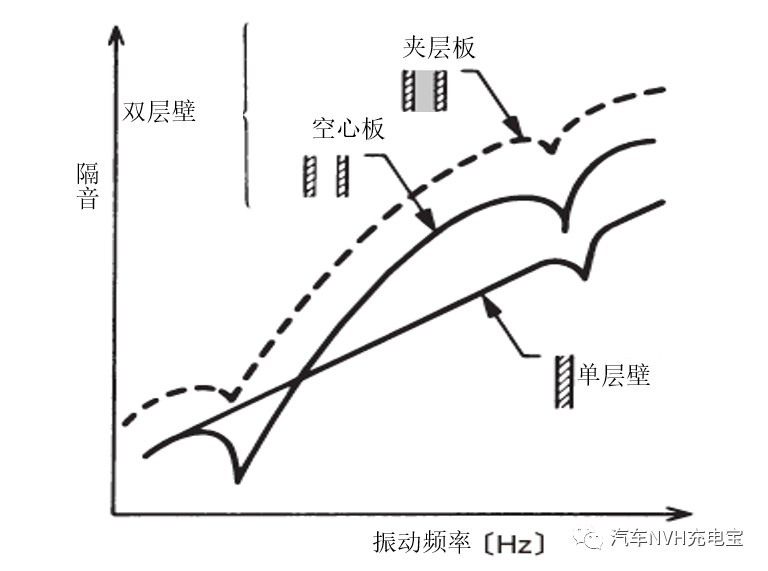
可以看到如果要增加零件的隔声性能,必须要要增加质量,不存在一个轻量化的方案,还能提升性能的,简直是天方夜谈!就在这里性能工程师就跟重量工程师结下了恩怨!
在前面如何进行汽车声学包的正向设计中,我们介绍了声学包装工程师应该具有系统思考的能力,在这里就派上用场了。真实的汽车声传递损失不单单是一个零件决定的,在文献1中,建立了一个混响-消声模型,利用统计能量法(SEA)推导了整体的声传递损失表达式。
从源头到接收者整个路径上的传递损失是由三部分组成的,声源附近的吸音、路径上的隔音和接受者附近的吸音组成。所以针对前面提到的问题,似乎找到一个完美的答案。提高吸音性能来弥补因减重导致的隔音降低,从而提高整个系统的声传递损失,简单的说就是“以吸代隔”。上述推导是严格遵行数学原理的,所以从数学上找到了轻量化的合理性解释。
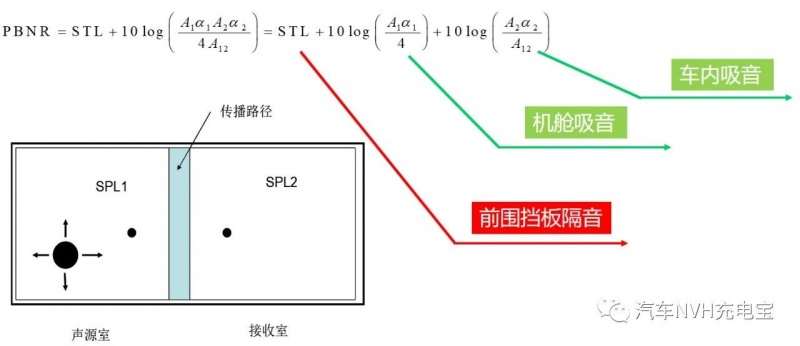
轻量化设计的思路和策略
声学包装轻量化策略主要从以下三个层面上进行。
· 整车级层面:注重于目标最优分解和布置位置的最优分配;
· 总成级层面:注重于对于某一个区域的主要部件进行厚度分布、材料组合配置。
· 材料级层面:注重于超细纤维材料的工艺制造与研发
①整车层面优化设计
车内噪声成分主要组成有两类:空气声和结构声。声学包装主要解决的中高频噪声问题,在汽车上,通常以400-10KHz频段来进行评价,它是一个宽频带声源,不针对某一个的单频的声音。对于400Hz以下的声源,效果就很有限。即使使用再多的材料,也不会以很好的效果,所以对于主机厂整车性能开发而言,如何将车内的中高频噪声分离出来,性能目标设定的不冗余,那么这就是轻量化设计的第一步。
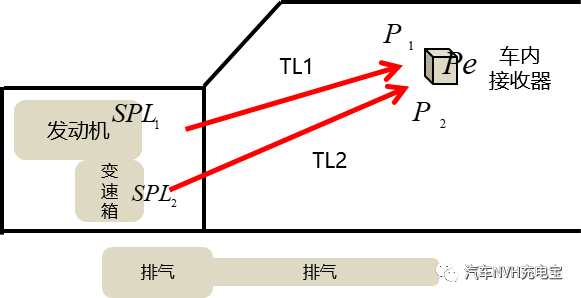
分离结构声和空气声常用的方法就是TPA(传递路径分析)。得到车内噪声的这个目标后,再根据声源的位置设定分区域的目标,比如针对动力总成噪声设定前围隔音指标(PNR),针对轮胎的辐射噪声,设定轮胎隔音指标(TNR),针对排气噪声设定指标(ENR)。针对前围隔音,在通过贡献量分析(CA),分解到前围区域、脚踏区域、前风挡区域和前侧位区域和机舱区域分别再设定插入损失(IL)或者吸音量(Ab)指标。这里面可以用到优化算法。以车内声学包装零件重量为目标,以噪声为约束条件,以零件的插入损失和吸音量为优化变量,就可以优化计算得到各个板块的最优目标。整车层面上更关注性能的分解和优化。
②总成零件优化
针对每一个区域的隔音目标,那么如何对结构进行设计才能达到目标要求。这一层级的就是总成级的优化。比如分解到内前围的插入损失指标是10dB,那么如何选择合适的材料和结构设计才能达到要求。
常用的内前围材料,一般都是以下三种材料组合:
1、重层质量耦合结构:可变密度质量层优化
2、吸音-隔音-吸音结构:嵌入纤维或者发泡材料的三明治结构, 吸音和隔音混合匹配
3、双阻抗耗纤维耗散结构:软硬层纤维搭配,偏重吸音型轻量化
以上三种组合成的总成重量一次是从重到轻,其隔音性能是逐步降低的,但是吸音性能是逐步提升的。所以针对不同的目标要求和声源特性,需要进行最佳的匹配。
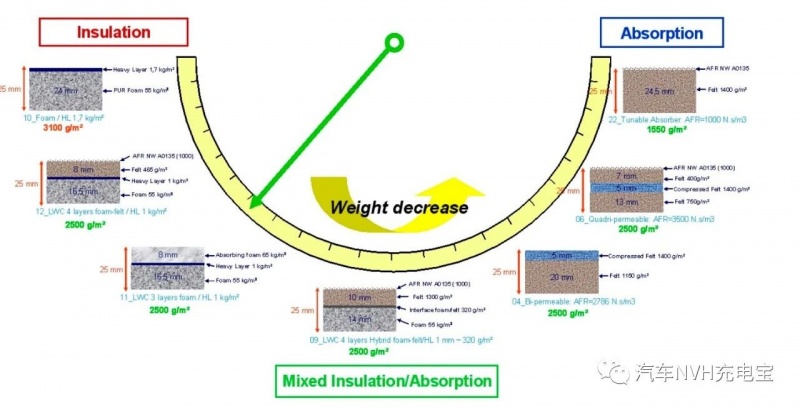
在一些国外的知名汽车公司,在平台架构研发阶段根据内燃机的型号和车型定位,基本就制定好了不同平台下不同车型的材料组合。比如针对豪华车车型,就偏向于选择传统隔音型,以发挥最好的静音效果。对于中低端产品,可以逐步向耗散型吸音材料下探,做到性能和重量的平衡。当然在平台架构开发阶段,空间和位置都已经预留好了,就已经考虑到了声学包装性能的发挥潜力,所以到了车型开发阶段工作就少了很多。
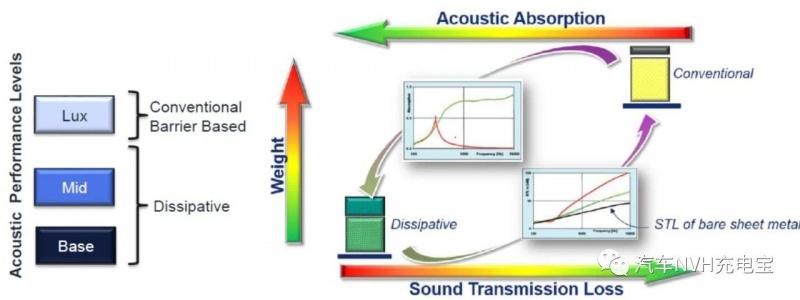
3、材料级轻量化设计
吸音材料大部分是由纤维类和棉毡类材料组成的,纤维类材料主要聚氨纤维(polyester)、聚丙烯纤维(polypropylene)和玻璃棉(fiber)等化学合成材料,棉毡类主要有废纺毡(shoddy)、棉毡(cotton)。由于对车内用材的环保性能的要求,所以汽车上主要用到的就是纤维类材料。
纤维类根据直径大小可以分为粗纤维和超细纤维,由于粗纤维具有良好的流阻性能,所以具有更优的吸音性能和重量优势。这部分的轻量化研究主要就是供应商进行的,比如超材料的性能研究。
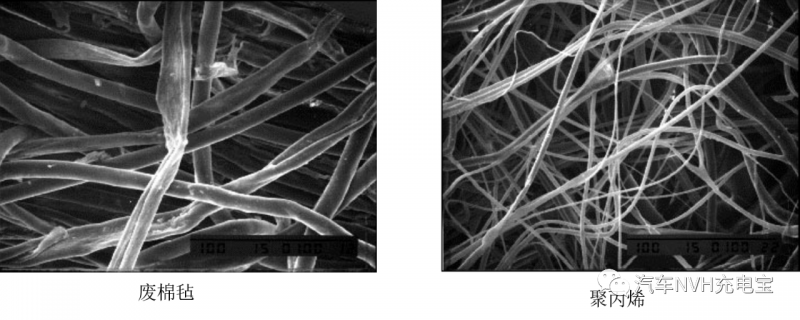
电动汽车的轻量化设计
电动车由于没有了内燃机,噪声源辐射能量变小了,是否可以更容易的推广轻量化方案?这样理解是片面的,我们从两个方面来进行解释
· 声源的变化:电动汽车由于没有内燃机的隐蔽效应,路面噪声和风噪声车内噪声将更加突出,在加速时的电机啸叫、机舱内的各种辅机和热泵的噪声也凸显出来,所以在底部隔音和声源位置包裹显得更加重要。但是有一点的是对于电动车内前围对中低频的隔音要求放松,主要对中高频噪声的阻隔,所以可以选择轻薄、偏重于吸音性能的材料组合。
· 车内声场的变化:很多电动车配备了主动降噪系统和车内的主动发声音效设计,还有比如向奥迪e-tron的8D环绕音效,这些功能配置最大潜力发挥就更需要使车内的静音性需要做的更好。
e-tron是奥迪的首款电动车型,它的声学包装的配置基本可以窥探到一些新能源车型的控制策略。动画配图可以参考奥迪e-tron的声学材料布置那一期视频中,它在声学包方面设计付出了不亚于传统车的配置,主要特点有:关注与声源处的降噪处理,包括对前后电机的包裹,对于前围和地毯仍然采用的是重层+发泡组合质量弹簧耦合传统配置。
综合以上,不见得新能源车型就比传统车在声学包装配置方面可以放松。
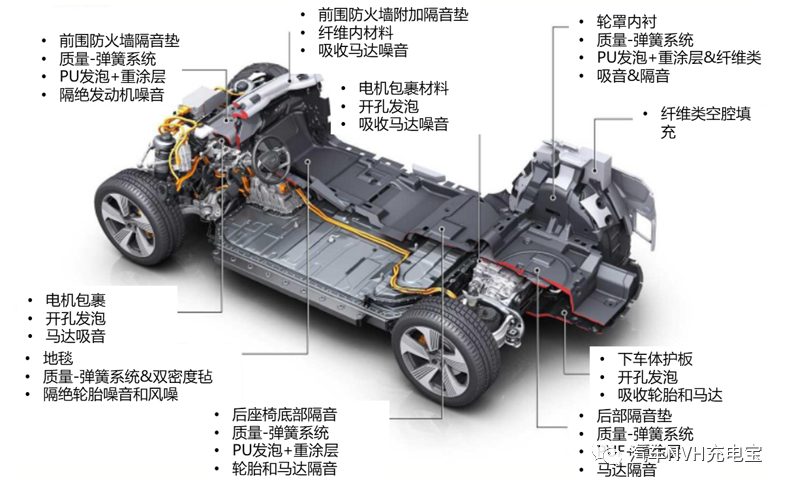
总结:
1、声学包装轻量化策略主要从以下三个层面上进行:整车级、总成级和材料级层面。整车层面注重于目标最优分解和布置位置的最优分配;总成级注重于对于某一个区域的主要部件进行厚度分布、材料组合配置。材料级注重于超细纤维材料的工艺制造与研发。
2、对于电动车车型,由于声源的变化和车内声场的更高要求,需要车内的基础静音性能做得更好,因此对声学包装的设计可能会更加精细和苛刻。
参考文献
1 Power-based Noise Reduction Concept and Measurement Technique SAE 2005-01-2401
2 Generalized Light-Weight Concepts Improving the Acoustic Performance of Less than 2500 gm2 Insulators SAE 2009-01-2136
3 An Acoustic Target Setting and Cascading Method SAE 2019-01-1581
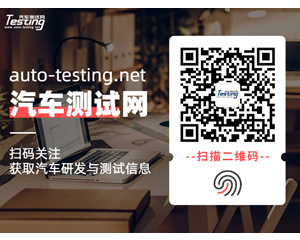
最新资讯
-
2025 汽车测试及质量监控博览会(中国)盛
2025-08-29 13:28
-
达安中心全景环视系统测试能力全新升级,筑
2025-08-26 19:28
-
ATE展会倒计时:迷你研讨会
2025-08-26 19:26
-
在竞技环境下,奇石乐先进测量技术亦能提供
2025-08-26 10:24
-
从创新的赛车六分力传感器到海量数据的高效
2025-08-26 10:21