高速直喷柴油机采用高喷油压力提高升功率的潜能
发动机小型化是提高效率最有前途的方法之一,由于发动机排量减小需要更大的升功率。研究基于具有代表性的乘用车的原型机IFP的单缸机的试验工作开展。在高热机负荷约束下,该机可达到非常高的升功率。在原型机高压共轨设备压力允许范围内(可达250MPa)对全负荷及部分负荷工况点开展试验。
结果表明,在全负荷工况,通过提高喷油压力来增加燃油速率比增大喷孔直径更有优势,这主要是由于较小的喷孔直径可以改善空气卷吸。当发动机的热机负荷受到更大限制,且有增压系统时,提高喷油压力体现的优势更加突出。最后,结合高喷油压力、高增压压力以及高爆压,升功率可高达85-90kW/L,燃空当量比可实现0.9。
介绍
在能源危机及石油储备限制的环境下,研究减少不可再生能源的消耗成为日益关注的焦点。昂贵的石油价格迫使全球消费者将目标转向低油耗的乘用车。此外,备受关注的全球变暖问题及燃油消耗与温室气体排放之间的关系促成乘用车严格的CO2排放法规。欧盟委员会提出将在2020年达到每年减少95g/km的CO2排放量。该目标意味着将在1990年的基础上将油耗降低50%。为了同时满足环境问题和消费者的选择需求,提高汽车应用的燃油经济性成为这十年来优先等级最高的事项。
各种新的或是改善动力系统的技术都被用来提高车辆燃油经济性,对于柴油机而言,小型化是潜在的最为高效的策略之一。小型化是指采用较小体积的发动机在较高升功率下运行从而实现较低的燃油消耗。通过发动机小型化实现燃油消耗降低的原因主要有两点:一是发动机在高负荷工况时效率较高,二是发动机尺寸减小后摩擦损失降低。
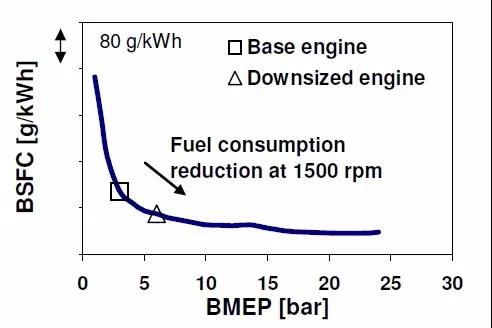
图1 IFP €5应用发动机在恒转速1500rpm时的BSFC与BMEP关系曲线
自汽车工业开始发动机逐步向小型化发展,该技术逐步依赖于技术可用性[1]。例如,汽车制造商标志雪铁龙集团用1.6L排量的DV6发动机(80kW,240Nm)取代了第一代生产的1.6L排量的DW10发动机(80kW,250Nm),并将CO2排放降低了10%。雷诺也用1.5L排量的K9K发动机(78kW,240Nm)替代了原来的1.9L排量的F9Q发动机(74kW,240Nm)。
然而,为了维持消费者需要的性能水平,现代柴油机的升功率将得到显著提升。考虑到目前发动机的升功率平均水平为55kW/L,若在同款乘用车上用1.5L的发动机替代2.2L的发动机,那么升功率必须提高到80 kW/L才能保持功率输出一致。为使这项工作向前推进,我们的目标是将升功率提高到90kW/L。
提高发动机升功率需要高燃油喷射率。高燃油喷射率可以通过不同的路径实现。这项工作研究了与增大喷孔直径相比,提高喷射压力在全负荷工况时提高升功率的潜能,同时也是发动机向小型化发展的必要步骤。
由于判定哪种技术在部分及全负荷工况时有最佳的折衷是非常重要的,因此对部分负荷下增大喷孔直径的潜能也做了相应研究。一方面,已经在柴油机上证明了高燃油喷射压力可有效降低碳烟排放[2.3.4.5]。另一方面,增大喷孔直径也被证明了在部分负荷工况时碳烟排放增加。论文中给出了可以证明上述结果的例子。
为了保证部分与全负荷工况有较好的折衷,需要对小型化的发动机燃烧系统进行优化。压缩比、燃油液相流速、喷孔数目及燃烧室几何结构等均为优化参数。为了优化部分负荷工况点,同时又能在全负荷时保持较高的升功率,针对不同发动机开展了大量试验。其中,燃烧系统由原机压缩比为18:1的窄口燃烧室(径深比为2.6)调整为压缩比14:1的敞口燃烧室(径深比为3),因此实现了较好的性能[6]。
除了高燃油喷射率外,其他方法也可提高升功率。全负荷时可还可以通过提高增压压力或者爆压来提高升功率。试验在增压压力、爆压及喷油压力的大范围变化基础上开展,三者组合优化达到最大的升功率[7]。
最后,通过对一台单缸机进行结构改进,使其在能够承受高水平的热机约束基础上实现高升功率。
试验设置
试验机型
针对三种不同单缸机开展试验,各机型技术参数如表1所示。
表1 单缸机技术参数
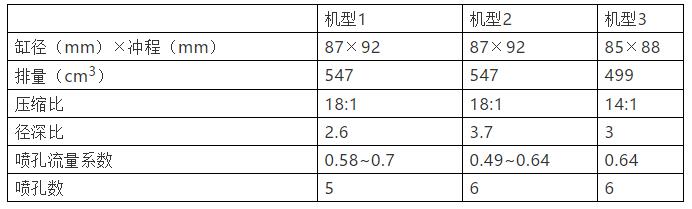
燃油
试验用油为EN590柴油,相当于常见的含硫量较低的(<10ppm)欧洲柴油(低热值42.8MJ/kg,密度835kg/m3,15℃)。
喷射系统
试验在Delphi超高压共轨系统(250MPa)上开展。该喷射系统原型的基础是DelphiMultecTM DCR[8],在研究开发初期将它设计为在160MPa(图2)时运行。
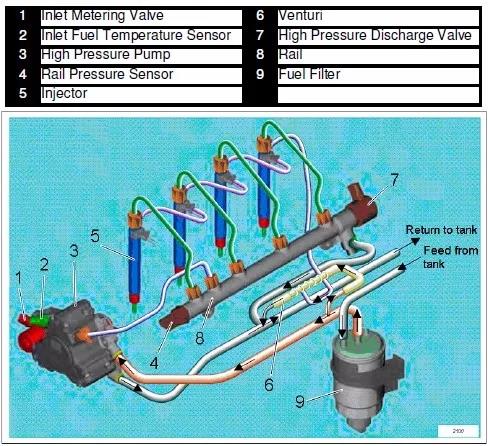
图2 DelphiMultecTM DCR高压共轨系统
低压转换泵集成在高压油泵上,通过滤清器从油箱中吸入燃油。燃油运送到高压油泵腔后由入口处的计量阀控制。ECU通过对比由安装在轨上的高压传感器监测到的实际压力,驱动入口计量阀精确跟随目标轨压。燃油随后经由轨和高压油管进入喷油器。
该喷油器基于运用快速平衡电磁阀概念的DFI1(图3)。正因为DFI1的尺寸小,执行器可以直列安装且位置非常靠近针阀从而能够快速起动并且精确测量。这项喷油器技术还支持低压回油,可提高液力效率最终达到非常高的压力性能。
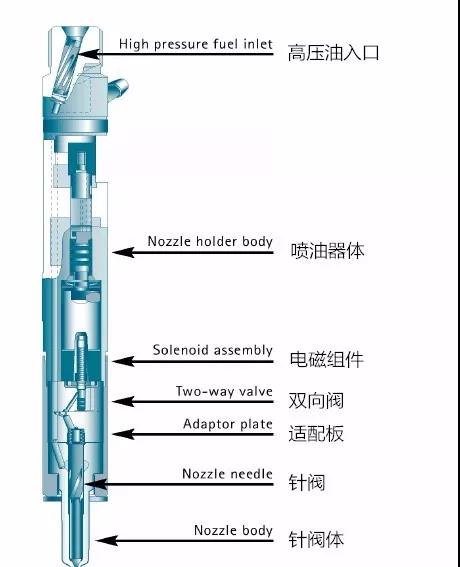
图3 Delphi DFI1快速电磁喷油器
为了达到目标喷油压力250MPa,需要在原机基础上做一些调整。采用一种新的具有更大压力范围的轨压传感器,同时为了安全性,需在轨上集成一种可以快速卸压的高压阀。产品应用上优先使用低成本的卸压阀喷油器策略,因为它能更好的适应单缸机运行。高压泵经过调试以适应更高的压力。原型喷油器系统经过验证确保有足够长的寿命来完成燃烧试验研究。图4所示为用于本研究的原型系统的液力循环。与传统高压共轨相比,将一些传感器(流量、温度、压力)集成为一体用来监控在单缸机运行期间系统的状态。在低压循环上集成一种水冷的燃油热交换器保证系统在正常的入口油温运行。

图4 高压喷油系统液力循环结构图
测试设备
试验台包含调节供给发动机的空气、燃油、机油及水温在内的标准控制系统,试验环境与四缸机类似。进气流量由音速流量喷嘴控制,分别对进、排气压力进行控制。发动机排放由标准的气体分析仪测量。发动机内部安装缸压传感器。通过对缸压曲线进行IFP编码计算得到放热率(ANADID)。
试验条件
试验在部分及全负荷工况下开展。通过逐渐增加的喷油量完成不同燃空当量下的全负荷试验(4000rpm)。喷油始角由爆压确定。4000rpm全负荷时的碳烟等级限制为3FSN(滤纸烟度值),该限制值的选择与微粒过滤器的载量和汽车制造商的要求有关。全负荷试验时没有采用EGR。
由于单缸机的摩擦损失不同于四缸机,所以平均摩擦压力(FMP)确定如下:
FMP=2.0 bar (4000rpm全负荷)
通过该方法,四缸机的平均有效压力(BMEP)可根据发动机的摩擦损失计算得到。这里提及的摩擦损失没有考虑缸压高带来的活塞部分摩擦损失或是喷油压力提高到160MPa以上后需要的能量增加量。
因为排气流量下降及管道连接长度不同导致单缸机的排气温度低于四缸机。两者的排气温度(Te)有以下经验公式:
Te4-cylinderengine= Te1-cylinderengine+40℃
尽管在单缸机上完成试验,但论文中的提出的试验结果代表了四缸机也可能得到的结果。针对两部分负荷运行工况开展了试验:1500rpm-0.3MPaBMEP,2500
rpm-0.8MPa BMEP。为保持相同的噪声等级,所有的喷油设置(喷油时刻,喷油压力和喷油持续期)都进行了优化。主要目的是为了找到排放(NOx、CO、HC、soot)与油耗的最佳折衷。
详细的试验条件如下表所示。
表2 试验测试条件
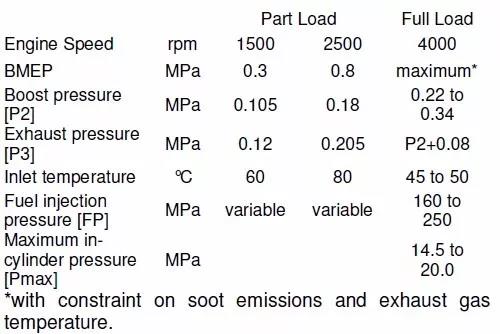
结果
提高喷油压力与增大喷孔直径对比
柴油机全负荷性能在高转速时受到排温或者碳烟排放的限制(>3000rpm)。排温受限于机体部件及增压设备的热机特性,只可能通过改善材料属性和发动机设计来增大极限值,但会因此给增压器集成、可靠性和成本来带问题。爆压确定后,排温主要取决于喷入的及其参与燃烧的燃油量,还有燃烧相位。提高燃油速率有助于加快燃烧速度。这意味喷油量相同时,通过喷油器提高燃油速率可加快燃烧速度。通过此方法,后燃期提前完成,可燃气体有更多的时间来膨胀最终降低排温。
燃烧过程中的碳烟排放受限于微粒捕捉器(DPF)容积(填充物和再生物)。全负荷高转速下,碳烟排放受到后期氧化持续期的强烈影响。提高燃油速率有助于降低碳烟水平:当燃油速率增加时,尽管可以通过延迟喷油时刻来保持爆压相同,燃油喷射和燃烧过程完成较早可为碳烟后期氧化提供更多时间,因此最终的碳烟水平会下降。高转速时,由于大部分燃烧过程发生在混合控制阶段,因此全负荷工况时燃烧过程与喷油终点紧密相关,碳烟水平也因此与喷油终点密切相关。试验在相同的燃空当量比0.65下进行。随着增压压力从0.22变化到0.26MPa,爆压从14.5MPa变化到15MPa。图5所示为碳烟水平与喷油终点的关系:随着喷油延迟碳烟排放增加。
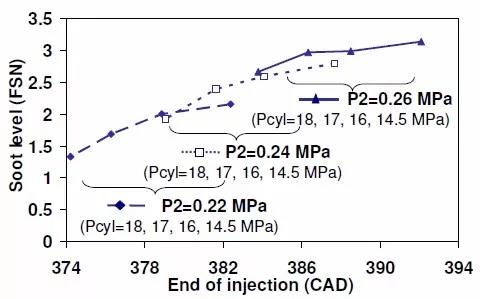
图5 碳烟水平与喷油终点的关系图
FP=200MPa,P2=0.22~0.26MPa,Pmax=14.5~18MPa燃空当量比0.65.4000rpm全负荷工况,Engine1。
在没有延迟燃烧过程的前提下,燃油速率增加使得进入缸内的燃油数量增加,可实现更高性能。
燃油速率是提高升功率的主要因素。燃油速率可由不同途径提高:采用更高液压速率的喷油器(也可增加喷孔数量或直径)或是采用更高的喷油压力。论文不对增加喷孔数量开展研究。下一步重点对比分析喷油压力与喷孔直径对提高燃油速率的影响。喷油压力受限于喷射系统技术。试验中的喷油压力最高到250MPa。试验中碳烟值限制在3FSN或者排温限制在830℃。这些值是未来发动机具有代表性的限制值。
高喷油压力结果
试验由两部分组成:在1号机上首先将喷油压力从160MPa提高到200MPa,随后在2号机上将喷油压力从200MPa提高到250MPa。如图6所示,升功率随着喷油压力提高不断增加。在喷油压力200MPa时升功率在两台发动机之间的增长变化可用燃烧系统优化来解释说明。
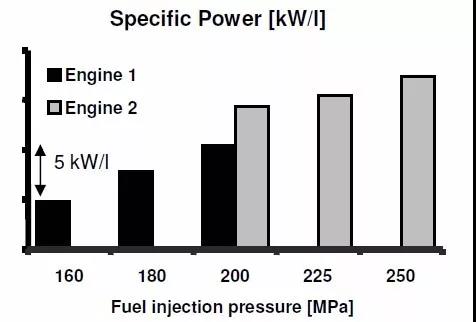
图6 4000rpm全负荷下喷油压力对性能的影响
P2=0.24MPa Pmax=16MPa 3FSN Te=830℃
提高喷油压力升功率提高增大的原因有以下两点:
1、燃烧速率增加
2、在碳烟排放水平(3FSN)或排温(830℃)限制范围内,最大燃空当量比增大。
为进一步说明效率提高,图7对比了200MPa和250MPa喷油压力下的试验数据,其中燃空当量比均为0.74。燃油喷射量一定时,提高喷油压力喷油持续期缩短。已被证明当喷油压力提高时空气/燃油混合速率不变[9,10]。喷油速率提高,混合控制持期缩短(表3)。为保持爆压相同,喷油时刻延迟但燃烧相位近似。所以,较短的燃烧持续期和相似的燃烧相位导致循环效率提高。
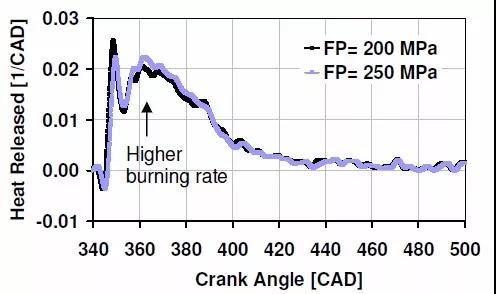
图7 4000rpm全负荷喷油压力对放热率的影响
P2=0.24MPa Pmax=16MPa 燃空当量比0.74 Engine2
表34000rpm全负荷喷油压力对燃烧速率的影响
P2=0.24MPa Pmax=16MPa 燃空当量比0.74 Engine2
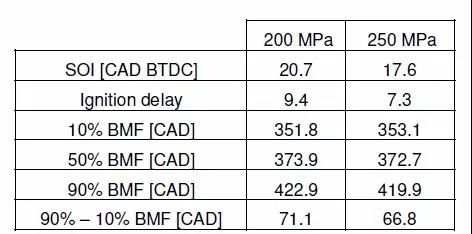
燃烧过程加速带来的另外一方面的积极效果是碳烟水平降低,这是因为喷油压力较高时,碳烟后期氧化可获得更多的时间,加快混合速度,同时也可看到排温有所降低。
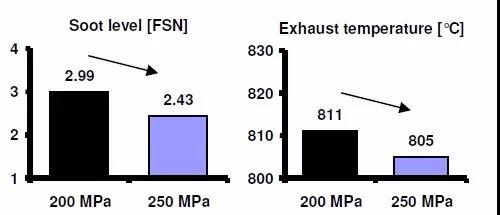
图8 4000rpm相同燃空当量比0.74时喷油压力对碳烟水平和排温的影响
P2=0.24MPa Pmax=16MPa Engine2
在碳烟限值(3FSN)或排温限值(830℃)前提下,高喷油压力需要更高的燃空当量比。这种影响与效率提高(相同燃空当量比)一起使得升功率提高。图9举例说明如下:当喷油压力从180MPa提高到250MPa,在碳烟水平为3FSN时升功率提高10%。
燃烧过程如图9所示便于解释以上结果。
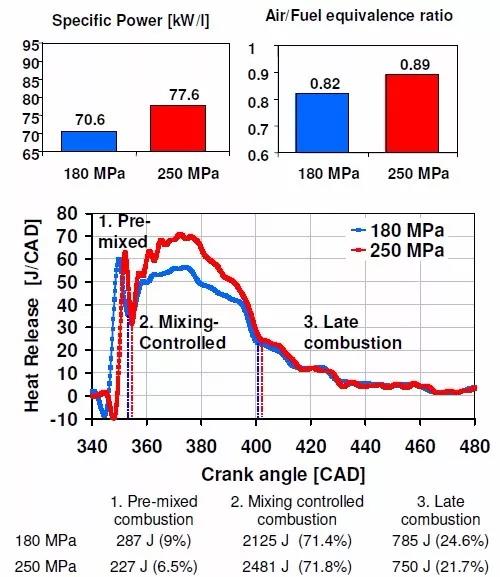
图9 喷油压力影响
P2=0.28MPa Pmax=17MPa 3FSN Engine2
1、为保持爆压17MPa,喷油压力为180MPa时,喷油时刻从19°CABTDC推迟到14°CA BTDC。喷油压力越高,燃烧始点越接近上止点,同时由于二者燃烧终点接近,因此喷油压力提高高循环效率更高。
2、180MPa时喷油量为74.7mg/st,250MPa时喷油量为82.4mg/st,通过对比喷油量显著升高,导致相当高的燃空当量比0.89(或空燃比1.12)。250MPa喷油压力混合控制期的放热率更高。表明喷油压力对燃烧速度和效率影响较为明显。
3、两种喷油压力下的燃烧后期的放热率相似,因此后期氧化持续期基本相同。
高喷油压力下,保持喷油终点相同,燃油喷射量在碳烟限值内可能因为混合控制期燃烧过程加快而增加。喷油压力从180MPa提高到250MPa循环效率提高,燃空当量比提高(7%),升功率提高10%。如果该结果可以保持到喷油压力250MPa以上,将会达到更大的升功率。
增大喷孔直径的影响
为了对比提高喷油压力与增大喷孔直径的影响,在保持喷孔数量一致的前提下,在燃油液相流速为0.58~0.7L/min/范围内开展试验。当通过增大喷孔直径增加燃油速率时:燃烧持续期缩短从而加快燃烧过程。燃空当量比相同时,升功率的增加与喷油压力无关(图10)。如图10所示,燃空当量比为0.66时,燃油液相流速升高升功率也随之提高。
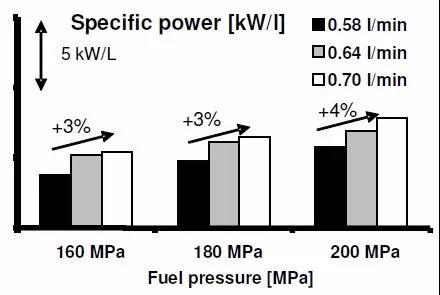
图10 喷孔数目相同时燃油速率对升功率的影响
P2=0.24MPa 燃空当量比0.66 Pmax=16MPa Engine1
图11所示为燃空当量比0.66时燃油速率0.58L/min和0.70L /min两者对放热率的影响。结果表明喷孔直径可加快燃烧速度。二者燃烧始点接近,燃油液相流速提高燃烧持续期缩短,燃烧效率提高。
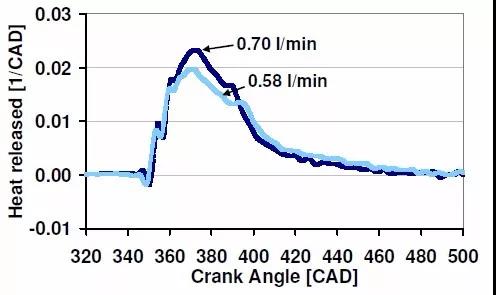
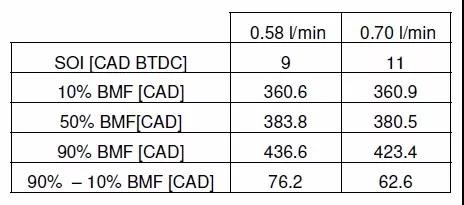
图11喷孔数量相同时燃油液相流速对放热率的影响
燃空当量比0.66 P2=0.24MPa Pmax=16MPa FP=160MPa Engine1
由于燃烧终点提前,碳烟排放也随液相燃油流速增大而降低。对喷油压力而言,在碳烟水平限值为3FSN时升功率提高的潜能来源于燃空当量比增大后效率的提高。
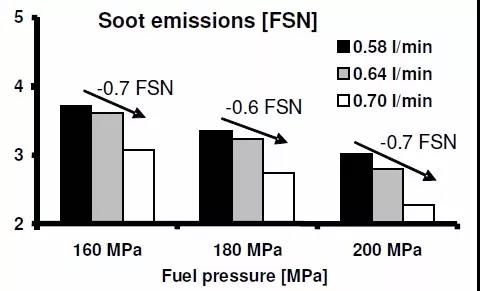
图12喷孔数量相同时燃油液相流速对碳烟排放的影响
燃空当量比0.66 P2=0.24MPa Pmax=16MPa Engine1
哪种方法更有利于提高升功率?
这部分内容主要对比通过增大燃油喷射压力与增大喷孔直径对燃油流速的影响。图13所示为升功率与燃油喷射压力和燃油液相流速之间的关系结果,仅考虑碳烟限值为3FSN时的结果。当提高喷油压力或燃油液相流速时升功率提升范围为5%~20%。正如预期结果一样,喷油压力和液相流速时同时增大时升功率达到最大。当喷油压力从160MPa增大到250MPa喷油速率增大9%。当增大喷孔直径使得液相流速从0.58增大到0.7L/min时喷油速率提高20%。试验在相同的喷油试验台上进行。下一步研究对于相同的燃油速率增加,究竟哪种方案引起了升功率的提高。
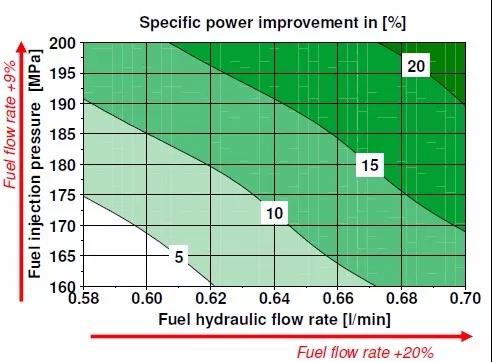
图13 4000rpm全负荷工况喷油压力和喷油速率对升功率的影响
P2=0.24MPa Pmax=16MPa 3FSN Engine1
碳烟机理较复杂,为了全面解释最终的碳烟水平需要考虑许多因素。如图5所示,高转速全负荷时喷油终点决定了燃烧终点和后期氧化持续期,因此对碳烟水平的影响非常明显。在3FSN试验中,假设将喷油终点作为影响碳烟的唯一因素,并在喷油相位和喷油持续期中作为参考,这样有可能推断出其他试验条件(燃油速率和喷油压力)下碳烟水平为3FSN时的的当量比。推断出的当量比叫作“理论”燃空当量比。当喷油压力为160MPa,喷油速率为0.56L/min时由喷油相位和喷油持续期导致的碳烟水平为3FSN时,该理论当量比可以计算出来并且认为在其他试验条件下均为恒定值。因此在没有改变喷油终点的前提下喷油速率的增加可能引起喷油量的增加,所以碳烟水平一直保持在3FSN。升功率也因此受限于被吸入缸内的燃油量。
针对其他试验条件对碳烟水平的限制值3FSN开展试验。燃空当量比通过尾气分析仪测得,因此该结果包含了碳烟产生和后期氧化过程在内的所有机理。图14所示为在碳烟水平为3FSN的试验中测得的燃空当量比(红虚线)与通过恒定的喷油相位和持续期计算得到的理论当量比(绿线)的对比结果。正如预期结果一样,因为只考虑了喷油终点两条曲线明显不同。然而,该结果对探讨这些不同点的原因有很大帮助。
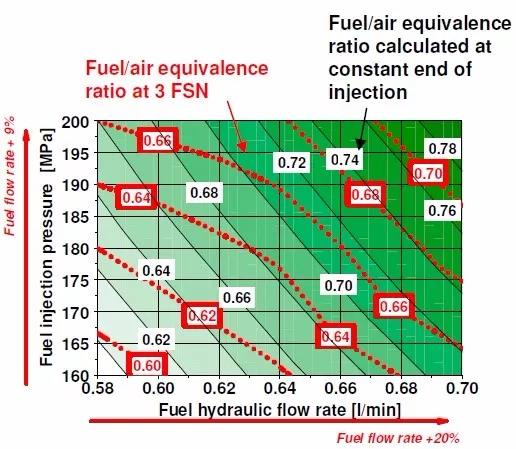
图14 4000rpm全负荷下喷油压力和喷油速率对燃空当量比的影响
P2=0.24MPa Pmax=16MPa 3FSN Engine1
一方面,图14的结果表明了在碳烟水平为3FSN时喷油速率从0.58L/min增加道0.70L/min时能够引起燃空当量比3%的增长率。在相同的喷油速率之间,理论燃空当量比可增加20%。在该方案中,即使喷油速率增加20%,实测的当量比只增加10%。另一方面,喷油压力从160MPa增加到200MPa时(燃油速率增加9%)实测当量比增加9%,“理论”当量比也同样增加9%。在该方案中,喷油压力的增大完全转化成燃空当量比的增加。然而,当增大喷孔直径时,燃油速率的增加仅有部分转化为燃空当量比的增加。
结果可用混合喷射过程中喷孔直径的影响来解释。喷射中的燃空当量比与喷孔直径成比例,但不受喷油压力的约束[11,12]:
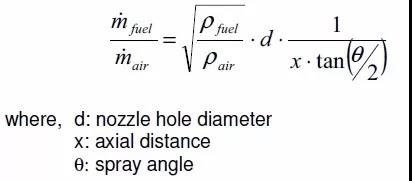
增大喷孔直径在喷射过程中产生较高的当量比,对碳烟形成有增大的趋势。
这种影响会抵消由于喷油速率提高带来的喷油结束早的优势,因此通过增大喷孔直径增大燃油速率的优势会被减弱,相反的,高喷油压力不能改变在喷射过程中的燃空当量比,因此可有利于燃油速率的增大。
另外需要考虑部分负荷结果。部分负荷时,为获得最好的发动机运行环境,喷油压力可能会被改变。然而,作为定义燃烧系统时包括在内的因素,喷孔直径不得不用来作为折衷部分负荷与全负荷的因素。
试验在部分负荷工况、不同喷油速率下进行,对于喷油速率试验,当降低PM排放时,为了得到相近的NOx排放结果、BSFC及噪声水平,需对发动机设置做一些优化。结果如图15、16所示,喷孔直径越大,碳烟排放越高。
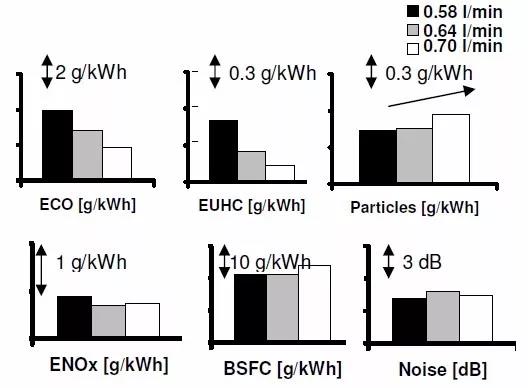
图15 部分负荷喷油速率的影响
1500rpm BMEP0.3MPa EGR25% Engine1
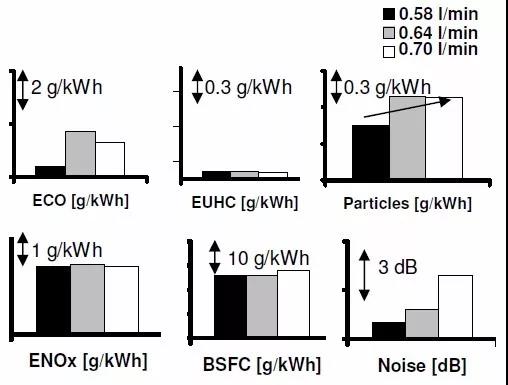
图16 部分负荷喷油速率的影响
2500rpm BMEP0.8MPa EGR22% Engine1
中低负荷时,由于转速较低,碳烟后期氧化的时间远多于4000rpm。因此,喷射过程中的燃空当量比对碳烟排放的影响比后期氧化持续期更为重要。1号机压缩比为18:1,尽管在低负荷时,燃油燃烧仍在混合控制燃烧期内占主要部分,因此喷射过程中的燃油当量比主要影响碳烟排放。这样就可以解释增大喷孔直径不利于颗粒排放。
综上所述,4000rpm全负荷时,通过提高喷油压力增大燃油速率是更好的提高升功率的方法。与通过增大喷孔直径提高燃油速率相比,在部分负荷保持低碳烟排放时,高喷油压力对提高升功率具有更大的潜能。部分与全负荷最好的折衷方法是,全负荷时采用高喷油压力,同时保持喷孔直径不增大来保证部分负荷时低碳烟排放。
采用高爆压和高增压压力在全负荷时提高升功率
除了超高的喷射压力,还可通过其他路径在高转速时提高升功率,比如增大增压压力或增大爆压。由于受到技术限制,最大的增压压力和爆压在全负荷工况时是硬性限制因素。应用单缸机的优势在于可以灵活调整增压压力,但是车用发动机采用高增压压力时意味着涡轮增压器的匹配和涡轮增压的能力。增大爆压则意味着要设计出能够承受较高的热机载荷的发动机。
提高增压压力,空气量增大,燃烧室内能够获得更多的空气从而使得碳烟排放降低。提高爆压可得到更好的燃烧相位,最终可改善燃烧过程并带来碳烟后期氧化持续期的潜在增加。
为测度在4000rpm全负荷时对增压压力和爆压对升功率的影响力,试验在1号机上开展,碳烟排放限值在3FSN以内。
高爆压
爆压从14.5MPa增加到18MPa。调整喷油量使得各试验点的碳烟排放保持在3FSN。升功率可提高8%。最大燃空当量比从0.69增大到0.74。
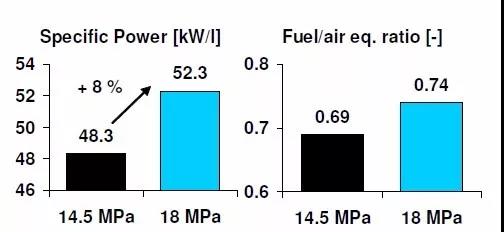
图17 爆压的影响
P2=0.22MPa FP=200MPa 3FSN Engine1
以下结果可由图18分析得到:
1、爆压18MPa时,喷油始点从爆压14.5MPa时的8°CA BTDC提前到16°CABTDC(表4)。喷油时缸内的热力学条件不太利于喷入的燃油自燃。因此,在预混合阶段积累的燃油量增多。
2、混合控制阶段二者的放热率基本相同。爆压为18MPa时,燃烧过程开始和终了都较早,为碳后期烟氧化留下更多时间。因此,当保持碳烟水平值为3FSN时,该方案参与燃烧的燃油量更多。
3、尽管两种方案燃烧过程的持续期接近,但由于爆压高燃烧相位较好,因此循环效率提高。
本方案中,增大爆压有助于提高升功率,并且在3FSN时最大燃油当量比更高。
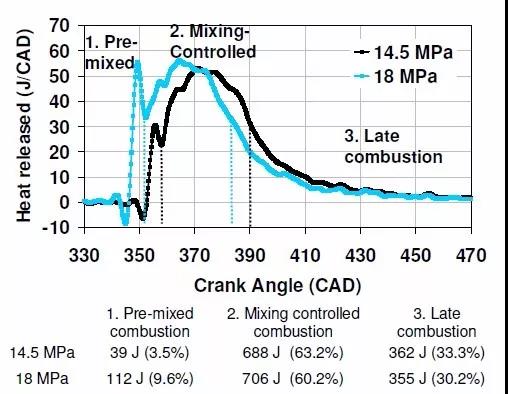
表4 爆压的影响
P2=0.22MPa FP=200MPa 3FSN Engine1
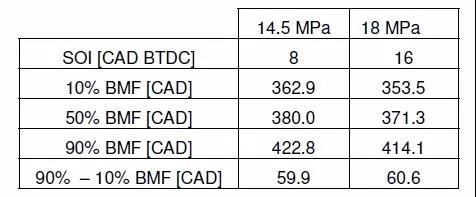
高增压压力
增压压力从0.22MPa增大到0.28MPa。尽管采用高增压压力时最大燃空当量比下降,但是燃油喷射量显著增加。(0.28MPa时62.9mg/st与0.22MPa时55.5mg/st相比)。因此,提高增压压力可使升功率提高15%。
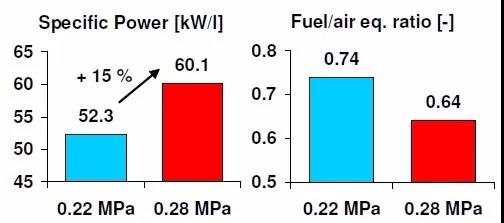
图19 增压压力影响
Pmax=18MPa FP=200MPa 3FSN Engine1
图20所示为燃烧过程中高增压压力的影响有助于理解以下结果:
1、高增压压力下,为保持缸压18MPa,喷油时刻推迟,此时缸内的热力学条件利于燃油自燃,因此预混燃烧阶段参与燃烧的燃油量减少。
2、混合控制阶段燃烧速度显著增加。燃烧持续期缩短时,随着燃油喷射,氧密度增加,积累了大量的燃油被消耗。
3、两种方案下的燃烧后期基本相同。增压压力提高后改善了混合控制燃烧阶段,并保持到燃烧终点,碳烟排放维持在3FSN尽管参与燃烧的燃油总量较大。
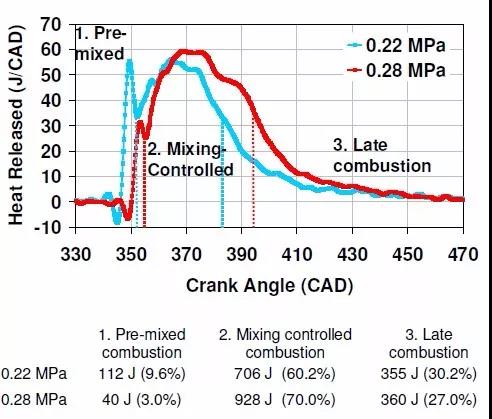
图20 增压压力影响
Pmax=18MPa FP=200MPa 3FSN Engine1
表5 增压压力
Pmax=18MPa FP=200MPa 3FSN Engine1
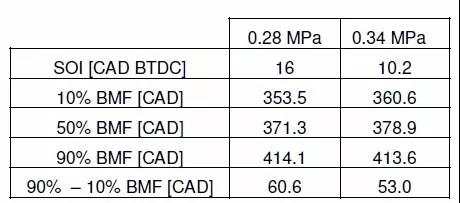
本方案中,增压压力从0.22MPa增大到0.28MPa可将升功率提高15%:高增压压力下燃油喷射量较大,功率输出较大,对燃烧过程进行优化可将碳烟排放保持在3FSN。
将增压压力、爆压与喷射压力结合起来优化升功率
通过提高增压压力或增大爆压可得到高升功率。在1号机上,保持碳烟水平3FSN开展更多运行工况(增压压力、爆压和喷油压力)的试验。这一部分主要有两个目的:
1、确定最大限度提高升功率的合理的组合[爆压×增压压力];
2、根据爆压和增压压力评估高喷油压力在发动机多工况条件下的优势。
图21所示为喷油压力160MPa时升功率、有效燃油消耗率与增压压力及爆压之间的关系。图21中有两个区域内的升功率没有显著提高。
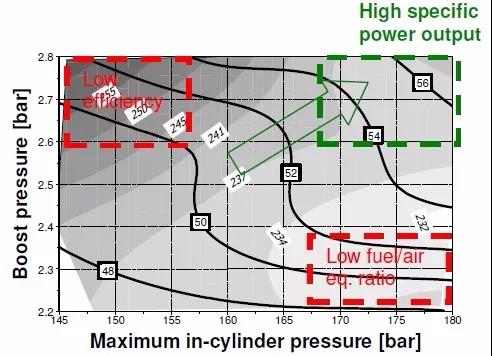
图21 4000rpm全负荷升功率和有效燃油消耗率与爆压及增压压力的关系
FP=160MPa 3FSN Engine1
1、低增压压力高爆压时:最大燃油当量比在3FSN时较低,这是因为大量的燃油喷到了燃烧室外(图22)。碳烟水平是制约升功率提高的主要因素。
2、高增压压力低爆压时:因为循环过程中的燃烧开始的太晚(为限制爆压喷油时刻延迟)燃烧效率偏低。
.jpg)
图22 喷油始角20°CABTDC时燃油喷射位置
图21表明当增压压力和爆压同时增大(斜箭头)可以提高升功率。
喷油压力较高时结果类似。当增压压力或爆压变化时在不同的喷油压力下开展试验以确定喷油压力对升功率的影响规律。图23所示为喷油压力200MPa时升功率和有效燃油消耗率与爆压及增压压力的关系。结果与160MPa时基本相同:当增压压力和爆压同时增大时可获得高的升功率。同时注意到两种喷油压力下低升功率的分布范围基本一致。
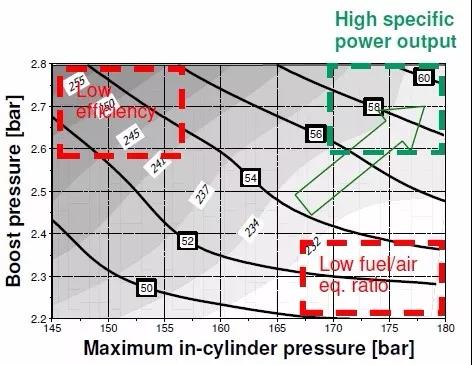
图23 4000rpm全负荷升功率和有效燃油消耗率与爆压及增压压力的关系
FP=200MPa 3FSN Engine1
图24所示为喷油压力从160MPa提高到200MPa时升功率的提高与增压压力及爆压之间的关系。与之前低升功率分布的区域相比,喷油压力增大后产生不同的变化。
1、增压压力低爆压高时,升功率增加量很小(3kW/L)如图22所示,在该区域为达到高爆压喷油提前角增大。因此,喷到燃烧室外部的燃油量增大带来高燃油密度和高碳烟排放。随着喷油压力升高,喷到燃烧室外部的燃油量更高,削弱了高喷射压力带来的优势。
2、增压压力高爆压低时,升功率比之前区域的高一些(4~6kW/L)。为限制爆压燃烧相位延迟,而喷油压力的升高有助于改善燃烧相位。
3、图24表明同时增大爆压和增压压力时提高喷油压力可显著提高升功率(>7kW/L)(箭头所指斜线部分)。
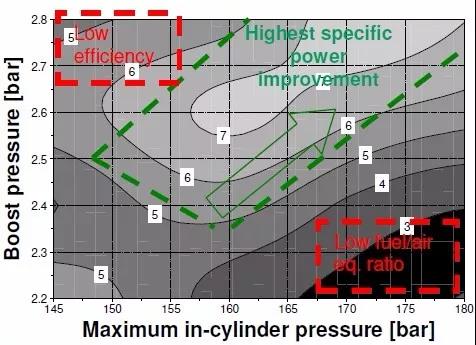
图24喷油压力从160MPa增大到200MPa时升功率增加
当喷油压力与高爆压高增压压力结合起来可大大提高喷油压力对于提升升功率的潜能。研究中没有规定爆压及增压力的限制范围。
突破技术极限达到更高的升功率
为达到升功率90kW/L的目标,要用到之前的结果趋势来规定比现在乘用车更高的增压压力和爆压。燃油喷射压力由DelphiDiesel Systems提供的燃油喷射系统所决定,最高可达250MPa。
正因为现在的乘用车受到机体热机负荷的限制,所以开发了一台可以承受高热机负荷压力的新单缸机。3号机由之前单缸机演变而来,其燃烧系统作了以下几个方面的优化:
1、压缩比从18:1降低到14:1。压缩比降低允许全负荷工况下在爆压相同时改善燃相位,从而在部分负荷时通过降低燃烧温度减少NOx排放。
2、在规定喷油器技术(NTP、喷孔锥角、喷孔数、燃油速率)的同时对燃烧形状进行优化以便兼顾部分负荷时最大升功率的要求。
3、为了保证部分负荷与全负荷有更好的折衷,精选出的喷油速率为0.64l/min@10MPa(对于升功率90kW/L而言该值非常低)。相比之前发动机对喷孔几何形状也作了优化,相同的喷油速率和喷孔数目下,优化后的方案喷孔直径更小。
试验在喷油压力250MPa,、增压压力0.34MPa、爆压20MPa下进行。这些值的选取是为了在碳烟限值3FSN内获得最大的升功率。
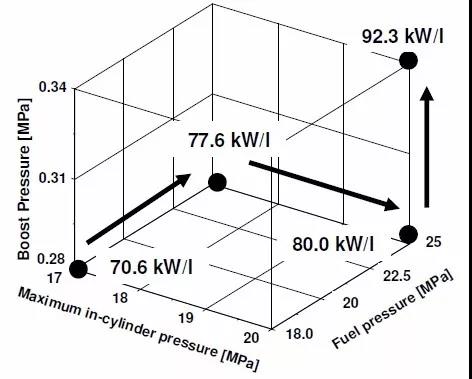
图25 4000rpm全负荷碳烟限值3FSN的3号机最大升功率
试验在平常的增压压力(0.28MPa)、爆压(17MPa)及喷油压力(180MPa)基础上逐渐增大各个变量。在这些基础设置时得到的升功率为70.6kW/L(图25)。保持增压压力及爆压值不变,喷油压力从180MPa增大到250MPa升功率提高了9.9%达到77.6kW/L(图9分析结果)。当爆压由17MPa增加到20MPa,增压压力和喷油压力均保持不变时,升功率提高了3%。这是因为提高爆压对改善燃烧效率和最大燃空当量比的影响较小:对于压缩比14:1,进气压力0.28MPa,爆压20MPa时的喷油时刻已经超过了最佳值。最后,增压压力从0.28MPa提高到0.34MPa,升功率提高了15%。在爆压(20MPa)增压压力(0.34MPa)、及喷油压力(250MPa)均为最大值时达到了碳烟限值3FSN内非常高水平的升功率(92.3最及大燃空当量比。需要特别引起注意的是此时爆压或增压压力均比之前试验时高,原因之前部分已作过解释。附录部分的图26和27显示了更多的细节。
试验结果展示了将喷油压力与爆压和增压压力结合起来并同时增大时升功率连续增加的结果。这让我们相信如果突破以前的技术限制升功率将得到更进一步的提升。
结论
发动机小型化是一种备受关注的提高升功率的同时能够降低油耗降低CO2排放的途径。试验研究确认了全负荷工况高喷油压力对于提升升功率的潜能。增大喷油压力对提高升功率的贡献主要有以下两个方面:
1、较低的碳烟排放使得燃空当量比增加
2、混合控制燃烧阶段速度加快使得燃烧效率提高。
上述影响在喷油压力从160MPa提高到250MPa时突显。功率输出变化没有停滞。如果喷油压力提高到250MPa更进一步的升功率研究。
高喷油压力可充分利用燃烧速率增大的优势。与此相比,增大孔径对于升功率的提升是有限的。通过增大孔径提高燃油速率使得喷射过程中燃空当量比增大,但会使得碳烟排放增加,因此限制了升功率的提高。当碳烟后期氧化过程不再是限制因素,这种影响在部分负荷时的受控制的扩散燃烧阶段非常重要。部分负荷时,喷孔直径增大碳烟排放增加。所以部分负荷与全负荷最好的折衷方案是提高喷油压力。
若想获得更高的升功率,结果表明在增大喷油压力的同时提高爆压和增压压力是非常重要的。在一台专门设计的可承受高强度的热机负荷的单缸机上,通过结合高增压压力(0.34MPa)高爆压(20MPa)以及高喷油压力(250MPa)最终达到了90kW/L升功率的目标(最大升功率为92.3kW/L)。该水平的性能是通过综合考虑部分负荷要求下的燃烧和喷射系统获得的,该结果是在柴油机应用上为减少燃油消耗实现更先进的小型化概念迈出的第一步。
参考文献
1. Hamm, T., Ecker, H. J., Rebbert, M., Grafen,M.,"Cylinder head concepts for high peak firing pressure", MTZ June2008.
2. Jansons, M., Lin, S., Choi, D.S., CampbellS.,Rhee, K. T., "Study of High-Pressure Injection DI Diesel Engine",SAE 1999-01-3494, 1999
3. Kohketsu, S., Mori, K., Kato, T., Sakai,K.,"Technology for low emission, combustion noise andfuel consumption ondiesel engine", SAE 940672,1994.
4. Shimada, T., Shoji, T., Takeda, Y.,"The Effect of Fuel Injection Pressure on Diesel Engine Performance",SAE 1992-25-0243, 1992.
5. Schommers, J., Duvinage, F., Stotz, M.,Peters, A.,Ellwanger, S., Koyanagi, K., Gildein, H., "Potential ofCommonRail Injection system for Passenger Car DI Diesel Engines", SAE 2000-01-0944, 2000
6. Cursente, V. , Pacaud, P., Gatellier, B. ,"Reduction of the Compression Ratio on a HSDI Diesel Engine:CombustionDesign Evolution for Compliance the Future Emission Standards", SAE2008-01-0839,2008
7. Heywood, J. B.,"Internal Combustion Engine Fundamentals", McGraw-Hill, 1988.
8. Guerrassi, N., Schoeppe, D., Bercher, P.,Breitbach,H., "Latest Developments in Diesel Common Rail Technology toMeet Future Demands", SIACongress Lyon,2004
9. Bruneaux, G, "Mixing Process in HighPressure Diesel Jets by Normalized Laser Induced Exciplex Fluorescence Part I:Free Jet", SAE 2005-01-2100,2005.
10. Bruneaux, G, "Mixing Process in HighPressure Diesel Jets by Normalized Laser Induced Exciplex Fluorescence Part II:Wall Impinging Versus Free Jet", SAE 2005-01-2097, 2005
11. Siebers, D.L., "Liquid Phase FuelPenetration in Diesel Sprays", SAE 980809, 1998.
12. Siebers, D.L., "Scaling Liquid PhaseFuel Penetration in Diesel Sprays based on Mixing Limited Vaporization",SAE 1999-01-0528, 1999.
附录
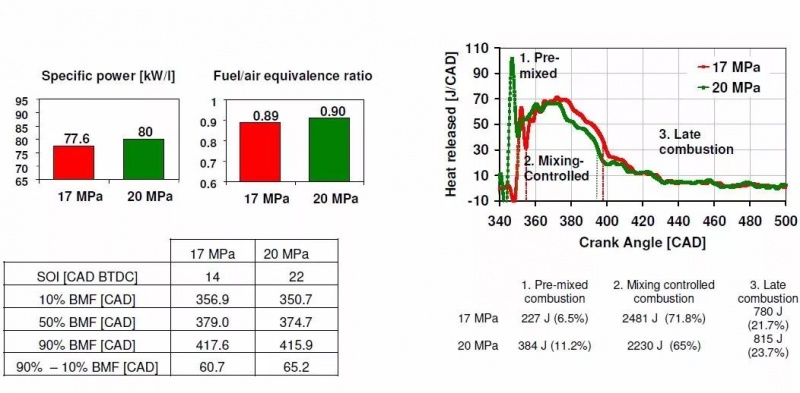
图26 爆压的影响
P2=0.28MPa FP=250MPa 3FSN Engine3
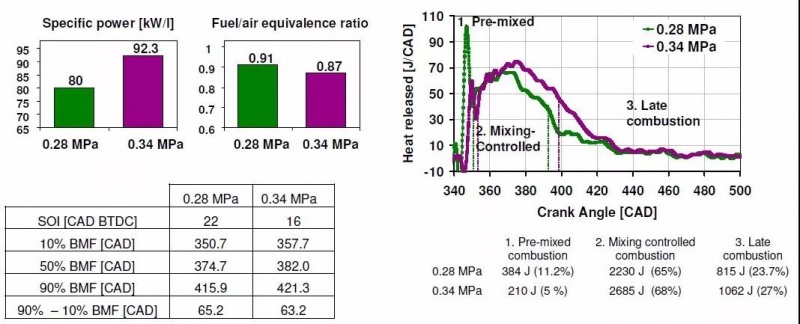
图27 喷油压力的影响
FP=250MPa Pmax=20MPa 3FSN Engine3
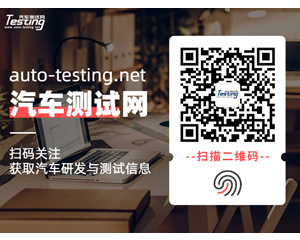
最新资讯
-
商用车及工程机械行业专场:NVH 及语音音频
2025-08-01 17:12
-
理想i8和重卡对撞测试引争议,东风柳汽发声
2025-08-01 15:52
-
艾德克斯IT-N2100 系列太阳能阵列模拟器
2025-08-01 15:43
-
ITECH重磅发布IT2705直流电源分析仪,重构
2025-08-01 15:34
-
现代汽车新一代混合动力系统:以技术革新引
2025-08-01 15:32