未来汽车对PCB的要求
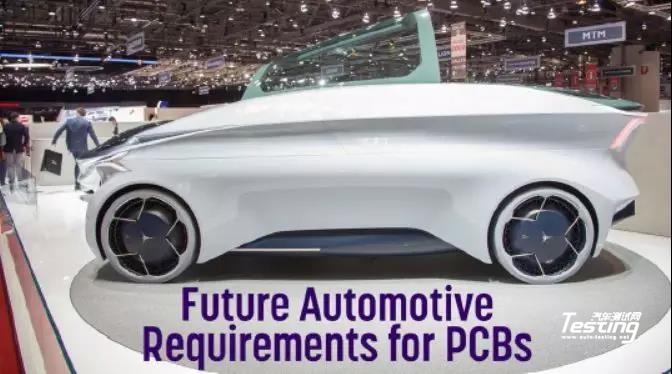
引言
Robert Bosch GmbH作为全球最大的汽车设备供应商,生产各种汽车电子产品。它旗下的PCB Technology Group除了完成标准的产品测试外,总是会在新PCB技术进入产品测试之前对其进行鉴定。过去会在鉴定过程中,对设计及供应链叠层的可能改进中发现PCB存在的失效模式。这些发现被纳入了技术规范中,并提交给了国际标准委员会。
不久的将来,汽车电子的功能及环保要求将发生巨大变化。主要是受到了三大趋势的影响:自动驾驶、互联互通的汽车及不断增加的电动汽车数量。
上述趋势将会增加汽车中电子产品的附加值。对于PCB,所采用的技术将要能够应付多个100A的高电流及GHz数量的信息处理。从产品性能的角度来看,远远超过了现在汽车中的PCB功能,需要采用新的理念。图1到图4给出了互联移动性、自动化移动性、动力传动系统和电气化移动性的示意图。
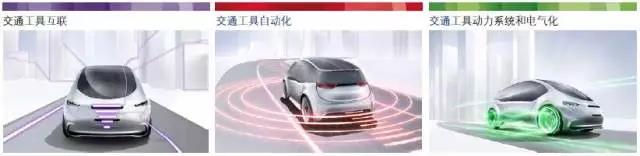
图1:汽车电子的三大发展趋势
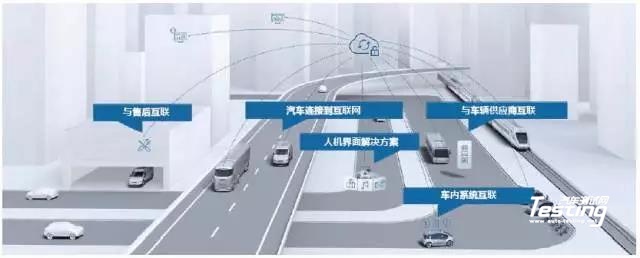
图2:互联移动性示例
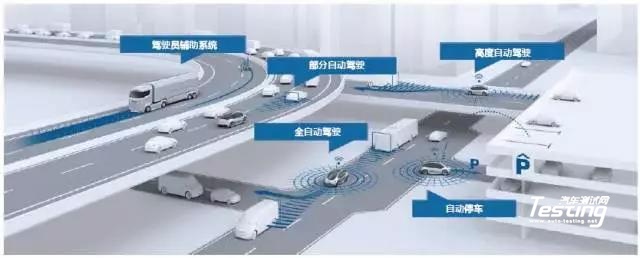
图3:自动移动性示例
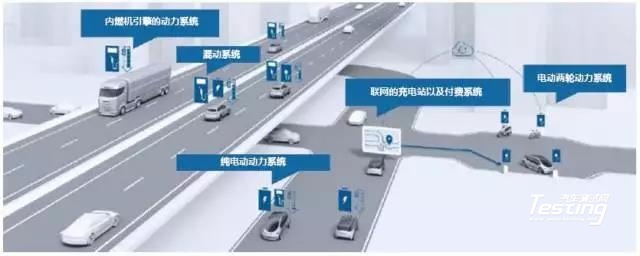
图4:动力传动和电气化移动性示例
与PCB中信号处理有关的多数技术,都可用于消费类产品行业,但用于汽车行业时,必须针对必要的质量和可靠性要求进行转换。对于电力电子产品,为了使其批量生产以获得更大的市场,有必要开发新的PCB。但截止到目前为止,电力电子产品仅进行了小批量的生产。
PCB是这些电子系统的关键部件,考虑到高速要求,PCB不只是设备之间的连接部件。必须特别注意可能会导致短路或开路的PCB失效模式。在一辆由几百伏的电压提供动力的无人驾驶汽车中,必须彻底了解其中的PCB以保证它的可靠运行。图5显示了PCB在生产和产品寿命期间的常见负荷,及其主要的失效模式。图6显示了汽车电子所要求的PCB特性。
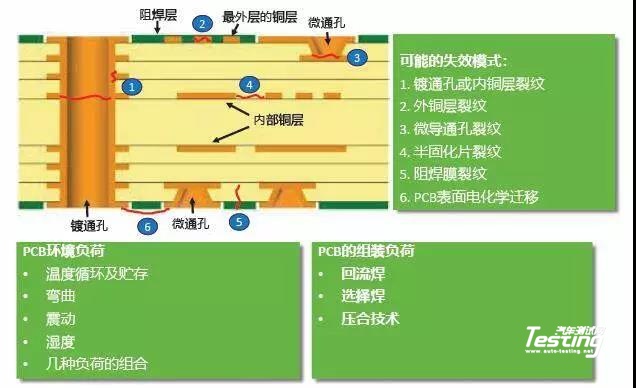
图5 PCB的常见环境负荷和组装负荷及其导致的可能失效模式
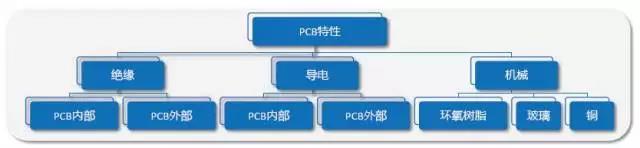
图6:PCB关键特性示意图
汽车对未来电子产品的要求
汽车对PCB的特定要求受到了其寿命期间环境负荷如温度、湿度及震动负荷的影响。取决于具体的应用,多样化要求将会增加。一方面,电子产品越来越小,距离致动器(如引擎)越来越近,例如功率电子元件要能经受更高的温度;另一方面,诸如车载电脑之类的电子设备可更好地防止外部应力的作用,由于充电时间及一天24小时不间断服务,需要有更长的使用寿命。图7列出了对PCB及基板的要求。
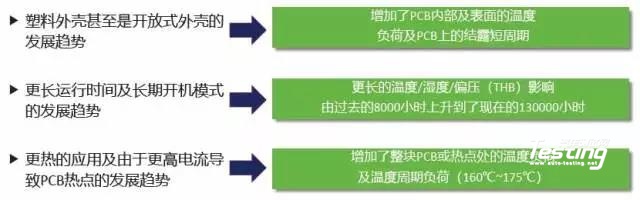
图7:增加了环境负荷要求采用汽车电子专用材料及理念,必须彻底了解原因和相互之间的影响
功能需求也是多种多样的。在电动车中使用PCB可能是具有成本效益的解决方案,但PCB必须要能够经受100万小时寿命时间内几百安培的电流,及高达1000伏的电压等汽车环境。
为了满足自动驾驶及互联汽车的信号处理要求,汽车的HDI技术还必须向前迈进一大步,才能够使用有几千个I/O和BGA间距<0.8 mm的处理器和存储器。高速要求需要使用新材料,新材料必须应对环境要求,特别是湿度和温度。图8总结了重要的功能要求。
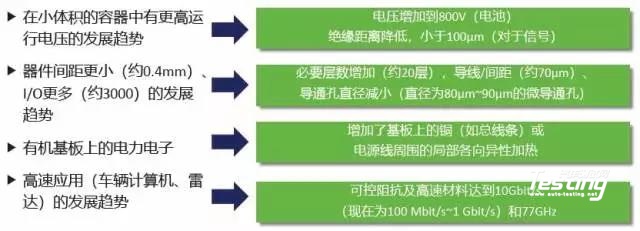
图8:新型PCB(如电力PCB及高集成逻辑PCB)必须具备的新功能要求
汽车环境中的温度及湿度导致的失效模式
对于汽车电子产品,长期以来,行业一直重点关注由于温度循环引发的失效,目前已针对这种失效模式优化了材料。但是,湿度和温度也很关键,尽管汽车的很多应用证实了在运行模式下的自加热。在启动前,汽车可能在潮湿的环境中停放数天或数周,湿度可通过塑料或大气补偿组件进入电子产品。
湿度对PCB表面及内部结构的影响是问题的主要方面,已对可能的失效模式进行了详细的研究。因此本文将强调由于温度、湿度及偏压(THB)导致的失效。图9显示了在PCB结露(水冷凝)期间导电晶体的生长,这是必须要避免的。
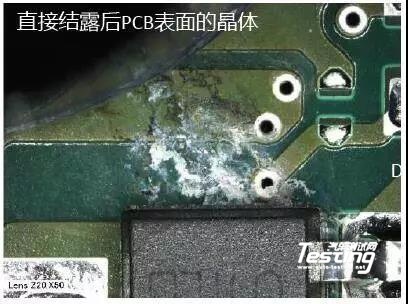
图9: PCB表面的失效模式
即使没有结露,如果没有仔细选择材料,高湿度也会造成电气短路。表面绝缘电阻(SIR)会下降,可能导致电子产品失效。我们的方法是通过模拟及实验测试彻底了解保护罩(金属或塑料外壳)内的温湿度状况。
另一方面,我们会根据IPC-9202中的SIR测试方法,在不同的温度和湿度的条件下鉴定所用材料(如PCB、器件、助焊剂、散热界面材料或覆形涂层)和设计要素。通过图10和图11显示的这种方法,所选择的设计元素和材料是安全可靠的,确保了汽车在产品生命周期内的适当功能。
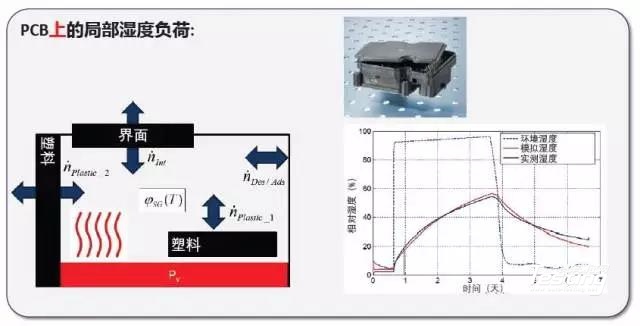
图10:通过有效的模拟模型预测ECU中局部湿度的实际状况
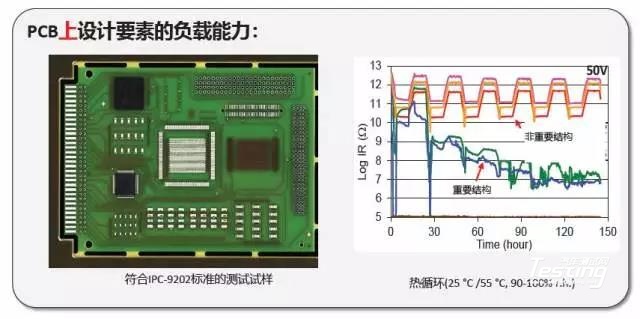
图11:通过测量最苛刻条件下封闭外壳内材料和设计的SIR,对材料和设计进行鉴定
在PCB内部,湿度也十分关键,由于电化学迁移(ECM)可能导致不同类型的失效模式。导电阳极丝(CAF)或中空纤维是行业中已知的失效模式。对镀通孔周围变形区、界面处的PCB裂纹或散装材料的裂纹必须进行研究。树脂裂纹可能是由于温度下降、高压力、弯曲和/或机械负荷而导致的。此外,PCB材料在高压下的性能也需要研究。所有这一切对于保证PCB绝缘特性都是必要的。图12显示了会造成短路和漏电的常见PCB内部失效。
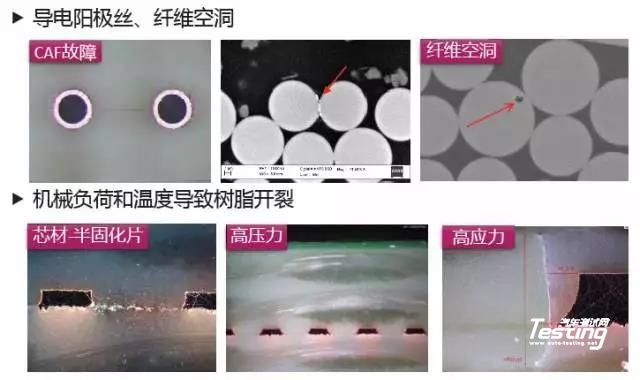
图12:PCB内部的失效模式,因为现场负荷增加(尤其是在亚洲市场),越来越需要关注由于湿度诱发的失效
为了保证汽车电子产品中PCB基板的稳定性,模拟了电子系统中PCB内的局部环境条件如温度和湿度。模拟条件将与所用材料的负荷能力以及设计进行比较。得出的寿命模型有助于将PCB鉴定测试结果转换为电子系统中的实际状况,并确定PCB内设计准则的适当距离。
同时针对CAF失效模式进行了模拟测试,正在考虑对PCB其它裂纹进行模拟测试。目前,鉴定测试和寿命模型仍正在开发中。如果没有适用的寿命模型,必须通过材料限制或严格的工艺控制(如对于中空纤维失效模式)去除材料或失效模式。图13和图14总结了这种方法。
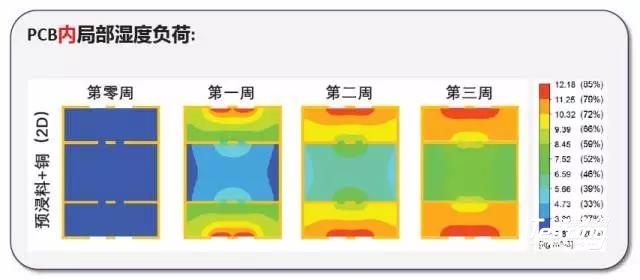
图13:通过模拟模型对PCB内局部湿度进行实际预测
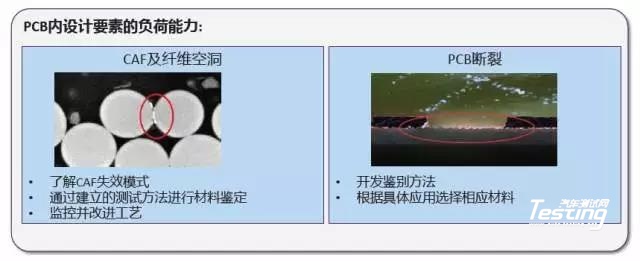
图14:PCB内环境负荷及所用材料的负荷能力
高速要求
对于互连性或图像识别(未来会达到10GHz),高速应用如雷达(77GHz),以及信号处理等都需要明确定义基板和设计规则要素。消费品行业的阻抗可控PCB叠层和PCB供应商工艺控制都是标准的,汽车行业必须保证优质的信号完整性和电源完整性,并具备良好的电磁兼容性。需要特别注意材料的选择,以保证除电气性能外,材料在温度、湿度、偏压方面的稳定性,这将导致未来对材料选择及设计规则的限制。为了确保必要的电气性能,要鉴定PCB供应商在高速应用方面的资质。
考虑到PCB基材(Dk、Df)的电气特性,汽车应用必须考虑生产容差及环境的影响,如温、湿度会影响电气值。例如,在热老化过程中,材料的相对介电常数和介电损耗都会降低,但介电常数会随着环氧树脂材料中水分含量的增加而增加。
结论
汽车电子的功能及要求面临着巨大的变化。可修改或调整消费类产品行业的解决方案,以满足汽车产品要求,并且必须发展电力电子批量生产的新理念。
总结汽车的更高要求:
更长的寿命(充电时间、运行时间);
更高的温度负荷(微型电子产品、新应用);
更小的距离 (微型化、功能-互联互通、自动化);
更大的湿度负荷;
更高的频率。
即将面临的挑战:
需要针对温度负荷优化PCB(TC级别达到150℃;未来将需要达到160℃以上);
考虑到2个电位之间可能形成裂纹,在更高温度下的材料必须保持稳定;
所有使用的材料在湿度、温度及偏压下必须不能发生相互作用;
目前用现有材料实现高速设计是可能的;但在未来,新型材料是必要的(>10 GHz)。
尤其是在设计和生产有可靠性要求的PCB产品时,必须考虑汽车所处的特殊环境条件。适当的PCB用新材料鉴定策略是必要的,目前正在开发中。
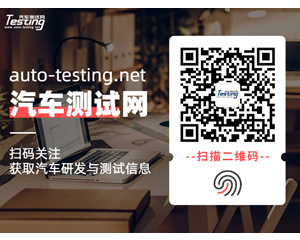
编辑推荐
最新资讯
-
商用车及工程机械行业专场:NVH 及语音音频
2025-08-01 17:12
-
理想i8和重卡对撞测试引争议,东风柳汽发声
2025-08-01 15:52
-
艾德克斯IT-N2100 系列太阳能阵列模拟器
2025-08-01 15:43
-
ITECH重磅发布IT2705直流电源分析仪,重构
2025-08-01 15:34
-
现代汽车新一代混合动力系统:以技术革新引
2025-08-01 15:32