某电动汽车噪声分析及优化
随着能源危机的日益凸现和环境意识的日益觉醒,电动汽车成为世界汽车工业发展的热点。伴随着电动汽车技术的不断发展,客户对电动汽车性能提出了更多的指标,噪声振动性能越来越备受关注,成为影响电动汽车品牌的一项重要指标。
本文通过使用LMS.TestLab测试系统,对某电动汽车的噪声进行测量分析,系统研究了其噪声特性,确定了电机及减速器是主要噪声源,并判断动力总成悬置系统性能不佳是电机及减速器振动向车内传递噪声的主要因素。根据测试分析,对电机及减速器进行了改进优化,并对悬置系统橡胶软垫刚度重新进行调整,取得了较理想的降噪效果。
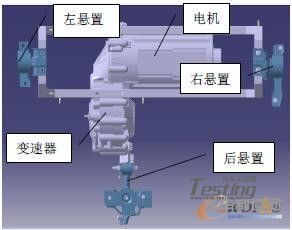
2.2 噪声源测试实验及噪声特性分析
要有效的识别噪声源,首先需要确定噪声产生的主要位置、主要发声部件以及各噪声源对总声级的贡献量。对于有多个发声声源的情况,控制噪声的主要方法是找到发声部件中占噪声总声级比重大的声源噪声,对其采取降噪措施,效果会很明显。其次,要确定噪声源的特性,包括声源类别、频率特性等。一般要综合多种测量方法和信号处理技术,来达到明确识别噪声源的目的。下表显示的是根据电动汽车的工作原理以及其发声特点,对电动汽车不同运行方式产生的噪声进行了测试分析。测点位置:驾右、副左、后左、后右。
测试分为以下几种工况,试验数据及分析如下:
(1)车辆匀速行驶车内噪声和熄火滑行车内噪声
表1 车辆匀速行驶和熄火车内噪声 单位:dB(A)
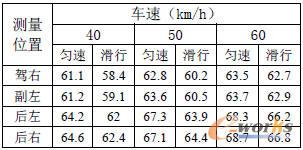
分析:匀速比滑行车内噪声大0.8~3.4dB(A),胎噪、风噪和路噪是匀速车内噪声的主要噪声源
(2)全负荷加速后右车内噪声
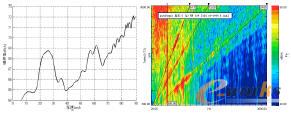
分析:全负荷加速在低速时有较大峰值,峰值主要是由电机的24阶噪声,8.17阶噪声是由减速器第二对啮合噪声,300Hz噪声主要是由电池风扇引起的。
(3)驻车背景噪声、真空泵噪声和电池风扇噪声
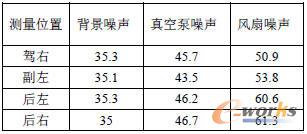
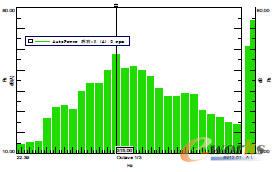
结论:电池风扇噪声是驻车时车内的主要噪声源,主要峰值集中在300Hz附近,其它部件噪声对整车噪声影响很小。
(4)总结
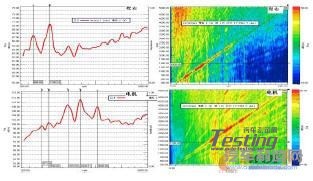
结论:驾驶员右耳的噪声峰值在电机688rpm、1300rpm,而电机近场噪声峰值在电机978rpm、1246rpm、1972rpm、2449rpm和3097rpm,因此电机辐射噪声不是驾驶员右耳噪声峰值的主要来源;在转速688rpm时,左悬置传递的振动较大,在转速1300rpm时,后悬置传递的振动较大,初步判断:低速时全负荷加速噪声主要传递路径是通过结构传递的。
3 实验数据分析及优化
3.1 8.17阶噪声分析及优化
由图二噪声型谱可以判定8.17阶是主要噪声源,8.17阶噪声来源分析:
减速器齿轮啮合原理:一级齿轮28/48,二级齿轮14/52,通过计算分析:齿轮啮合冲击1*28/48*14=8.17阶。因此,8.17阶噪声是由减速器第二对啮合噪声。
电动汽车减速器与普通手动档变速箱工作情况完全不同,电动汽车用减速器工作转速较高,一般在4000rpm以上运行,而且扭矩较大。因此,电动汽车用减速器的齿轮参数、精度以及齿轮装配侧隙要求更加严格。针对电动汽车用减速器的工作特点,对减速器齿轮参数进行了优化,进行齿轮修缘,同时采用弹性隔振齿轮,即在齿轮的轮体和齿圈之间加橡胶用于隔振。采用一系列措施后,通过实验验证,减速器优化后8.17阶噪声明显消除(如图5)。
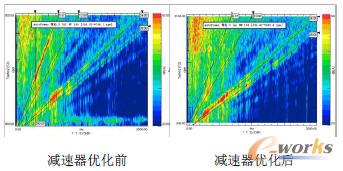
3.2 电机噪声分析及优化
3.3 悬置系统分析及优化
通过图四车内噪声数据可以确定电机及减速器的噪声传递途径是悬置系统,经过分析,确定原悬置刚度过小,致使悬置内外圈接触,隔振性能较差,增加刚度使悬置内外圈分离,提高隔振性能。下表是悬置更改后的对比数据。
表3 悬置系统优化前后对比数据
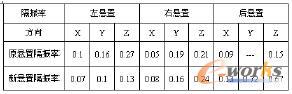
结论:左悬置隔振率提高,右悬置变化不明显,后悬置隔振率虽然上升,但传递到车身的振动较小。
4 结论
通过上述电动汽车噪声的研究,以及对噪声源地测试分析并对主要噪声源进行优化改进,以及控制电机及减速器振动对车内噪声的原理和方法的研究,主要得到以下几个结论:
- 下一篇:RADIOSS多域求解技术在汽车侧碰仿真的应用
- 上一篇:汽车进气噪声的分析及优化
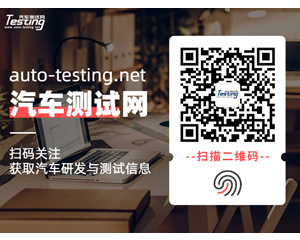
最新资讯
-
商用车及工程机械行业专场:NVH 及语音音频
2025-08-01 17:12
-
理想i8和重卡对撞测试引争议,东风柳汽发声
2025-08-01 15:52
-
艾德克斯IT-N2100 系列太阳能阵列模拟器
2025-08-01 15:43
-
ITECH重磅发布IT2705直流电源分析仪,重构
2025-08-01 15:34
-
现代汽车新一代混合动力系统:以技术革新引
2025-08-01 15:32