汽车生产DV与PV验证
在汽车开发和生产过程中,DV(Design Verification,设计验证)和PV(Production Validation,生产验证)是两个关键的质量控制环节,分别针对设计可靠性和生产一致性进行验证。
01、什么是DV验证?
Design Validation(设计验证,简称DV)是汽车及制造业中的关键质量控制环节,指在产品开发阶段对零部件设计方案进行系统性实验验证的过程。
其核心作用在于:通过模拟量产后的实际工况,在产品定型及模具投入前识别潜在设计缺陷,验证零部件性能是否达到预设技术标准,从而规避因后期设计变更导致的模具返工、生产延期等重大经济损失。DV测试通常涵盖材料性能、结构强度、环境耐受性等维度,是衔接产品开发与量产制造的重要技术闸口。
几乎每个零部件都会要求去做DV实验。
测试内容:
-
功能性能测试(动力、制动、NVH等)。测试产品的核心功能是否达标。例如,发动机的功率输出、转向系统强度、ADAS(高级驾驶辅助系统)的感知与决策逻辑等。
-
环境可靠性(高温、低温、振动、盐雾等)。模拟极端环境条件,验证产品在高温、低温、湿热、盐雾、振动等场景下的可靠性。例如,在-40℃低温下测试车门密封性,或通过振动台模拟10万公里路试后的零部件疲劳。
-
耐久性测试(台架试验、道路试验)。通过加速老化实验评估产品寿命。例如,变速箱的台架耐久测试需模拟超过30万公里的使用工况,动力电池需完成充放电循环数千次以验证容量衰减率。
-
法规符合性(排放、碰撞安全等)。确保产品符合国家或国际强制标准,如中国的C-NCAP碰撞安全标准、欧洲的ECE R100电动车辆安全法规、美国的FMVSS(联邦机动车安全标准)等。
研发团队(设计工程师、测试部门)主导DV实验,供应商配合提供样件并参与问题分析,实验结束需要输出设计缺陷清单、优化方案、设计冻结批准等文件。若测试失败,需回溯设计缺陷,修改图纸或调整参数,甚至可能重新进入设计迭代。
02、什么是PV验证?
PV(Production Validation,生产验证,核心目的在于验证量产工艺的稳定性和一致性,确保批量产品能够完全复现DV(设计验证)阶段的设计性能。其本质是通过系统性测试回答"生产是否可控"这一核心问题,从而规避因工艺波动引发的质量风险。该实验的实施节点位于量产准备阶段,具体时间轴为:在完成试生产流程(如PPAP生产件批准程序)后,正式进入量产前的产能爬坡期。此时,生产线、工装模具及供应链体系已实现全要素就位,具备开展工艺稳定性验证的基础条件。
测试内容:
-
工艺稳定性(焊接、装配精度等)。评估生产线的过程能力(如CPK值),确保关键尺寸公差、焊接强度等参数稳定可控。例如,车身焊点的强度需通过破坏性抽检,保证每批次合格率≥99.9%。
-
生产节拍验证(产能达标)。验证生产线的实际产能是否达到设计目标(如每小时/每天生产量),确保生产线能够满足市场需求。例如,某车企总装线因机器人抓取零件速度慢,导致节拍从60秒/辆延长至75秒/辆。
-
零件一致性(供应商量产件质量)。对量产零件进行抽样检测,验证其与DV阶段样件的性能一致性。例如,电机绕组的绝缘电阻、车灯的光学参数等需与DV数据对比,偏差需控制在5%以内。
-
整车质量检测(合格率、缺陷率统计)。通过检测试生产车辆的质量,统计合格率和缺陷率,确保量产产品的一致性和可靠性。例如,试生产车辆中30%存在中控屏黑屏故障。。
制造工程团队(工艺工程师、质量部门)主导PV实验,供应商需提供量产级零件并配合过程审核,实验结束后,需要输出工艺优化报告、量产许可(SOP批准)等文件。若测试失败,需优化生产工艺(如调整注塑温度、改进装配流程)或更换不合格的供应链资源。
03、DV验证与PV验证的差别
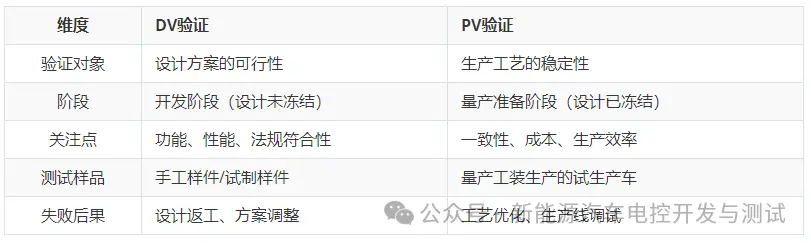
DV实验作为产品从概念设计到实体验证的首个关键环节,通过极限环境检测消除产品设计缺陷;PV实验则承担着工程样件到批量生产前的终极验证使命,运用全维度测试体系规避制造环节风险。这对质量验证机制犹如精密仪器的双重安全锁,共同构筑工业品可靠性的坚固防线。面对白热化的市场竞争,构建DV-PV无缝衔接的验证体系,正成为制造企业提升产品成熟度、保障市场口碑的关键技术壁垒。
- 下一篇:汽车零部件常见可靠性实验总结
- 上一篇:Aurora无人自动驾驶重卡开始商业运输交付
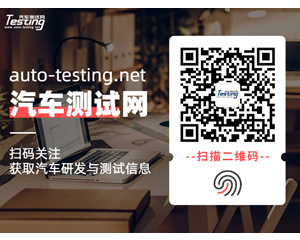
最新资讯
-
首次开展多场景连续动态测试 | IVISTA中国
2025-07-14 14:44
-
锁定直播间,汽车一体化压铸检测一次性全解
2025-07-14 10:04
-
Eckel是全球声学测试消声室的领导者。SineT
2025-07-14 09:19
-
中国汽研汽车指数最新批次多项测评结果权威
2025-07-13 08:48
-
ArtemiS SUITE 基础及模态测试与分析培训(
2025-07-12 09:53