新能源混动架构乘用车NVH性能匹配优化技术研究
摘 要:新能源乘用汽车混动架构车型在整车 NVH 性能开发匹配过程中主观评价存在整车启停抖动及敲击等问题。本文针对此问题点,从悬置隔离率,扭转减振器不同的刚度、阻尼、配合间隙及控制策略等方面介绍了新能源乘用车混动架构整车匹配调校过程中,影响整车启停抖动及敲击产生的因素并主要通过悬置隔振、扭转减振器的匹配、控制策略优化组合方案来解决该问题的方法。
关键词:新能源 混动架构 柔性连接器 NVH 性能 匹配
1 引言
近几年以来,全球新能源汽车销量取得了飞跃式的发展,传统车企也逐步从燃油车向新能源方向转型升级,国内主流汽车厂和新势力车企都已大力布局混合动力汽车、纯电动等新能源汽车。其中当前最新的、主流的混合动力方案从单个国内市场辐射至全球。该混合动力方案发电系统发动机相关附件都用电来供电如电子水泵、电动压缩机、空调系统等,该套混合动力方案减轻发动机负载发动机工作区相比传统燃油发动机工作区更高效,从另外一方面来提高发动机整体的效率,可持续在高热效率区工作发电,可持续为电池包和驱动电机提供电能;降低整车油耗、降低碳排放性能。其该架构产品销量飞跃上升,得到了国内外市场消费者认可。新能源汽车本文以混合动力架构为例,
在传统动力系统发动机加变速器的组合方案基础上将变速器进一步架构调整成电混系统即发动机加电混系统组合方案,其中电混系统主要包括发电机、驱动电机、以及双电机的集成式电子控制器、离合器、减速器等,当离合器分离的时候发动机输出通过齿轮可以直接驱动轮端输出动力,也可以让驱动电机通过减速器直接驱动轮端输出动力。将多合一的电混系统集成加发动机组成混合动力系统,将该混合动力系统匹配搭载到整车上,有传统发动机 NVH 问题也有电机 NVH 问题、以及整套动力系统架构发动机与电机之间匹配不佳所带来新的 NVH 问题,相比传统燃油车其整车 NVH 性能匹配调校相关工作给NVH 工程师带来前所未有的具有极大挑战也是对 NVH 工程师专业能力的考验。
本文结合某新能源乘用车混合动力车型在样车开发匹配调校过程阶段,主观评价整车存在启停抖动及动力系统敲击问题,并对能引起该问题的机理进行详细分析,并对其混合动力系统架构悬置系统悬置前期仿真布置到悬置台架整车试验验证 NVH 性能隔振率要求、扭转减振器影响 NVH 性能的关键参数及其匹配、控制策略优化等方法进行介绍。
2 悬置系统 NVH 性能
悬置系统其关键性作用是承载支撑整车混合动力系统、抑制混动系统内部反作用力的外力造成对混动的动态位移、减少因混动系统只身的振动传递到车身端。这其中涉及到悬置系统各个悬置布置位置及布置方式有很重要的关联性,需在项目前期仿真设计阶段通过仿真方法,输入混动系统质心、转动惯量、主惯性轴等参数仿真计算优化,使在空间坐标轴 X、Y、Z 3 方向平动以及绕 X、Y、Z 3 方向转动,共 6 各方向上自由空间内各个方向上解耦,提高各个方向上解耦率满足设计开发要求,混动系统上悬置系统各个悬置安装位置并结合整车车身端位置,可确定悬置系统各个悬置的在车身端与动力端的位置,悬置系统安装位置确定通过优化各个悬置刚度、阻尼等参数调整,仿真计算出解耦率及其 6 个方向上的混动系统缸体模态固有频率。并满足设计开发要求解耦率及混动系统缸体模态固有频率 6 个自由度模态分布。
通过前期设计阶段悬置系统在混动系统上的布置数据、供应商将按照混动悬置系统设计开发要求台架试验测试各个悬置系统刚度、阻尼是否满足设计要求,一般要求悬置系统样件 3 套,分别是前期设计值样件以及在设计值基础上 ± 偏差 15% 样件各一套、将台架试验合格件搭载到样车阶段整车上摸底试验验证调校悬置系统是否满足隔振要求以及确定 NVH 更优样件的刚度、阻尼,同步将该刚度、阻尼参数样件需满足疲劳耐久可靠性等性能要求,一般在隔振率在 20-25dB,同步校核试验结果与前期设计阶段仿真差异,若混动悬置隔振率较差不能起很好的隔振要求,使得混动系统在整车状态下瞬态工况下如启停产生抖动及敲击等问题会通过悬置系统路径将激励源放大,从而使整车 NVH 问题恶化。
混动系统架构悬置隔振率对整车 NVH 性能匹配调校过程中起着很关键性的作用,也是降低混动系统激励源通过悬置系统路径传递到整车 NVH 上重要的有效优化方法。
3 柔性连接器结构
本文某新能源乘用车混合动力车型样车搭载为扭转减振器,扭转减振器是混合动力系统总成上连接发动机与电混系统的零部件,由弹簧组件、摩擦片、碟形簧片、盘毂、减振环、减振压板、从动盘等构成,具有减振、限扭的作用。为达到更好的减振及衰减效果,扭振减振器往往搭配一个单质量飞轮使用。
4 扭转减振器参数匹配
在开发设计前,需根据混动系统参数进行初步选型或根据项目需求新开发扭转减振器匹配,为达到更好的 NVH 减振效果,同时需满足疲劳耐久可靠性性能试验需求,在整车样车调校阶段扭转减振器工程实践中往往需要对不同刚度、阻尼、配合间隙、启动和停机控制逻辑等参数进行不同温度环境下NVH 工程师与控制策略优化相关工程师一起匹配联调。
4.1 扭转减振器刚度匹配
一般而言,小刚度的扭转减振器 NVH隔振性能更好,为了达到更好的瞬态工况如启停性能,扭转减振器刚度的设计会从整个动力输出传动系统层面全方位进行考虑。发动机、扭转减振器以及发电总成组成混动系统的传动系统模态应当与混动系统刚体模态Roll(绕 Y 轴)频率间隔 3HZ 以上。若传动系统模态频率与混动系统刚体模态 Roll(绕Y 轴)频率相同或接近,两者频率耦合,则整个混动系统在启停过程中容易产生较大冲击,且整车状态下抖动明显主观评价较差。
4.2 扭转减振器阻尼匹配
扭转减振器不同的阻尼参数在整车状态下停机和稳态表现对整车 NVH 性能影响很大。阻尼太小,会导致停机时扭振不收敛,产生抖动、敲击;阻尼太大,会导致稳态工况扭转减振器隔振差,整车 NVH 振动和噪声恶化。如图 1 为某新能源乘用车混动系统架构车型搭载同一刚度、不同阻尼扭转减振器的停机表现。
从图 1 试验结果可以看出,阻尼小的扭转减振器停机时相对扭转角达 6°,且不收敛,导致车内座椅持续抖动且振幅大;阻尼大的扭转减振器停机时相对扭转角为 3°,收敛快,座椅振动幅值小。
但是阻尼的选择并不是越大越好,如图 2为某新能源乘用车混动系统车型搭载同一刚度、不同阻尼扭转减振器怠速发电工况表现。当阻尼过大时,稳态工况扭转减振器隔振性会变差,导致整车车内噪声变大。为设计出合适的阻尼范围,需综合启停、怠速、加速等工况整体表现进行 NVH 工程师与控制策略优化工程师一起匹配联调。
4.3 扭转减振器间隙匹配
扭转减振器作为一个装配部件,各子零件之间的配合间隙对启停性能也有很大影响。以盘毂外齿与驱动盘之间的配合间隙为例,通过优化配合间隙能显著改善停机敲击异响问题。
从图3可以看出:同一扭转减振器,搭载相同的停机程序,当间隙较大时,启停敲击更明显。盘毂与驱动盘之间设计一定的间隙是为了补偿发动机与变速器装配时的误差。在此基础上,尽可能的减小系统间隙能改善扭转整车启停表现。
4.4 扭转减振器控制程序参数匹配
在某新能源乘用车混动系统中,发动机启动前,由 ISG 电机作为主动件,拖动发动机到一定转速进行进而释放扭矩,当发动机点火后,ISG 电机变为被动件进行发电;停机时,ISG 作为主动件提供一定的扭矩,拉停发动机。在此过程中,ISG 电机经过了主动 - 被动 - 主动的转换,其控制参数对启停性能影响很大。
如图 4,当启动加载斜率(力矩)较大时,发动机转速快速通过系统共振区间,启动敲击小;当启动加载斜率(力矩)较小时,在传动系统共振区间停留时间长,易引起敲击。但启动力矩太大会引起发动机转速上冲太高,导致发动机噪声大。
不同的停机扭矩对发动机停机性能也有显著影响。如图 5,当停机扭矩过小时,扭振不收敛,导致车内持续抖动。停机扭矩也不能设计过大,扭矩过大会导致扭转减振器敲击。
5 结语
本文结合某新能源乘用车混动系统架构车型在整车调校过程中主观评价存在整车启停抖动及敲击等问题并通过悬置隔振、扭转减振器的匹配、控制策略优化组合方案来解决该问题的方法,从前期仿真分析到样车阶段试验验证去识别、校核及 NVH优化性能匹配、与控制策略优化工程师联调匹配,在整车状态下试验测试悬置系统隔振率满足要求的前提条件下,对混动系统架构关键性零部件扭转减振器不同的刚度、阻尼、配合间隙、控制策略优化等关键性能参数的匹配方案进行了介绍,并对参数设计不当可能导致的后果进行了分析与说明,为新能源汽车行业内相同或类似新能源乘用车混动系统架构车型类型的车在前期设计阶段及后期样车调校阶段主观评价存在整车启停抖动及敲击产生等问题及 NVH 性能优化提供参考。
郭杨 刘虎
比亚迪汽车工业有限公司 广东省深圳市 518118
新能源汽车
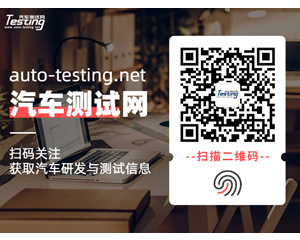
最新资讯
-
商用车及工程机械行业专场:NVH 及语音音频
2025-08-01 17:12
-
理想i8和重卡对撞测试引争议,东风柳汽发声
2025-08-01 15:52
-
艾德克斯IT-N2100 系列太阳能阵列模拟器
2025-08-01 15:43
-
ITECH重磅发布IT2705直流电源分析仪,重构
2025-08-01 15:34
-
现代汽车新一代混合动力系统:以技术革新引
2025-08-01 15:32