团体标准《乘用车固定式制动钳总成性能要求及试验方法》
中国汽研牵头的T/CAAMTB 161—2023《乘用车固定式制动钳总成性能要求及试验方法》团体标准正式发布。
本项标准起草单位:中国汽车工程研究院股份有限公司、浙江万安科技股份有限公司、长城汽车股份有限公司、上海汽车制动系统有限公司、北京汽车股份有限公司、弗迪科技有限公司、浙江亚太机电股份有限公司、辰致(重庆)制动系统有限公司、布雷博(南京)制动系统有限公司、浙江力邦合信智能制动系统股份有限公司、辰致科技有限公司、雷达新能源汽车(浙江)有限公司、炯熠电子科技(苏州)有限公司、重庆大学、阿维塔科技(重庆)有限公司、江苏恒力制动器制造有限公司、宁波吉利汽车研究开发有限公司、重庆长安汽车股份有限公司、成都吉世威汽车科技有限公司、浙江万安智驭汽车控制系统有限公司、重庆凯瑞测试装备有限公司、曙光制动器(苏州)有限公司、重庆慧鼎华创信息科技有限公司、中汽院(江苏)汽车工程研究院有限公司。
本文件主要起草人:王应国、曾繁卓、竹利江、唐俊、陈锋、朱奇章、李立刚、郝之凯、郭真龙、马闯、卜凡彬、朱作龙、彭锋、孙仁杰、洪庆良、李传博、胡文中、赵飞林、朱建明、张和平、雷文、黄俍、呙波、李伟、任学良、郑德金、赵立杰、魏跃、刘永刚、姜鹏、乔冠朋、高鸣晓、黄愿明、王雄、郭技超、周哉松、肖成诚、郭强强、向辉、刘冠鉴、杨鹏翱、李杰、李学佳、余学贵、魏政、邓海威、江仁旺、高宇、吴相国、欧发强、窦文娟、黄兴、赵红全、申娟、李宗玉、刘洋洋、辛元强、周移民、冉陶。
本文件为首次发布。
乘用车固定式制动钳总成性能要求及试验方法
1 范围
本文件规定了乘用车固定式制动钳总成(以下简称“定钳总成”)的术语和定义、性能要求及试验方法。
本文件适用于GB/T 15089规定的M1类和N1类车辆行车制动器用液压定钳总成。其它类型的液压定钳总成可参照执行。
2 规范性引用文件
下列文件中的内容通过文中的规范性引用而构成本文件必不可少的条款。其中,注日期的引用文件,仅该日期对应的版本适用于本文件;不注日期的引用文件,其最新版本(包括所有的修改单)适用于本文件。
GB/T 5620 道路车辆 汽车和挂车 制动名词术语及其定义
GB/T 10125 人造气氛腐蚀试验 盐雾试验
GB/T 15089 机动车辆及挂车分类
QC/T 316 汽车行车制动器疲劳强度台架试验方法
QC/T 556 汽车制动器温度测量方法及热电偶安装要求
QC/T 592-2013 液压制动钳总成性能要求及台架试验方法
QC/T 1167 乘用车行车制动器噪声台架试验方法
T/CAAMTB 84 彩色喷涂制动钳漆层性能要求及试验方法SAE J2522 制动性能台架试验国际规范(Dynamometer Global Brake Effectiveness)
3 术语和定义
GB/T 5620和QC/T 592-2013界定的以及下列术语和定义适用于本文件。
固定式制动钳总成 fixed brake caliper assembly
内外侧钳体固定,在制动促动力作用下通过设置在内外侧钳体内对置的加压机构同时推动制动衬块总成夹紧制动盘,在制动促动力卸除后在回位机构作用下实现加压机构同时回退的制动部件。参见图1。根据加工方式不同,分为一体式定钳和分体式定钳;根据油路设置不同,又分为内油路定钳和外油路定钳,参见图2。
图1 固定式制动钳总成示意
标引序号说明:
1——钳体;
2——进油孔;
3、6——活塞;
4——衬块总成;
5——密封圈;
7——活塞防尘罩;
8——放气螺钉。
图1 固定式制动钳总成示意(续)
标引序号说明:
1——分体面;
2——外油道;
A——外油道分体式定钳;
B——内油道分体式定钳;
C——外油道一体式定钳;
D——内油道一体式定钳。
图2 固定式制动钳总成分类
4 性能要求
4.1 静置密封性
按6.1进行试验,定钳总成应无液体泄漏。
4.2 真空密封性
按6.2进行试验,定钳总成的压力升高值不应大于200 Pa。
4.3 低压密封性
按6.3进行试验,定钳总成的压力降不应大于2 kPa。
4.4 高压密封性
按6.4进行试验,定钳总成的压力降不应大于0.2 MPa。
4.5 放气螺钉密封性
按6.5进行试验,定钳总成不应出现龟裂和损坏,制动钳及放气螺钉处应无液体泄漏。
4.6 油管连接螺纹密封性
按6.6进行试验,定钳总成不得出现龟裂和损坏,制动钳及油管连接处应无液体泄漏。
4.7 所需液量
按6.7进行试验,定钳总成安装圆形金属制动衬块和全新制动衬块总成在0.5 MPa、1.0 MPa、3.0 MPa、5.0 MPa、7.0 MPa、10.0 MPa、12.0 MPa和16.0 MPa的所需液量应满足产品技术文件要求。
4.8 拖滞扭矩
按6.8进行试验,定钳总成拖滞扭矩在制动盘第1圈转动过程中的最大值不应大于2.5 N•m,在第10圈转动过程中的最大值不应大于1.5 N•m,或满足产品技术文件要求。
4.9 钳体刚性
按6.9进行试验,钳体在10.0 MPa压力下沿液压缸轴线方向的单侧变形量不应大于0.3 mm,双侧总变形量不应大于0.4 mm,或满足产品技术文件要求。
4.10 活塞回退阻力
按6.10进行试验,每一个活塞的回退阻力应在98 N~300 N范围内,或满足产品技术文件要求。
4.11 活塞启动压力
按6.11进行试验,每一个活塞的启动压力不应大于120 kPa,或满足产品技术文件要求。
4.12 工作耐久性
4.12.1按 6.12 进行试验后,在活塞、密封圈及缸孔内壁上允许有无损害功能的磨损,定钳总成不应有影响使用功能的损坏。
4.12.2 试验后的各项性能指标应满足以下要求:
a)低压密封性应满足 4.3要求;
b)高压密封性应满足 4.4要求;
c)其拖滞扭矩在制动盘第 1圈转动过程中的最大值不应大于5 N•m,在第10圈转动过程中的最大值不应大于3 N•m。
4.13 高温高压耐久性
4.13.1 按6.13进行试验后,各零件不应产生影响使用功能的变形或损坏。
4.13.2 试验后的低压密封性和高压密封性应分别满足4.3和4.4要求。
4.14 振动耐久性
按6.14进行试验后,定钳总成不应有破坏、龟裂、零件脱落及剪断等影响使用功能方面的损坏,螺纹类零件的拧紧扭矩下降值不应大于产品技术文件规定扭矩下限值的20%;在试验过程中不应有泄漏。
4.15 防水性能 按6.15进行试验后,定钳总成缸体内部及活塞防尘罩内部不应有水浸入。
4.16 扭转疲劳强度 按6.16进行试验后,定钳总成不应产生影响使用功能的变形或损坏,在试验过程中不应有液压泄漏。
4.17 安装螺孔强度按6.17进行试验,定钳总成两个安装螺孔破坏或螺套转动时的力矩均不应低于产品技术文件规定的最大紧固力矩的3倍。
4.18 爆破压力按6.18进行试验,定钳总成的爆破压力不应低于35 MPa,不得出现龟裂和损坏,制动钳及油管连接处应无液体泄漏。
4.19 制动性能按6.19进行试验,定钳总成的制动性能应满足产品技术文件要求。
4.20 动态拖滞性能按6.20进行试验,定钳总成在400 r/min和800 r/min转速下的动态拖滞性能应满足表1要求,或满足产品技术文件要求。
表1 动态拖滞性能要求
4.21 制动噪声
按6.21进行试验,定钳总成的制动噪声应满足产品技术文件要求。
4.22 不均匀磨损试验
按6.22进行试验,定钳总成的制动衬块沿圆周方向的周向不均匀磨损量不应大于1 mm,沿直径方向的径向不均匀磨损量不应大于0.5 mm;定钳总成的内、外制动衬块的平均磨损量差值不应大于1 mm。
4.23 耐腐蚀性
按6.23进行试验后,定钳总成应满足QC/T 592—2013中4.12的要求。
4.24 漆层性能
按6.24进行试验,制动钳壳体漆层的耐化学试剂性能应满足T/CAAMTB 84的要求。
5 试验相关要求
5.1 试验设备要求
5.1.1 制动钳综合性能试验台
用于替代制动盘和衬块总成的测量夹紧力的模拟工装,其刚性不应低于实车制动盘、衬块总成。模拟工装不应影响活塞与衬块总成之间的正常接触。试验夹具应保证制动钳安装面与制动盘的平行度不应大于0.10 mm。
5.1.2 制动器惯性试验台
制动器惯性试验台应为单工位惯性式制动器试验台,试验台应装备用于连续记录主轴转速、制动力矩、制动管路压力、一次制动期间所完成的转动圈数、制动时间和制动盘温度的装置,单个采集通道的数据采样频率不应低于50 Hz。试验台的制动管路压力供给系统应满足各种制动工况对制动管路压力的要求,并保持稳定。制动管路压力升、降速率应为25 MPa/s±5 MPa/s。测量制动盘、制动衬块温度的装置和热电偶应满足QC/T 556的相关规定。
5.1.3 测量仪器
用于测量压力、力、位移的仪器或仪表的精度等级不应低于0.5级。
5.2 样件要求
5.2.1 样件应为按经规定程序批准的技术文件制造的产品。
5.2.2 样件的外表面应清洁,无锈蚀、毛刺、裂纹和其它缺陷。
5.2.3 样件应配备在制动衬片需要更换时采用声学或光学报警装置向在驾驶座椅上的驾驶员报警的装置。
5.2.4 试验顺序和试验项目组合宜按表 2进行,每组样件数量宜为 3件。
5.3 试验条件
5.3.1 除非另有规定,试验环境温度应为5 ℃~38 ℃。
5.3.2 制动液容器的液面距制动钳放气孔的高度应为600 mm±50 mm,或与实车状态下的高度相当。
5.3.3 试验前,全新样件需注入制动液并在室温下放置不少于 24 h。5.3.4 高压试验时应做好安全防护。
表2 试验顺序和试验项目组合
6. 试验方法
6.1 试验方法 静置密封性
6.1.1 将定钳总成按实车安装状态固定到试验台上,将液压制动软管连接制动钳进液口,并按产品技术文件规定的最小扭矩进行紧固。
6.1.2 对系统进行排气后,按产品技术文件规定的最小扭矩紧固放气螺钉,然后去除活塞防尘罩。
6.1.3 调整制动液油壶液位高度,使制动钳内部形成10 kPa ±2 kPa的压力。6.1.4 静置24小时后,检查定钳总成制动液泄漏情况。
6.2 真空密封性按QC/T 592—2013中5.1.1进行试验。
6.3 低压密封性
6.3.1 将定钳总成按实车安装状态固定到试验台上,然后将压力源加压管路连接到制动钳进液口,制动盘可用模拟制动盘。
6.3.2 从制动钳进液口加压,当压力达到150 kPa±10 kPa时,截断压力源。
6.3.3 稳压5 s,记录此后30 s内压力下降值,然后释放定钳总成中的压力。
6.4 高压密封性
6.4.1 将定钳总成按实车安装状态固定到试验台上,然后将液压源加压管路连接到制动钳进液口,彻底排净系统内空气,制动盘可用模拟制动盘。
6.4.2 从制动钳进液口加压,当压力达到20 MPa±0.5 MPa时,截断压力源。
6.4.3稳压5 s,记录此后30 s内压力下降值,然后释放定钳总成中的压力。
6.5 放气螺钉密封性
6.5.1 将放气螺钉的螺纹部位涂上制动液或防锈油后,安装到制动钳上,以产品技术文件规定的最小拧紧扭矩拧紧放气螺钉,然后从制动钳进油口施加液压至35 MPa±0.5 MPa,保压5 s后卸压至零。
6.5.2 松开放气螺钉,以产品技术文件规定的1.3倍最大拧紧力矩拧紧放气螺钉,然后从制动钳进油口施加液压至35 MPa±0.5 MPa,保压5 s后卸压至零,如此反复3次。6.5.3 松开放气螺钉,按产品技术文件规定的最小拧紧力矩拧紧放气螺钉,然后从制动钳进液口施加35 MPa±0.5 MPa的液压,保压5 s后卸压至零。6.5.4 每步操作完成后,检查定钳总成龟裂和损坏情况,以及制动钳及放气螺钉处制动液泄漏情况。
6.6 油管连接螺纹密封性
按QC/T 592—2013中5.1.5进行试验,但将1.3倍最大拧紧力矩更改为2倍最大拧紧力矩。
6.7 所需液量
6.7.1 将定钳总成按实车安装状态固定到试验台上,制动盘可用模拟制动盘,宜采用真空加注方式将系统抽至真空度为99.8 kPa±2 kPa,然后充入制动液。
6.7.2 给制动钳施加1.0 MPa的压力,使制动钳活塞在密封件上滑动至少3 mm。
6.7.3打开放气螺钉,手动将活塞退回,然后锁紧放气螺钉。
6.7.4 重复6.7.2、6.7.3步骤3次。
6.7.5 使用新制动衬块总成,在制动衬块和制动盘之间各放置一个厚度为0.6 mm的钢垫片。加压至16.0 MPa,保持2 s后卸压至零,并重复3次。6.7.6 去掉0.6 mm的钢垫片。
6.7.7 给制动钳施加1.0 MPa的压力,保持2 s后卸压至零,重复10次后静置60 s。
6.7.8 以2 MPa/s±0.5 MPa/s的加压速率加压至16.0 MPa±0.5 MPa或产品技术文件规定的压力,同时记录并绘制所需液量V随输入压力P的变化曲线(简称“P-V曲线”,下同)。对于不带液量传感器的测试系统,可测量建压过程中加压装置的活塞位移d随输入压力P的变化关系,按公式(1)计算所需液量V。
式中:
V——制动钳从0 MPa建压至压力P的所需液量,单位为毫升(ml);
d——加压装置的活塞缸径,单位为毫米(mm);
s——从0 MPa建压至压力P时加压装置的活塞位移量,单位为毫米(mm);
V0——测试系统不带定钳总成样件时,从0 MPa建压至压力P的系统所需液量,单位为毫升(ml)。
6.7.9 将定钳总成的衬块总成更换为圆形金属制动衬块(形状如图3所示),用于模拟新件状态的制动衬块厚度。重复6.7.5~6.7.8,测量圆形金属制动衬块(不带垫片)状态下的P-V曲线。
6.8 拖滞扭矩按QC/T 592—2013中5.3进行试验。
图3 圆顶钢块尺寸示意图
6.9 钳体刚性6.9.1 将定钳总成固定于安装架上,然后将液压源加压管路连接到制动钳进液口,彻底排净系统内的空气。
6.9.2 钳体变形量测量点应选择在平坦部位,避开铸件表面的凹凸不平处,减少测量误差。测量点原则上应位于活塞轴线上,如果活塞轴线上不能测量时,可选在其它有代表性的位置上。也可参照图4选取钳体刚性较为薄弱的中心位置。
6.9.3 安装位移测量装置。
6.9.4 对制动钳施加液压至10.0 MPa±0.5 MPa或产品技术文件规定的压力,保压5 s后卸压。如此反复进行5次,将位移传感器数值清零。
6.9.5 对制动钳缓慢加压至10.0 MPa±0.5 MPa或产品技术文件规定的压力,记录钳体两侧在活塞轴线上的变形量随压力的变化曲线。
6.9.6 分别测量钳体在10.0 MPa压力下沿液压缸轴线方向内外两侧的单侧变形量,并计算两侧钳体最大位移量绝对值之和,即为钳体在活塞轴线方向的总变形量。
6.9.7 对于包含不同缸径活塞的定钳总成和多活塞定钳总成,可进一步选取其他有代表性的测量点,重复步骤6.9.3~6.9.6,并取多次测量结果中的最大值作为测试结果。
图4 钳体刚性变形量测量点示意
6.10 活塞回退阻力
6.10.1 将定钳总成去除衬块总成后按图5安装到试验台上,将气压或液压源加压管路连接到制动钳进液口。
6.10.2 选取一个被测活塞并在其中心位置安装好传感器探头,对其它不测量的活塞进行限位。
图5 活塞滑动阻力和启动压力试验装置示意图
6.10.3 对制动钳施加压力使被测活塞缓慢推出2 mm~3 mm,卸压后通过推拉装置将活塞推到原位,以此作为一次操作,重复5次。
6.10.4 对制动钳施加压力使被测活塞缓慢推出2 mm~3 mm,卸压后通过推拉装置的推杆以不大于0.5 mm/s的速度匀速将活塞回推,记录活塞回推1 mm过程中的最大力,即该被测活塞的回退阻力。
6.10.5 重复步骤6.10.2~6.10.4,逐个完成所有活塞的回退阻力测量。
6.11 活塞启动压力
6.11.1 完成6.10试验后,通过推拉装置将活塞推回原始位置。
6.11.2 通过气压或液压源对制动钳缓慢加压,推动被测活塞向外移动1 mm,记录活塞刚开始移动时的输入压力,即该被测活塞的启动压力。
6.11.3 按上述步骤逐个完成所有活塞的启动压力测量。
6.12 工作耐久性
按QC/T 592-2013中5.10.2进行试验。
6.13 高温高压耐久性
6.13.1 将安装新制动衬块的定钳总成按实车安装状态安装到试验台上,然后将液压源加压管路连接到制动钳进液口,排净系统中的空气。
6.13.2 在120 ℃±2 ℃的环境温度下,以13.5 MPa±0.5 MPa的制动液压和0.278 Hz±0.028 Hz制动频率,连续进行5×104次制动。
6.13.3 将新制动衬块更换成全磨损状态的制动衬块,再进行5×104次制动。
6.13.4 试验结束后,按6.3和6.4分别进行低压密封性和高压密封性,检查并记录定钳总成各零件是否有影响使用功能的变形和损坏。
6.14 振动耐久性
按QC/T 592-2013中5.10.3进行试验。
6.15 防水性能
按QC/T 592-2013中5.11进行试验。
6.16 扭转疲劳强度
按QC/T 316进行试验,试验次数为35万次。
6.17 安装螺孔强度
6.17.1 将定钳总成按实车安装状态安装到试验台上。
6.17.2 选取其中一个制动钳固定螺栓,以不超过3 r/min的速度对其施加力矩,直到该安装螺孔破坏或者安装螺纹套同螺栓一起转动,记录此时的力矩。
6.17.3 选取另外一个安装螺孔,重复6.17.2。
6.18 爆破压力
6.18.1 将定钳总成按实车安装状态固定到试验台上,然后将液压源加压管路连接到制动钳进液口,排净系统内空气,制动盘可用模拟制动盘。
6.18.2 以100 MPa/min±20 MPa/min的速度对定钳总成施加压力至36 MPa±0.5 MPa,保持5 s后卸压。
6.18.3 检查定钳总成龟裂和损坏情况,以及制动钳及放气螺钉处制动液泄漏情况。
6.19 制动性能按SAE J2522进行试验。
6.20 动态拖滞性能
6.20.1 试验转动惯量按附录A规定,制动器温度测量方法及热电偶安装要求按QC/T 556规定,试验过程中的冷却风速为11 m/s,冷却空气的温度为室温。
6.20.2 磨合试验。制动初始车速65 km/h,制动末速度小于等于1 km/h,制动初始温度120 ℃±2 ℃,制动减速度3.5 m/s2,制动次数 200次。6.20.3 调整制动盘端面跳动量,使其在距制动盘外缘10 mm±2 mm处的工作面所测的端面跳动量不应大于0.05 mm。
6.20.4 将定钳总成的活塞完全退回,退回两侧的制动衬块,使制动盘与制动衬块不得接触。
6.20.5 将扭矩传感器数值置零至0 ±0.05 N•m。
6.20.6 对制动钳预施加0.3 MPa±0.1 MPa的液压,同时记录压力、所需液量随时间的变化曲线。
6.20.7 再次对制动钳预施加0.5 MPa±0.1 MPa的液压,以使制动衬块紧贴制动盘,同时记录压力、所需液量随时间的变化曲线。
6.20.8 对制动钳施加0.5 MPa± 0.1 MPa的液压,保持时间10 s± 2 s后卸压至零。
6.20.9 使制动盘以100 r/min±10 r/min旋转120 s± 1 s,同时测量并记录制动盘转动过程中的扭矩,并计算去除前后10 s后的中间100 s的平均扭矩值。
6.20.10 重复6.20.8至6.20.9步骤6次,但施加液压0.5 MPa±0.1 MPa依次变更为1.0 MPa±0.1 MPa、1.8 MPa±0.1 MPa、2.5 MPa±0.1 MPa、5.0 MPa±0.1 MPa、7.0 MPa±0.1 MPa和10.0 MPa±0.1 MPa。6.20.11 以6.20.4~6.20.10为一个循环,重复该循环3次。
6.20.12 重复6.20.4至6.20.11,但制动盘转速100 r/min±10 r/min变更为400 r/min±10 r/min。
6.20.13 重复6.20.4至6.20.11,但制动盘转速100 r/min±10 r/min变更为800 r/min±10 r/min。
6.20.14 动态拖滞性能试验步骤及顺序可见表3。
6.21 制动噪声
按QC/T 1167进行试验。
6.22 不均匀磨损试验
6.22.1 试验转动惯量、温度测量及冷却风速等试验相关要求同6.20.1。
6.22.2 按6.20.2进行磨合试验。
表3 动态拖滞性能试验步骤及顺序
6.22.3 用精度不低于0.1 g的天平测量制动衬块的质量,使用分辨率为0.001 mm、测量精度为0.01 mm的螺旋千分尺按图6测量制动衬块的厚度,并按附录B规定表格记录。
6.22.4 按表4规定的不均匀磨损试验条件,以A、B、C作为一个试验循环,重复该循环2次。
6.22.5 每完成1200次制动试验后,检查制动衬块的磨损情况,按6.22.3测量并记录制动衬块的质量和厚度,然后按公式(2)分别计算制动衬块厚度测量点位置1~位置8的磨损量,并计算平均磨损量。
式中:
δi——制动衬块厚度测量点位置i 的制动衬块厚度磨损量,单位为毫米(mm);
di——制动衬块厚度测量点位置i 的制动衬块厚度,单位为毫米(mm);
d0——磨合试验后,制动衬块厚度测量点位置i 的制动衬块厚度,单位为毫米(mm)。
6.22.6 按公式(3)计算周向不均匀磨损量的最大值,按公式(4)计算径向不均匀磨损量的最大值。
式中:
δi——制动衬块厚度测量点位置i 的制动衬块厚度磨损量,单位为毫米(mm);
δc——制动衬块的周向不均匀磨损量最大值,单位为毫米(mm);
δr——制动衬块的径向不均匀磨损量最大值,单位为毫米(mm);
δi, j——制动衬块厚度测量点位置i 和j 的厚度磨损量差值,即不均匀磨损量,单位为毫米(mm)。
6.22.7 计算定钳总成的内、外制动衬块的质量磨损差值、厚度平均磨损量差值。
6.22.8 重复6.22.4~6.22.7步骤3次,累计进行4800次制动试验。
6.22.9 试验完成后,评价定钳总成的不均匀磨损情况。
图6 制动衬块厚度测量点位置示意图
表4 不均匀磨损试验条件
6.23 耐腐蚀性按QC/T 592—2013中5.12进行试验。
6.24 漆层性能对制动钳壳体漆层按T/CAAMTB 84进行耐化学试剂性能试验。
试验转动惯量确定方法
A.1 前制动器试验转动惯量计算方法
前制动器的试验转动惯量按(A.1)进行计算:
式中:
Iq——前制动器转动惯量计算值,单位为千克二次方米(kg·m2);
Ga——车辆满载总质量,单位为千克(kg);
b——重心至后轴距离,单位为米(m);
hg——车辆满载时质心高度,单位为米(m);
r——车轮滚动半径,单位为米(m);
L——车辆轴距,单位为米(m)。
A.2 后制动器试验转动惯量计算方法
后制动器的试验转动惯量按(A.2)进行计算:
式中:
Ih——后制动器转动惯量计算值,单位为千克二次方米(kg·m2);
Ga——车辆满载总质量,单位为千克(kg);
a——重心至前轴距离,单位为米(m);
hg——车辆满载时质心高度,单位为米(m);
r——车轮滚动半径,单位为米(m);
L——车辆轴距,单位为米(m)。
附录B
(规范性)
不均匀磨损试验记录表
B.1 不均匀磨损试验记录表
不均匀磨损试验数据按表B.1进行记录。
表B.1 不均匀磨损试验记录表
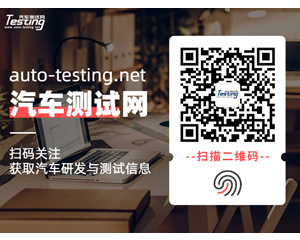
最新资讯
-
商用车及工程机械行业专场:NVH 及语音音频
2025-08-01 17:12
-
理想i8和重卡对撞测试引争议,东风柳汽发声
2025-08-01 15:52
-
艾德克斯IT-N2100 系列太阳能阵列模拟器
2025-08-01 15:43
-
ITECH重磅发布IT2705直流电源分析仪,重构
2025-08-01 15:34
-
现代汽车新一代混合动力系统:以技术革新引
2025-08-01 15:32