可调牵引车表面气动设计空间的表征
摘要
拖车定位在牵引车-拖车组合的整体空气动力学中起着重要作用,并且根据配置和预期用途而有很大差异。为了尽量减少拖车位置范围内的空气阻力,可以使用可调节的空气动力装置。为了获得最大的效益,需要确定每个拖车位置气动装置的最优位置。这可以通过表征由拖车高度和拖车间隙长度组成的二维设计空间来实现,并以空气动力阻力作为响应。采用基于Lattice-Boltzmann的方法进行CFD模拟,并结合modelfrontier创建多个克里格响应面。仿真分多个阶段进行,允许生成中间响应面来估计预测误差并跟踪响应面收敛。利用这些响应面生成给定气动装置的最优定位图。通过获得多个拖车配置的定位图,该方法得到了进一步完善。
1 表征方法
表征给定可调气动装置性能的第一步是确定并适当地参数化设计空间。这包括在连续范围内或离散范围内确定周围车辆几何形状和空气动力装置的可能位置,并确定完整描述这些几何形状变化所需的各种独立参数。然后对可调装置的每个位置,在每个参数范围的最小值、最大值和中点处进行气动阻力评估。通过Kriging算法,通过这些评估得出的车辆阻力系数为气动装置的每个位置创建响应面,从而得出设计空间中所有中间点的预测阻力值。
阻力评估点的分布跨越整个设计空间,因此通过消除在响应面创建过程中外推的使用,最大限度地减少了结果响应面的误差。评估点之间的均匀间距还确保了气动装置的每个位置都在同一组拖车位置上进行评估,从而防止响应面出现偏差。图1显示了由两个独立参数组成的设计空间的样本分布。
图1 双参数设计空间的样本评估分布图,其中蓝色圆圈表示初始批评估,绿色正方形表示可能的第二组评估,红色三角形表示可能的第三组均匀间隔评估
进一步的气动阻力评估,然后进行每个位置的可调装置在拖车位置对应的设计空间的中心和每个极限边界之间的中点。这些增加的评估通过增加Kriging算法的插值点的数量来改进响应面,同时继续保持点之间的均匀间距。这种分布可以很容易地扩展到任意数量的独立参数。图2显示了一个使用三个参数的示例。
图2 三参数设计空间的样本评估分布图,其中蓝色圆圈表示初始批评估,绿色正方形表示可能的第二组评估,红色三角形表示可能的第三组均匀间隔评估
通过计算各中间阶段响应面的平均绝对误差,跟踪了当气动阻力数据增加时响应面的收敛性。响应面的平均绝对误差定义为设计空间中相应位置的计算阻力与预测阻力之差的实际平均值。这种递归平分过程在对应于前一个位置之间的中点的连续位置重复。这可以重复,每个连续的迭代细化响应面,直到达到所需的分辨率。
通过对气动装置的每个位置在设计空间内的附加点进行阻力评估,并将所得阻力系数与相应响应面预测的阻力系数进行比较,可以验证最终精确响应面的分辨率。
所得的精细化响应面然后彼此相交,以产生可调节装置的最终空气动力学性能图。该图显示了可调节装置的位置,该装置可以在给定的拖车高度和牵引车-拖车间隙长度的范围内,在指定的操作车辆条件下减少空气动力学阻力。
安装在拖车上的气动装置主要是通过偏转气流来减少阻力,从而在牵引车与拖车之间的间隙上方和周围创造更顺畅的气流。气流的这些变化沿着拖车的长度向下传播,并可能与拖车上安装的空气动力学装置相互作用。它们还可以通过与车身下气流的相互作用影响拖车产生的低压尾迹区,从而影响拖车基底压力阻力。对拖车安装的可调装置进行气动阻力评估,可以利用前阻力值来创建各种响应面。前阻力定义为车辆从牵引车前部到拖车中点的累积阻力。
2 示例实现的细节
2.1可调顶棚
将参数化方法应用于两种不同的8级牵引车-挂车配置的具体案例。所研究的气动装置是一个气动饰片的概念,如图3所示,用于引导从拖拉机车顶后缘过渡到拖车顶部的气流。扩展安装在车辆车顶的后部,并且可以调整到各种位置。使用定位点来指导操作最佳的饰片定位(图4)。
图3 安装气动装饰装置的图像
图4 Volvo VNL670®可调节车顶扩展器定位图像
2.2参数描述/范围
气动饰片定位研究有三个参数,如表1所示,并评估它们对前阻力的影响。如表2所示,有5个独立的饰片位置按高度增加的顺序排列,由饰片杆附着在哪个支架孔来定义(见图4)。第二个参数是牵引车间隙的长度,从牵引车驾驶室后壁的最大x位置到拖车的前表面测量。最后一个参数是拖车前缘相对于车架轨道顶部的高度
表1 气动饰片定位研究的参数说明和范围
表2 饰片后缘中心垂直高度差占位置1和位置5之间总差的百分比
2.3分析方法
车辆阻力系数数值通过基于lattice-boltzmann的仿真工具PowerFLOW进行计算仿真得到。模拟设置与SAE国际地面车辆推荐实践J2966一致,以近似道路状况。在顶棚和壁面无摩擦边界条件下,采用小于1%堵塞的计算域对全尺寸模型进行了仿真。地板以无滑移边界条件建模,移动速度相当于65英里/小时的自由流速度。车辆位于一个4.5度偏航角。拖车是一个通用的53 '干货车拖车。驾驶室和货箱设置符合65mph的旋转壁面条件。在雷诺数为6.33×10e6、特征长度为3.245m的条件下进行了模拟。
采用modeFRONTIER优化环境,将挂车高度、牵引车-挂车间隙长度和气动饰片位置作为输入变量,以前阻力作为期望的响应变量,实现仿真过程的自动化。这允许自动后处理,利用车辆阻力系数为每次运行。这些阻力系数用于生成每个饰片位置的克里金响应面,这些响应面进一步后处理以生成饰片定位图。
图5 仿真中采用了具有代表性的牵引车-挂车间隙网格结构
3 结论
3.1模型1
图6 初始评估分布显示在设计空间的角和中点的阻力评估点
对于第一个牵引车模型,进行了最初的25次模拟运行,以创建初始表征。初始表征的目的是生成一组粗响应面,可以可视化地分析每个饰片位置的整个设计空间的空气动力学阻力趋势。这些粗响应面进一步后处理,并相交在一起,以产生一个粗略的定位图的修剪标签。该地图用于确定设计空间的点,以便进行下一阶段的阻力评估。在设计空间的每个象限的中点处选择评估点,以便在继续保持设计空间样本的均匀性的同时,提供更多平行和垂直于阻力趋势方向的Kriging插值点,如图6所示。
3.1.1初步鉴定
表3列出了初始表征的参数和结果。选取的初始评价点位于设计空间的每个极值边界和中心点。
表3 第一个模型的初始表征结果
两个饰片定位位置生成的响应面如图7和图8所示。这些粗响应面相交以生成初始修剪选项卡定位图,如图9所示。这张图表明,在拖车间隙小而拖车高度大的情况下,为了最大限度地减少阻力,必须将调平片设置在其最大高度,当拖车间隙增大和/或拖车高度减小时,较低的调平片高度是最有利的。这与气流离开车顶整流罩的空气动力学是一致的,必须充分偏转以避免拖车正面撞击,同时也要尽量减少偏转表面的正面面积,以减少空气动力学装置上的流动停滞。选择额外的阻力评估点,以进一步解决不同最优饰片定位区域之间的边界问题。
图7 第一款车型的初始25次运行中饰板位置1的响应面,颜色表示前阻力大小,黑点表示设计空间中的阻力评估点
图8 第一个模型的初始25次运行中,气动饰片位置5的响应面,颜色表示前阻力大小,黑色点表示设计空间中的阻力评估点
图9 第一款车型的初始25次运行的定位图,颜色描绘了具有最低前阻力的饰片位置。灰色区域描述两个或多个位置之间的阻力差小于0.5counts
3.1.2参数化优化
在研究了最初的一组数据结果后,又对另外25次运行进行了优化。每个饰片位置在附加的四个点上进行分析,这些点位于最初五个设计空间的中点之间。表4列出了精化运行的参数和结果。
表4 第一个模型的参数化细化结果
图10和图11分别显示了对1和5个饰片位置进行45次运行后的最终响应面。这些表面表现出阻力行为的差异,特别是在小拖车间隙和大拖车高度时,位置5可以显著减少阻力。图12显示了细化后的定位图,可以看到粗图显示的前拖动趋势仍然保留,但在不同最优饰片位置区域之间的接口上具有更清晰的定义。
图10 第一款车型共运行45次,饰片位置1的响应面,颜色表示前阻力大小,黑点表示设计空间中的阻力评估点
图11 第一款车型共运行45次,其中饰板位置5的响应面,颜色表示前阻力大小,黑点表示设计空间中的阻力评估点
图12 第一款车型总共45次运行的定位图,颜色描绘了具有最低前阻力的饰片位置。灰色区域描述两个或多个位置之间的阻力差小于0.5counts
利用响应面的平均绝对误差判断各切边位置的初始响应面和最终响应面分辨率。选取1个前阻力计数作为截止值,表示与定位图中±0.5个计数边界区域对应的收敛响应面。从表5可以看出,所有的最终响应面都是收敛的,误差值都很低。图13显示了当将拖动数据添加到trim tab位置1的响应面时,平均绝对误差的减少情况。其他修剪标签位置显示相同的趋势。从导出的定位图中创建最终的定位图,如图14所示。
表5所示 第一种模型的响应面误差分析
图13 响应面收敛图显示,在第一种模型上,饰片定位位置1的平均绝对误差随运行次数的增加而减少
图14 第一个模型总共45次运行的最终定位图
3.2 模型2
对于第二种拖车模型,使用与第一种表征相同的参数进行了全套45次模拟。表6列出了表征的参数和结果。由于设计空间的参数与第一个模型相同,所以使用了相同的评价点。对于一个已知的特征问题,我们可以用一组运行来描述设计空间,而不是一个连续的过程(如模型1中所示)。
图15和图16分别显示了第二个模型中选项卡位置1和5的最终响应面。值得注意的是,与第一个模型相比,响应面的行为有显著差异。这表明,在不同型号的拖拉机上,饰板的空气动力学性能差异很大,这进一步反映在图17所示的饰板定位图中。这张图还显示了在整个设计空间中最佳饰片位置的预期变化,但在最佳区域之间具有不同的边界。
表6 第二个模型的表征结果
使用相同的截止阻力误差值为1计数,对第二个拖车模型进行了类似的收敛研究。从表7可以看出,最终的响应面是收敛的,误差值很低。添加拖动数据时第二个模型的误差减少情况如图18所示。从导出的定位图中创建最终的定位图,如图19所示。
图15 第二款车型共45次运行时饰板位置1的响应面,颜色表示前阻力大小,黑点表示设计空间中的阻力评估点
图16 第二款车型总共45次运行中饰板位置5的响应面,颜色表示前阻力大小,黑点表示设计空间中的阻力评估点
图17 第二款车型总共45次运行的定位图,颜色描绘了具有最低前阻力的饰片位置。灰色区域描述两个或多个位置之间的阻力差小于0.5ocunts
表7 第二种模型的最终响应面误差分析
图18 响应面收敛图显示在第二个模型上,饰片定位位置1的平均绝对误差随运行次数的增加而减少
图19 第二个模型的最终定位图,总共45次运行
4.总结
提出了一种通用气动减阻装置气动效益的表征方法。这包括首先确定拖车和气动装置在一个连续范围内或一组离散位置上的可能位置,然后在拖车位置范围的最小值、最大值和中点处获得每个装置位置的气动阻力值。通过Kriging算法,这些车辆正面阻力系数值用于为每个气动装置位置创建响应面,从而得到设计空间中所有中间点的预测阻力值。在对应于设计空间中心和每个极限边界之间的中点的拖车位置上,对可调节装置的每个位置重复此过程。这可以重复,每个连续的迭代细化响应面,直到达到所需的精度。根据这些克里格曲面,最终的定位图被创建,该图描绘了在设计参数范围内的任何配置下空气动力阻力最小化的空气动力装置的位置。然后利用该方法获得了两种不同型号拖拉机的气动效益图。
第一个模型表明,对于较小的牵引车-挂车间隙长度和较大的挂车高度,为了产生最大的阻力减少,必须将修剪标签设置在其最大设置。随着牵引车与挂车间隙的增大和/或挂车高度的降低,最佳饰边标签位置降低。第二个模型展示了类似的模式,然而,它也表明,修剪标签装置的空气动力学性能在不同的拖拉机模型中差异很大,并显示出最佳位置之间的边界变化。
结果表明,可调气动装置可以提高牵引车间隙长度和高度范围内的燃油经济性。这些装置的空气动力学性能可能取决于牵引车的配置,因此使用有效的表征方法对于最大限度地提高燃油经济性至关重要。
文献来源:
Justin J. Novacek, et al. Characterization of Aerodynamic Design Spaces for Adjustable Tractor Surfaces. SAE Int. J. Commer Veh. 2016,10,9(2):350-358.
- 下一篇:纯电动汽车车底风噪声传递的数值分析
- 上一篇:轿车主动格栅与主动气坝减阻气动分析
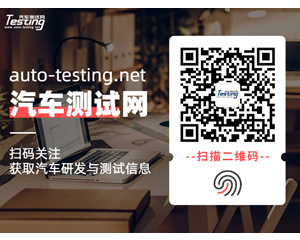
最新资讯
-
商用车及工程机械行业专场:NVH 及语音音频
2025-08-01 17:12
-
理想i8和重卡对撞测试引争议,东风柳汽发声
2025-08-01 15:52
-
艾德克斯IT-N2100 系列太阳能阵列模拟器
2025-08-01 15:43
-
ITECH重磅发布IT2705直流电源分析仪,重构
2025-08-01 15:34
-
现代汽车新一代混合动力系统:以技术革新引
2025-08-01 15:32