汽车试验场搓板路强化系数的研究
【摘要】通过对试验车辆的疲劳寿命估算,利用道路强化系数计算方法,研究汽车试验场搓板路强化系数,为汽车可靠性强化道路试验规范的制定、验证和优化提供依据。采用有限元动态仿真技术模拟汽车在试验场搓板路的试验过程, 仿真与试验结果进行对比验证,对应的特征参数基本一致。利用有限元仿真的结果对样车关键部件进行疲劳寿命分析和预测,求取试验场搓板路面的强化系数,并得到搓板路强化曲线。研究的结果应用于指导汽车路试规范的准确制定,减少试验的盲目性,增强试验的可信度,缩短研发周期和试验成本。
【关键词】汽车工程;强化系数;有限元仿真;搓板路;可靠性
汽车可靠性强化试验是考核和验证汽车可靠性、 耐久性的重要手段,试验场各种强化路面的强化系数测定是制定可靠性强化试验规范和对强化试验结果进行科学评价的关键。强化系数也称为加速系数或快速系数,其反映强化试验相对于基准路面条件下的强弱程度,本质上是试验对象在实际使用中的寿命与强化试验中的寿命之比。汽车在试验场搓板路上可靠性强化试验仿真,并 计算道路的强化系数,可以指导汽车路试规范的准确制定和优化,缩短试验周期,降低成本,并具有风险小、试验数据的重复性好的优点。
1 疲劳寿命估算理论和强化系数计算方法
疲劳寿命预测算法采用Smith-Watson-Topper(简称 SWT )方程,并考虑了平均应力的影响。疲劳寿命分析是基于Palmgren-Miner线性累积损伤法则(简称 Miner 法则),其形式简单、使用方便,在工程分析中应用广泛。 1.1 Smith-Watson-Topper方程 考虑平均应力对疲劳寿命影响的 SWT 方程:
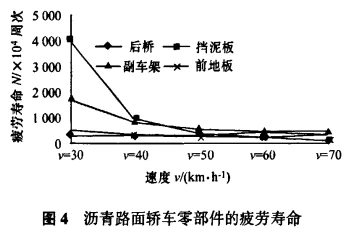
式中,

为最大应力值;

为对应的应变量;b 为疲劳强度指数;c 为疲劳延性指数;

为疲劳延性系数;

为疲劳强度系数;

为载荷反向次数(也称失效的半周期数)。(1)

为载荷的周期数,即载荷循环的次数,以此来表达试验样件的疲劳寿命;(2)

用以修正实际测试条件下的非零平均应力对样件疲劳过程的影响。如果应力和应变是从线弹性分析中得到,则需要经过 Ginka 能量密度法计算得到真实的应力和应变,才能应用到方程中。 1.2 Palmgren-Miner线性累积损伤法则 线性累积损伤法则基于如下假设:试样受交变载荷的作用产生变形,所吸收的能量达到极限值时产生疲劳破坏,且试样吸收的能量与交变载荷的循环次数成正比。例如,有一作用在试样上产生应变的应力

,其实际循环次数为

时,试样吸收的能量为

,其中 j= l,2,…,则该假设可以表达为:
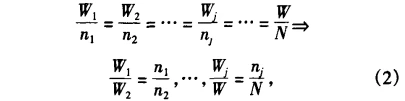
式中,W 为试样破坏前可吸收的总能量;N 为应力

作用时试样破坏前总循环数。 因此,试样在某一应力和应变下的疲劳寿命可以用极限循环次数来表达。 如果试样的加载历史由

个不同的应力

构成, 各应力条件下的疲劳寿命为

,实际循环次数为

,其中
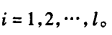
根据线性叠加原理和线性累积损伤法则的假设,试样实际吸收的总能量为

,即作用于试样上产生应变的多个应力造成疲劳失效的总效果相当于每个应力作用效果的叠加,这就是线性累积损伤法则。可以得出:

试样疲劳损伤值的表达式可以定义为:

当疲劳损伤值D =1时,试样吸收的累积能量

达到极限值W,试样发生疲劳破坏。1.3强化系数的计算 VPG 仿真预测的疲劳寿命以循环次数表示,当仿真时间和速度不同时,相同的循环次数会得到不同的里程数,无法进行比较,可以根据公式(5)换算成寿命里程,而且表达更为直观。

式中,N 为循环次数;L 为行使里程;v 为仿真设定的速度;t为仿真设定的时间。 采用试验场沥青路面替代普通城市路面进行强化系数的估算,设沥青路的强化系数为1,即汽车在沥青路面上进行可靠性试验视为与普通城市道路行驶等同,则其他强化路面相对于沥青路面的强化系数可以表达为:

式中,
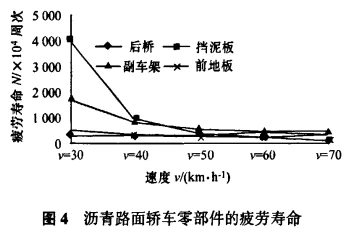
为样件在沥青路面试验的疲劳寿命;

为样件在其他强化路面试验的疲劳寿命。 2 汽车在搓板路可靠性试验仿真 2.1系统有限元建模与仿真 根据汽车道路试验的特点,在不影响精度的前提下,系统建模的重点主要包括车身的结构、行驶系统等;在驾驶员与副驾驶员位置、前后车门、行李箱等部位施加了集中质量载荷。仿真系统有限元模型如图1所示。
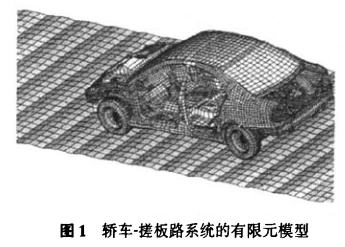
试验场搓板路面来源于实际试验路面的三维实体建模及其有限元网格划分,仿真的整车模型是在某车型白车身的基础上,增加了发动机、悬架和轮胎等主要构成部件,并创建用于车身疲劳和寿命分析的轮胎模型,整车共212个部件、68 626个节点、65 138 个单元。 设置仿真速度为30、40、50、60、70 km/h,轮胎和路面的为点一面(NODES-TO-SURFACE)接触,轮胎接触类型设置为INTERIOR,以避免轮胎模型中的橡胶材料的体单元在计算过程中出现负体积以及节点速度无限大等问题。为了控制由单点积分引起的沙漏,保证求解精度,设置沙漏系数为0.1,仿真过程设定为0.6 s。 2.2仿真结果的试验验证在车速为50 km/h的条件下进行试验和仿真,采集中央通道的 X、Y、Z 方向的加速度信号进行对比验证,如图2所示。
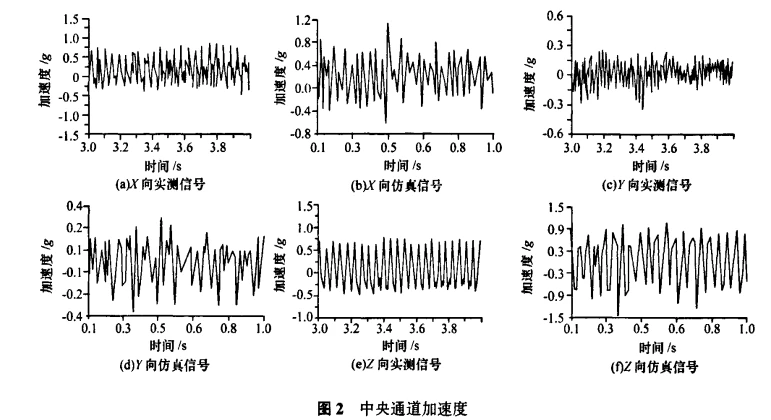
通过中央通道的仿真和试验的加速度曲线对比分析表明,建立的汽车一搓板路仿真模型能够较真实地再现试验结果,所建模型和仿真数据有较高的精度,满足工程应用的要求。3 疲劳寿命分析与强化系数计算 3.1疲劳寿命分析 车辆分别以5种车速在沥青路和搓板路上进行仿真,并针对汽车的后桥、挡泥板、副车架、前地板进行疲劳分析和疲劳寿命计算。 疲劳寿命云图能够清晰表达车辆及其零部件动态的应力应变以及疲劳失效情况,其中车辆前地板在各速度条件下的疲劳寿命云图,如图3所示;车辆其他部件与前地板的疲劳寿命云图具有相似的规律性。
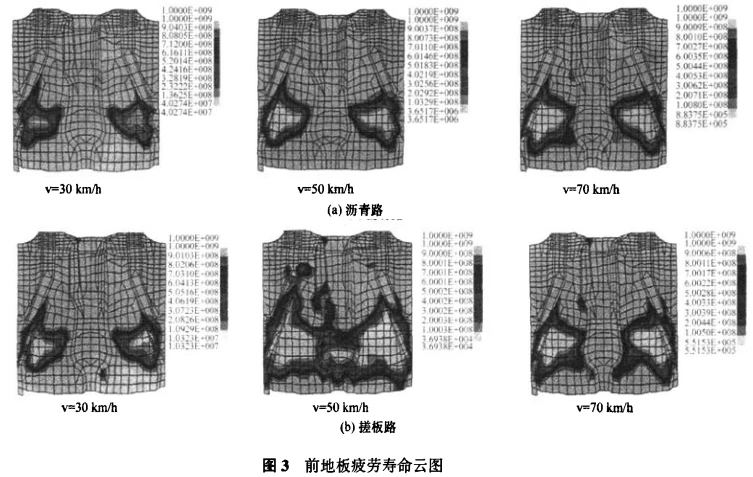
车辆的前地板在各速度条件下的疲劳寿命云图可以看出: (1)疲劳损伤主要集中在前排座椅的正下方的位置,贴近车身两侧的B柱;(2)在相同速度条件下,沥青路的疲劳损伤范围和程度都小于对应搓板路的结果;(3)沥青路仿真试验结果表明,随着车速的增加,疲劳损伤范围扩大、损伤程度加深,疲劳损伤结果具有明显的规律性;(4)搓板路仿真试验结果表明,随试验车速的增加,疲劳损伤范围扩大、损伤程度加深,在车速为 50 km/h 时达到最大值;随车速的继续增加,疲劳损伤范围缩小,损伤程度减弱,在70 km/h之后的疲劳寿命云图与沥青路面试验接近。 因此,汽车在搓板路上进行可靠性试验过程中, 搓板路具有加速和强化零部件疲劳损伤作用,强化程度与试验车速相关。对比不同速度对同一零件疲劳寿命的影响,能够反映车速和疲劳寿命以及搓板路强化程度的关系。 试验样车在沥青路上行驶的主要零部件疲劳寿命曲线,如图4所示。
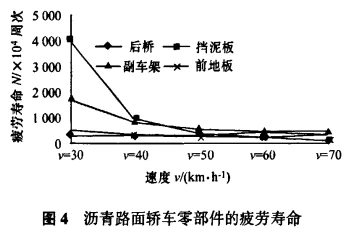
图4可以看出,在低速阶段不同零部件的疲劳寿命有较大的差距,随速度的增加,疲劳寿命及其差距减小、疲劳损伤加剧。试验样车在沥青路上行驶的主要零部件疲劳寿命曲线,如图5所示。
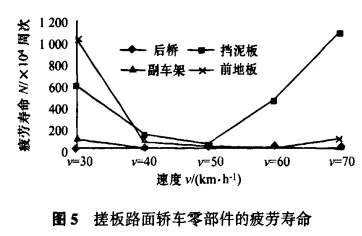
图4和图5曲线对比可以看出,搓板路面试验具有明显的强化作用,随车速的增加,存在最佳强化的速度范围,本例为50 km/h 时试验车辆及其主要零部件的疲劳寿命最小。3.2强化系数和强化曲线强化系数也称为快速系数,其反映强化试验相对于基准条件下的强弱程度。仿真得到疲劳寿命通过公式(4)计算搓板路强化系数,不同车速下的强化系数为强化曲线,试验样车主要零部件搓板路强化曲线,如图6所示。
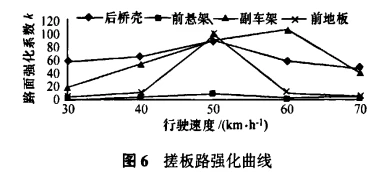
从图6可以看出,汽车在搓板路上进行可靠性强化试验有一定的规律性: 第一、搓板路面对车辆不同部位的强化系数不同; 第二、随速度的增加,强化系数先增大后减小,存在强化程度的最大值。 在实际试验过程中,搓板路试验循环多次反复, 很难保证相同的试验速度;同时,有效试验速度需要尽量兼顾车辆不同部件的强化程度和强化效率的要求。因此,有效速度一般确定为一个速度范围(车辆内部的车速表可以分辨,驾驶人员可以感觉到明显的不同。 因此,针对此虚拟试验样车,速度在50~60 km/h 这个范围内时,搓板路的强化作用较大、强化效率较高,可以确定为最佳有效车速范围。
4 结论
汽车试验场的可靠性强化试验,在路面的强化性能不失真的条件下,最大限度的加速对应于该路面的车辆及其部件的可靠性、耐久性考核,但存在着成本高、周期长、重复性差、获取数据不足等缺点。利用有限元仿真的方法对样车关键部件进行疲劳寿命分析,在保证仿真精度的前提下,对样车关键部件的疲劳寿命进行分析和预测,求取试验场搓板路面的强化系数,能够指导汽车路试规范的准确制定和优化,减少试验的盲目性,增强试验的可信度,缩短研发周期和试验成本,有效解决实车道路试验所存在的问题。研究表明,试验场搓板路的强化系数与试验车速、零部件的疲劳寿命密切相关。
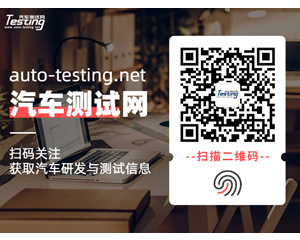
最新资讯
-
商用车及工程机械行业专场:NVH 及语音音频
2025-08-01 17:12
-
理想i8和重卡对撞测试引争议,东风柳汽发声
2025-08-01 15:52
-
艾德克斯IT-N2100 系列太阳能阵列模拟器
2025-08-01 15:43
-
ITECH重磅发布IT2705直流电源分析仪,重构
2025-08-01 15:34
-
现代汽车新一代混合动力系统:以技术革新引
2025-08-01 15:32