某纯电动车前悬麦弗逊悬架弹簧颤鸣声问题的分析与改进
摘 要
纯电动汽车有动力强劲、自重大等特点,这对整车制动性能提出了更高的要求。市场客户又非常关注制动时的整车舒适性,因此,如何全面考虑纯电动汽车制动场景,如何前期充分识别与验证各项制动性能,成为困扰目前制动性能设计的技术难题。本文以某纯电动汽车强度制动后前悬架弹簧颤鸣声问题为研究对象,系统地介绍了弹簧颤鸣声的识别与排查过程,基于制动受力分析与弹簧颤振机理,设计了一种用于验证动态复杂整车问题的静置试验方法。通过静置试验还原了整车问题并进行了弹簧颤鸣声的传递路径分析,识别出弹簧座到车身传递路径是弹簧颤鸣声的关键要素,并且,通过改进弹簧座结构,在静置试验与实车验证了方案的有效性。这为快速解决汽车此类问题和前期制动开发问题识别提供了借鉴与参考。
关键词:制动;弹簧颤鸣声;传递路径;隔振
作者:
沈龙,男,主任工程师,浙江智马达智能科技有限公司, 负责整车NVH性能开发。
张军,男,博士,正高级工程师,吉利汽车研究院(宁波)有限公司,主要研究方向:汽车NVH性能开发。
引 言
近年来,随着清洁能源领域热度不断攀升,纯电动汽车产业也伴随着契机蓬勃发展。纯电动汽车有着超高动力性、自身重量大等特点,这就对制动性能提出了更高的技术挑战。制动过程中的振动噪声问题不仅严重降低消费者的感官体验,更甚者会让消费者产生安全方面的顾虑,继而售后投诉问题频发,大大降低了消费者的满意度及汽车品牌的品牌力,更会导致高昂的售后维护费用。汽车行驶过程中,由于路面不平和动力总成、车轮等旋转部件的激励会导致汽车产生振动噪声,路面激励的输入是汽车振动的基本输入,振动频率一般在0.5-24Hz。往往在汽车开发过程成中只考虑到了悬架弹簧与该激励的避频,忽视了纯电动汽车高强度制动效能往往还会对相邻部件产生高能量冲击激励,这会引发弹簧的颤鸣声。制动过程中引发的悬架弹簧颤鸣声问题属于系统问题,涉及到弹簧、弹簧座、阻尼器、Top Mount等悬架系统零部件。悬架弹簧颤振发生时在弹簧中引起很高的应力,而悬架弹簧属于低阻尼系统,导致弹簧颤鸣声久久不能消散。这是制动性能开发领域中存在的急需解决的技术难题之一。
张立军[1]等在线性假设的条件下, 利用四端参数的分析方法, 研究分析了悬架螺旋弹簧的驻波效应,并发现降低螺旋弹簧端部衬垫的刚度和增大其内部阻尼, 都可以有效的控制螺旋弹簧的驻波效应对悬架振动隔离特性的不利影响。W Sun[2]等采用动刚度矩阵法确定了一种轨道车辆主悬架螺旋弹簧的动刚度,并分析了动刚度和螺旋弹簧一阶固有频率相对关系对车身振动的影响,通过与螺旋弹簧串联橡胶层可以有效减弱传递至车身振动。Shinichi Nishizawa[3]等人通过有限元分析了悬架螺旋弹簧座几何形状及材料对弹簧力线(力线是螺旋弹簧在压缩过程中与弹簧座相互作用产生的反力轴)的影响,橡胶等弹性材料用于弹簧底座会降低噪声振动。刘瑶瑶[4]通过建立整车系统多体动力学模型进行动力学分析结果表明,采用侧载螺旋弹簧后车身受到的加权加速度降低,可提高乘车的舒适性。R. A. Simmons[5]等人的研究表明,弹簧颤振往往是显著的不能被断然忽视,弹簧的内部施加阻尼对弹簧颤振共振是有效的,在设计初期弹簧的颤振频率应该与系统中其他零部件固有频率进行避频处理。另外,部分文献[6-8]采用仿真或试验的方法研究了弹簧的设计方法。
制动过程中ABS触发后的麦弗逊悬架螺旋弹簧颤鸣声问题与ABS系统控制逻辑和悬架系统复杂运动形式相关,属于非稳态和非线性问题,目前无法通过有效的仿真手段进行前期规避,整车制动时的滑移率不能通过台架模拟导致无系统的台架试验进行对悬架弹簧颤鸣声问题进行前期验证。因此,整车NVH开发过程中还未形成系统的解决措施和先期控制手段。
本文基于某纯电动汽车制动ABS触发后,前麦弗逊悬架螺旋弹簧颤鸣声问题的排查分析过程,阐述了弹簧颤鸣声产生机理,并通过静置等效的方法将动态复杂的问题现象快速还原成静态可分析的问题现象,通过静置试验快速的进行传递路径分析查找问题敏感影响因素,通过改进螺旋弹簧上安装座橡胶厚度和骨架结构,在实车验证了方案的有效性,这对提高制动舒适性开发有一定的工程指导价值。
1 前悬架螺旋弹簧颤鸣声的测试分析
某后驱纯电动汽车在平直路面正常行驶遇到突发状况紧急制动时触发ABS(制动防抱死系统),当车停住后车内前排可听见持续的弹簧颤鸣声。ABS工作原理是在检测到轮胎与地面产生滑移后,以200-300ms为时间步长不停释放制动力来达到控制制动力的目的,以保证轮胎以最大的摩擦系数进行制动,从而获得最短的制动距离。为了提升车辆驾乘安全,车辆普遍都配备了各式的主动和被动安全系统,ABS系统便是各车型的标配之一。随着中国汽车保有量的逐步提升,城市路况越来越复杂,紧急制动触发ABS经常发生。且因惯性原因,前轴分配了65%左右的制动力,后轴分配了35%左右的制动力,加大了前悬架的制动激励,增加了前悬架弹簧颤鸣声问题发生率。导致用户在用车过程中产生大量抱怨,也会带来高额的售后维护成本。
通过不同车速及路面反复进行紧急制动评价,发现60kph进行紧急制动后的弹簧颤鸣声明显,且属于消费者常用工况,因此,在平直沥青路上60kph匀速行驶工况作为制动前悬架弹簧颤鸣声问题排查分析的基础工况。
1.1►整车道路测试的传感器布置
结合主观评价结果,初步锁定制动后的噪声问题发生在前悬架,且发声系统应该具有类似弹簧的欠阻尼特征。为了分析此问题的特征与潜在机理,分别在前悬架Knuckle、摆臂、转向器、横向稳定杆、弹簧、Top Mount等悬架零部件结构上和Top Mount车身侧布置加速度振动传感器,在车内前排布置麦克风。传感器布置及坐标系如图1和图2所示。
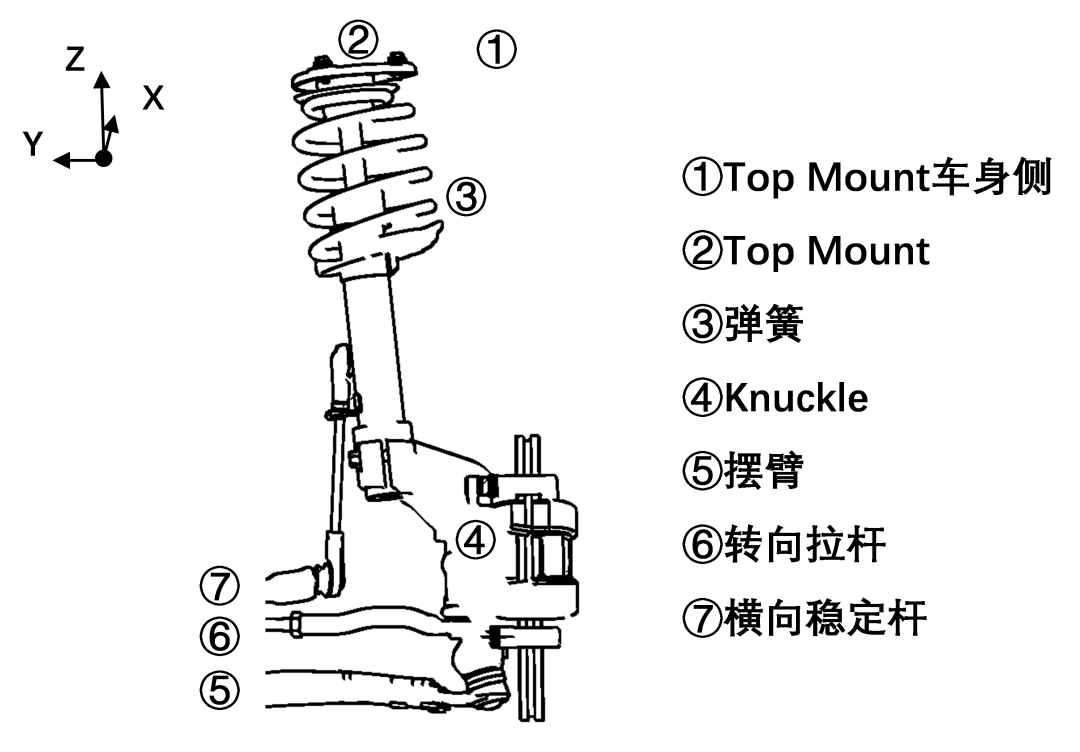
图1 传感器布置及坐标示意图
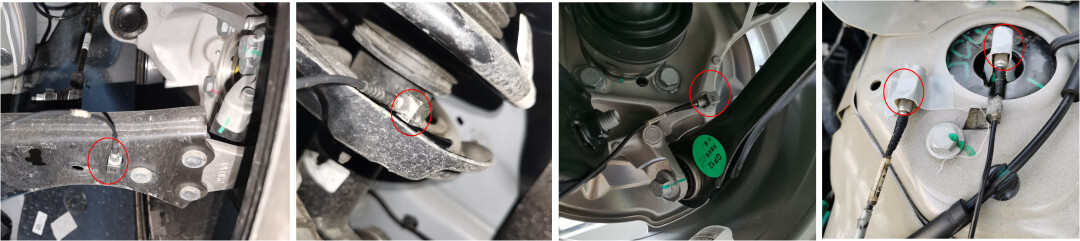
图2 整车测试传感器布置
1.2►颤鸣声的道路测试与分析
图3为制动后颤鸣声时频域测试分析结果,通过对声音数据的回放和主观评价的识别,该制动后的颤鸣声主要特征是持续4s左右的125Hz的单频声音。其中,在车辆制动至静止状态后125Hz低频颤鸣声声压级峰值为47dB(A),为频谱曲线的最高峰值,此频率噪声强度大,衰减慢,是此车颤鸣声问题的关键因素。
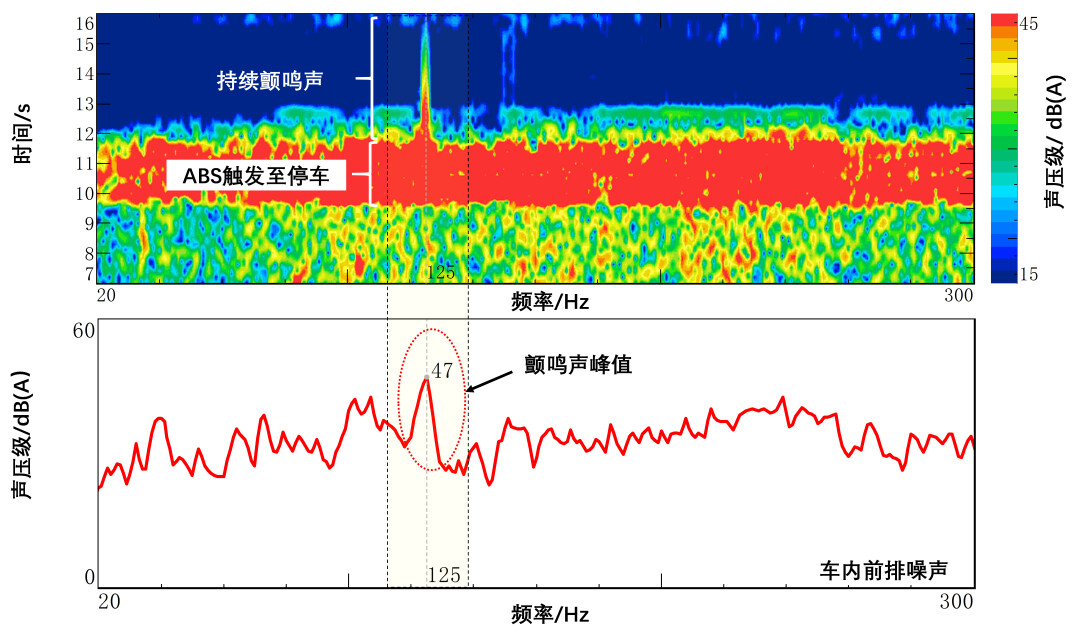
图3 制动后车内前排噪声的时频域分析
1.3►颤鸣声振动的道路测试与分析
车辆制动后,弹簧颤鸣声发生过程中,前悬架各位置的主方向振动频谱与车内前排噪声频谱分析结果如图4所示,通过对比噪声与振动频谱特征,可以得出:(1)问题车辆在60kph匀速行驶进行紧急制动后,车辆停稳后车内有严重的125Hz噪声;(2)前麦弗逊悬架各部件均能捕捉到同频振动峰值,弹簧上振动的主方向为Z向,且振动量级远远大于其他部件,属于声源;(3)Top Mount车身侧和Knuckle振动的主方向为Y向,说明弹簧颤鸣声产生及传递过程涉及悬架系统及车身的复杂耦合结构振动。
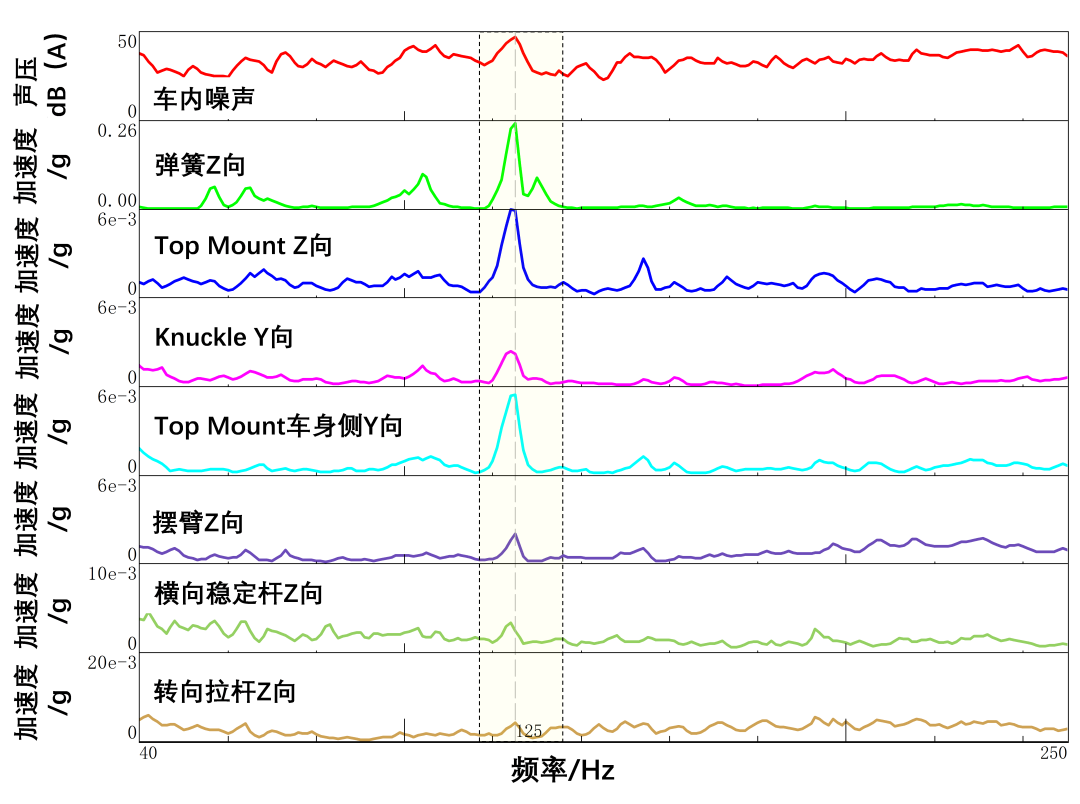
图4 颤鸣声过程中噪声振动频谱对比分析
2 螺旋弹簧振动理论分析
弹簧在接近其固有频率时可以横向和纵向振动,如果一个一端固定的螺旋弹簧,在另一端被给予一个足够快的压缩,在剩余的线圈有时间相应位移之前,末端线圈将被推到他的相邻线圈,以此类推直至传递至扰动的另一端,然后扰动将被反射回来,这个过程将不断重复,直到运动被阻尼消耗。这种现象即为弹簧颤振,弹簧颤振在弹簧中会产生很高的应力,这大约等于弹簧被压缩到其固体长度时的应力。[9]
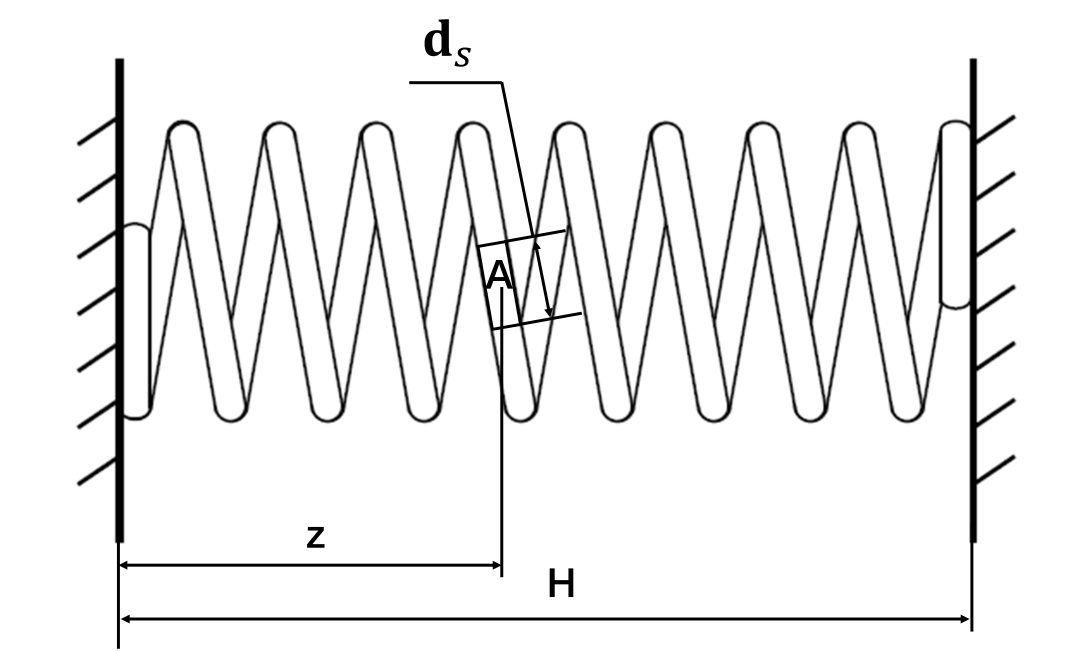
图5 两端固定支承弹簧颤振频率的分析
螺旋弹簧对于未受到载荷或者载荷量相对较小的两端固定的情况下,如图5所示,其颤振计算公式推导如下。令弹簧长度为H,在距离弹簧左端z处取一个微小单元体A,其长度为ds 。A在任意时间t内产生的位移为f,微小单元体A会受到弹性力Fs,阻力Fd,惯性力Fa等力的作用。根据平衡关系,他们的关系如下[10]
Fa=Fs-Fd (1)式中惯性量Fa为单元体A的质量与加速度
的乘积,则Fa可以写成
。在ds长度中F的变化为
,一圈的变化为
,单圈弹性力的变化
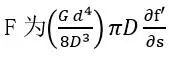

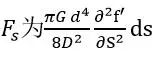
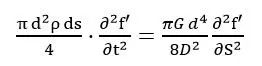
弹簧小段左端z长度内的材料长度S为带入式(2)得到
(3)
式中
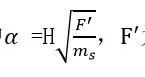
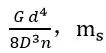

因瞬态变形f既是z的函数,又是t的函数,即


当弹簧两端固定,在两端即z=0和z=H时,因此ω为将α代入v,当弹簧一端固定,另一端为自由状态时,弹簧的颤振频率为
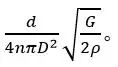
3 前悬架弹簧颤鸣声的静置试验设计
3.1►受力分析及静置激励设计
该车型问题发生于ABS触发工况,具有一定的危险性,且根据前文测试结果,弹簧颤鸣声影响因素耦合复杂,在整车上进行分析验证势必降低效率。为了简单和有效的对颤鸣声问题进行分析及快速进行方案有效性验证,根据如图6所示的受力结果,设计静置试验。
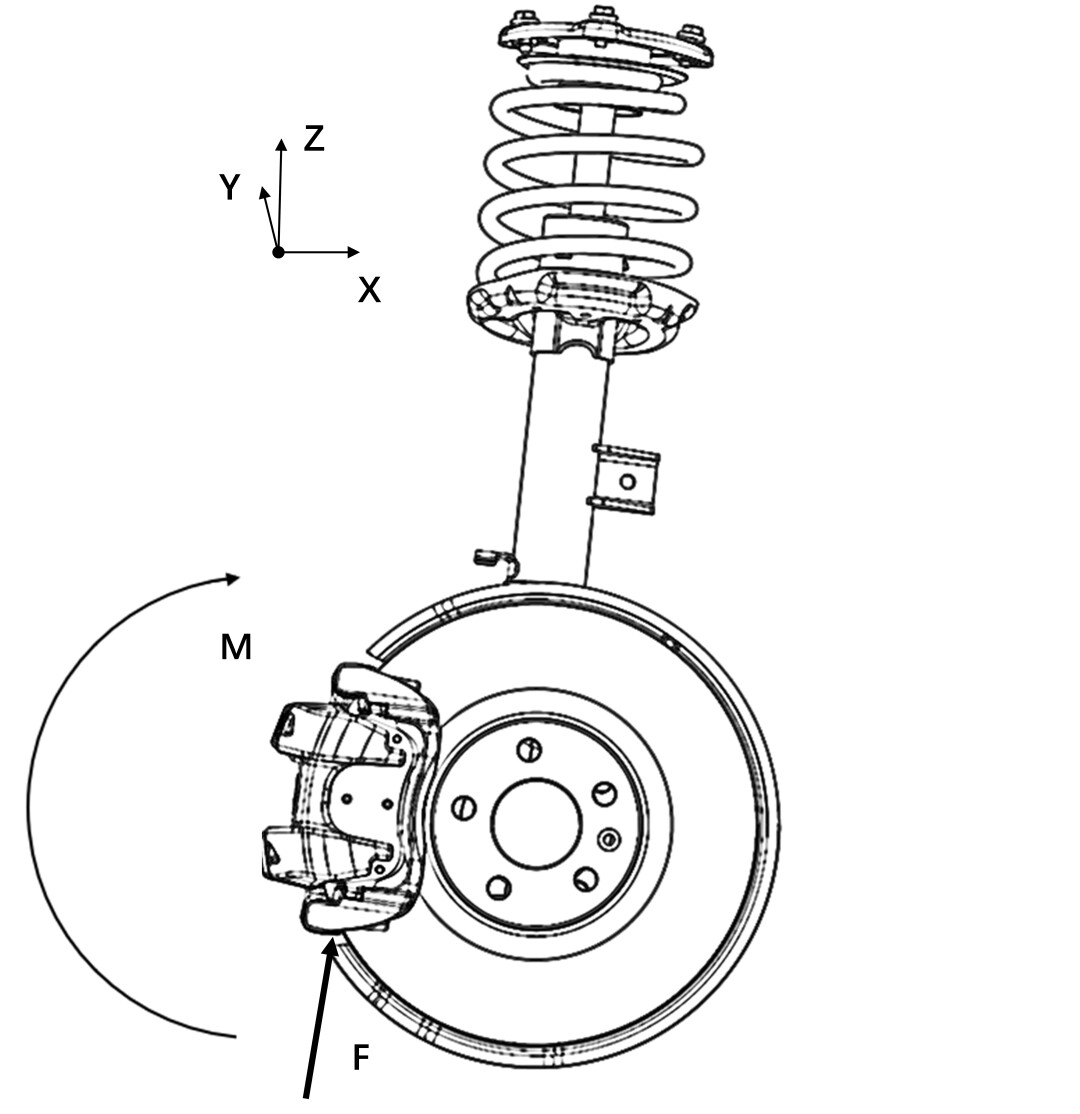
图6 制动时悬架的激励力分析
制动时,摩擦片给制动盘一个顺时针摩擦力矩M,ABS触发时该力矩以3.3-5Hz频次进行建立与释放,将其简化为沿摩擦片切线方向的激励力F,这与弹簧颤振产生原理相符合。但是根据前文测试结果,颤鸣声产生过程存在复杂耦合情况,为了静置试验的准确性,在静置试验时同时对X、Y、Z向和切向方向进行激励以便确认最高信噪比的激励方式。在平板举升机上使用制动踏板执行器将制动踏板踩下以模拟颤鸣声过程的整车状态,用力锤分别激励制动盘与摩擦片接触切线方向和制动盘X、Y、Z方向,同步测试弹簧近场和车内前排噪声,前悬架各部件、Top Mount车身侧振动。
3.2►静置试验问题复现及传递路径分析
按照设计静置试验进行问题复现,分别于摩擦片与制动盘接触的X、Y、Z三向及切向方向使用力锤进行激励,同步进行振动和噪声的数据采集,测试噪声、振动结果如图7和图8所示,弹簧颤鸣声问题复现,且切线方向是最容易激励复原问题的激励方向,后续以该方向为激励方向。
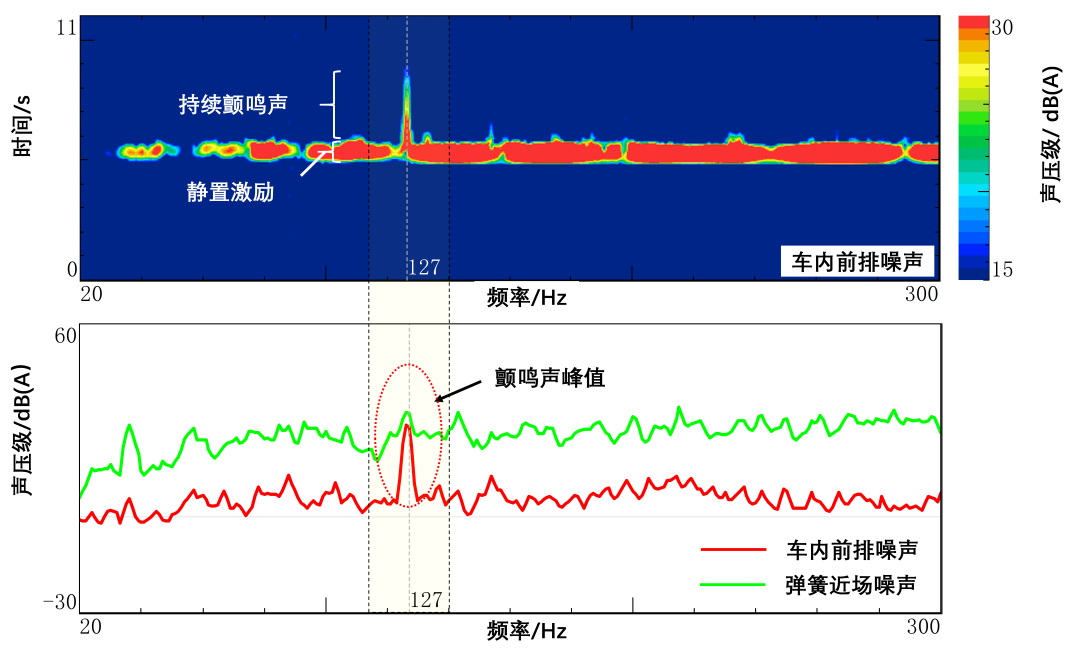
图7 静置试验颤鸣声频谱对比分析
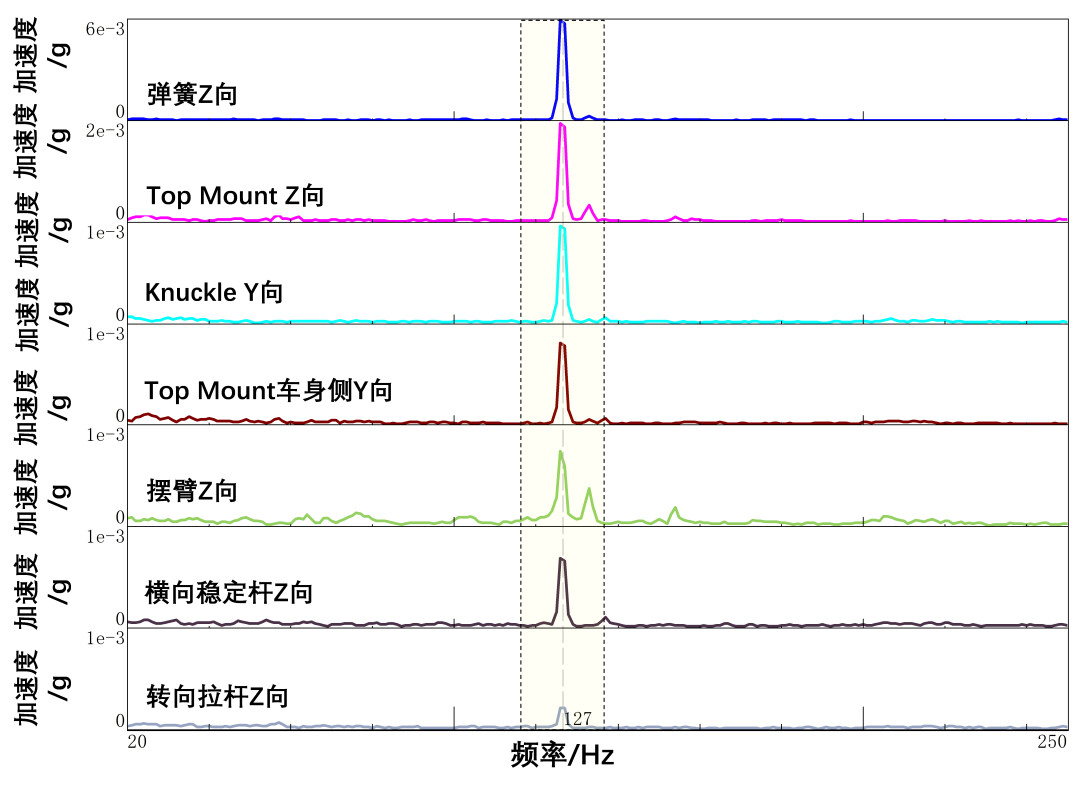
图8 静置试验振动频谱对比分析
通过静置试验复原问题并测试振动噪声可知:(1)设计静置试验可以以静态方式复现整车动态悬架弹簧颤鸣声问题,颤鸣声频率为127Hz与实车相差2Hz,考虑为制动激励与静置激励差异和实车制动时车辆姿态发生偏移等差异导致,但问题频率差异较小,可以进行后续验证工作;(2)车内前排噪声问题频率凸出声压级曲线包络线20dB(A),远大于弹簧近场噪声问题频率凸出声压级曲线包络线值,基本排除该噪声通过空气传播。127Hz振动以弹簧为最大,其次是Top mount和Top mount车身侧。悬架其他零件到车身传动链长,问题频率振动量级偏小不是主要传递路径;(3)颤鸣声以弹簧127Hz颤振为激励源,通过Top mount传递至车身并在车内形成噪声的结构声问题。
3.3►基于静置试验的问题改进验证
综上所述,此车型制动后弹簧颤鸣声问题主要是由ABS触发后,摩擦片对制动盘的制动力矩激励悬架弹簧产生颤振,并通过Top mount传递至车身并在车内形成噪声的结构声问题。因此,降低悬架弹簧激励和改进悬架弹簧响应传递是控制该车型问题的解决思路,考虑可实施性,从以下几个方面进行改进验证。
(1)改善主要传递路径在问题频率的隔振性能,降低弹簧颤振激励向车身的传递。可以增加上弹簧座橡胶厚度或使用阻尼特性更好的硅胶材料等方案进行改进。还可以通过降低Top Mount刚度来提升隔振性能,但该措施可能会对车辆动力学性能发生冲突。
(2)颤鸣声源头额外附加减振或者降噪措施。在弹簧上添加附加质量、动态吸振器或者使用弹簧表面阻尼材料,使弹簧颤振能量快速衰减。
(3)增大弹簧线径,提升弹簧颤振所需要的激励力,使得在现有ABS触发激励力下弹簧不发生颤振现象。但该措施会对车辆动力学性能发生冲突,在项目进行到中后期不建议采取该项措施。
通过前文设计静置试验,快速将以上分析方案进行静置验证,结果如图9所示,以上分析方案均可改进弹簧颤鸣声。

图9 颤鸣声方案静置验证结果
4 工程化改进措施及验证
添加吸振器和阻尼结构可以解决弹簧颤鸣声问题,但会带来成本增加和可靠性验证时间增加。此车型如图10所示方案,将上弹簧座橡胶厚度提升3.25mm,并增加特殊孔洞结构利于隔振;骨架从L形改进成环形,减小弹簧与骨架的接触传递并防止弹簧脱圈,以提升弹簧颤鸣声传递路径上的隔振能力。

图10 弹簧座改进方案示意图
该方案静置试验验证了有效性,但静置试验与整车的还原度还要通过实车验证。更换改进后的上弹簧座方案样件,采用相同试验方法进行主观评价与客观测试。如图11所示,整车试验结果与静态试验结果吻合,改进方案解决了制动后弹簧颤鸣声的问题。此将动态复杂整车问题转换为静置可快速多方案验证的试验思路,为后续项目弹簧开发设计在前期进行验证提供了条件,降低后续项目弹簧颤鸣声发生的机率。

图11 工程化方案路试效果
结 语
本文以某纯电动汽车强度制动触发ABS后,前悬架弹簧颤鸣声问题为研究对象,系统阐述了前悬架弹簧颤鸣声的识别与排查分析过程,结合弹簧颤振机理和制动时悬架受力分析,设计能够高度还原问题现象的静置试验,将动态复杂的问题验证等效成简单静置的试验,并通过静置试验进行了弹簧颤鸣声的传递路径分析与多方案验证,并实车验证了方案的有效性。由于弹簧颤鸣声机理复杂,与悬架各部件多有耦合,需要继续深入弹簧颤振与悬架结构的动态耦合非线性理论的研究,亟需建立高置信度的全面的制动性能仿真分析方法,充分考虑纯电动车与燃油车的差异,建立完善的更宽频域范围考虑的悬架弹簧设计与验证流程。
参考文献
[1] 张立军,余卓平.螺旋弹簧的驻波效应对悬架隔振特性的影响[J].振动与冲击,2002(02):45-47.
[2] Sun W. Analysis of Dynamic Stiffness Effect of Primary Suspension Helical Springs on Railway Vehicle Vibration[J]. Journal of Physics: Conference Series, 2016, 744(012149).
[3] Nishizawa, S. The Effect of Rubber Seats on Coil Spring Force Line[C]. SAE Technical Paper 2002-01-0317, 2002.
[4] 刘瑶瑶. 麦弗逊悬架侧载螺旋弹簧的设计与研究[D].燕山大学,2017.
[5] Simmons, R. A. Surging in Coil Springs[C]. International Compressor Engineering Conference. 1996,Paper 1190.
[6] Liu H. Estimation of valve spring surge amplitude using the variable natural frequency and the damping ratio[J]. International Journal of Automotive Technology,2011,12(5):631-638.
[7] Nam Chanhyuk. Riding Comfort Enhancement Using C-Shaped Spring Suspension[J]. International Journal of Automotive Technology,2021,22(5).
[8]Sahu. Design and Characterization of Progressive Coil Spring for Suspension Systems[J]. Journal of The Institution of Engineers (India): Series C,2022.
[9] Peter R.N. Childs,Mechanical Design Engineering Handbook (Second Edition)[M]. Butterworth-Heinemann, 2019, Pages 719-771.
[10]陈家瑞.汽车构造.第三版[M].北京:人民交通出版社,1997:35-37.
作者简介
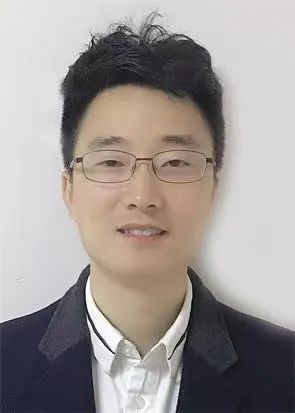
沈龙
主任工程师
浙江智马达智能科技有限公司
浙江智马达智能科技有限公司,负责smart国内外车型NVH开发。
E-mail:sl_wjstx@126.com
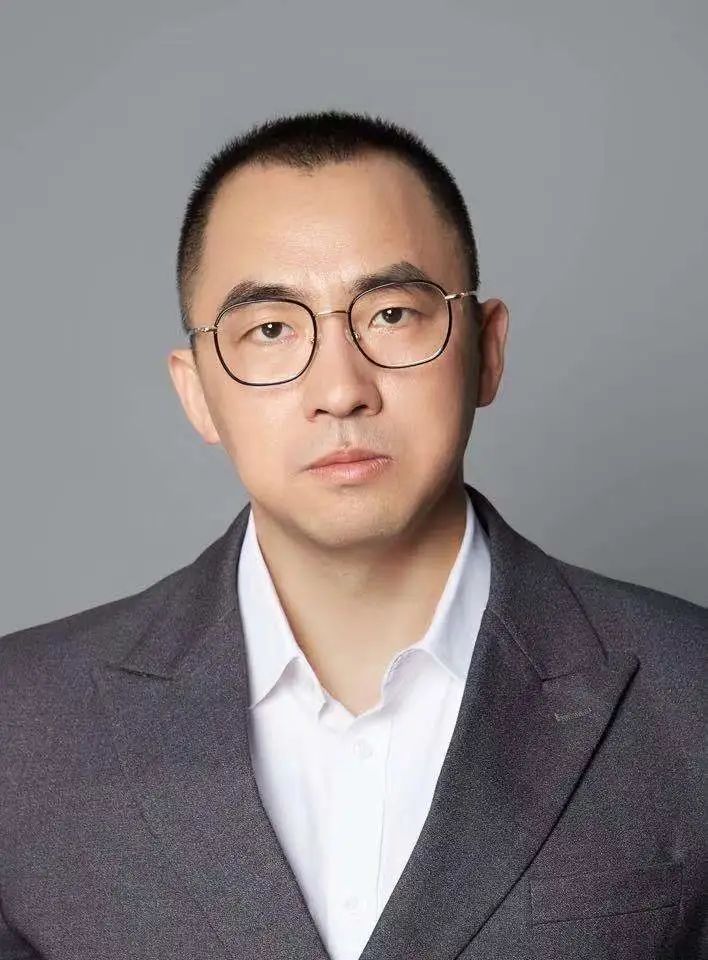
张军
博士,正高级工程师
吉利汽车研究院
上海交通大学博士,正高级工程师,现任吉利汽车研究院NVH技术专家,专注于振动噪声领域研究与工程实践20多年。
E-mail:zj_zmkm@126.com
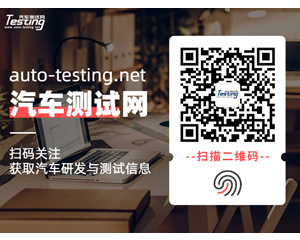
最新资讯
-
商用车及工程机械行业专场:NVH 及语音音频
2025-08-01 17:12
-
理想i8和重卡对撞测试引争议,东风柳汽发声
2025-08-01 15:52
-
艾德克斯IT-N2100 系列太阳能阵列模拟器
2025-08-01 15:43
-
ITECH重磅发布IT2705直流电源分析仪,重构
2025-08-01 15:34
-
现代汽车新一代混合动力系统:以技术革新引
2025-08-01 15:32