主机厂对动力电池性能有哪些要求?
今天给大家简单分享一下整车厂对动力电池的性能具体要求到底是什么样的,需要走什么样的开发测试流程。
一,车厂对电池性能的需求
其实对电芯的基本需求包括:能量密度(续航里程),安全,快充,成本,寿命,尺寸兼容。
比能量
比能量是保证混合动力汽车能够达到基本合理的行驶里程的重要性能,连续2h放电率的比能量至少不低于44W·h/kg。
充电时间短
蓄电池对充电技术没有特殊要求,能够实现感应充电。蓄电池的正常充电时间应小于6 h,蓄电池能够适应快速充电的要求,蓄电池快速充电达到额定容量的50%时的时间为20min左右。
连续放电率高,自放电率低
蓄电池能够适应快速放电的要求,连续1h放电率可以达到额定容量的70%左右。自放电率要低,蓄电池能够长期存放。
不需要复杂的运行环境
蓄电池能够在常温条件下正常稳定的工作,不受环境温度的影响,不需要特殊加热。保温热管理系统,能够适应混合动力汽车行驶时振动的要求。
安全可靠
蓄电池应干燥、洁净,电解质不会渗漏腐蚀接线柱和外壳。不会引起自燃或燃烧,在发生碰撞等事故时,不会对乘员造成伤害。废蓄电池能够进行回收处理和再生处理,蓄电池中有害重金属能够进行集中回收处理。电池组可以采用机械装置进行整体快速更换,线路连接方便。
寿命长、免维修、制造成本低
蓄电池的循环寿命不低于1000次,在使用寿命限定期间内,不需要进行维护和修理。
根据中国汽车动力电池技术路线图计划,到2020年系统级能量密度要达到250Wh/kg,成本要降到1块钱以下,续航里程达到400km以上,可选择的成熟材料体系着实不多,目前基本上确认使用高Ni三元材料和硅基负极材料或者相应的高电压材料。
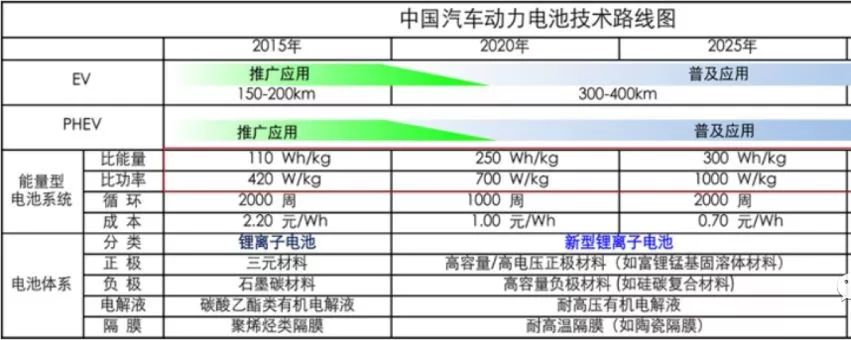
国内外的主流电池企业实际的目标如下:
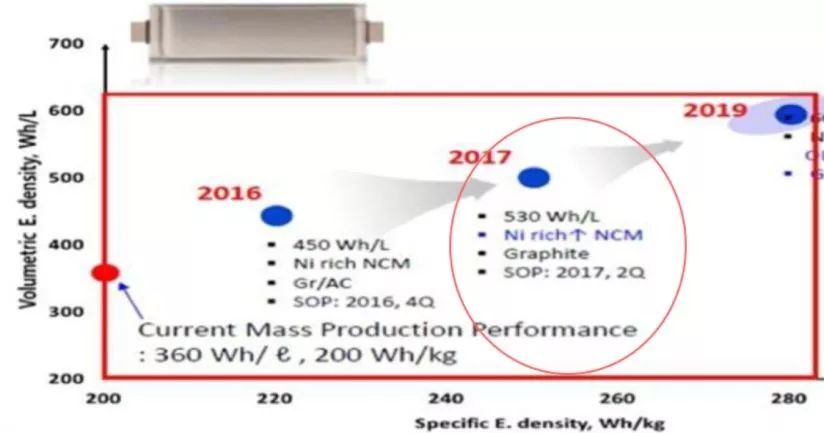
电芯能量密度提升、Pack轻量化与紧凑化设计、系统能量利用效率提升对提升续航里程及降低成本贡献巨大。
电芯安全性能
电芯能量密度快速提升对应电芯安全挑战增加,市场急迫需要产品规模化投放。此外还应加强系统安全设计投入,从系统角度通过多层级、多维度设计实现产品集成应用安全。
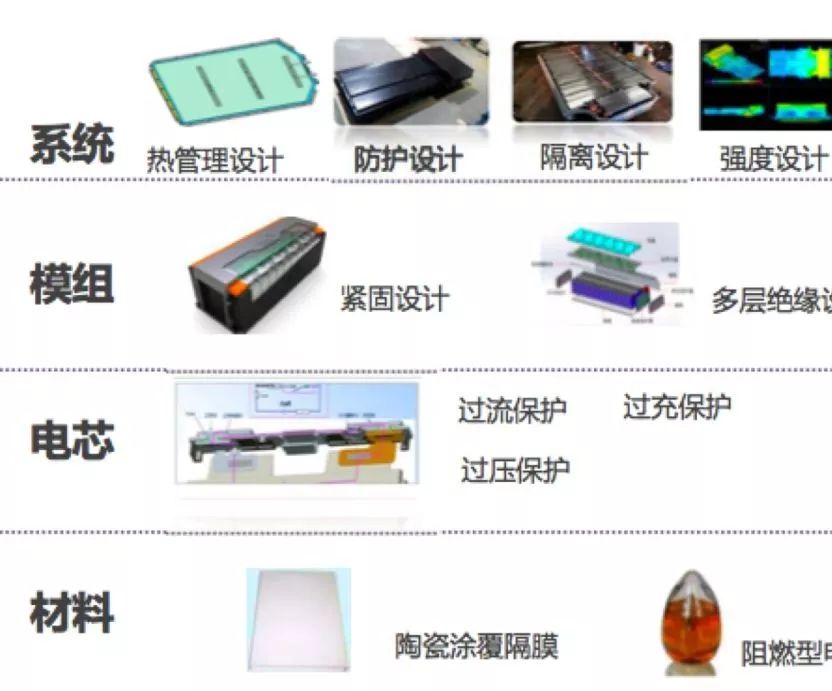
快充特性
综合充电设施及电池技术进步认为:30~45min快充会作为主流技术需求,10-15min快充会局部研究并应用。换电模式主要出现在出租车的运营上,目前水平为3-5min快换。
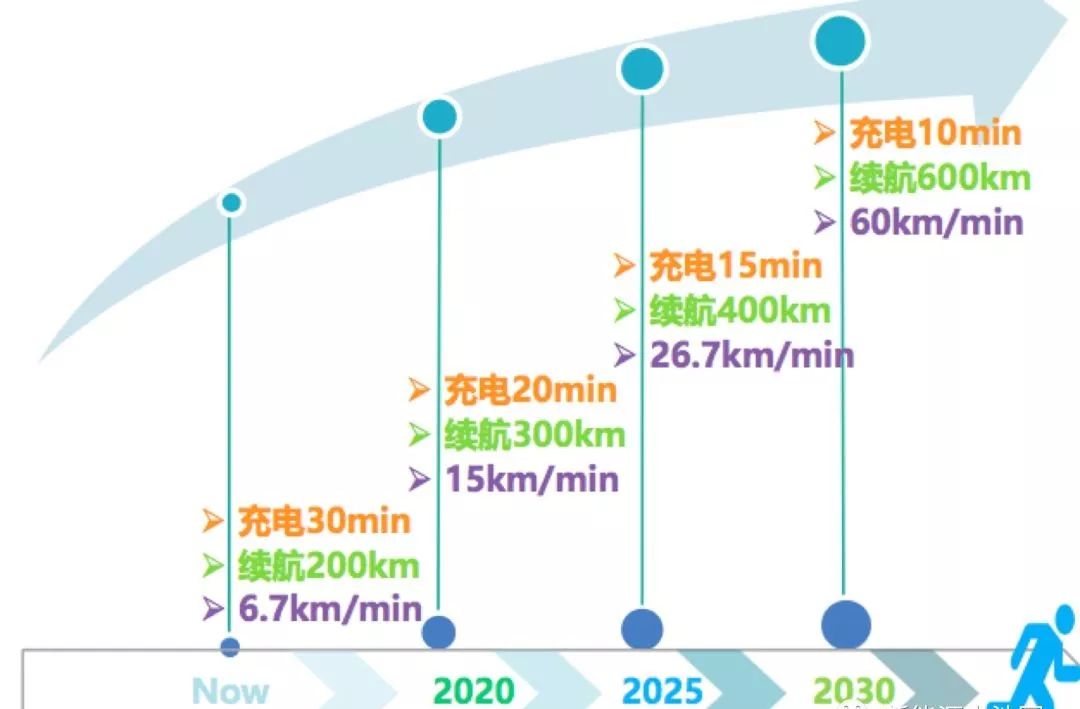
电池成本和尺寸兼容
材料技术进步及规模化、标准化、整车能耗降低、梯次利用促进电池降本。标准化最大限度减少开发成本,同时对梯次利用也是一个很重要的基础。整车企业未来将会定义模组规格(比如VDA或新国标电动汽车用动力蓄电池产品尺寸规格),在模组规格范围内进行布置,有利于跨平台应用,同时便于回收梯次利用。随着整车布置的优化需求,滑板式电池包布置在电池底盘,对于Z向要求越来越高,高度在120mm进一步压缩到100mm,对于电芯的高度91mm优化到80mm。
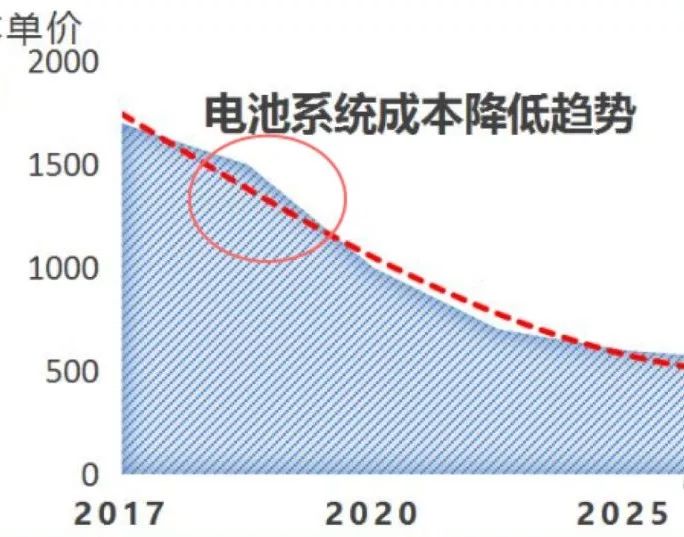
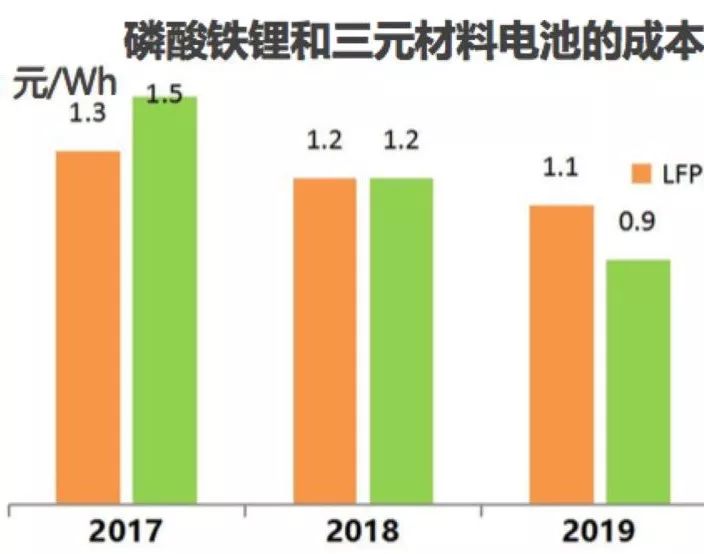
寿命
电池寿命需要做到质保承诺: 10年或16万km,寿命目标:10 年,240,000 km,随着车辆续航里程增加,对电池的循环寿命相应放宽。
车厂对动力电池的开发流程
以北汽为例,基于整车的开发总体流程如下:
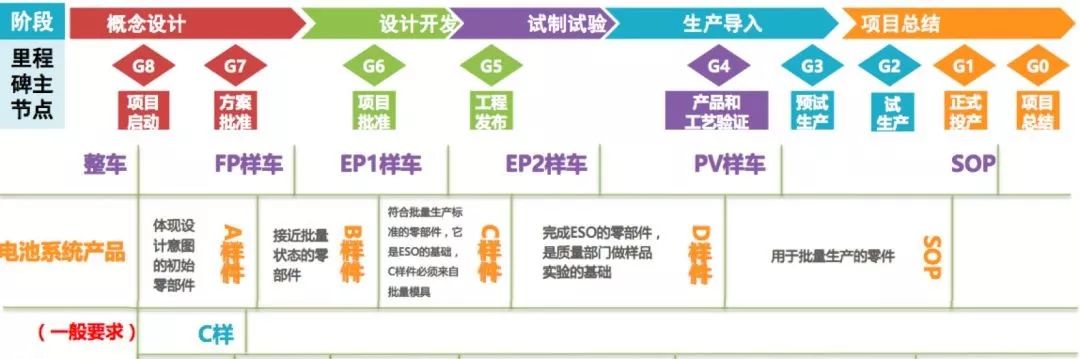
北汽的整车EVDP流程,每级子系统的开发验证流程要先于母系统,保证产品开发过程的可靠性。以上是基于电池系统与电芯同步开发情况下定义的开发流程。根据实际开发情况,会优先选择成熟度高的电芯产品。
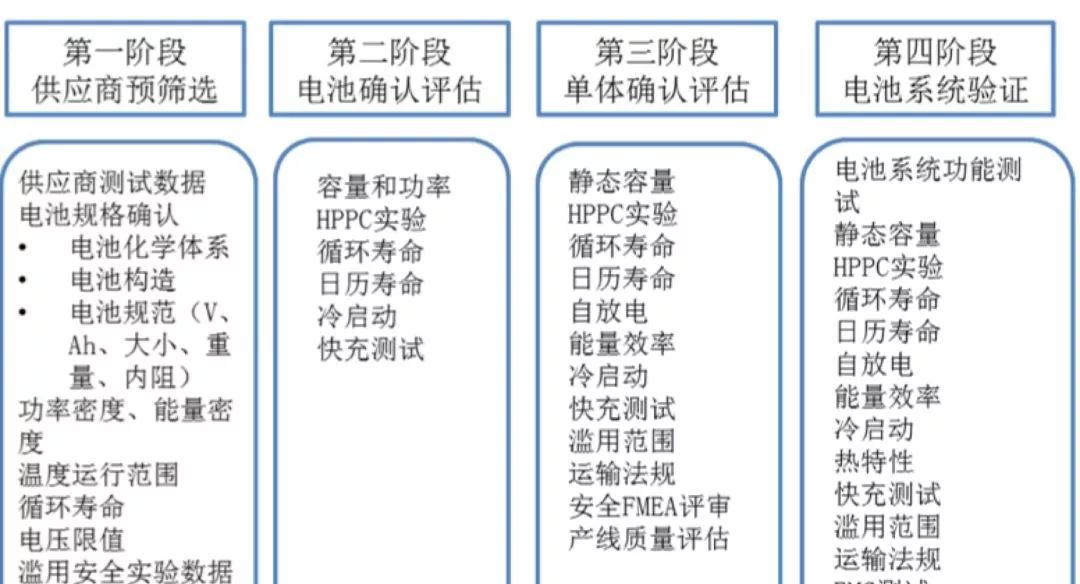
上汽集团共把它分为四个阶段:预筛选-电池确认和评估-单体确认和评估-系统验证。各个阶段都有严格的测试流程和控制。
电芯类型的选择
电芯从正负极材料的角度来看目前有NCM(111,523,622,811),LCO,LFP,LMO,LTO等。车企要从能量密度,功率特性,循环寿命和安全性的维度进行筛选。另外从电池封装形状上又可分为圆柱,软包(叠片和卷绕),方形(叠片,卷绕,并联卷绕)。各个类型的电芯主要特点总结如下:
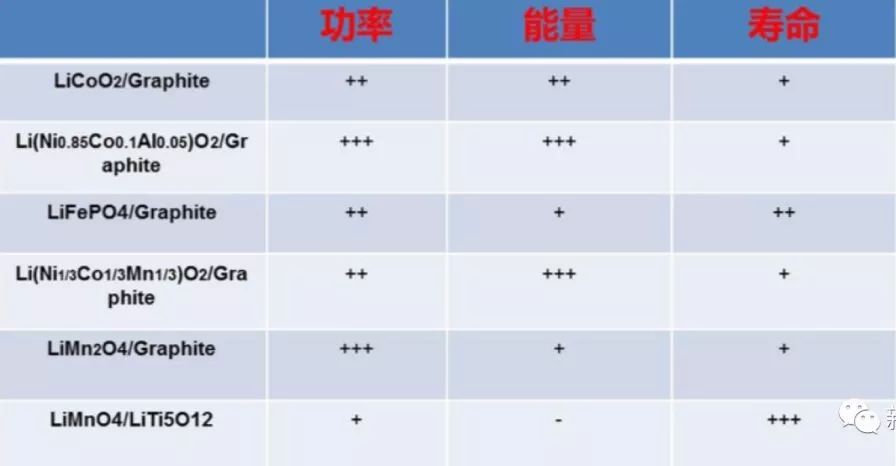
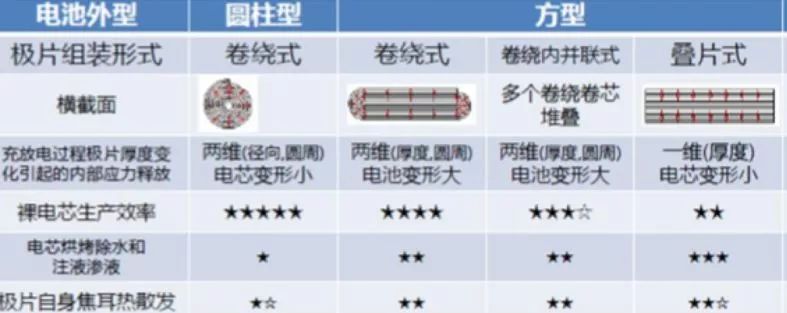
电池测试评价体系
三横四纵评价体系。三横:以电芯为核心的关键零部件、电池模组、电池系统三大产品维度,根据不同开发阶段开展不同的测试评价; 四纵:认可试验、标定试验、拓研试验、虚拟验证四大试验类型,验证项目近158项,其中系统热安全、电安全及机械安全33项。其中热安全又包括11子项,29分项; 电气安全包括15子项,33分项; 机械安全包括17子项,35分项;
认可实验
五步四级电芯管理办法,包括技术状态管理、工艺、材料信息建档管理。
对电芯从外特性到内部材料、工艺进行分级开发管理,实现从应用的技术可行性向产品的批量可行性进行评估管理。
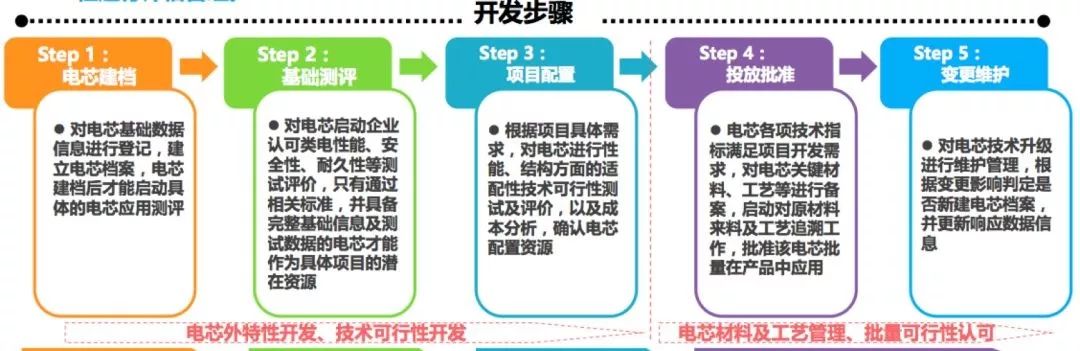
标定实验
这是对整车动力性,经济性,环境适应性,耐久性,热平衡,SOC算法验证的过程。
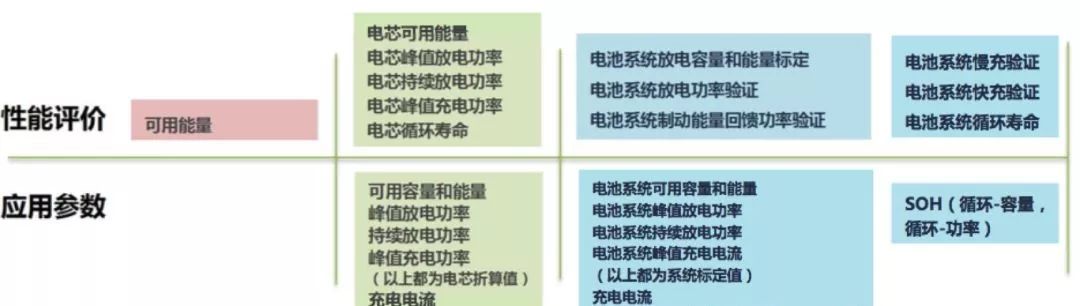
拓研实验验证
电池全生命周期性能评价
整车高水位涉水
高湿环境下的电气安全距离研究
高空跌落试验
持续火烧试验
动力电池系统剖切试验
虚拟仿真验证
在产品开发阶段虚拟验证共计进行两类(结构、热)两级(模组级、系统级)40项仿真分析。
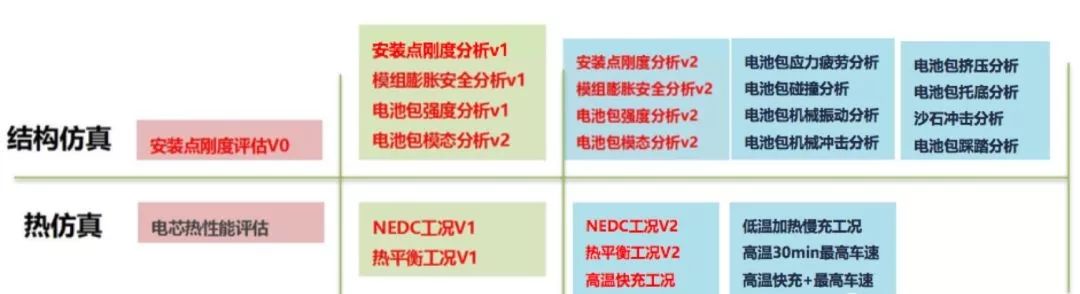
平衡设计动力电池
在电动汽车的设计中,要有平衡的概念。要充分了解用户需求,设计出来的产品不是为了通过标准测试,而是迎合消费者。以安全为中心,寿命、能量密度、功率密度、可靠性之间需要权衡。权衡以后,比如说能量密度和功率密度,在设计上有矛盾,而且能量密度大到一定程度,也会影响安全性的。能量密度高到一定程度也不好控制,所以追求能量密度的时候,安全性问题就会变得越来越突出。
电池设计要平衡,指标不能光看电芯,还要看系统。举个能量和功率的平衡的例子:电池的空间有限、重量有限,都知道电容量越大,要追求卷绕的面积越大越好,而且多绕两圈最好,这是追求能量密度。所以在做的时候,能量型电池不要求过很大电流,电子导电的极片做薄一点,让电极材料涂得厚一点,但是功率型电池要求把极片做厚,但是涂层要薄,离子通道要短,经过隔离膜、电解液到对面去比较快。高能量要求可用的锂电池数量多,高功率要求锂离子跑得快。功率和能量密度同时做到世界第一,是做不到的。
目前,电动客车坚持用磷酸铁锂,因为三元电池没解决热失控这个问题。而乘用车都在用三元,为了优先保证能量密度(但系统热失控也需要满足逃生时间)。所以,不同的应用需求,可以做不同要素优先级的选择。关于共性需求,目前的用户调研,基本上,成本和能量密度在纯电动里面还是放在最先的位置。
动力电池未来变化和发展趋势
1.价格降低。在看后面几年需求的变化和电池发展技术趋势,比较通俗讲,价格至少降一半,我们的目标是2020年完成。其实我们老板要求我们把2020至少降一半的情况要往前提,我们用户觉得这是一个好的事。
2.能量密度提升。能量密度将提升到现在的1.3倍到2倍,磷酸铁锂现在的行业平均水平130Wh/kg上下,但是有可能纯磷酸铁锂有机会做到150~170Wh/kg。纯的磷酸铁锂硅极材料用上去以后,有机会达到180 Wh/kg。现在国家提出更高指标是350 Wh/kg,系统能量要到260 Wh/kg,国家提的要求更高一些。
3.循环寿命提高。现在乘用车和物流车使用的三元电池大多数是1000-2000次的循环寿命,但是现在也有些做2500次的,做混合动力的也有6000、7000次的也有。同样的技术水平,功率型电芯设计到位的话,它的循环寿命会比能量型的长一些,基本上循环寿命提升到现在的2倍。磷酸铁锂可以从2000-4000次提升到10000次以上。
4.电芯、模组、电池包行业标准化。电芯、模组、电池包行业标准化是第四个趋势。
电池开发设计的流程及技术
电池系统不好做的地方,在于它的化学系统受环境影响很大。不管是电池还是电控,只要用到车上就要按照汽车核心零部件的要求来做。V模型开发非常重要的一点就是分层设计、分层验证,比如管理系统是一个小部件,把管理系统的需求加进去,设计开发出来,等到管理系统测试验证好以后,做PACK的集成设计,然后再做到整车的集成设计,是一层一层非常严谨的开发设计流程。
1.机械设计。PACK GBT31467.3的16项安全测试都要做,还有火烧跟挤压测试。对PACK来讲,降成本、减重量,保证安全性和可靠性还存在矛盾,在进行安全设计时,既要考虑成本,又要考虑安全性、能量密度。PACK减重时,要考虑机械强度、机械寿命、防腐蚀性,确保可靠性。
2.IP67的重要性。IP67是牵扯安全的,不仅是能不能用,还有安全性。分几个方面分析IP67的控制,先看箱体加工,要保证箱体不会被破坏;二是看压力平衡阀,能保证不同的纬度、不同的温度下,里外的气压保持平衡;三是上下盖的密封面,需要考虑是否阻燃的,密封好不好,除了材料选择、形状选择,还有固定的压缩比;第四,连接器容易漏水,主要是线束、导线跟插头的关系、插头跟插座的关系、插座跟箱体的关系。要特别注意设计的时候,连接器底座的固定方式是否需要使用盲孔,如果需要盲孔,而箱体里面设计的不是盲孔,再补加胶水也没有用,长期来看是不行的。此外,安装连接器的时候,对箱体的平面性是有要求的,当结构设计不合理,连接器底座和电箱密封也是会漏水的。
3.电池热管理设计。电池热管理设计分三大步骤。第一步是建立热模型。有模型后,单个电池专门测试发热点,建立功率和发热模型的关系;第二步是系统热设计。从机械结构的布局,热传导路径,算它的热阻回路;第三步是热管理和策略,一个目的是防止热失控,保证安全,另一个目的是为了电池的长寿命,控制一些应用功率,防止电池处于较高温度。
4.水冷+热冷热管理系统。高温区的应用有制冷系统,供冷水;高寒区的应用有加热系统,供热水。这两个之间有一个切换功能。但是,目前即便是做出这个产品,也只能说能用,仍不完善。解决方法有两个方向:低温电池和速热技术。
5.电池管理系统。BMS要具备保护和自我诊断功能。特别强调的是,管理系统能够对电池做到自动维护、延长电池寿命。电池长期维护的关键是均衡,而在整车的电池包里,电池结构分布不同,温度、并联回路过电流存在差异,会让电池功率的输出不同。所处的温度环境不一样,性能也会慢慢离散,所以均衡是需要的。
我反对均衡的时候要用多大电流来标榜,那会带来另外的安全和可靠性的问题。在均衡当中,要能够时刻检测出电池状态、单体状态,判断均衡条件比执行均衡更重要,最好能够提前判断,防微杜渐。
主动均衡和被动均衡的区别是什么?主动均衡是“劫富济贫”,电池状态好的可以去救状态差的。被动均衡是“劫富不济贫”,就是把SOC高的容量放掉,达到一致的SOC,再在外面给电池组充电补上去。这里两种方式的成本差异比较大,基本上是两倍以上的关系。
BMS软件分应用层和底层,APP跟BSW。应用层除了系统本身外,其实就是五个模块:前处理、后处理、状态估计、输入、输出。关于管理策略,电池的安全性和可用性是要兼顾的。设计的时候,其实在提高管理系统安全性的同时,也要提高用户的体验。
关于电池保护安全策略这一块,其实电池最怕的是过充、过温,也怕过放后再充电。安全保护要分级、分策略。充电安全方面,充电机的安全是很重要的问题,但目前充电机的质量、技术水平差别很大。
关于SOC算法。既要保证司机能够安全地用SOC,不能虚高虚低,又要保证用户不会觉得SOC乱变化,要有显示策略。高压保护也不说了,非常重要的是高压保护的熔断器和接触器。特别重要的一点,直流耐压不够的话,在短路的时候不能有效分断,所以耐压一定要足够。接触器在高压的时候要断开它,选择时也要考虑耐压和过电流能力,还要注意跟结构设计相关的,我在这两个电极上不要施加不当应力,破坏它的结构。
6.电池系统安全。关于电池系统安全,要从电芯材料和电芯设计的机理开始,就做到防热失控。而在系统级做到防止热扩散,这是全过程的控制。全方位安全(化学、机械、电气和功能安全)中,化学安全要求不起火、不爆炸和阻燃性能,还包括不排放有毒气体,也包括不发生热失控,这些都是在化学安全里面。机械安全包括振动和IP等级,防爆、防撞、防挤压都要考虑。第三是电气安全,就是放触电、防漏电、防绝缘失效和高压防触摸,这些都是属于电气安全的东西。还有功能安全,功能安全在这里是一个概念扩展,通俗地讲,就是当功能失效的时候不能产生安全事故。
电池安全是底层的,是车上的核心零部件,要服从于车安全,要服从于人安全。可靠性是设计制造出来的,主要讲系统设计分层分级去分析它的失效模式和影响,按照每一级去分解可靠性指标,这就是一个FMEA的概念,做DFMEA、PFMEA就是为了在设计开发阶段就识别风险,会不会带来可靠性问题,甚至带来安全问题,把影响分析导出来,从严重度、发生频率、可检测度各个方面考虑,FMEA分析是必须要做的,这也是汽车产品开发的一环。
7.电池系统寿命。电芯寿命的评估,会把它放到电池包乃至整车系统的大环境下来评估。电芯评估有一个模型,用存储寿命和循环寿命来评估用户的使用寿命,存储寿命和循环寿命的影响机理和因素是不一样的。存储寿命主要是化学因子影响,循环寿命是化学和机械的影响。在微观来看,充放电循环中,电极片会膨胀收缩,SEI界面会出现微裂纹,修复裂纹会消耗锂离子,影响寿命。
为什么功率型电池循环会相对好一些?因为功率性电芯的极片涂布压实密度比较低,膨胀量相对小,机械应力小。反之,压实密度越高膨胀越大,膨胀量相对大,机械应力大,对循环寿命影响大。所以说功率型的循环寿命会好过高能量型电芯。模型评估电池寿命的意义:比如一年时间,就能评估电池是否能存储8年10年,500次以内的循环测试数据,就能预测全生命周期能不能达到5000次、3000次循环。
最后,说下目前市场很热的东西:快充。快充电池系统必须至少满足四个条件:电芯性能、过电流、热管理和高压连接安全防护等必须满足。
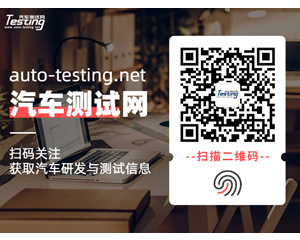
最新资讯
-
商用车及工程机械行业专场:NVH 及语音音频
2025-08-01 17:12
-
理想i8和重卡对撞测试引争议,东风柳汽发声
2025-08-01 15:52
-
艾德克斯IT-N2100 系列太阳能阵列模拟器
2025-08-01 15:43
-
ITECH重磅发布IT2705直流电源分析仪,重构
2025-08-01 15:34
-
现代汽车新一代混合动力系统:以技术革新引
2025-08-01 15:32