关注中国十佳车身评选,不妨先来了解车身安全百年史
1890~1920年,人类的交通工具逐渐从马车过渡到了汽车。1885年,德国工程师卡尔·本茨做出了世界上第一辆三轮汽车Motorwagen,金属车身出现,并于1886年1月29日申请并获得了发明专利,这一天被认为是汽车的诞生日。几乎就在同时,德国工程师戈特利布·戴姆勒也成功研制了一辆公认的、以内燃机为动力的四轮汽车。1894年,奔驰Velo成为最早的量产汽车。
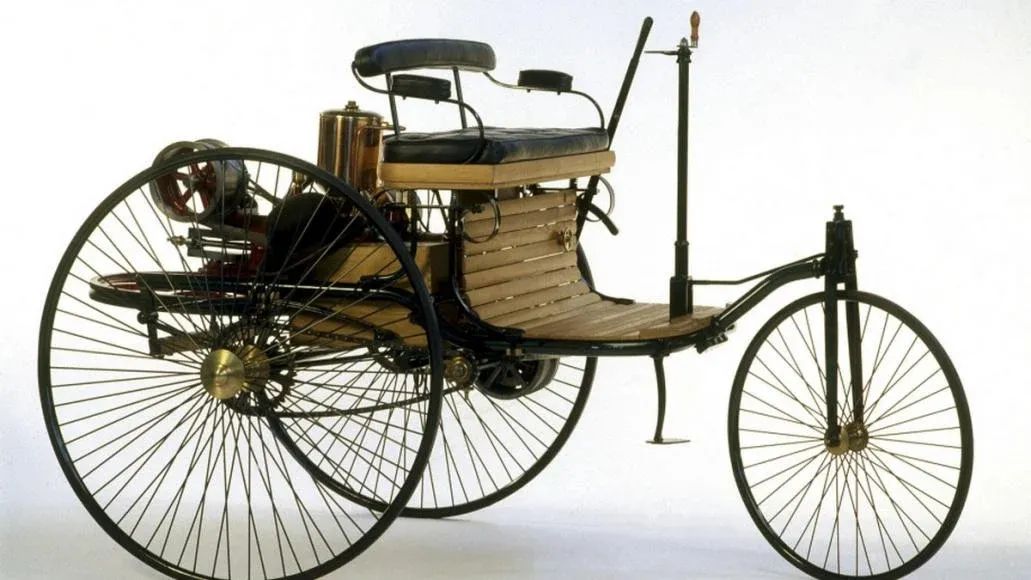
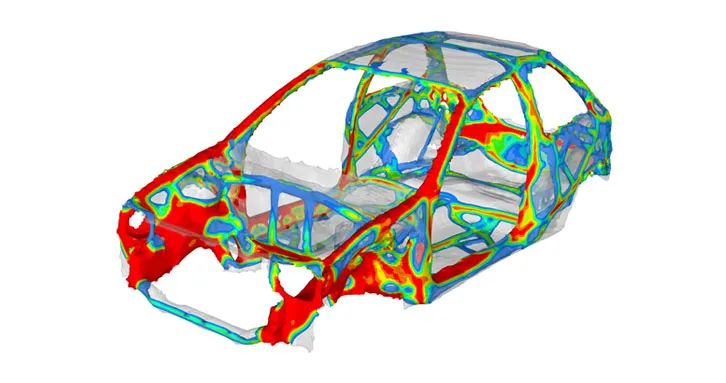
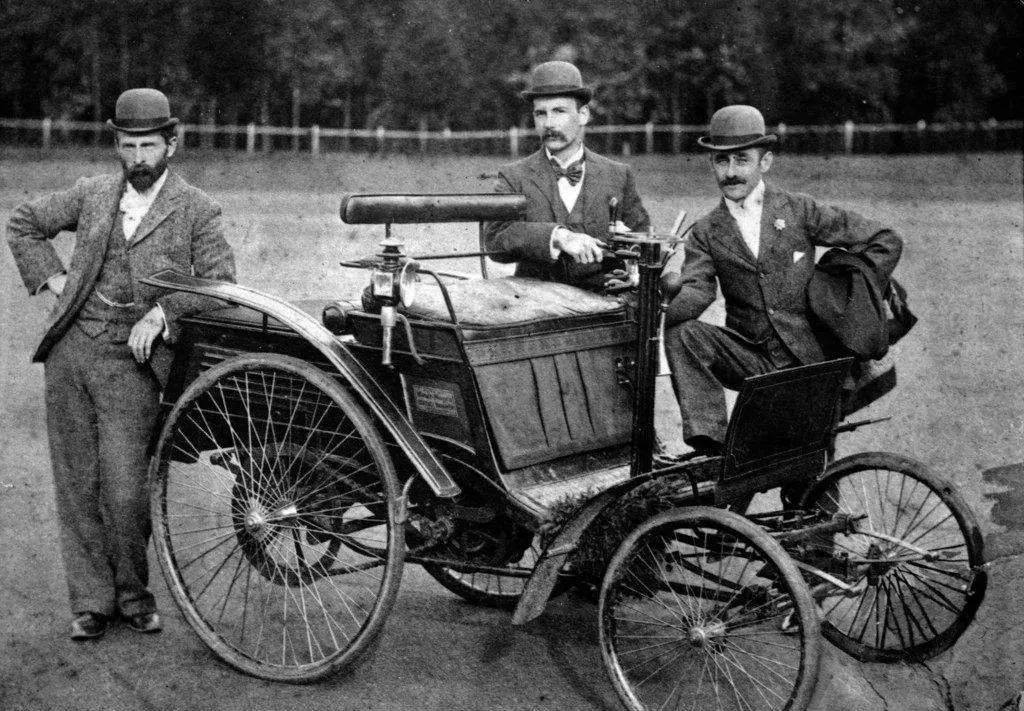
1900年,金属车身获得专利,但主体结构仍然是木材和连接用的钢材。20世纪初,随着John Pierpont Morgan创建的美国钢铁公司能够为迅速发展的汽车工业提供充足的原料,1914年Edward G budd发明了全金属车身。同年,道奇公司生产了第一辆全金属汽车,1918年意大利蓝旗亚公司也开始生产全金属汽车,汽车不再是底盘与车身的简单组合,而是成为了一体。
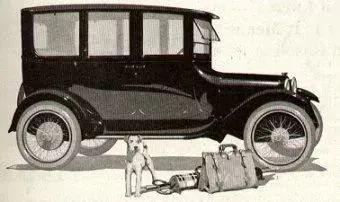
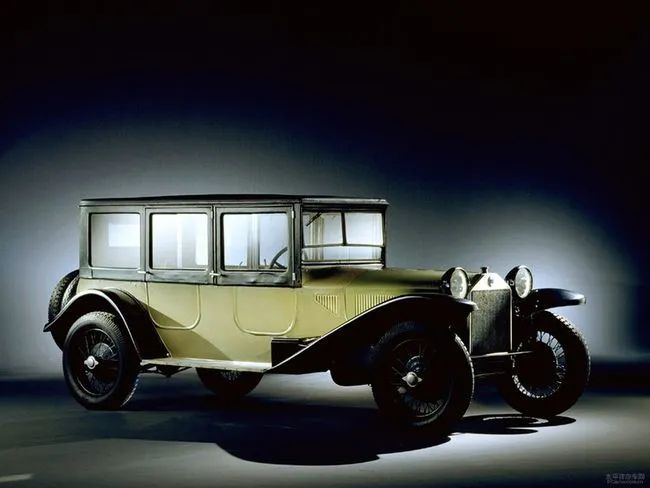
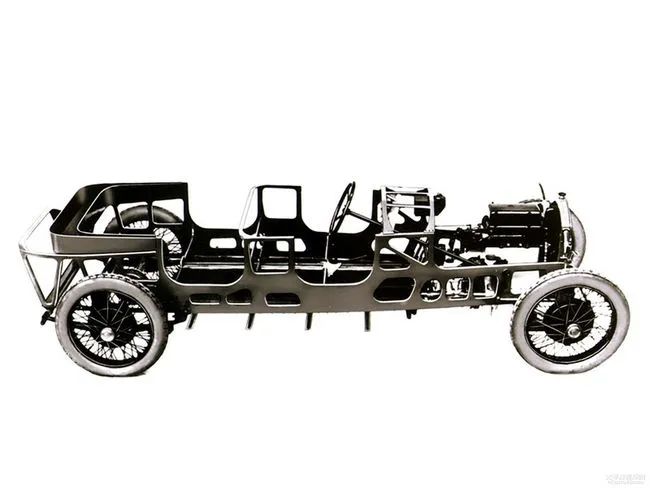
1912年,已经大规模量产的福特T型车车身采用了非承载式结构,其发动机、前后轴均与大梁相连,但是还没有汽车安全性的概念。因此,以现代的安全理念角度看当时的T型车,绝对是安全风险系数极高。20世纪20年代,劳斯莱斯采用了大梁式非承载车身设计,其驾驶室已经有了与今天汽车相似的A、B、C柱设计。但是,车身还是相当脆弱,如果发生碰撞事故,发动机会直接被撞进驾驶室,车身脆弱的结构无法保证驾乘人员的安全,汽车的安全性还是没有受到关注。
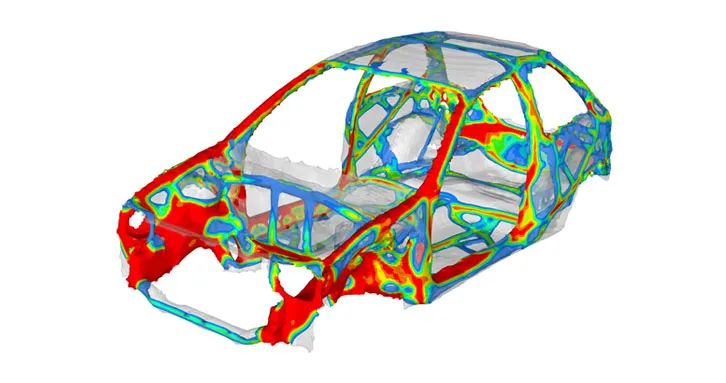
1944年,沃尔沃轿车发明了钢制一体式车厢和胶合夹层风挡玻璃。20世纪50年代以后,奔驰底盘号为W111的车系(包括220、220S和220SE车型)由工程师贝拉·巴恩伊设计车身结构,成为第一个拥有碰撞吸能区设计的车系,第一次将车身分为刚性区和吸能变形区。这种设计在发生碰撞事故时,刚性较弱的吸能区首先接受冲击变形,以达到吸收碰撞能量的目的,刚性较强的乘员区则不容易发生变形。这一设计在当时成为了划时代的技术,奠定了现代车身安全结构设计的基本理念。此外,该车系还配备了经过安全设计的转向柱和软性材质的中控台,从不同细节保证车内乘员在碰撞发生后的安全。该车系还首次应用了楔形销门锁,保证在碰撞发生时不会将车门撞开,也可以在碰撞发生后保证顺利打开车门营救乘员。1959年9月10日,奔驰W111车系进行了有史以来第一次碰撞试验。当时的碰撞试验是由喷气发动机驱动汽车正面碰撞硬质避障,具备了现代碰撞测试的雏形。此后,碰撞测试还促进了汽车在其他安全性能方面的研发,安全带、安全气囊和可溃缩的转向机构等相继诞生,发动机舱和尾箱均采用强度较低的吸能设计,座舱则经过强化,具备了现代轿车车身结构的雏形。1966年,沃尔沃144被评为“全球最安全车型”,其车身前后均设计了能量吸收区。
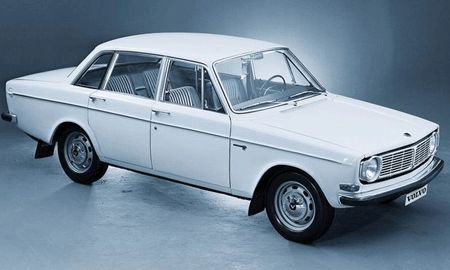
20世纪80年代,计算机技术发展迅速,逐渐被大量应用在汽车产业,模拟碰撞试验的产生推动了汽车安全性的发展,同时也降低了汽车的研发成本,使汽车设计更高效和更安全。在模拟碰撞试验中,在应用有限元分析软件后,能有效模拟车架在受冲击时的变化情况,为车架结构设计提供了很大便利和帮助,并极大缩短了研发周期。随着计算机、焊接和材料等领域技术的不断发展,现代汽车的车身设计更加科学,非承载式车身演变为更加合理的承载式车身,底盘与车身成为一个整体,一改过去底盘与车身各自为政的状态,使各部分在受到碰撞冲击时能有效分解能量。
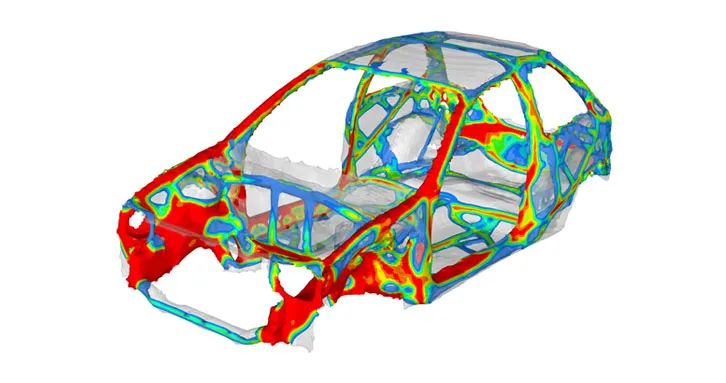
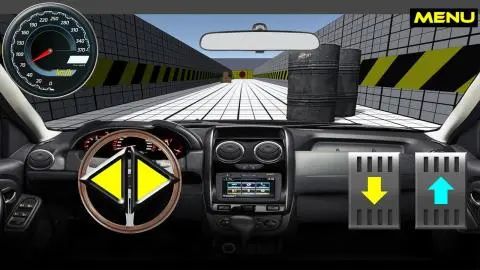
近年,汽车车身的安全性能得到明显提升,越来越多的车型开始应用更先进的三层笼式车身结构,车架的主要受力结构采用三层钢板冲压,并且三层钢板由外到内强度逐步增强,最里层钢板采用强度和厚度最高的硼钢板。同时,汽车安全性不仅在结构上发生变化,在材质方面也发生了变化。由于铝合金比同等强度的钢材质量更轻,在不减弱强度的前提下,应用铝合金材料能更有效减轻车身的质量,使车辆的动态表现更好、更节油,在发生碰撞事故时产生的冲击能量也更小。此外,复合材料的一体式设计已经在超级跑车上得到广泛应用,这种结构的强度远高于普通乘用车的车身结构,但高昂的造价限制了其应用范围,随着技术的发展,其应用范围会越来越广泛。
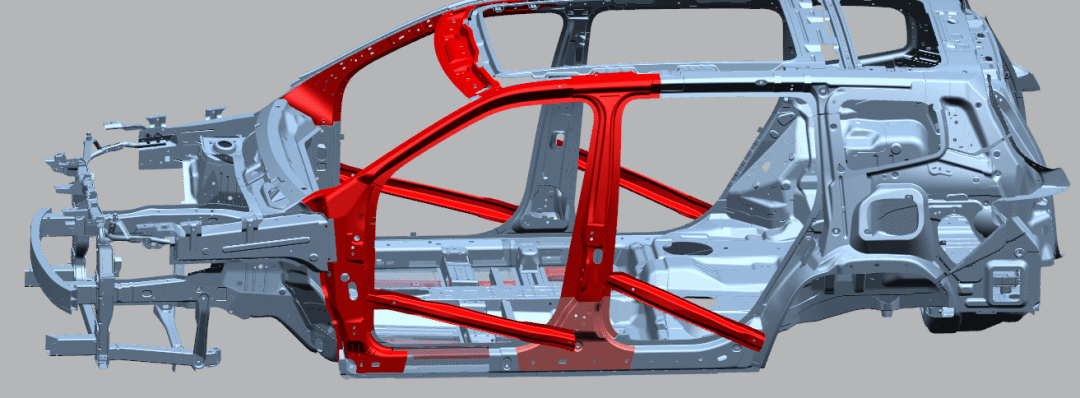
2000年3月29日,沃尔沃汽车的安全中心在瑞典哥德堡落成,其碰撞测试实验室配备了两条车道,一条是可调整的活动车道,能围绕中心旋转移动90°,另一条是永久性固定车道,长度能满足汽车0~120km/h加速全过程。沃尔沃汽车每年在这里进行约450次碰撞测试,比奔驰、宝马和奥迪等豪华品牌进行碰撞测试的总和还要多。该中心还保存有20世纪60年代至今的车辆碰撞数据,可以基于这些数据模拟仿真各种类型事故现场。该中心除了能进行单车和两车不同角度碰撞测试外,还能进行翻滚、侧撞、追尾载货车、撞击建筑物、撞山等各种实验。其中,固定车道和可移动车道均可以反向起跑,可移动车道的另一端是自然山体,可以模拟车辆冲出路面撞击山体的实验。2003年,沃尔沃汽车发明了防翻滚稳定系统。
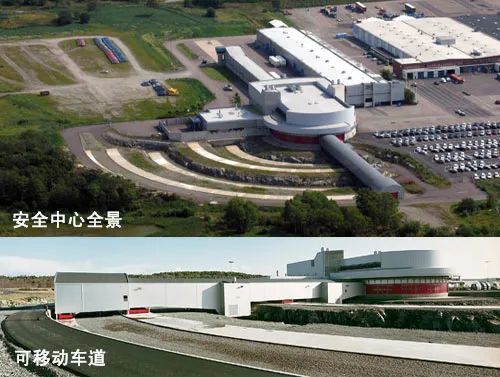
在汽车安全方面,不得不提美国法规起到的推动作用。20世纪60年代,很多美国车企为了节约成本纷纷采取减配手段,减配一些不常用的配置还能理解,但是部分车企居然减配了防倾杆,导致车辆在过弯道时极容易发生转向过度,引发了很多交通事故,美国民众发出了反对声音,而车企居然无动于衷。1965年,美国现代消费者运动之父拉尔夫·纳德出版了《Unsafe At Any Speed》一书,提到了很多车型因设计缺陷或过度降低成本影响了汽车的安全性,并抨击了某些减配防倾杆的车型,导致舆论哗然。1966年9月,美国国会立法通过了《国家交通及机动车安全法》,规定汽车企业必须严格遵循安全的原则设计和生产汽车,同时有义务公开发布汽车召回信息和免费修理。此后,很少有汽车企业在美国玩弄安全方面的把戏,美系车也从骨子里开始敬畏安全原则。
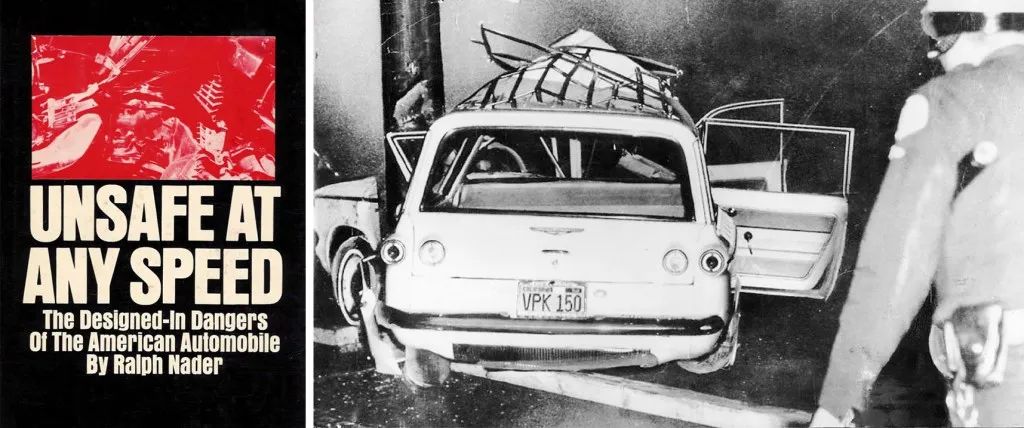
在车身安全方面,还有一家车企不能不提,其对车身安全技术的贡献也是有目共睹,这家车企就是日本的丰田汽车。丰田汽车在使其产品风靡全球的发展过程中,十分关注各国的法律法规、各企业的安全标准、最新技术成果、不同地域的典型事故形态以及不同市场中消费者的关注点,并根据这些经过反复试验,研发出了一项被动安全技术——Global Outstanding Assessment(GOA),还获得了设计专利。该项技术的主要目的在于当车辆发生不可避免的碰撞时,将撞击力分散,以保证乘员舱不变型,最大限度保证车内乘员的安全。
该技术的结构特点是:车身整体分为前后部碰撞变形区和高强度乘员室三部分。前后部碰撞变形区的基本要求是应拥有较软的变形吸能区,以便当发生碰撞时吸收较多的能量。在正面碰撞中,车身前后部碰撞变形吸能区的变形越大,吸收的碰撞能量越多,产生二次碰撞的能量就越小,使传递到乘员室的冲击力也越小。同时,乘员室采用高强度钢,可有效增强碰撞后乘员室的变形强度,减轻或避免乘员因乘员舱的空间变形受到挤压,以降低乘员受到伤害的几率。
1995年,该技术首次应用在Starlet和Corona Premio两款车型上,GOA成为丰田汽车在安全技术方面的总目标,也是丰田汽车内部的安全标准,满足这个标准的车身结构设计就被称为GOA车身。但这个标准不是一成不变,当某个国家或某个企业内部安全标准提高时,GOA标准也随之提高,从而保证丰田汽车的车型安全性在同级别车型中始终保持国际领先水平。
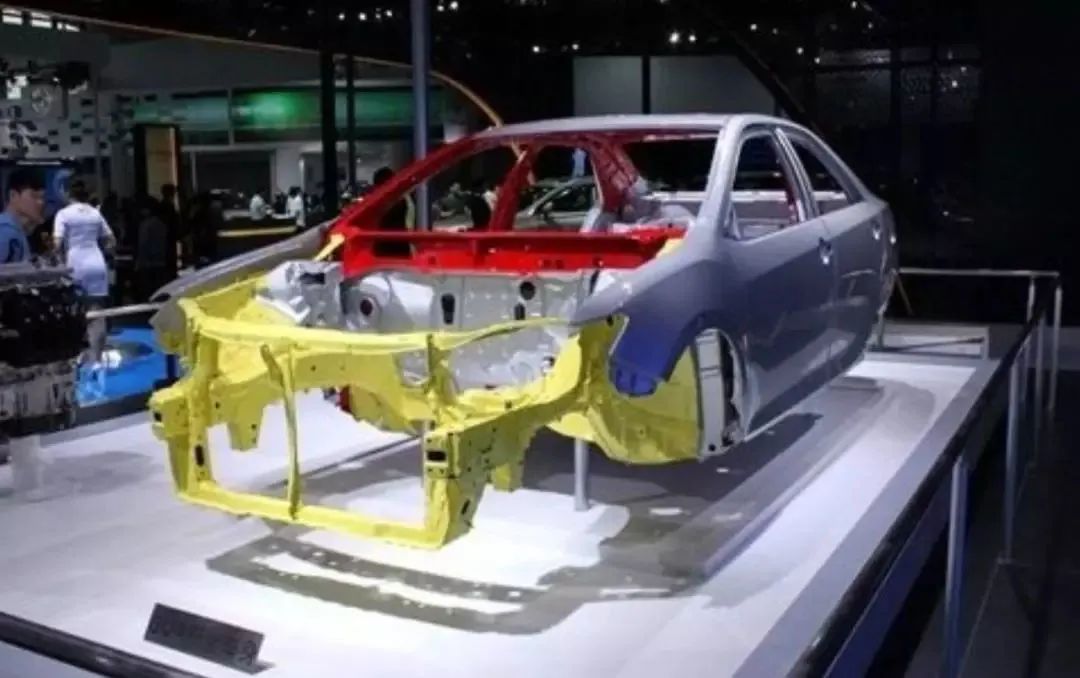
2009年,美国公路安全保险协会(IIHS)进行了一次非常有代表性的碰撞测试:用一辆2009N款雪佛兰Malibu中型轿车与一辆长度超过5.3m的1959款雪佛兰Bel Air全尺寸轿车进行50%偏置对撞测试。碰撞后两车均发生了严重变形,但两车情况不尽相同,Malibu的发动机舱严重变形,但乘员舱基本完好,而Bel Air的A柱严重变形,如果乘员舱内有驾驶员,其生存几率非常小。两车的碰撞测试结果表明了,汽车车身结构设计的进步对车身安全的影响之大,随着安全技术不断发展,车身安全性将不断得到提高。
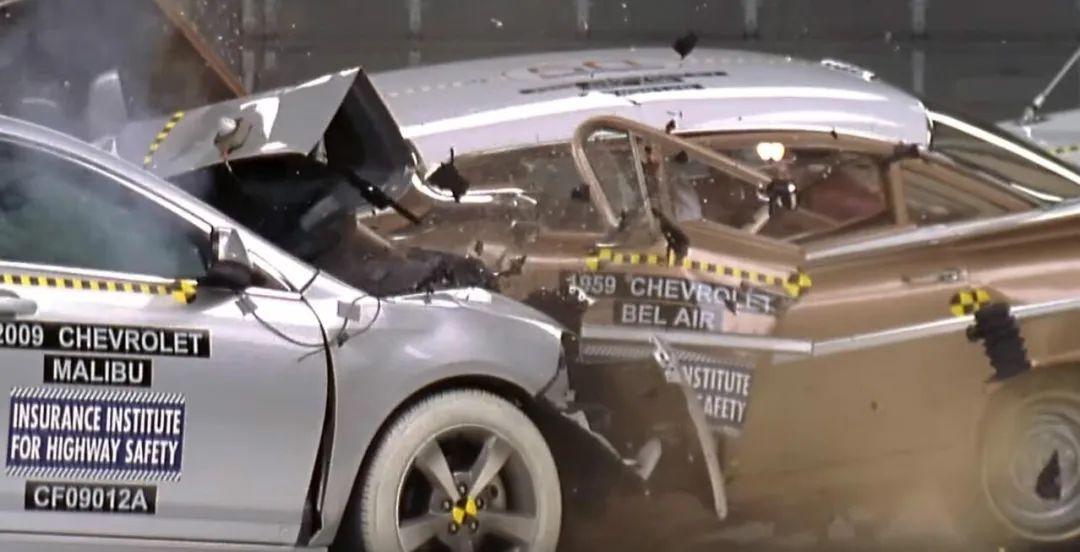
汽车安全技术发展到今天,在消费者中其实还有些误解。有很多消费者的概念中认为车身应用的钢板越厚越好,其实并非如此。过去车身采用厚钢板的目的是为了增加车身自重,使驾驶更平稳。而现在的汽车更多是通过降低车身重心来增加稳定性。在现在汽车设计中,为了降低油耗和生产成本,车身的钢板正在向更薄的方向发展。20世纪80年代,普通汽车车身钢板厚度大部分为1mm或者以上,到了90年代降低为0.8~1mm,到了现代大部分已经降低到0.6~0.8mm。但同时通过改进车身结构的设计,在应用更薄钢板后,车身的刚度和碰撞时的保护能力并没有下降。而且在车身的不同位置,会根据不同的作用选用不同厚度和强度的钢板。例如在车头、车顶和前后翼子板等部位,因为受力较小而是应用薄钢板,在前后防撞梁、纵向边框等部位受力较大,则应用较厚的高强度钢钢板。所以,车身的安全性能不取决于钢板厚度,而主要取决于车身结构、碰撞吸能技术和焊接工艺等多种因素。因此,在车身设计中遵循能量守恒定律,使前后车体在发生碰撞时能够吸收大部分能量,同时让乘员舱更加坚固,使其减少变形起到保护驾乘人员的作用。
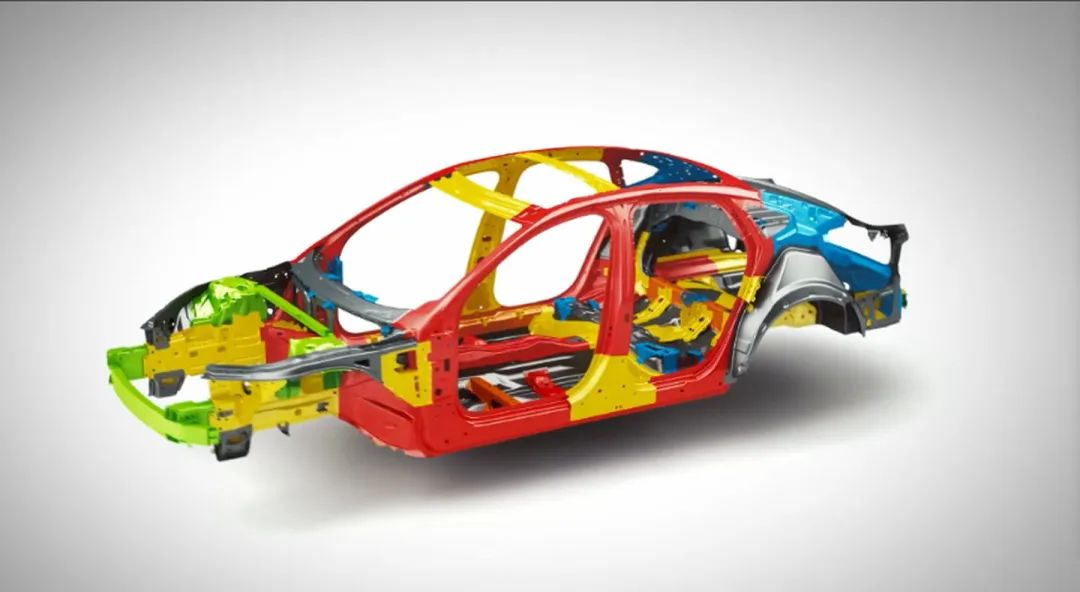
除应用材料和结构设计对车身安全能够产生影响之外,焊接工艺也是影响车身安全性能的一个重要因素。在现代汽车制造中,已普遍采用人工焊接和自动焊接相结合的方式,人工只负责焊接自动焊接不便操作的部位,对安全性能要求较高和大钣金件则交由自动焊接完成。此外,近年激光焊接技术已经逐渐在汽车制造中广泛应用,其特点就是变形极小、焊缝深度大,能够最大限度保证焊接强度,节省原料,位置准确,焊缝外观漂亮,最主要是能保证产品精密可靠,从而保证车身的安全性能。

如今,为更好的让消费者了解汽车车身发展情况,促进行业发展进步,中汽中心、中国钢研两大央企联合推出中国十佳车身评选活动。
中国十佳车身评选旨在通过专家技术背书引领汽车消费、唤起公众对车身技术的重视。评委团队由院士领衔,国内外顶级专家、教授组成,从材料、工艺、结构等维度,针对消费者购车时最关注的安全、舒适、节能等指标进行全方位评价,参与评选车型覆盖国内外主流品牌。
中国十佳车身评选主要从企业战略与车型定位、新设计理念、新材料开发及应用、白车身基本属性、生产过程及工艺、车身及整车中的应用性能和演讲的全面性及车身拆解展示等六个维度,针对消费者日常买车用车最关注的安全、舒适、NVH、节能等指标对车身的性能进行全方位考量,并加入了目前社会和行业比较关注的低碳策略,考察车型在设计、选材、工艺、生产、使用生命周期内等低碳措施。
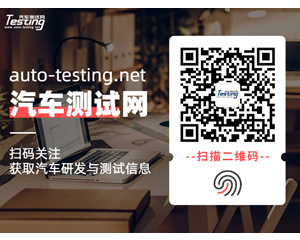
最新资讯
-
商用车及工程机械行业专场:NVH 及语音音频
2025-08-01 17:12
-
理想i8和重卡对撞测试引争议,东风柳汽发声
2025-08-01 15:52
-
艾德克斯IT-N2100 系列太阳能阵列模拟器
2025-08-01 15:43
-
ITECH重磅发布IT2705直流电源分析仪,重构
2025-08-01 15:34
-
现代汽车新一代混合动力系统:以技术革新引
2025-08-01 15:32