电驱动系统台架试验概述、测试结果举例及评级分析
一、电驱动系统台架试验的意义
相比于传统的内燃机汽车,电动汽车具有零排放、能量转换效率高等优点,已成为世界汽车技术发展的主流,其产业化进程飞速发展;同时,电动汽车相关的法律法规及整车性能对零部件技术要求日益提高,对汽车动力总成的性能测试要求也越来越严格。电动汽车车用驱动电机系统作为电动汽车动力总成的关键零部件之一,其性能参数、控制精度和可靠性直接影响整车的动力性、经济性和舒适性,台架试验不仅能够实时精确测量电机系统的性能,而且能够对其控制参数进行在线标定测量;基于电机测试台架或动力总成测试台架,能够实现整车道路循环测试工况的模拟,从而缩短其开发测试周期、降低开发测试风险与成本;因此,实现电动汽车用驱动电机系统的台架试验研究的必要性日益凸显。
1.1电机系统测试台架的组成
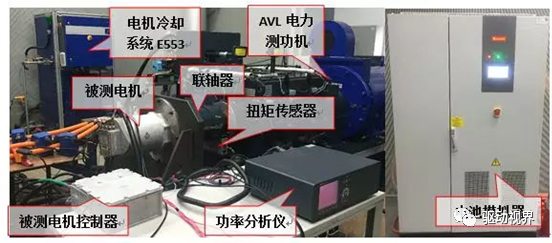
电机系统试验台架的功能模块主要包括电力测功机系统、冷却系统、电池模拟器、功率分析仪、自动控制系统,及被测电机系统、环境仓等。
1) 电力测功机系统包括测功机(永磁同步电机或异步电机等)、变频器、扭矩/转速传感器、联轴器等部分。联轴器实现测功机和被测电机系统的机械连接,扭矩和转速传感器负责测量系统的转速和扭矩。电力测功机系统主要的功能为:在试件驱动模式下,模拟实际负载并消耗被测电机消耗的机械功率;在试件发电模式下,提供机械功率输入。
2) 冷却系统的功能是为被测试件(电机和电机控制器)提供设定的冷却条件,此外还为测功机和电池模拟器提供冷却。
3) 电池模拟器,用于模拟车用电池的充放电行为,主要功能是保证电机控制器DC侧电压稳定,并实现和电网之间的电能传输。
4) 功率分析仪的主要作用为采集测试过程中电机控制器的DC侧、AC侧的电压、电流信号,以及机械侧的转速及转矩信号,为用户计算效率、损耗等性能指标提供依据
5) 自动控制系统的主要功能是用户和台架系统信息交互的窗口,主要包括三大功能:a. 用户通过自动控制系统输入试验工况,包括测功机的转速,试件扭矩,温度控制台架等;b. 测试数据的可视化及数据存储;c. 测试系统运行监控,自动控制系统实时监控测功机及被测试件的运行状态,一旦发生异常,自动控制系统发出急停信号,测试系统则会相应发来的急停信号,按一定的规则控制系统停机,保护测试系统不被损坏。
6) 环境仓为可选模块,用来模拟电动汽车可能遇到的不同范围内的温度条件。
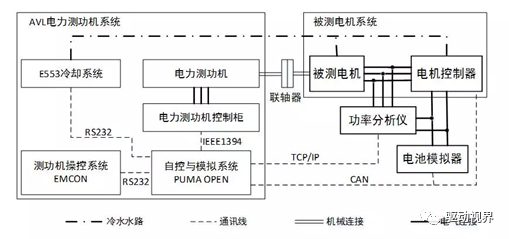
要实现对电机系统性能参数的全面有效分析,必须保证不同设备所测数据的实时性和同步性;因此,采用高速通讯总线(CAN或以太网)将电池模拟器、功率分析仪所测数据统一集成到台架软件控制系统,通过软件控制系统的时间基准实现所有测量数据的实时同步测量与记录,可以保证数据的时效一致性。
二、电机系统系统常见的性能试验测试项目:
参考《GB/T 18488.1-2015-电动汽车用驱动电机系统第1部分:技术条件》及《GB/T 18488.2-2015-电动汽车用电机及其控制器第2部分-实验方法》,在电机系统测试台架上,常见的测试项目包括:温升测试、开路测试、持续转矩/功率测试、峰值转矩/功率测试、堵转测试、效率测试、转矩控制精度测试、转矩响应时间测试、驱动电机控制器持续/短时/最大工作电流测试、驱动电机控制器电容主/被动放电时间测试等。此外,在电机系统测试台架上还可以进行路谱输入测试,如NEDC/CLTC等典型路谱
下面将介绍这些测试项目解读:
2.1温升测试
随着电动汽车技术的不断演进,集成化设计将无可争辩地成为未来发展的趋势,电动汽车三合一电驱系统技术是指将电控、电机和减速器集成为一体的技术。三合一电驱动技术给电动汽车带来诸多优点的同时,在工作过程中会产生大量的热,散热系统的设计对于散热能力、电驱动产品性能及系统安全至关重要,因此系统温升试验是电动汽车用电机设计的关键试验。
电机系统温升试验是指在特定的冷却条件下、特定的环境温度、特定的工况下,电机系统的温升性能的一项测试,其温升表现直接影响系统的扭矩输出性能。
温升试验重点考察一下几个方面的温升:电机定子、转子、轴承、IGBT、高压铜排、高压线束等。
GB/T 18488.1中对二合一系统的温升测试也有简要描述(在规定的工作制下,驱动电机的温升应符合GB755-2008中8.10规定的温升限值)。
通常通过设定常温冷却条件如25℃,设置额定工况,让系统持续运行一段时间或运行至热稳态,期间电机的温度变化值即为系统温升试验结果。温升应符合相关标准或者产品设计任务书中的要求。如下图,此图为某款电机在额定工况下运行至热稳态的温升曲线。
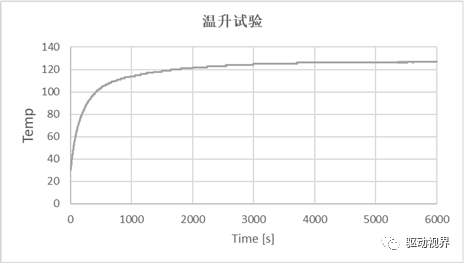
2.2 开路试验
开路测试即反电势测试。在最常见的永磁同步电机中,磁场来源于线圈和永磁体,永磁体产生的“电”即为电机中的反电势。由理论分析可知,线圈中励磁电流(is)为0时,此时产生的反电势就是永磁体产生的反电势,此时反电动势只和电机的转速和温度有关。通常用此方法来测试电机的反电动势:在不同的温度条件下,通过测功机以不同的转速拖动电机转动,测试反电动势的大小。
此时又分两种情况:
a. 如果电机和电机控制器之间是分离的,则直接测量电机UVW三相之间的相电压即为反电势的值
b. 如果电机和电机控制器之间三相是连接的,则测量经电机控制器整流出的直流侧电压值即为反电势的值。此时要注意的是,随着测功机不断的拖动使电机转速升高,能量反馈到母线上,可能会造成母线或者电池电压过高,损坏IGBT。
如下图为某款三合一电驱产品的开路反电势测试结果:
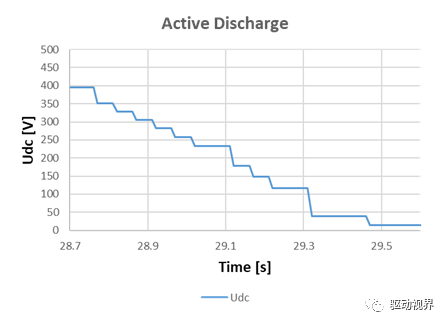
2.3 持续转矩、功率测试
电动车“百公里加速时间”和“最大爬坡度”等动力性指标是在零件设计之初就必须要考虑的事情,与其直接相关的就是电驱动系统的峰值性能和持续性能,本节我们先讨论在台架上进行持续转矩和持续功率的测试。
在台架上,通常设定电机处于热态,模拟整车上可能出现的最高冷却温度,在全转速范围内,请求最大的扭矩输出,持续运行30分钟或1个小时,取第30或者60分钟的扭矩值和功率值,作为电驱动系统的持续扭矩和持续功率,下图为某款电驱动系统的持续特性曲线:
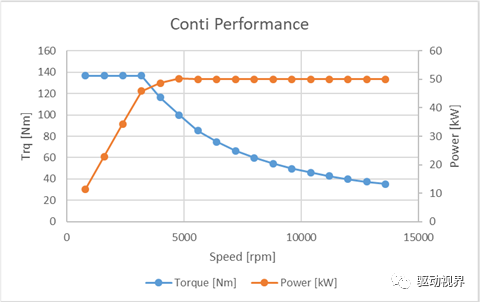
2.4 峰值转矩、功率测试
和电动车动力性相关的另一个性能就是电驱动系统的峰值性能。在台架上,通常在全转速范围内,请求最大的扭矩输出,持续运行30s或者60s,取第30或者60s的扭矩值和功率值,作为电驱动系统的峰值扭矩和峰值功率,作为评判此产品是否符合产品设计要求的依据。下图为某款电驱动系统的持续特性曲线:
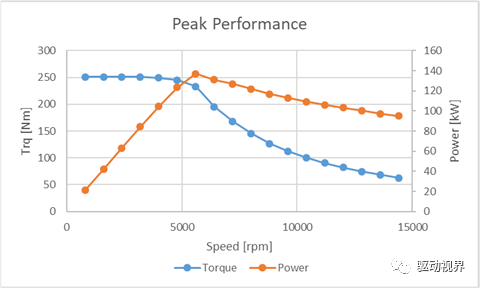
2.5 堵转测试
堵转描述的是电机转速为0时,在一定时间内,在母线仍然有足够电压保证扭矩输出的一种情况。由此可见,与堵转相关的两个参数分别为扭矩和扭矩持续时间。堵转工况是纯电动汽车常见的工况之一,主要表现为车辆由静止启动,在一定的坡度路面上启动,车轮被马路牙子卡死等情况。以上情况都属于驱动电机输出轴被抱死无法正常转动而处于堵转状态。
通常在台架上通过特定的制动锁止装置将测功机轴锁止,通过请求试件输出峰值扭矩或者峰值扭矩的60%~80%,持续运行5~30s,取第5/15/30s时刻的扭矩作为堵转扭矩,具体看主机厂要求,同时保证试验后试件能够正常输出功率。此外需要在电机转轴周向均布选取五个堵转位置,按照同样的初始条件重复堵转测试,以最小值作为最终测试结果。
下图是某电驱动系统在堵转工况下三相绕组电流的分布情况,可以看出,三相绕组的电流分布不均匀,且呈直流分布状态,此现象在此不做过多解释。
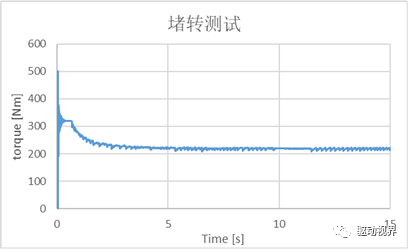
2.6 效率测试
电驱系统的效率描述的是系统输出机械功率和输入电功率的比值,效率越高意味着每度电的行驶里程更长,也就意味着用户得到的更长的续驶里程。电驱产品的设计要求中通常会有效率的指标,如最高效率和高效区(效率≥80%)占比。通常在做效率测试时,在全工作范围内,转速从最低转速到最高转速,按500rpm为间隔取点;转矩从0至最高转速按10Nm为间隔取点;取出所有的工况点作为输入,每个点稳定运行一段时间,取稳定时的功率数据进行效率计算,作为结果,并绘制效率map。如下图是某款三合一产品的效率map曲线,最高效率为97.7%,并且可以统计出高效区占比。
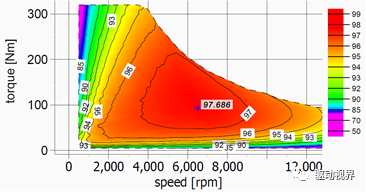
2.7 转矩控制精度测试
转矩控制精度也是评价电驱产品的一个重要指标,是整车关注的关键指标之一,直接影响了整车的驾驶性、能耗优化、以及转矩突变时的响应时间。在《GB/T 18488.1-2015-电动汽车用电机及其控制器第1部分-技术条件》3.11中给出了转矩控制精度的定义:转矩实际值和期望值的偏差,或者转矩实际值和期望值的偏差占期望转矩的百分比。对于电动车电驱动系统,输出转矩范围大,精度需要分情况定义,标准中给出了偏差与百分比两种不同的定义方式,一般在低转矩段,采用转矩偏差定义,在高转矩段,采用百分比定义,如输出转矩0~100Nm,转矩控制精度±5Nm,大于100Nm,转矩控制精度±5%。
在实际测试时,通常设置直流母线电压为额定电压,电机处于热态、电动工作模式,在设定转速下的10%~90%峰值转矩范围内均匀的取10个不同的转矩点作为请求值,达到稳定后记录数据作为实际扭矩,计算扭矩偏差值或偏差百分比,此值即为此转速下,对应目标扭矩的转矩控制精度。每个转矩下最大的扭矩控制精度即为特定转速下的转矩控制精度。此外在进行转矩控制时需要控制每个点的初始条件一致,如环境温度,电机温度,因为温度模型对转矩控制精度的影响是很大的。
2.8 转矩响应时间测试
转矩响应时间直接影响了纯电动车辆的驾驶性,以及遇到紧急情况时的反应速度。在《GB/T 18488.1-2015-电动汽车用电机及其控制器第1部分-技术条件》3.13中给出了转矩响应时间的定义:驱动电机控制器从接收到转矩指令信息开始到第一次达到规定的容差范围的期望值所经过的时间。
通常在堵转状态下测试电机系统的响应时间,使用抱紧装置将测功机轴抱死,请求扭矩在0s内上升至最大值,在此过程中,电机系统的输出转矩从零快速上升,尽量以较高的采样频率记录此过程的数据,驱动电机控制器从接收到转矩指令信息开始到第一次达到规定的容差范围的期望值所经过的时间即为转矩响应时间。此外,和堵转试验一样,需要在电机转轴周向均布选取五个堵转位置,按照同样的初始条件重复堵转测试,以响应时间的最大值作为最终测试结果。
2.9 驱动电机控制器持续/短时/最大工作电流测试
控制器的持续/短时/最大工作电流指标是和峰值转矩/功率、持续转矩/功率类似的评价指标,但其侧重于评价控制器输出电流的能力,是电机控制器的一个主要设计指标。通常选取接近弱磁区的基速区转速作为测量转速点,请求最大的扭矩,持续运行60s,记录全过程的三相电流数据,取此过程中的最大值最为短时/最大工作电流,取此过程中均值作为持续工作电流。
2.10 驱动电机控制器电容主/被动放电时间测试
电驱系统设置主被动放电的功能最主要的目的是高压安全,具体的说就是在紧急情况,如碰撞,短路等情况,以及每次操作时,都会有高压下电,而电机控制器中由于有薄膜电容等可储能装置,BMS控制下电以后,内部仍存在高压,为防止人员伤害,电机控制器需将电机控制器中的电压降低到A级电压以下(即60Vdc以下)。一般国标要求被动放电时间为5min内,主动放电时间要求10s内。
在有主动和被动放电回路设计的电驱产品中,可以采用以下方法测试被动放电时间:将电机控制器和电池模拟器正常连接,控制电池模拟器输出电压为电机控制器最大的工作电压,断开电池模拟器和电机控制器之间的继电器,此时电机控制器进入被动放电模式,记录全过程的电压数据,电压从最高电压降至60V所经历的时间即为电机控制器的被动放电时间。
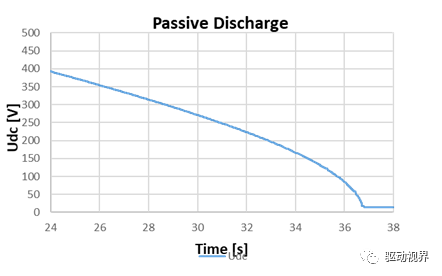
主动放电时间的测试方法类似,只是在断开电池模拟器和电机控制器时,同时请求电机控制器进行主动放电,电压从最高电压降至60V所经历的时间即为电机控制器的主动放电时间。
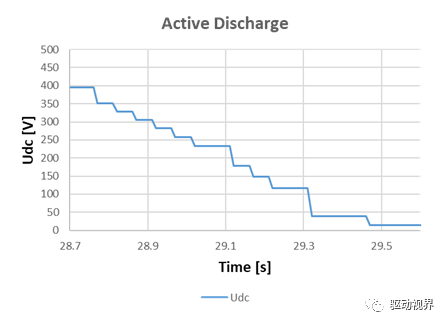
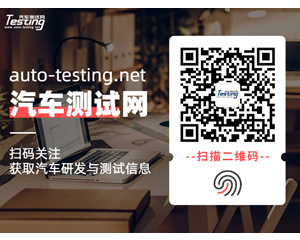
最新资讯
-
奇石乐两款发动机研发传感器新品亮相8月汽
2025-07-31 17:40
-
国内首个路空一体化大型综合试验场正式启用
2025-07-31 14:48
-
全球法规—日本汽车工业标准大全中文版(20
2025-07-31 12:38
-
直播预告 | 面向 ADAS 和 HMI 开发的可视化
2025-07-31 12:33
-
VW80000 GS95024 K-15冷凝实验 详细解读
2025-07-31 12:32