纯电动汽车动力电池组布置效率提升方法
文章来源:泛亚汽车技术中心有限公司
1提高电池布置效率的必要性
虽然中国纯电动汽车近几年发展势头愈加猛烈,但其销量还是远远落后于燃油车,客户对于纯电动的里程焦虑一直是制约纯电动车发展的重要因素,各个车企对于提高行驶里程也是费劲脑汁。例如特斯拉的超级充电桩,以及蔚来的换电站都是解决里程焦虑的有效措施。但无论是超级充电桩还是换电站都需要一个发展过程以及相关基础设施的普及。对于车企而言,成本最低、首先要考虑的就是在有限的空间内提高电池布置效率,增加续航里程。
早期的纯电动车动力电池有“土”字形、“T”字形、“平板”形等。但随着近几年电动汽车以及动力电池的飞速发展,开始向平板电池、模块化发展。电池组布置在车底,不仅可以尽量释放更多空间给乘客舱,还可以尽量降低整车重心,让车辆在同等情况下拥有更好的高速稳定性。因此,本文讨论的重点就以如何提高平板电池布置效率为主要内容。
2影响电池布置物理因素
2.1长度方向
从纯电动汽车底盘布置图可以看出,动力电池绝大部分都布置在前后轮之间,因为现有电动车一般都会保护四驱配置,前后轮心位置会留给前后电机,因此,电池组可以布置的长度空间与车型轴距有着直接的关系,轴距越大,留给电池的空间就越大。在一定的轴距条件下,可以看到电池前端被前副车架限制,电池后端被后悬架限制,如何在一定的轴距条件下布置尽量长的电池,需要重点关注。
选取市场上几款主流电动车,绘制整车轴距与电池长度关系,如图1所示。可以发现,虽然整车轴距对于电池长度有着至关重要作用,但是对于轴距空间的利用,每个车型大小有很大区别。在拟合曲线之上的车型轴距利用率较高,而在拟合曲线之下的车型轴距利用率较低。为了更好地找到影响轴距利用率的因素,选取前轮心—前副车架后端a和后轮心到后副车架前端b两个指标来研究布置效率。
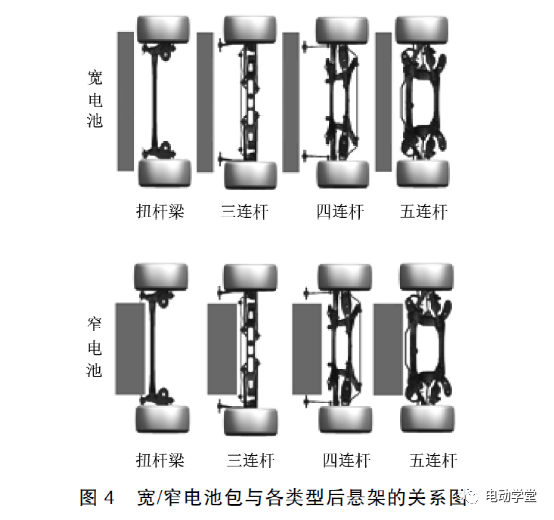
1.电池前端
前副车架的设计不仅起到支撑动力总成的作用还提供前悬架的安装点。从图2可以看出前悬架的安装点位置对于副车架的后边界位置有着决定作用,首先研究前悬架不同类型对于副车架后边界设计有无影响。目前乘用车主流前悬架分为麦弗逊和双叉臂两种类型,针对不同车型的前悬架后衬套边缘到轮心的距离p为研究对象,发现前麦弗逊悬架p值基本都稳定在325mm~335mm,q的主要因素在于副车架后安装点和悬架安装点的排列方式,传统车型两个安装点都是前后排列,为了缩小X向的距离,可以采用Y向排列,如图2中的圆圈所示。这种排列方式可以释放副车架衬套所占用的长度方向空间。图3为宽窄电池车身Y向界面图。
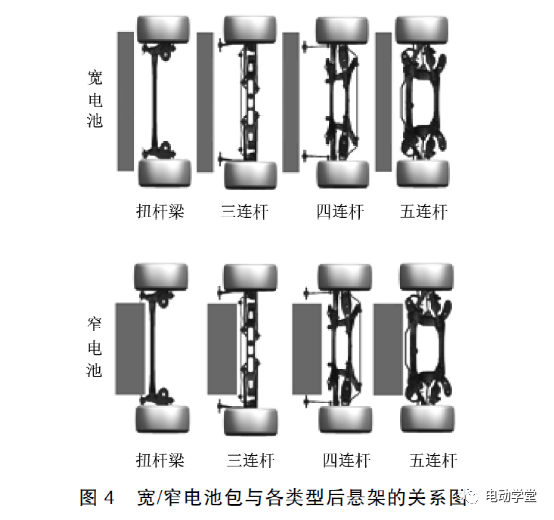
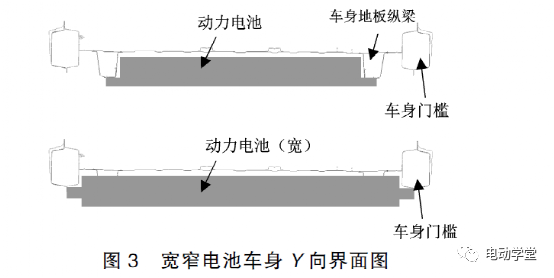
2.电池后端
后副车架的设计与前悬架不同,主要是由于后悬架类型诸多,如扭杆梁、三连杆、四连杆和五连杆。每种悬架在X向尺寸差异巨大,且它们侧重点不同。因此,对于电池布置的影响很大。研究发现,宽电池包和窄电池包对于不同后悬架影响不同。
对于宽电池包来说,其宽度基本已经到达门槛板,因此,限制宽电池包长度有两大因素:(1)轮胎大小;(2)悬架类型。
若轮胎前端面已经超过悬架或副车架最前端,则轮胎大小直接决定电池长度,五连杆和扭杆梁的X尺寸较小,就属于这种情况。
若轮胎前端面没有超过悬架或副车架最前端,则悬架类型决定了电池长度,三连杆或四连杆悬架由于纵向连杆(拖曳臂)的存在,悬架限制电池长度。
统计了不同悬架类型在X向的空间尺寸,如图4所示。可容纳电池长度:五连杆-扭杆梁>三连杆>四连杆。这是由于三连杆或四连杆自身结构存在纵向连杆,能支持侧向力,占用了大量X向尺寸。
对于窄电池包,宽度较小,电池可以布置在悬架纵梁连杆以内,从而增加电池的长度布置空间,因此,影响窄电池长度方向尺寸的主要因素是悬架类型。
分别统计了不同悬架类型在X向的空间尺寸,可知三连杆>四连杆>五连杆~扭杆梁。因此,各个车企可根据自身需求,选择适合自己的悬架类型和电池尺寸。
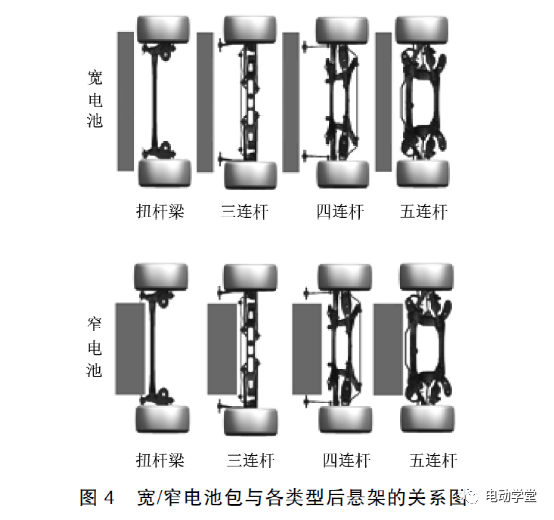
2.2宽度方向从图3车辆宽度尺寸链可以看出,电池宽度主要是由整车宽度决定的,减掉造型发挥空间,也就是由门槛版的宽度来定的,各个车企需要根据车辆尺寸定义级别以及造型需求尽量多的利用Y向空间。早期电动车大部分以油改电为主,燃油车架构的特点使得窄电池更容易满足侧碰的要求,且需车身提供内纵梁来固定,宽电池可以充分利用Y向空间,电池可以直接固定在门槛版上,目前的主流纯电动汽车平台都是采用此类做法发挥Y向空间最大化。
3影响电池布置的性能因素
3.1电池布置对车身拓扑优化的影响动力电池尺寸大,几乎平铺整个底盘,对整车拓扑分析、传力路径以及安全碰撞保护设计起着尤为重要的作用。因此,动力电池的布置与性能相关影响相辅相成、密不可分。根据上文阐述,宽平板电池和窄平板电池在拓扑分析、车身结构设计上有着很大的区别。宽电池传力路径:纵梁—车身门槛。窄电池传力路径:纵梁—车身地板纵梁。
3.2动力电池对安全性能的影响整车安全对电池保护的要求:整车完整的电路系统要求在各种国家规定的碰撞工况下均不可以与周边零件产生断裂应变的直接接触损伤,不允许有任何短路或者断路的风险。
X向:考虑到前碰各个前碰工况(RGB\ODB\SOF)下对电池的冲击,一般电池前端避免布置尖锐的硬性零件,电池离前轮心越远越好,但考虑到实际情况下,为了增大电量,在布置允许情况下会尽量将电池前置。这就对前舱零件布置提出了更高的挑战,转向前置可以避免转向电机对电池前端模块的冲击,这也是市场上大多数电动车采用的主要方法之一。
Y向:从整车安全角度,窄电池会更容易满足电路完整性保护的要求。但同样与整车增加电量的需求矛盾,因此,各车企也是费劲脑汁解决电池侧碰柱碰的问题。加大门槛板截面积以及内部填充各种支撑都是方法,但各有利弊,需要综合权衡。并且动力电池内部或外部框架需增加Y向承载纵梁。最后,对于电池周边零件,需要避免在碰撞路径上钣金尖锐边正对电池或者其他需要保护的连接电路系统,以免引起短路或者断路风险。
Z向:根据车型不同,电池厚度设计差异性很大。一般情况下,运动型多用途汽车(SportUtilityVehicle,SUV)车型有更高的车高,更高的离地间隙,可以支持更大Z向尺寸的电池,因此,SUV的电池厚度一般在140mm~160mm。而对于轿车,有车高和离地间隙的限制,减去乘客舱人的空间,可支持电池的厚度有限,目前大部分的轿车的电池厚度都在110mm~130mm。
3.3动力电池对制造的影响动力电池对制造的影响主要分两种,一种在油改电电动车,为减少车间改造带来的巨额投资,一般会与现有燃油车共线生产,其弊端是车身定位孔的保留会对电池的设计产生很大限制,比如电池要避开总装吊具,而原有产线前后吊具的距离也直接影响了电池长度;另一种是纯电动平台电动车,这种一般是全新产线,吊具前后定位孔的相对位置以及整车各个零件的装配顺序都可以重新设计,在保证电池电量的前提下去设计全新产线是相对容易的。
4结束语
通过以上分析可知,影响电池布置的因素诸多,要把所有因素考虑在内,再加上底盘一系列管路的布置,提高电池续航是对整车集成的一种挑战。当然,各个电池厂也在积极研究CTC、CTP等电池集成方案,或许在不久的将来,随着大家对诸多因素的整合、摸索,可以形成电池的标准化,对国家基础设施的建设无疑是巨大的贡献。
- 下一篇:航裕电源:汽车仪表电性能测试解决方案
- 上一篇:不同荷电状态下动力锂离子电池的热失控
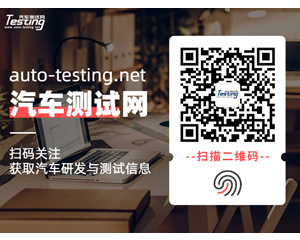
最新资讯
-
正式启用!上海再添一家高标准汽车试验中心
2025-09-05 16:10
-
「行业信息」座椅舒适性有行业标准了!《汽
2025-09-05 15:03
-
E-NCAP2026对驾驶员参与度的要求V1.0
2025-09-05 15:01
-
直播预告 | 从概念设计到虚拟验收:实时车
2025-09-05 15:01
-
基于VA ONE的eVTOL舱室噪声仿真分析(一)
2025-09-05 14:55