汽车双质量飞轮动态试验方法研究
[摘 要]:发动机产生的扭振影响了汽车舒适性和安全性。双质量飞轮较传统单质量飞轮而言,具有更好的减振效果。根据周向长弧型弹簧式双质量飞轮的结构和减振原理,结合机械系统动力学推导出双质量飞轮的扭转振动角度数学解析式。根据双质量飞轮的减振原理以整车为扭振试验对象,进行了量化的测试试验。研究与试验结果表明:经双质量飞轮减振后,车辆传动系的低频共振区处于汽车怠速转速以下,且扭振振幅得到了衰减,试验验证了双质量飞轮对发动机轴端扭振具有一定的抑制作用。
关键词:扭转振动,双质量飞轮,动态试验
1 引言
随着汽车工业的发展越来越成熟,人们对车辆驾驶的舒适性和运行的平稳性要求越来越高,车辆的振动噪声等问题成为当前研究的热点。当发动机工作时,发动机运动部件的重力和往复惯性力以及气缸内气体的压力变化产生扭矩周期性的波动,会在曲轴上产生周期变化的作用力矩,引起较大的扭转振动,并将扭振传递到汽车传动轴系中,是引起汽车振动与噪声的主要原因[1]。
传统的扭振减振器受限制于空间,弹簧转角很小,减振效果有限。双质量飞轮(Dual MassFlywheel,DMF)具有良好的动态性能,能够有效地降低汽车传动系统的扭振,在国内外得到广泛的应用[2];但是,国内对DMF 的研究起步较晚,对减振特性缺乏有效地理论与试验验证。目前,对于DMF 的扭振特性研究大多采用台架动态试验,结果与实际情况存在一定的差异。因此,以目前最常用的周向长弧形弹簧式双质量飞轮为研究对象,对整车状态下DMF 的扭振特性进行研究。
2 汽车传动系统扭转振动特点分析
汽车动力传动系统是一个非线性多自由度的扭振系统,当激励频率与系统的固有频率重合时,会产生严重的共振现象。传统汽车控制扭振的方法是在离合器从动盘中安装扭振减振器,这种减振方法存在两个方面的局限性:(1)由于离合器从动盘中弹簧扭转角度受到限制,弹簧刚度无法降低,减振效果不是很理想;(2)不能将传动系统固有频率对应的转速降低到怠速转速以下,即不可避免地在怠速时产生共振。而DMF 通过主、副飞轮的转动惯量,弧形弹簧的两级刚度,以及黏性摩擦阻尼三部分控制汽车动力传动系统的扭振,以便有效地达到隔振和减振的目的,完美地解决上述问题。
汽车发动机起动和停止的过程中,不可避免地通过传动系统的共振区,其特点是振动频率较低,且产生较大的扭角,随着发动机转速下降扭角会进一步加大;汽车怠速和正常行驶的过程中,在激振频率较高的情况下,易产生轴系的扭振;发动机加载的过程中,突发性的加载激励会在低频区产生较大的扭角。上述三种情况的扭振特性主要体现扭振频率和扭角振幅,所以通过调整DMF 的扭转振动、阻尼和主副飞轮的转动惯量控制传动系统的扭角振幅[3]。不同工况下汽车传动系扭振特点分析,如表1 所示。
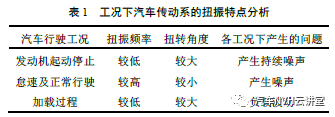
3 双质量飞轮扭振数学模型
3.1 双质量飞轮的结构
双质量飞轮介于发动机与离合器之间,是由第一质量和第二质量两部分组成。第一质量(也称主飞轮)保留在原传统飞轮的位置上,用于起动和传递发动机的转动扭矩;第二质量(也称副飞轮)放置在传动系变速箱一侧,用于提高变速箱的转动惯量;两级质量由阻尼弹簧减振器耦合为一个整体,阻尼弹簧为两根周向长弧型扭振弹簧,该结构形成了多级的扭转刚度,满足怠速和正常行驶不同工况下的刚度要求。由于减振弹簧布置半径增大,允许的相对扭角变大;同时,在滑道中充满了粘性油脂,产生阻尼作用,使DMF 具有很好的阻尼特性。DMF 的结构,如图1 所示。
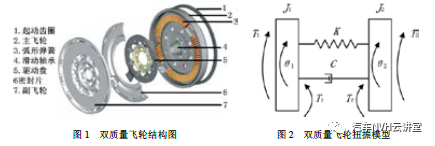
3.2 双质量飞轮扭振的数学模型
双质量飞轮扭转振动特性反应DMF 在怠速及正常行驶工况下主、副飞轮扭转角度之间的关系,其扭振模型如图2 所示。在工作过程中,主飞轮扭转角θ1,副飞轮扭角θ2,激振输入扭矩 T 1 ,负载输出扭矩T 2 ,传递扭矩T t ,主飞轮及发动机曲轴系转动惯量J 1 ,副飞轮及传动系转动惯量J 2 ,扭转刚度K ,阻尼系数C 。
一般DMF 采用的是两级弹簧刚度并联式的设计,弹簧刚度随着发动机转速的变化成阶梯跳跃:在怠速或转矩较小的工况下,当T≤K时, K K1 ,第一级的扭转刚度可以有效的隔振和控制噪声;在正常行驶工况下,当T Kθ1-θ 2 时, K K2 ,第二级的扭转刚度以传递较大的扭矩,隔离路况对传动系统的反向作用。运用系统矩阵法,对阻尼作线性化处理进行求解。将系统离散为两个质量、阻尼和弹性元件组成的二自由度振动系统,根据机械系统动力学,建立DMF 的强迫扭振方程:
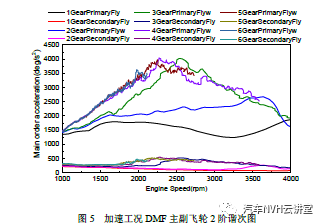
以外部激励为简谐激振为例,设系统外部激振频率,主、副飞轮扭角振幅A 1、A 2,振动位移相位角A 1 、A 2 ,激振力矩相位角 φ1、φ2,化为矩阵方程形式:
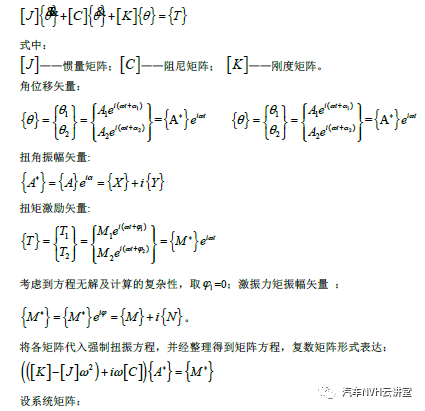

由上述扭转角度解析式得知:合理设计DMF 的转动惯量J ,连接刚度K 及阻尼系数C 可达到最佳阻尼值。但事实上,三个参数是相互牵连的,会受到结构、强度及工艺等各个方面的限制,因此需要通过理论仿真和试验来调整DMF 的工艺参数,以达到最优解。
4 双质量飞轮扭振试验与分析[4]
人们在乘坐汽车时,车辆的振动作用会直接影响到驾驶员的工作效率和乘客的乘坐舒适性、健康和安全。现在人们对于振动的感觉“量化”已经形成国家标准SIO2631《人体承受全身振动的评价指南》。
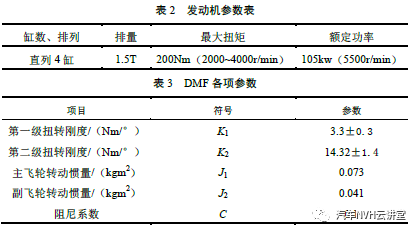
以往DMF 的扭振测试,都是在扭振试验台上进行的,未考虑到DMF 与整车的相互作用,所以有必要进行双质量飞轮的整车试验,以此来评价双质量飞轮的减振降噪效果[3]。本文以某车型为研究对象,研究整车状态下双质量飞轮的扭振特性[5]。试验所用的发动机参数如表2 所示,DMF 的具体参数如表3 所示。
为客观的评价双质量飞轮的减振性能,一般测量DMF 的主、副飞轮扭转振动的角速度或者角加速度,以及汽车驾驶室、车身各处的振动和噪声,以此来分析减振器的隔振效果。
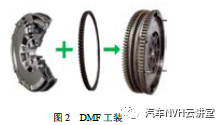
整车状态下,可以利用霍尔式转速传感器和主飞轮的起动齿圈,采集DMF 第一质量的扭转角度。但是,副飞轮没有齿圈,无法采取第二质量的扭转角度,为此将齿圈工装安装在副飞轮上,且保持其转动惯量不变(如图2 所示),进而采集DMF 第二质量的扭转角度。
4.1 起动工况
双质量飞轮可以通过扩大扭振减振器的扭转角度,改变角动量的分量来改变发动机的共振转速范围。发动机的角动量由主飞轮来调整,变速器的角动量受到副飞轮、离合器压盘及从动盘的影响。起动工况下,DMF 主副飞轮的转速、相对转角及2 阶角加速度如图3 所示。传动系在15.6s 左右出现共振转速约为500rpm 左右;由于DMF 穿越传动系的共振转速,使得DMF 出现了较高的相对摆动,所以主副飞轮的相对转角和2 阶出现幅值,且可以看出DMF 具有较好的隔振作用,从而提高了整车的驾驶舒适性。
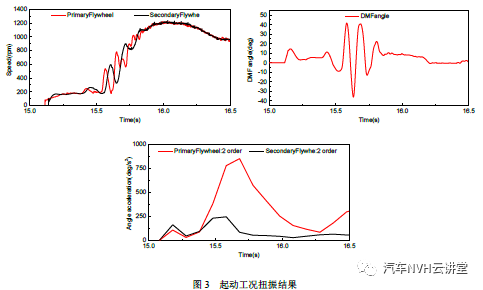
4.2 怠速工况
怠速工况下,DMF 主副飞轮的转速、相对转角及2 阶角加速度如图4 所示。
从图中可以看出,匹配DMF 后,在整个转速范围内,副飞轮的转速波动与主飞轮相比大幅降低,主、副飞轮的相对转角在2deg 以内;与传统的单质量飞轮加带扭振减振器从动盘的组合相比,双质量飞轮将发动机在怠速状态下的扭转振动几乎全部衰减掉,这是DMF 的特点,这对降低变速器的Rattle 噪声和提高驾乘舒适性是有利的。
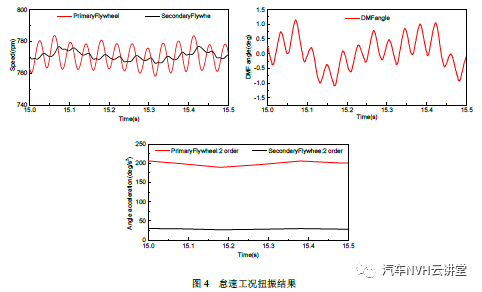
4.3 加速工况
各档位全负荷加速工况下,DMF 主副飞轮的2 阶角加速度如图5 所示。
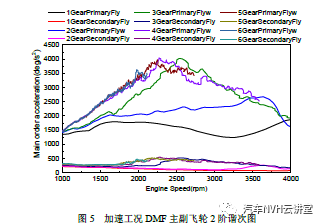
从图中可以看出,发动机端主飞轮的2 阶角加速度最高达4000deg/s2,经过DMF 的减振作用后,副飞轮的2 阶角加速度降低到500deg/s2 以下,达到的行业内双质量飞轮的减振要求,较大的降低了变速器输入端的转速波动,抑制了传动系扭振,从而提高了整车的驾乘舒适性。
综上所述,双质量飞轮对汽车在不同工况下的减振、降噪等方面具有突出地优点,提高了手动档车辆驾驶的舒适性和平顺性。然而,双质量飞轮也存在一些缺点:首先,双质量飞轮较传统单质量飞轮的成本高;其次,由于飞轮一分为二,主飞轮的转动惯量小于传统单质量飞轮的转动惯量,在一定程度上加剧了发动机曲轴本身的扭转振动,对发动机的附件系统会产生不利影响;再次,双质量飞轮的轴向尺寸比较大,适用前置后轮驱动汽车,对前置前轮驱动的汽车空间布置加大了难度。
6 结论
(1)以某增压车型为试验对象,分析了不同工况下,匹配DMF 汽车的传动系扭转振动特点,得出了DMF 的整车动态试验分析方法;
(2)根据DMF 的结构和工作原理,结合机械系统动力学推导出DMF 的扭转振动角度数学表达式;
(3)提出了DMF 的整车动态试验方法,试验结果表明,采用双质量飞轮后,降低了汽车动力传动系统的低阶固有频率,明显地降低了传动系的转速波动,抑制汽车传动系的扭振,具有较好的减振效果,改善汽车常用车速行驶时的扭振特性。
作者:李建鹏,贺娜娜,王鹏,鲁守卫
作者单位:北京汽车动力总成有限公司技术中心,北京 101108
来源:2016汽车NVH控制技术国际研讨会论文集
- 下一篇:HBK推出最新版本Tescia软件
- 上一篇:电动汽车用电动压缩机控制策略研究
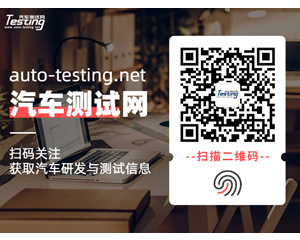
最新资讯
-
商用车及工程机械行业专场:NVH 及语音音频
2025-08-01 17:12
-
理想i8和重卡对撞测试引争议,东风柳汽发声
2025-08-01 15:52
-
艾德克斯IT-N2100 系列太阳能阵列模拟器
2025-08-01 15:43
-
ITECH重磅发布IT2705直流电源分析仪,重构
2025-08-01 15:34
-
现代汽车新一代混合动力系统:以技术革新引
2025-08-01 15:32