动力总成系统标定与单电机标定对比分析
电动汽车因节能环保已经成为未来汽车发展的必然趋势。与传统的燃油汽车不同,电动汽车的动力系统主要是动力电池供能下的电机驱动系统。电机驱动系统主要包括驱动电机与控制器(包含电机逆变器部分),电机驱动系统的性能直接影响整车的动力性、经济性和舒适性等,因此驱动电机与控制器的性能测试和标定在整个电动汽车系统开发中占据重要的地位。
本文介绍的标定是指电机实际功率特性的测试试验,根据功率分析仪对电机功率的测试与测功机对电机输出功率的测试,标定出电机在不同工况下的效率值。另外,也是对电机后期控制的一个准备。根据标定时电机的电流、反电势等参数,得到电机输出功率值,从而在实际使用中更准确的控制输出。不同的电机自身的一些本体参数不同,额定电压、额定扭矩、额定转速等等也不同,如果不进行标定,可能电机和控制器也能运行起来,但肯定达不到想要的效果。所以电机标定主要也是使控制器和电机达到最佳的匹配。
一、单电机标定:
单电机标定连接方式如下图1:
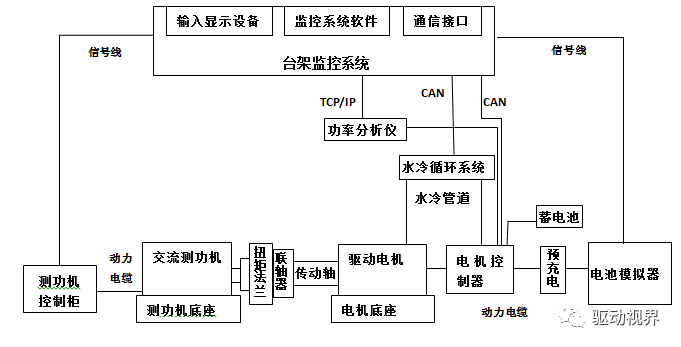
图1
1.1电机标定前准备
电机标定前都要对旋变零位进行校准,电机零位初始角对电机输出扭矩的精度至关重要,例如,某款电机当旋变零位初始角存在±2的电角度偏移,则会导致电机输出扭矩在无弱磁区±3Nm的误差,在高速弱磁区约±7Nm的误差。
1.2 电机标定
给定某三相电流,使UVW合成电流Is始终指向A相,即U相,此时电流Is产生的感应磁场和转子永磁体的磁场相互作用,使D轴与A相重合,此时读取旋变实际测量角度为0,基于该理论可实现电机标定,电机标定方式有手动标定和自动标定,可根据各自情况选择。
1.2.1 手动标定
手动标定:转速都由对拖电机或测功机控制,对对拖电机设定固定转速,然后被测电机标定所需要的数据。标定使用电流环标定,通过上位机给定对应Id、Iq确定电机最大电流、最大转矩、最大功率。
1.2.1.1 拐点之前
拐点之前使用MTPA(最大电流转矩比方式)标定,设定Is和θ角,寻找最大转矩电流比的值,如下图2所示。
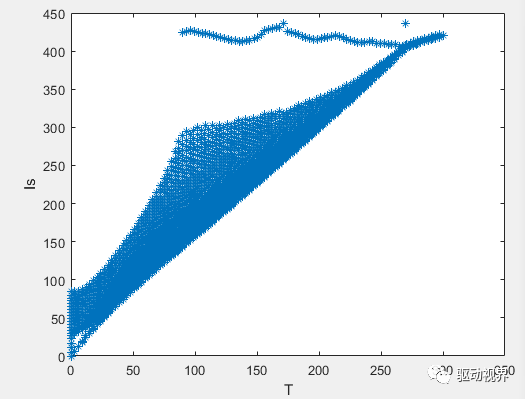
图2
具体操作:
1) 测功机或对拖电机设定500rpm,把最大电流等分成15个点。
2) Is从0开始每次增加1/15,之后调节θ角度,观察反馈转矩,找到转矩最大点,记录当前转矩对应的Id、Iq给定值。
3) Is继续增加,按上述方法找到新的Is下的最大转矩点。找到转速拐点,设定标定好的MTPA最大转矩点,增加转速,观察电压利用率,电压利用率刚好达到90%时对应的转速为拐点转速,拐点转速之前都是用MTPA曲线。
1.2.1.2 过渡区
增加转速继续标定,先按照MTPA曲线从0开始增加,观察电压利用率(可以观察Vd、Vq合成矢量Vs的大小占电压圆(Vdc/1.732)百分比),电压利用率超过92~95%,电压到了95%之后,直接使用Id、Iq模式,先负向增加Id,电压利用率会下降,然后增加Iq,增加到电压利用率到了95%左右。
1.2.1.3拐点之后
随着转速上升,会从MTPA完全过渡到MTPV,预先给定足够大的Id,然后再增加转速,保证到达新的预定转速之后电压利用率不能超过90%,直接使用Id、Iq模式,先负向增加Id,电压利用率会下降,然后增加Iq,增加到电压利用率到了90%左右。
以上流程为手动给定Is电流和角度来实现,标定点的数量决定后续扭矩精度;手动标定基本标定后将标定数据对应写入程序中,用于后续控制上查表。
1.2.2 自动标定
当前趋势是使用自动仿真来实现对应数据,使用上位机自动模式控制电机运行不同角度和电流;同时将相关数据存储通过仿真来得到所需的Id、Iq(如图3所示)用于后续查表使用。
具体操作:
1) 固定1个弱磁以下恒定转速n1, 根据最大电流设定好电流步长,相应电流步长对应设定好的角度θ给出不同的Id/Iq,通过上位机自动遍历所有设定的电流和角度
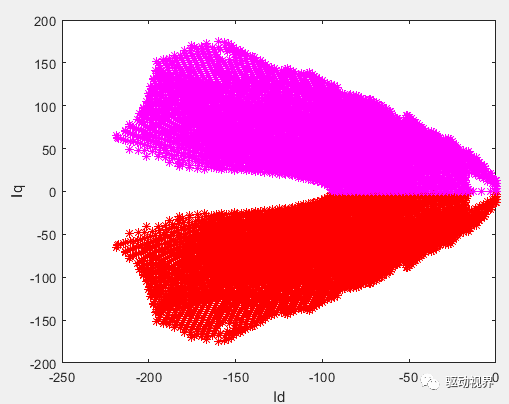
图3
2) 固定1个弱磁以下恒定转速n2,该转速为原n1转速2倍, 根据最大电流设定好电流步长,相应电流步长对应设定好的角度θ给出不同的Id/Iq,通过上位机自动遍历所有设定的电流和角度点,自动记录转速并计算得到对应Ud/Uq。注意:在实施1)和2)之前,先选择其中一个角度下设定好的电流步长进行运行,将测试数据进行仿真得到相关Id/Iq、扭矩、电流、功率、转速数据。根据该数据将转速调节到对应值,输入对应的Id/Iq查看扭矩、电流是否对应;如扭矩偏差小扭矩±5Nm,大扭矩±3%,实际电流有效值和仿真数据基本一致;在判定一致后重复1)和2)遍历所有工作点。
3) 通过matlab仿真软件读取电机峰值功率(如下图4所示)、最高转速、峰值电流、母线电压、最大转矩、电阻、电感与运行得到的Ud/Uq等相关参数;通过相应运算得到对应Id/Iq值,并生成对应.h头文件和.c文件用于程序中。
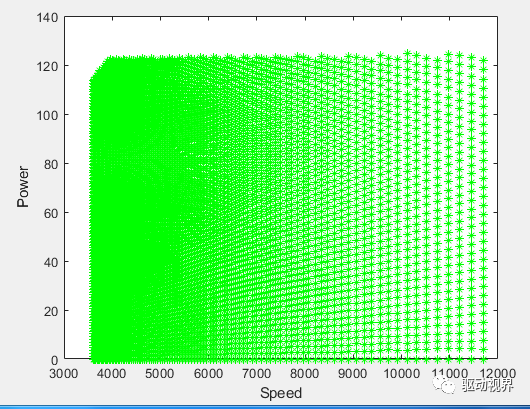
图4
二、动力总成系统标定:
随着行业的不断发展,动力总成小型化、高速化已是新能源汽车驱动系统的主要发展趋势,乘用车是目前驱动系统基本已经转向电机、电控、减速器集成设计,同时电机和减速器很多情况下共壳体。为解决需重新单独做单电机标定壳体问题,电机标定将开始从单电机标定到电机连接减速器一体的动力总成系统标定模式,总成标定台架搭建如下图5所示。
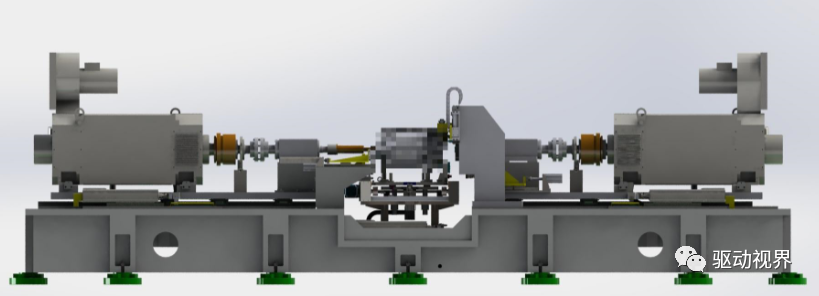
图5
总成标定和单电机标定模式基本没有差异,只是在处理转速和转矩的数据时乘或除减速器相关速比,同时总成标定相比单电机标定存在以下几个主要差异:
1、如单电机标定电机的高速化也会导致对拖台架或测功机的电机转速高速化,扭矩传感器高速化,对比来说总成标定两端陪测电机只需要低转速大扭矩即可,该方案更加容易实现。
2、总成标定读取的扭矩是减速器两端的扭矩,即最终动力输出扭矩,标定完成即可得到减速器、控制器、电机一体的最高效率,总成标定更加接近于实车性能。
3、总成标定需要考虑扭矩对应精度问题,经过减速器后两端采集的扭矩传感器会根据减速比关系放大,因使用的扭矩传感器量程大,所以精度上肯定会有所降低,但是对整车工况实际作用影响并不大。
综上所述,随着新能源乘用车动力驱动系统的发展,不管是从标定与整车性能参数的适用性,还是标定的便利性,动力总成系统标定将越来越受行业的青睐。
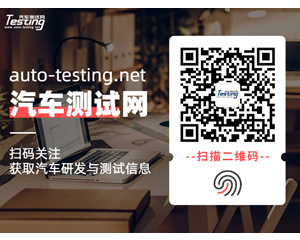
最新资讯
-
商用车及工程机械行业专场:NVH 及语音音频
2025-08-01 17:12
-
理想i8和重卡对撞测试引争议,东风柳汽发声
2025-08-01 15:52
-
艾德克斯IT-N2100 系列太阳能阵列模拟器
2025-08-01 15:43
-
ITECH重磅发布IT2705直流电源分析仪,重构
2025-08-01 15:34
-
现代汽车新一代混合动力系统:以技术革新引
2025-08-01 15:32