800V高压平台 & SiC 车规级应用
摘要
■800V 平台可有效解决电动车里程焦虑、快充速度问题,车企纷纷布局:续航能力和充电时长是影响电动车普及程度的重要因素,现阶段新能源车的续航里程大约为 500-600km,无法满足城际间长里程驾驶需求;另外由于新能源车补能效率较低, 燃油车的加油时间仅为 5 分钟左右,而新能源车充电通常需要 60 分钟,提升电压平台可提升整车运行效率及充电速度。以保时捷为例,保时捷将电压平台从 400V 提高至800V 后,实现 300kW 充电功率,可以在 22.5 分钟内把 Taycan Turbo S容量 93.4kWh 的动力电池从 5%充至 80%, 提供 300 公里的续航能力,高压线束的截面积仅为 400V 架构下的二分之一,线束减重 4kg。吉利极氪、小鹏汽车、广汽埃安、比亚迪、理想汽车、北汽极狐、岚图等车企也相继投资 800V 电压架构产品,并逐步计划量产。
■采用碳化硅器件并未提高整车成本:目前单个碳化硅功率器件的价值量约为硅基IGBT的3倍,但主机厂通常从整车成本考虑,采用碳化硅能带动整车系统效率提升,从而降低系统其他部分成本。根据产业调研,在中高端车型中使用硅基IGBT的总体成本约为3000元左右,碳化硅器件成本约为硅基IGBT的3倍,在相同性能的产品中,使用碳化硅器件可使汽车续航能力提升5-10%,以5%的性能提升计算,对应电池端即可节省4000-5000元,碳化硅耐高压和耐高温特性可使得电缆、散热系统等成本降低,仅散热系统即可节省1000元左右,综合成本可抵消器件本身成本的增加。使用碳化硅并不会增加整车成本,这为行业发展带来长久动力。
■碳化硅成本下降空间大,800V架构车型有望向经济型下沉:目前碳化硅衬底制作难,长晶速度慢导致成本过高,是影响碳化硅器件渗透率的主要因素,现阶段采用碳化硅器件的多为中高端车型。未来随着碳化硅衬底工艺提升、尺寸扩大及行业产能增加,势必带来产品成本降低,经济型电动车也将有望搭载高压方案。目前6寸导电型衬底片的市场零售价约1000美元/片,据产业调研,到2025年价格有望下降至500美元以下,硅基和SiC基的成本差距会在2倍内,届时碳化硅器件更据优势,渗透率将有望持续提升。
■目前问题:新能源汽车发展不及预期;800V架构产品量产不及预期;SiC技术难度大,产品研发、量产不及预期;SiC渗透率不及预期。
01新能源汽车向 800V 高电压平台演变, 对功率器件要求持续提高
1.1. 电压平台演变历史:从量变到质变
在燃油车时代,通过升高电压的方式实现电能的大功率传输,满足汽车供电需求。1918年,汽车引入蓄电池,其电压仅为6V;随着汽车电器如车灯、照明、ISG等用电器件的增加,6V低电压系统无法满足车用电器功率要求,加之电气化部件的大量集成,1950年汽车电压平台升级为12V;二十世纪九十年代,出现42V汽车电压平台,但是由于零部件升级电压规格成本高而未能实现;2010年前后,在信息娱乐、混动的需求背景下,欧洲发起48V电压系统升级,Audi, BMW, Daimler, Porsche, Volkswagen 联合推出48V系统,与12V电压平台共存;2020年,各国节能法规的颁布推动48V低电压平台发展。
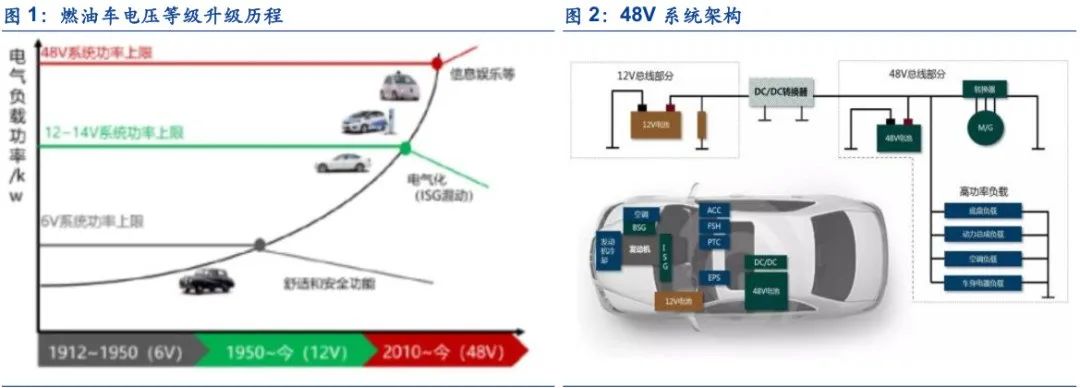
随着车载电器数量的增多,以及自动驾驶、节油减耗等要求的提出,电动汽车的电压平台将逐渐由 400V 升高至 800V,以分担蓄电池的工作压力。纯电动汽车中成百上千个电池串并联形成超百伏的电池包, 其高压系统主要包括动力电池、配电盒、OBC、DCDC、电驱、PTC、空调、充电口等。
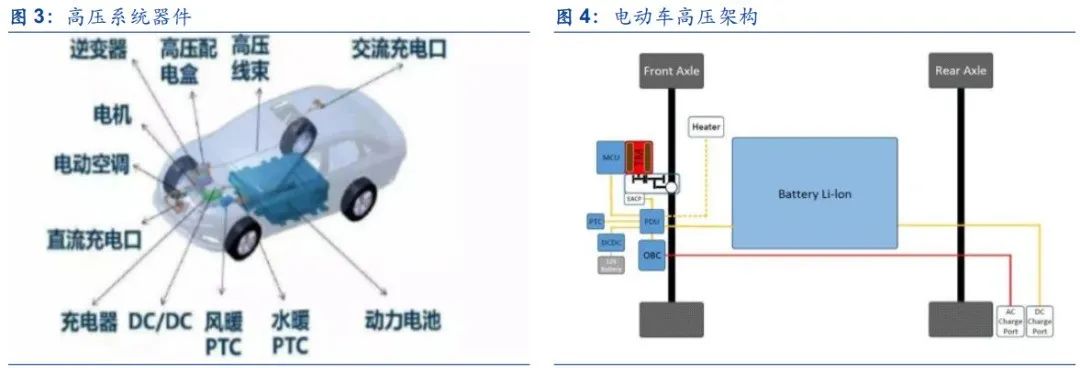
目前,电动车根据带电量不同选择不同的电压等级。一般小型代步车的电压为48V、60V和72V;乘用车的电压范围大约为250-450V;大巴车、公交车等由于带电量高,其基本电压为450-700V。在未来,随着对续航里程、充电速度要求的提高,电动车电压有望升至800V-1000V。
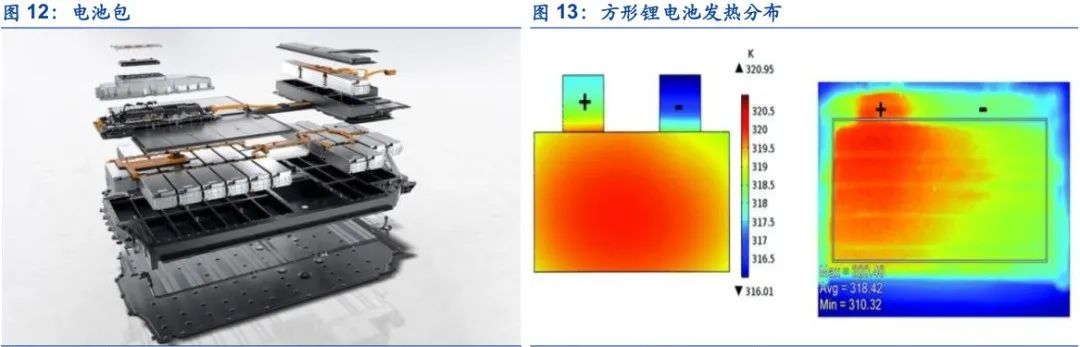
国内外车企纷纷布局800V高电压平台。2019年4月保时捷Taycon Turbo S 全球首发,业内最先量产800V高电压平台的汽车,将最大充电功率提升到350kW,可以在22.5分钟内把Taycon Turbo S容量93.4kWh的动力电池从5%充至80%,提供300公里的续航能力。2020 年12月,现代汽车集团推出全新电动汽车专用平台 “E-GMP” ,该平台同样搭载可以实现最大 800V 多功能充电系统。Rivian和通用也已经计划将电压改为800V。国内,吉利极氪、小鹏汽车、广汽埃安、比亚迪e平台、理想汽车、北汽极狐、岚图等车企也已经布局了800V快充技术。
1.2. 电压高压化:里程焦虑、充电速度慢问题的最好解决方案
续航能力是决定新能源汽车普及程度的重要因素。大部分新能源汽车的续航里程低于600公里,低于燃油车的续航里程,难以满足城际间的长里程行驶需求。目前,市场上较畅销的新能源车型包括特斯拉、比亚迪、蔚来、小鹏等,其中,比亚迪唐和比亚迪宋的续航里程为505公里;特斯拉的续航里程范围为545-675km;小鹏P5续航里程600km。新能源车的续航里程仍有较大的上升空间,不足以满足未来人们长里程驾驶需求。
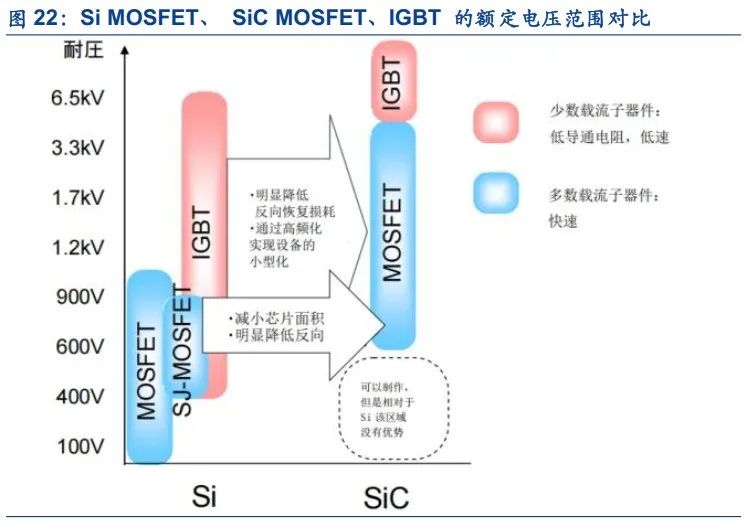
与燃油车相比,新能源车的补能效率较低。燃油车的加油时间仅为5分钟,而目前快充至少需要60分钟。在高峰期充电排队等候的时间亦进一步拉长。目前,主要有以下三种充电方法:
➢ 在家中充电:家庭用户使用的三眼插座有10A和16A两种规格,约8-10小时可以充满。
➢ 交流充电桩:将电动车直接在电流更大的交流电网上,用充电桩进行充电,充电时长约4小时。慢充电桩功率通常为3.5kW和7kW,取决于车载充电机的额定输入功率。
➢ 直流充电桩:将电动车连接到交流电网或直流电网时,使用了带控制导引功能的直流供电设备。由大功率非车载直流充电机直接输出直流给车辆电池充电。在充电时,充电桩需要提供与电池相匹配的电压,国标规定直流输出电流最大不超过250A,多数电动车能获得不高于102.5 kW的峰值充电功率,充电时间大约需0.5h。
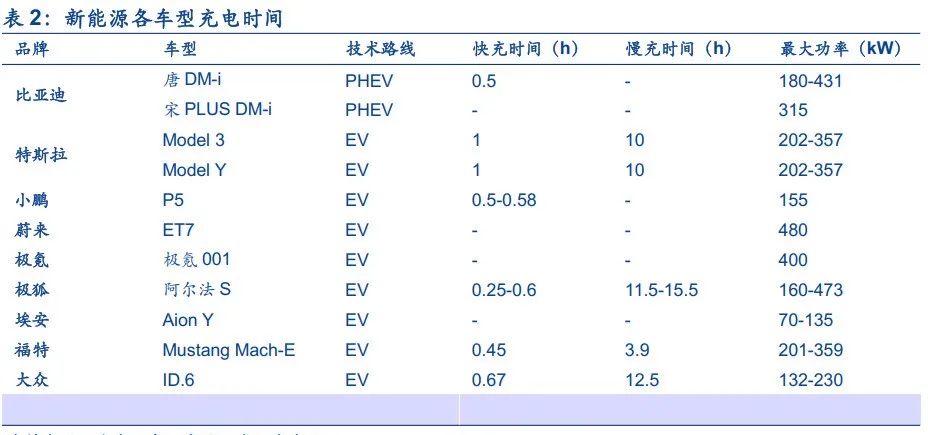
提高汽车电压平台可以大幅提升整车运行效率、缩短充电时长。电阻大小相同情况下,高电压可使电损耗减少,效率提升。2021年9月,比亚迪发布e平台3.0,有800V闪充功能,实现充电5分钟续航150公里,搭载该平台的车型有望在2022年量产;极氪001 具备 400V 和800V 两种电压架构,10%-80% SOC 充电时间仅需30分钟,充电5分钟续航可增加120 公里;北汽极狐发布极狐αS Hi 版,具备800V 充电架构,2.2C 闪充技术能实现10 分钟补充 196 公里续航的电量,30%-80%SOC 充电时间仅为 15 分钟。2021 年 10 月,小鹏汽车公布首个量产的800V 高压 SiC 平台,充电峰值电流超过600A,采用高能量密度、高充电倍率电池,充电 5 分钟最高可补充续航200 公里。
1.3. 相较于提高电流,高电压仍为未来发展趋势
根据P=UI,提升快冲效率的方向有二:提升电压,将新能源汽车的电压系统从400V升高至800V后电动车的功率提高一倍,大幅降低充电时间;提升电流,特斯拉是采用提高电流方法的代表。
高电流模式推广程度低,对热管理要求高。根据特斯拉官网,特斯拉V3超充桩在400V电压下可达到250kW的峰值充电功率。特斯拉电动车的充电时间需要30分钟左右,大电流超充的推广难度较高,由焦耳定律Q=I2RT,热量与电流的二次方成正比,大电流充电过程中产生的热量大幅增加,对汽车的散热系统有更高的要求。以特斯拉为例,特斯拉V3 超充桩峰值工作电流超过600A,故需要使用更粗的线束。此外,大电流模式的应用场景有限制,目前大电流模式仅在10%-20%SOC 进行最大功率充电,在其他区间充电功率也有明显下降。
高电压模式是车厂普遍采用的模式,除减少能耗、提高续航里程外,还有减少重量、节省空间等优点。根据焦耳定律,高电压系统下,电流变小使得整个系统的功率损耗减小,提高效率。若电流不变,汽车的电机驱动效率则会提升,从而增加续航里程、降低电池成本。高电压模式的有点还包括降低高压线束重量,同功率情况下,电压等级的提高客减少高压线束上的电流,使得线束变细,从而降低线束重量、节省安装空间。以保时捷为例,保时捷将电压平台从400V提高至800V后,实现300kW充电功率,高压线束的截面积仅为400V架构下的二分之一,线束减重4kg。小鹏也推出800V平台下的400kW快冲,充电效率可达5C,实现充电10分钟续航400公里的效果。
1.4. 400V电压平台下功率器件使用情况
与燃油车相比,新能源车对电力控制的需求提高,功率器件在新能源车中的占比远高于燃油车。在传统燃料汽车中,汽车电子主要分布于动力传动系统、车身、安全、娱乐等子系统中;而在新能源汽车中,功率器件主要集中于“三电系统”,即电池、电机和电控系统,新增 DC-DC 模块、电机控制系统、电池管理系统、高压电路等部件。新能源汽车系统架构中涉及到功率半导体应用的组件包括:电机驱动系统、OBC、 AC/DC 和 DC/DC。
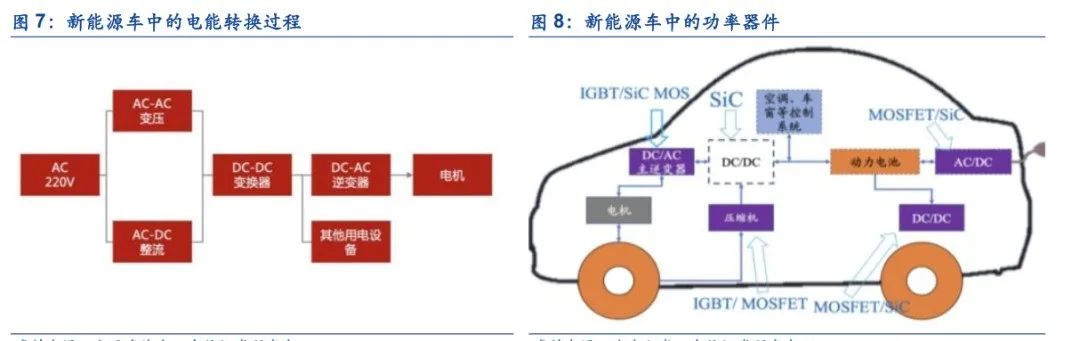
不同档次的电动车采用功率器件存在差异。根据产业调研,A00-A0级车售价集中在2-3万元,电控系统主要采用最小的MOS方案,以92V的低压单管为主,主要供应商为ST,上汽通用五菱是采用该方案的典型代表;A0-A级车,售价在10万元以下,通常采用650V的IGBT方案,低压IGBT领域目前斯达半导在国内市场的份额最大;10万-20万元的电动汽车大部分采用750V IGBT,英飞凌占据该细分市场最大的市场份额;比亚迪着力于高压1200V IGBT模组,物流车、商用车等C级车主要采用1200V方案。
主电机驱动:汽车的电机驱动系统包括传动机构、电机和逆变器。功率器件主要应用于逆变器,400V电压平台下,电机驱动系统中的逆变器主要采用硅基IGBT,约占其成本的50%。
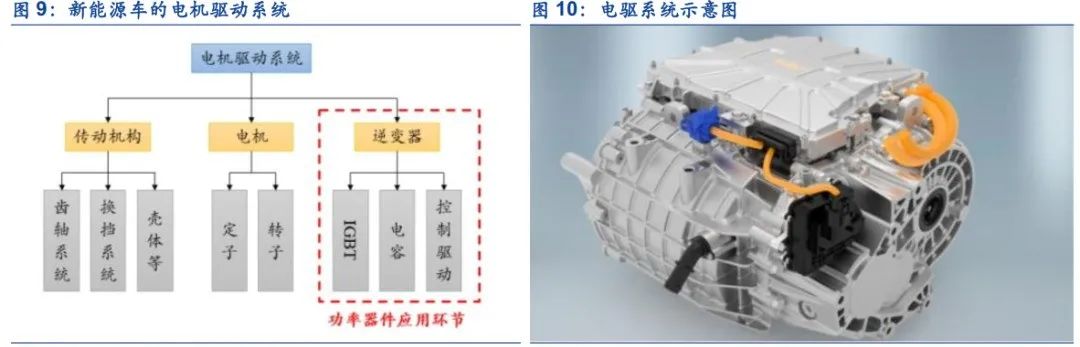
OBC(车载充电系统):车载蓄电池充电机可将来自电池子系统的DC电源转换为主驱动电机的AC电源,通常采用硅基IGBT方案,由于SiC器件可使得OBC减少能耗、改善散热情况,全球范围内汽车厂商陆续采用SiC功率器件代替硅器件。
AC/DC:车载AC/DC变换器可将高压直流电逆变成交流电来驱动电动机、空调工作,通常采用硅基IGBT方案。
DC/DC:车载DC/DC变换器可将动力电池输出的高压直流电转换为低压直流电。从车载动力电池取电,给车载12V或24V低压电池充电,并为整车提供全部的低压供电,通常采用硅基IGBT方案。
1.5. 800V电压平台下的电动车部件升级
实现 800V 电压平台,需要面对元器件重新开发、电池模组安全性能提高以及半导体器件路线改变等难题。就电池包而言,4C 以上充电倍率以及电压和电流的增大会极大的影响电池的稳定性和使用寿命,需在 BMS 和电池材料电导率上进一步改善。此外,更大的充电功率对电池系统的冷却提出较大挑战,需对发热较为集中的电芯正极区域进行针对性冷却和热管理, 保障电池在理想温度区间内工作。
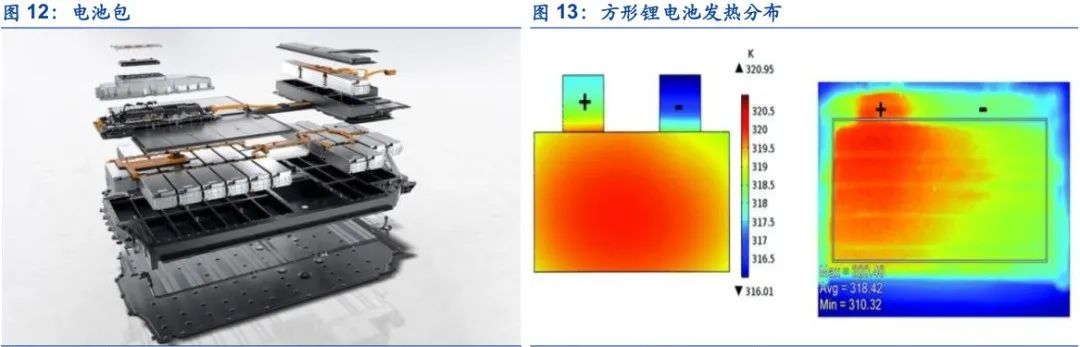
电压平台的升高要求电动车的三电系统以及空调压缩机、DC/DC、OBC等部件在800V甚至1000V的电压下正常工作,即需要各部件耐高压、耐高温。
➢ 电控:800V平台要求电机控制器采用碳化硅 MOSFET代替硅基IGBT。硅基IGBT在450V平台下耐压650V,汽车电压平台升高至800V后,要求功率半导体耐压等级达到1200V,硅基IGBT的开关/导通损耗将大幅升高。而800V下的碳化硅器件在耐压、开关频率、损耗等多个维度表现优异,高电压平台将推动碳化硅MOSFET发展。
➢ 电机:800V逆变器导致电压变化频率高,轴电流增大,轴承防腐蚀要求增加,同时,由于电压/开关频率增加,800V电机内部的绝缘/EMC防护等级要求提升。
➢ OBC+DC/DC:OBC/DCDC等功率器件集成化趋势明显。电压升高800V后,充电机OBC将不会使用目前的650V的硅基方案,变为使用碳化硅的方案;考虑高频特性,DC/DC不会使用1700V的IGBT,效率比较低。据产业调研,电压平台从400V升高至800V后,充电机70%以上的功率器件将换为碳化硅方案。
➢ 连接器+线束:平台架构从 400V 升级至 800V 要求连接器重新选型,为增加大功率快充借口,连接器数量可能增加;在同等功率条件下,电压提高,电流减小,线束材料用量更少,但对耐压、绝缘要求更高。
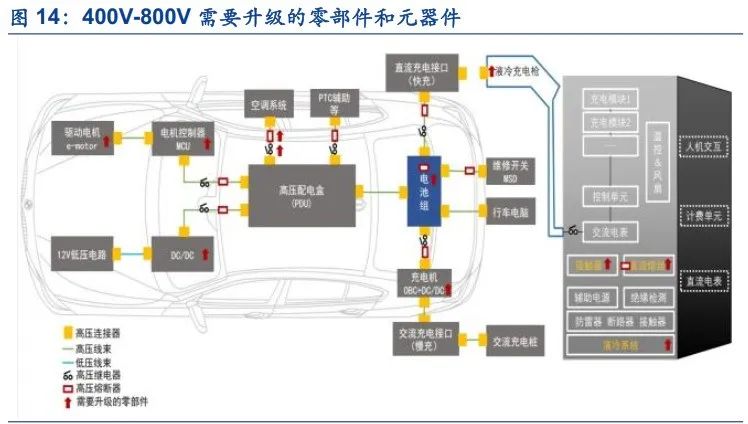
02碳化硅物理特性优良,适合制备高温、高压、高频器件
2.1. 碳化硅:第三代半导体材料,具备耐高压、高温等优点
碳化硅光电特性优越,耐高温、高压、高频,是800V电压平台下功率器件的首要选择。碳化硅属于第三代半导体材料,与前两代半导体材料相比最大的优势是较宽的禁带宽度,保证了其可击穿更高的电场强度, 适合制备耐高压、高频的功率器件。
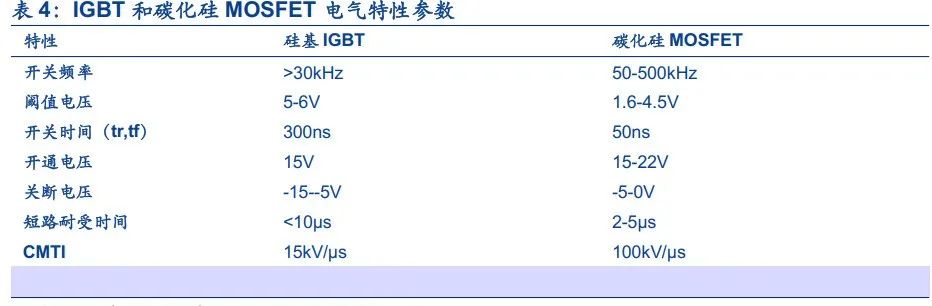
SiC适合制备高压器件。SiC的绝缘击穿场强是Si的10倍,较大的绝缘击穿场强使碳化硅能够以更高的掺杂浓度并且膜厚更薄的漂移层制作出600V~数千V 的高压功率器件。高压功率器件的电阻成分主要由该漂移层的电阻所组成,因此使用SiC 材料可以实现单位面积导通电阻非常低的高压器件。理论上当耐压相等时,SiC 在单位面积下的漂移层电阻可以降低到Si 的1/300。使用碳化硅材料,可避免硅基IGBT开关损耗大、高频驱动发热等问题。SiC 材料能够以具有快速器件结构特征的多数载流子器件(肖特基势垒二极管和MOSFET)实现高压化。
SiC可以在高温场景下应用。SiC的带隙宽度大约为Si的3倍,可以在较宽范围内实现必要的P 型、N 型控制,超越Si器件的物理极限。因此,SiC可以在高温条件下稳定工作。根据罗姆官方《SiC功率器件-模块应用笔记》显示,目前由于受到封装的耐热可靠性的制约,只保证到150℃~175℃,但是随着封装技术的发展,将来也可能达到200℃以上的保证温度。
2.2. 碳化硅二极管可替换快速恢复二极管,在高频高压情况下表现优异
碳化硅肖特基势垒二极管具有恢复损耗小、开关电源高频、减小元件体积、降低噪音等优点。SiC 能够以具有 Si 快速器件结构特征的肖特基势垒二极管(SBD)结构,制作出 1200V 以上的高耐压二极管(Si SBD 的最高耐压为 200V 左右)。
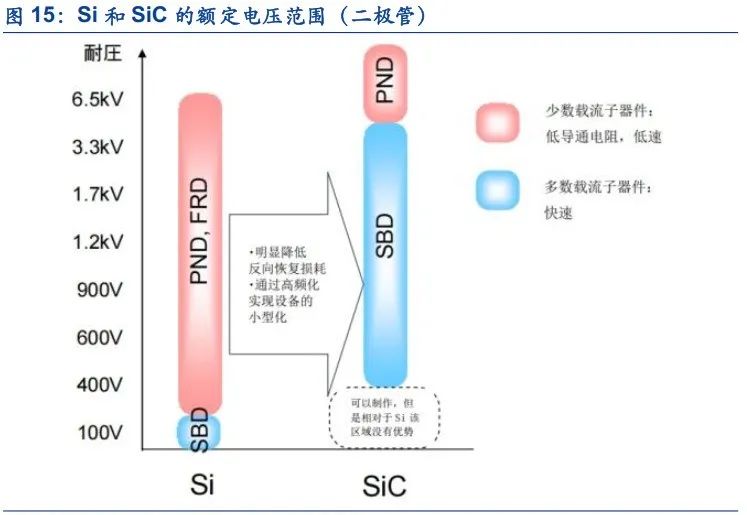
碳化硅肖特基二极管的正向特性使其适合并联使用。SiC SBD的开启电压与 Si FRD为同等水平, 都小于 1V。开启电压是由肖特基势垒的势垒高度所决定的,若降低 VF值,则需要减薄肖特基势垒的高度, 但这会使器件反向偏压时的漏电流增大。“降低开启电压” 和“控制漏电流” 存在折中关系。SiC SBD 的温度特性与 Si FRD 不同,当温度升高时,随着工作电阻的增加,VF值也上升,不易发生热失控,因此 SiC SBD 更适合并联使用。同等温度条件下,IF=10A 时碳化硅与硅二极管正向导通电压比对,碳化硅肖特基二极管的导通压降为1.5V, 硅快速恢复二极管的导通压降为 1.7V, 碳化硅材料性能好于硅材料。
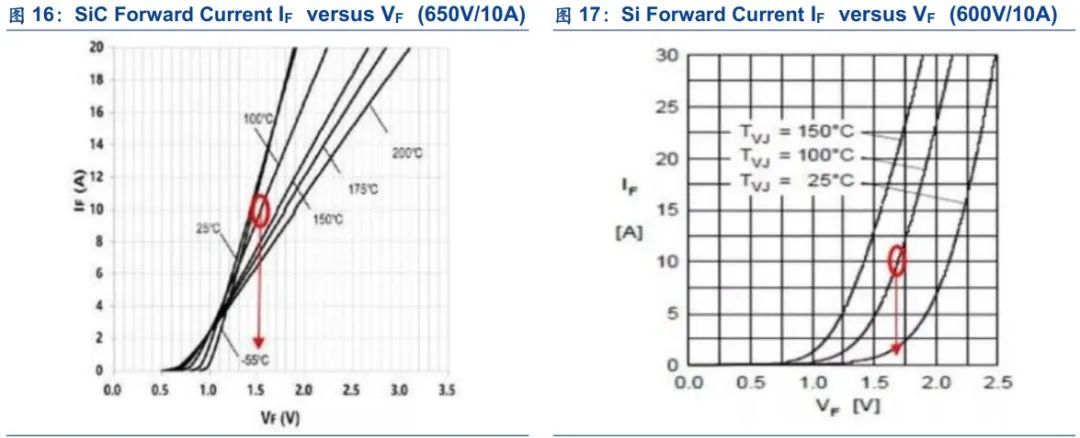
由于碳化硅肖特基二极管的恢复特性,SiC SBD可大幅减少损耗,稳定实现器件的正反切换。硅快速恢复二极管在从正向导通状态切换到反向截止状态的瞬间,会产生极大的反向瞬态冲击电流,器件从正压导通转向反压截止偏压状态。此过程时间长,电流大,会产生较大的损耗,当器件正向电流越大及温度越高时,恢复时间和恢复电流就越大,损耗也就越大。而碳化硅肖特基二极管是一种多数载流子导电器件(单极性器件),在工作过程中不会发生少数载流子存储的现象,也不会产生过大的正反向切换瞬态冲击电流,只有结电容放电的小电流,因此碳化硅肖特基二极管的开关损耗比硅快速恢复二极管更低。根据ROHM测试结果,无论使用温度和正向电流如何改变,SiC的反向恢复电流都得到了大幅减小。
2.3. 碳化硅MOSFET在性能上优于IGBT
硅基 IGBT 与 SiC MOSFET 在电气参数上存在较大差异。
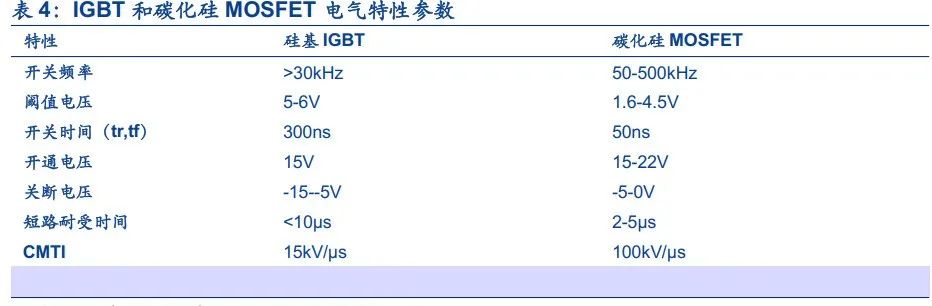
与硅基IGBT对比,SiC MOSFET不仅耐压性更好,而且可有效减少开关损耗。虽然IGBT器件可应用于600V以上的电压场景,但是由于少数载流子的积聚,在关断时会产生拖尾电流,产生较大的开关损耗。而SiC器件的漂移层电阻比 Si 器件的要小,不必使用电导率调制,就能够以具有快速器件结构特征的 MOSFET 同时实现高耐压和低导通电阻。采用SiC MOSFET 可以达到开关损耗减小、散热器小型化的效果。并且,SiC MOSFET可实现IGBT无法进行的高频驱动,有助于实现被动器件的小型化。
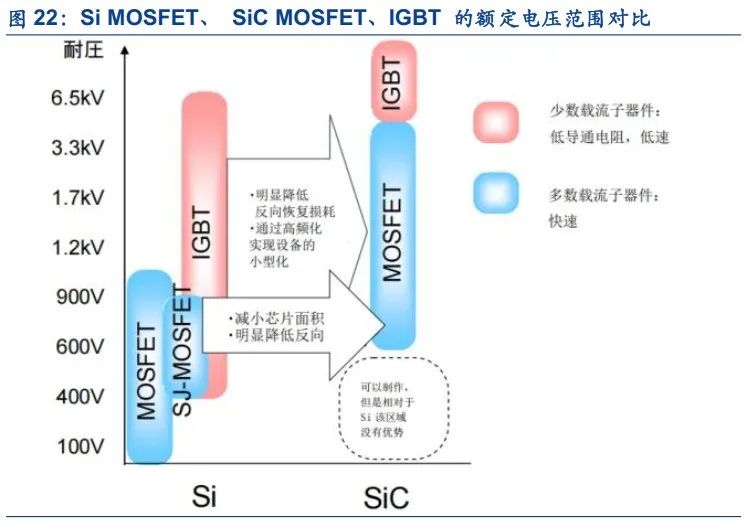
SiC MOSFET可以在更宽的电流范围和温度范围内稳定工作。SiCMOSFET 不存在像 IGBT 那样的开启电压,因此从小电流到大电流的宽电流范围内都能够实现较低的导通损耗。另外,Si MOSFET 在 150℃时的导通电阻会上升为室温时的2倍以上,但是 SiCMOSFET 的上升率相对较低,因此热设计更加容易、高温下也能够实现较低的导通电阻。
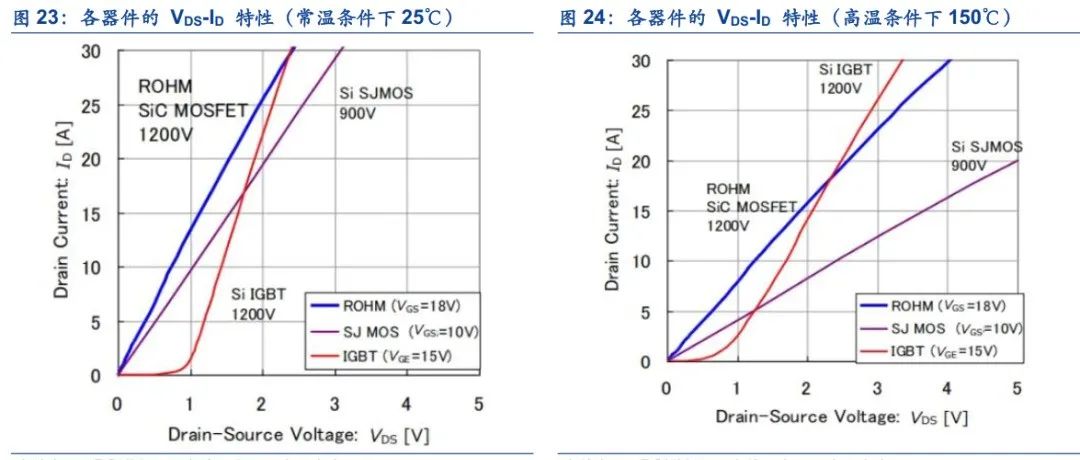
SiC MOSFET在温度升高时,其导通电阻上升率低于Si MOSFET和IGBT,耐高温程度高。这是因为在器件的导通电阻中,漂移层电阻的占比较小,其他电阻成分的占比较大。沟道电阻 RCH 在高温时会稍微下降,n+基板的电阻 RSUB 几乎没有温度依存性。650V 产品的漂移层电阻成分较小,因此温度系数非常小;1200V 产品的漂移层会变厚,电阻成分较大,SiC MOSFET的优势更加显著。
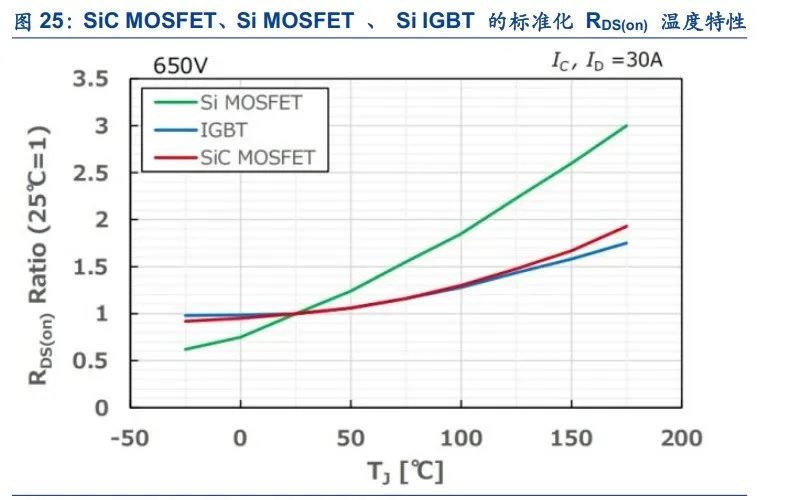
03碳化硅在高压车型渗透率提升趋势明显
3.1. 高压车型不断推出,碳化硅渗透趋势明显
800V 方案中快充功率可以达到 400-500kW, 如小鹏 G9 充电十分钟续航 400 公里。 目前市面新能源汽车主流电压平台介于 400V-500V 之间,理想 ONE 、小鹏汽车和蔚来汽车的换电方案都在尝试解决里程焦虑和充电速度慢的问题,未来 800V 快充趋势明显。
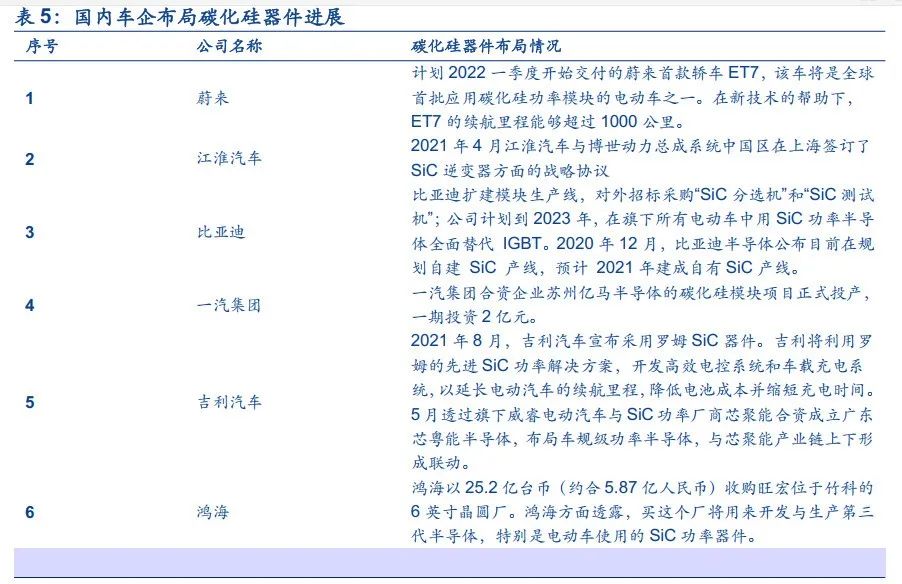
搭载高压架构的车型逐渐趋向经济型下沉,推动碳化硅市场渗透率提升。碳化硅在高压方面有先天性能优势,只要车企用的是高压、650V以上的电池,电压越大,碳化硅的优势越明显;在车的续航能力方面,续航要求越高,碳化硅越有优势。就乘用车而言,300km以上续航,碳化硅具备优势,电池需求越大,碳化硅优势越明显。目前在高续航和快充的市场需求下,新能源汽车由400V向800V架构升级趋势已成大局,未来随着电池、器件车成本的降低,经济型电动车也有望搭载高压方案。随着碳化硅尺寸的增大、产业链的完善,碳化硅衬底成本下降,碳化硅器件会逐渐扩展至中低端车市场,SiC市场空间将被进一步打开。据CASA预测,到2025年新能源汽车中SiC 功率半导体市场预计将以38%的年复合增长率增长。
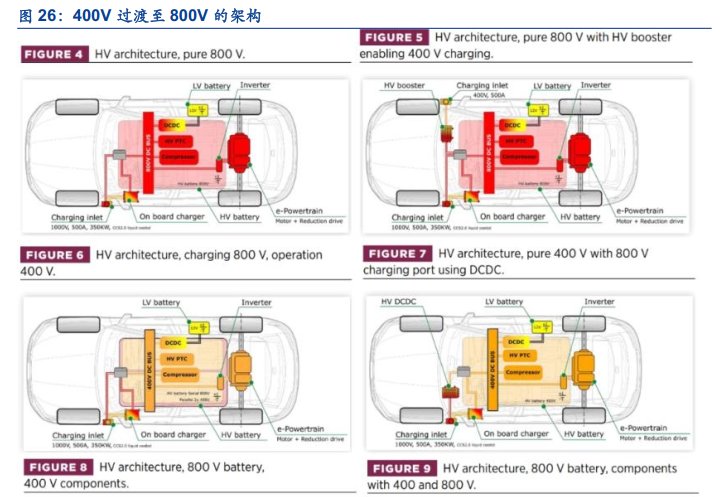
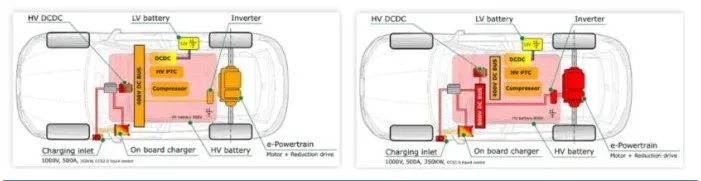
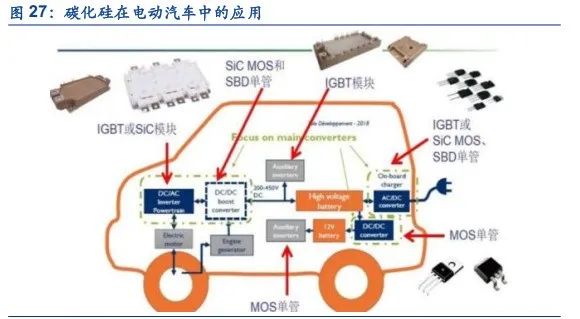
碳化硅方案能提升电驱系统性能,减小器件体积,提高30%左右功率密度:碳化硅功率器件主要应用于新能源汽车电机驱动系统中的电机控制器。2020年比亚迪汉EV车型电机控制器使用其自主研发制造的SiC MOSFET控制模块,使得其可以在更高的电压平台下工作,从而减少设备电阻损失。比亚迪汉在电力电子系统实现了更小的体积,同功率情况下,体积缩小30%,即功率密度也将提升30%左右,功率达到了更高的363kW;车辆的加速性能提升明显,实现了3.9s内0-100公里的加速;延长汽车的续航里程至600km以上;这均得益于碳化硅低开关、耐高压、耐高温、导热率高的优良特性。
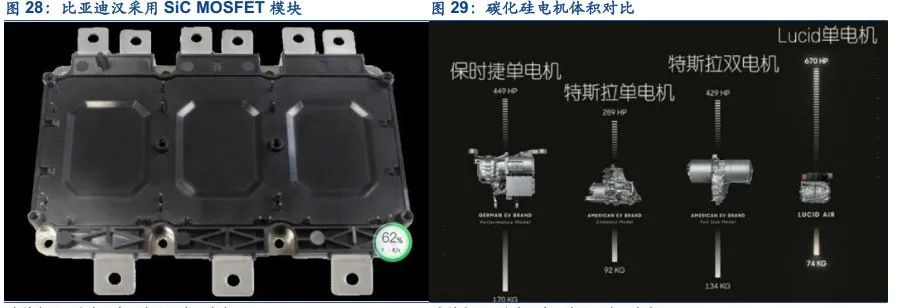
碳化硅器件可使OBC体积减少60%,能量损耗减少30%:根据Wolfspeed数据,OBC采用碳化硅器件与硅器件相比,其体积可减少60%,并减少30%的能量损耗,SiC的峰值效率可以达到97%,比硅器件提升2%,BOM成本将降低15%。据产业调研,目前OBC市场单价在300元,即单件成本可降低45元左右。在400V系统相同充电速度下,采用SiC方案充电量将实现翻倍。目前,全球已有超过20 家汽车厂商在车载充电系统中使用碳化硅功率器件,电压升高至800V以后,OBC将采用1200V的碳化硅方案。据Wolfspeed 2021年12月7日化合物半导体大会观点,现在用的650V的硅方案将逐渐淡出市场,在2022年11kW将取代6.6kW成为主流的功率等级。据产业调研,每一个11kW的SiCOBC约用到10颗碳化硅MOS,单价7美金,合计70美金,假设300万辆新能源车采用,即对应2.1亿美金市场。
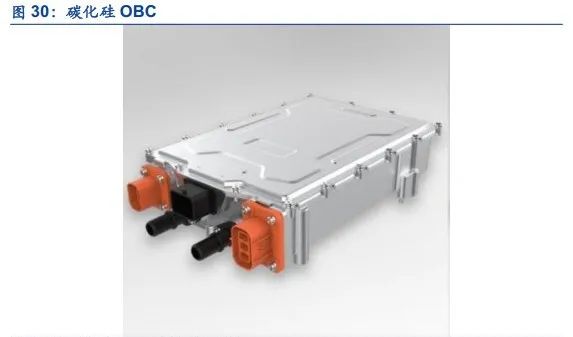
碳化硅电源转换系统(车载 DC/DC)可简化设备结构,减小体积:电动车上的电池电压一般比较高,400v或者800v,需要用DC/DC部件将其转换成12v,采用碳化硅器件,设备温度积累减少,加之材料本身高导热率、耐高温的特点,散热设备可以简化,从而减小变压器体积。
碳化硅充电桩充电效率可由95%提升至97%,电路所占的面积减少25%到30%:SiC的高开关速度保证了快速充电器的充电速度。用SiC MOSFET设计的两级拓扑比硅AC/DC转换器更简单、更小、更高效,同时可减少元件数量,基于SiC的设计中有6个有源元件,而基于Si MOSFET的设计中有12个有源元件,两级IGBT设计中有18个有源元件。在尺寸方面,基于SiC的电路所占的面积减少了25%到30%。
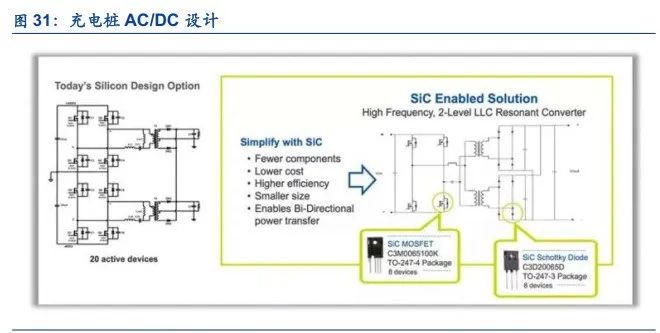
据产业调研,采用碳化硅方案,在电池容量相同的情况下,其续航里程可提高5-10%;同理,在续航里程相同的情况下,电池容量可以减少5-10%。同等电池情况下,明显增加续航历程,假设原车600KM里程,提升7%,意味着提升有效里程到642KM。整合在电机能量密度上的提升,以及电路面积等的优化,如果为了提升里程,充分利用有效面积,可以进一步增加电池容量。
3.2. 使用碳化硅并未增加整车成本
整车厂更加关注整车成本变化而非仅功率器件成本变化,使用碳化硅方案并未增加整车成本。据产业调研, 在中高端车型单个电驱硅基 IGBT 价值量约 1000-1500 元,按中高端车型两个电驱来计算,总价值量约 2000-3000 元;OBC 功率器件成本约 300 元,车载空调功率器件成本约 100 元,其它如助力转向等约 300 元,合计硅基功率器件用量约 2700-3700 元。目前碳化硅方案成本是硅基 IGBT 的 3 倍左右,使用碳化硅方案总成本增加 5400-7400 元左右。
动力电池占纯电动汽车总成本的40%-50%,假设某中高端电动车价格为20万元,电池成本约8-10万元,假设碳化硅方案提升里程5%计算,相同性能的产品条件下,仅电池系统就为总成本节省4000元-5000元。
根据戴姆勒奔驰研究,800V高压平台下采用碳化硅模块较Si基IGBT 模块整车能降低7.6%的能耗,冷却系统将节约1000元左右。
高压平台碳化硅方案下,线路电流减小,器件更紧凑,对电缆的需求降低,综合计算最终使用碳化硅并未增加整车成本。未来碳化硅规模化量产之后成本会更低,将为整车成本创造更大空间。

04新能源车用碳化硅市场预测
4.1. 碳化硅成本下降趋势可期
衬底制备是碳化硅器件核心难点, 衬底工艺进步是成本下降主攻方向。新能源汽车中使用的碳化硅器件衬底主要以导电型碳化硅衬底为主, 目前, 以 6 英寸占主流, 8 英寸衬底开始研发;半绝缘碳化硅衬底以 4 英寸为主, 目前逐渐向 6 英寸衬底发展。6 英寸衬底面积为 4 英寸衬底的 2.25 倍, 相同的晶体制备时间内衬底面积的倍数提升带来衬底成本的大幅降低。与此同时, 单片衬底上制备的芯片数量随着衬底尺寸增大而增多, 单位芯片的成本也即随之降低, 因此碳化硅衬底正在不断向大尺寸的方向发展。
成本下降方向:结合目前成本情况及技术发展方向,碳化硅衬底的成本可以通过做大尺寸、提高材料使用效率和提高良率等方式下降。
➢ 做大尺寸:衬底的尺寸越大,边缘的浪费就越小,有利于进一步降低芯片的成本。6英寸衬底面积为4英寸衬底的2.25倍,相同的晶体制备时间内衬底面积的倍数提升带来衬底成本的大幅降低,与此同时,单片衬底上制备的芯片数量随着衬底尺寸增大而增多,单位芯片的成本也即随之降低。
➢ 提高材料使用效率:由于技术限制,长晶时间很难缩短,而单位时间内长晶越厚成本越低,因此可以设法增加晶锭厚度;另一方面,目前的切割工艺很容易造成浪费,可以通过激光切割或其他技术手段减少切割损耗。
➢提高良率:以山东天岳为例,碳化硅衬底产品良率逐年提升。招股书披露,天岳在衬底制造核心生产环节的晶棒良品率由 2018 年的 41.00%上升至 2020 年的 50.73%,衬底良率总体保持在70%以上。随着工艺的逐步提升,碳化硅衬底生产成本将得到进一步下降。
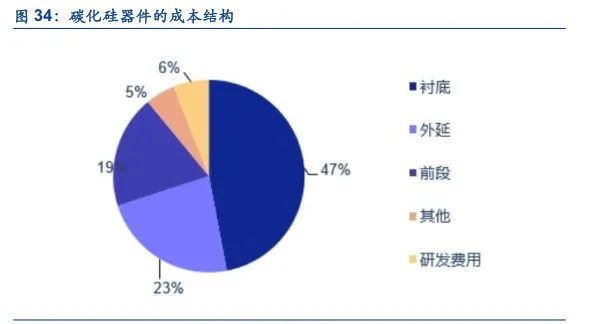
4.2. 800V电压平台大力带动碳化硅市场
新能源汽车碳化硅功率器件市场规模推算:根据中国汽车工业协会数据,我国新能源汽车销量由2015 年的33.1 万辆增至2019 年的120.6 万辆,复合增长率达38%,2021年前11个月新能源车累计产量突破300万辆,销量接近300万辆。中汽协预计2021年全年中国新能源汽车销量有望达到340万辆。IDC预测中国新能源车销量至2025年的年均复合增长率(CAGR)将达到36.1%。目前比亚迪、吉利极氪、小鹏汽车、广汽埃安、理想汽车、北汽极狐、岚图等车企相继投资800V电压架构产品,合理假设2025年碳化硅器件渗透率30%,年均价格降幅10%,仅碳化硅功率器件在电动车市场空间达220亿元。
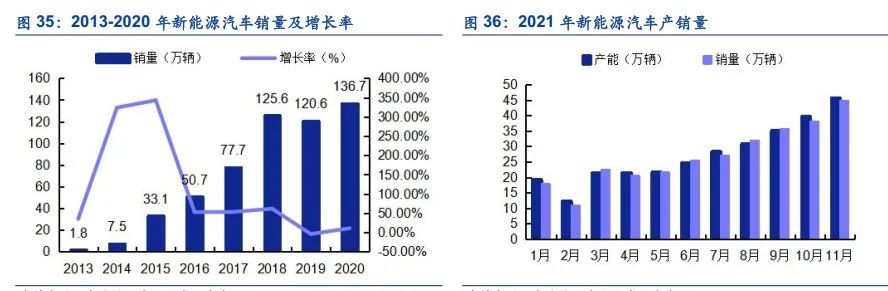
05目前难点
(1)新能源车发展不及预期风险。新能源车为碳化硅功率器件带来巨大的增量市场。若新能源车销量不及预期, SiC 的发展会随之受到影响。
(2)800V 架构产品量产不及预期风险。碳化硅器件优势在高电压平台架构下发挥明显,若800V 车型量产不及预期,SiC 渗透率会受到影响。
(3)SiC 技术难度大, 产品研发、 量产不及预期风险。国外龙头企业大力布局 SiC 领域研发,若国内企业产品研发失败、产能不足,无法满足下游应用市场要求,对市场前景会产生不利影响。
(4) SiC 成本高居不下, SiC 渗透率不及预期风险。目前碳化硅功率器件的价格仍数倍于硅基器件, 下游应用领域仍需平衡碳化硅器件的高价格与因碳化硅器件的优越性能带来的综合成本下降之间的关系, 一定程度上限制了碳化硅器件的渗透率。若碳化硅制造成本无法下降,对市场应用进展产生不利影响。
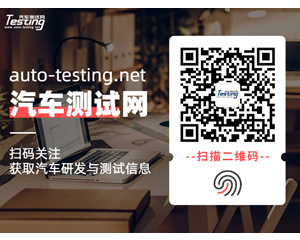
最新资讯
-
商用车及工程机械行业专场:NVH 及语音音频
2025-08-01 17:12
-
理想i8和重卡对撞测试引争议,东风柳汽发声
2025-08-01 15:52
-
艾德克斯IT-N2100 系列太阳能阵列模拟器
2025-08-01 15:43
-
ITECH重磅发布IT2705直流电源分析仪,重构
2025-08-01 15:34
-
现代汽车新一代混合动力系统:以技术革新引
2025-08-01 15:32