汽车试验:轿车轮胎耐撞击性能评价
轮胎鼓包是轮胎损坏中较为常见的一种现象,也是轮胎投诉较多的问题之一,轮胎鼓包主要出现在轿车轮胎中。轮胎鼓包现象一般是在车辆行驶过程中撞击路面障碍物或凹坑以及轮胎撞击马路牙等情况时,轮胎由于受力造成不可逆的伤害。轮胎鼓包后存在爆胎的风险,一旦车主未及时发现,或发现后未及时更换轮胎,随时可能发生爆胎,从而导致严重的安全事故。
轮胎鼓包现象在世界范围普遍存在。在我国,近年来随着道路交通的快速发展以及汽车保有量的不断增长,轮胎鼓包一直在轮胎质量问题中存在,但目前国内外尚无相关的标准法规对轮胎鼓包问题进行评价。在此情况下,从我国实际国情出发,借鉴国际经验,并进行了大量的标准验证试验,积累原始数据,完成了《轿车轮胎耐撞击性能评价》,并力求使得标准中相关指标更加科学合理。
该标准的发布实现了我国对轿车轮胎耐撞击性能评价从无到有的质的飞跃,对提高我国轮胎耐撞击性能整体水平具有积极的推动作用。标准将为主机厂在轮胎耐撞击性能方面选择配套轮胎以及轮胎供应商生产和研发时提供技术依据,同时还有助于消费者在轮胎替换时根据自身需求和不同种类轮胎的特性合理选择轮胎。
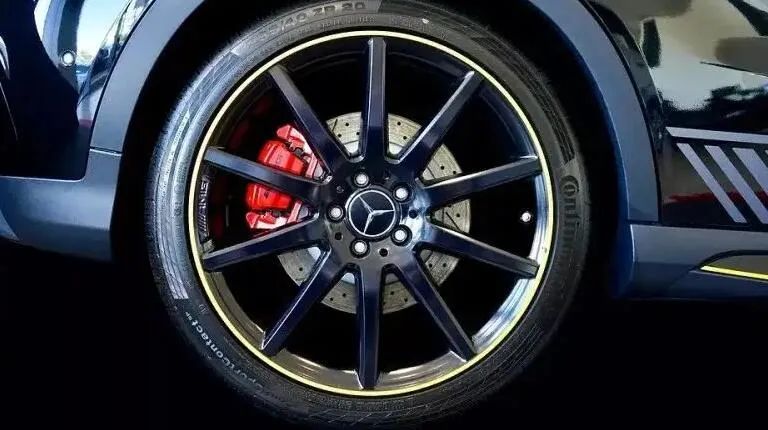
1 范围
本标准规定了摆锤法轿车轮胎耐撞击性能评价要求、试验方法、判定规则和试验报告。
本标准适用于新的30系列至65系列充气无内胎轿车轮胎,不适用于缺气保用轮胎和仅供临时使用的备用轮胎。
2 规范性引用文件
下列文件对于本文件的应用是必不可少的。凡是注日期的引用文件,仅注日期的版本适用于本文件。凡是不注日期的引用文件,其最新版本(包括所有的修改单)适用于本文件。
GB/T2978 轿车轮胎规格、尺寸、气压与负荷GB/T3487 乘用车轮辆规格系列GB/T6326 轮胎术语及其定义GB/T8170 数值修约规则与极限数值的表示和判定GB/T30195 汽车轮胎耐撞击性能试验方法HG/T2177 轮胎外观质量
3 术语和定义
GB/T6326和GB/T30195界定的以及下列术语和定义适用于本文件。
3.1 撞击锤角度striker angle
撞击锤中心平面和撞击锤前端曲面的交线与车轮中心平面的夹角,如图1a)所示。
3.2 外倾角camber angle;CA
撞击锤角度在通过车轮旋转轴的水平面上的投影,如图1b)所示。
3.3 侧偏角slip angle;SA
撞击锤角度在通过车轮旋转轴的铅垂面上的投影,如图1c)所示。
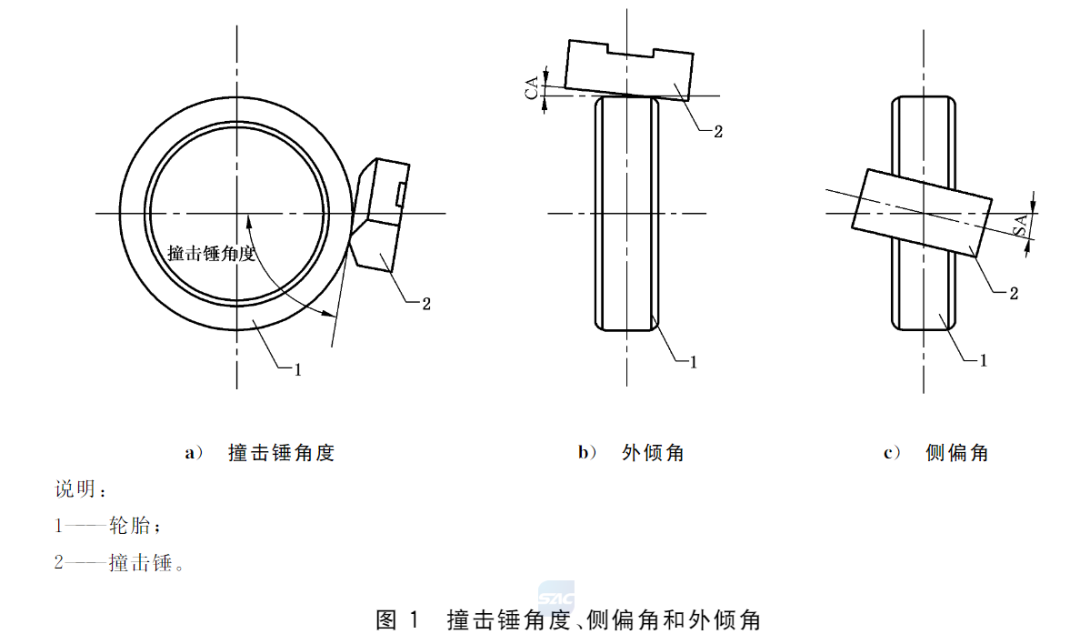
3.4 撞击能量impact energy
E撞击锤从撞击高度或撞击角度落下撞击轮胎瞬间时的动能。
3.5 鼓包impact bulge
轮胎受到撞击导致轮胎胎侧异常起鼓的现象。
3.6 漏气air leakage
轮胎受到撞击导致轮胎气压明显持续下降的现象。
3.7 鼓包高度impact bulge height
Hb轮胎受到撞击后鼓起的高度。
3.8 轮胎耐撞击因子robustness factor
f轮胎耐撞击性能的评价指标。
3.9 鼓包破坏能impact bulge energy
Ebu撞击锤撞击轮胎引起轮胎鼓包或漏气时的撞击能量。
3.10 钢制轮辋machined steel rim
通过机加工制作,仅用于室内试验,且轮廓曲线符合GB/T3487规定的钢质材料轮辋。
4 评价要求
4.1 试验轮胎的耐撞击因子应不小于表1的规定。

4.2 将表1规定的轮胎耐撞击因子(f)代入式(1),计算得出试验轮胎应通过的最小鼓包破坏能(Ebu min) , 并按GB/T 8170的规定修约到个位整数。
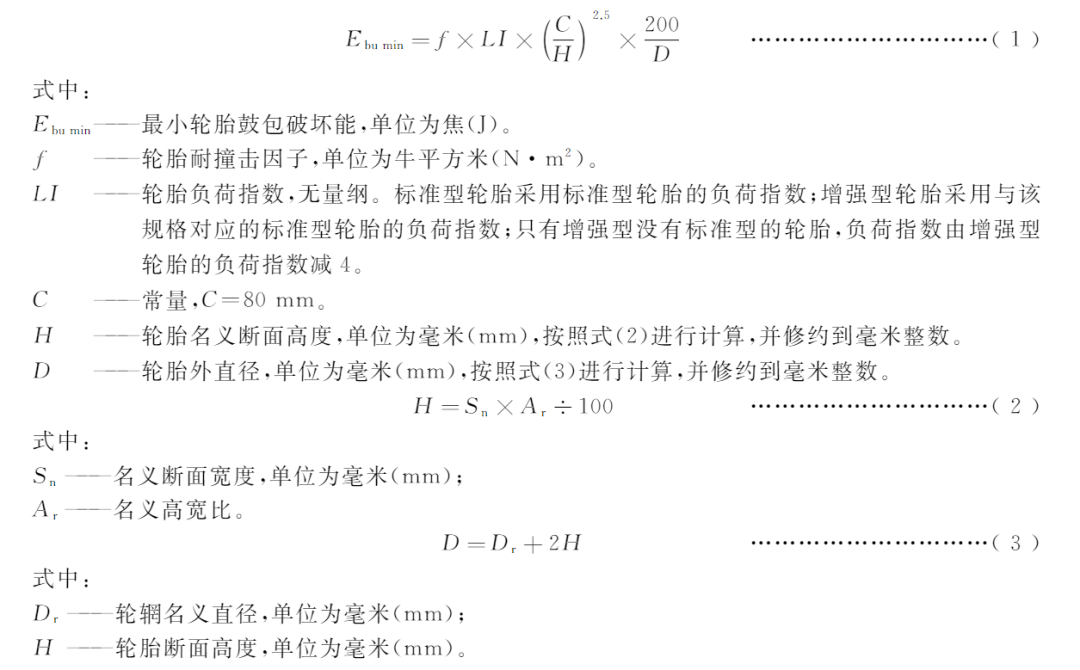
5 试验方法
5.1 设备和仪器
5.1.1 撞击试验设备
撞击试验设备的撞击锤、撞击锤支架、撞击锤组合件应符合附录A的规定,其他应符合GB/T 30195的规定。
5.1.2 鼓包测量仪
鼓包测量仪由百分表和支架组成,具体参见附录B。
5.1.3 充气压力表/气压传感器
手持充气压力表气压传感器, 精度为士5kPa。
5.1.4 图像记录设备
试验中出现的鼓包或漏气现象应采用彩色、清晰、可存储的图像记录设备进行记录。
5.2 试验条件及试验准备
5.2.1 试验轮胎在硫化后应放置24h以上,其外观质量应符合HG/T 2177的要求。
5.2.2 试验环境温度为20℃~30℃。
5.2.3 试验轮辋应为轿车轮胎耐撞击性能试验专用钢制轮辋,其规格型号应与GB/T 2978中规定的测量轮辆一致;装配柔性轮的车辆所使用的轮胎应使用与车辆要求一致的柔性轮辆进行试验,并在试验报告中加以说明。
5.2.4 将试验轮胎安装在5.2.3规定的试验轮辆上, 充人200kPa气压。安装轮胎时, 可使用润滑剂。
5.2.5 充气后的轮胎轮组合体应在试验环境温度下放置3h以上。
5.2.6 沿轮胎圆周方向确定5个大致等间距分布的试验点,并逐一做标记、编序号。
5.2.7 轮胎耐撞击性能试验机的撞击锤角度固定在外倾角6°,侧偏角0°,偏差为±0.5°。
5.3 试验程序
5.3.1 将放置后的试验轮胎气压重新调整到5.2.4规定的气压, 偏差应不超过±2kPa。如果放置后的试验轮胎气压有不正常的损失,应观察试验轮胎和轮辆状况,重新准备试验轮胎。
5.3.2 将校正气压后的试验轮胎轮组合体按GB/T30195的规定安装在试验装置上,并将轮辆进行锁定,使其在周向上不能转动,按标记序号逐点进行试验。
5.3.3 将摆杆调整到自由悬挂状态,使轮胎旋转中心与撞击锤顶部处于同一水平线上,沿水平方向横向调整轮胎位置,使轮胎胎肩触及撞击锤中部。摆杆因轮胎触及撞击锤产生的摆杆角位移应不超过0.1°。
5.3.4 提升撞击锤使其撞击能量等于4.2规定的最小鼓包破坏能,然后锁定摆杆。
5.3.5 使撞击锤从锁定位置自由下落,撞击试验轮胎。撞击锤反弹时,由锁定装置锁定摆杆,防止二次撞击。再将轮胎后退,撞击锤缓缓下落到自由悬垂状态。
5.3.6 每个试验点撞击后3min, 使用5.1.2规定的鼓包测量仪对该撞击点附近进行检查, 并记录检查结果;用5.1.3规定的充气压力表/气压传感器测量轮胎气压并记录结果;用5.1.4规定的图像记录设备对撞击部位出现的鼓包或裂口等受损情况进行记录。
5.3.7 轮胎如出现漏气或3min内气压损失超过5.2.4规定气压的5%, 应检查轮胎和轮辋。如明显可见因轮辆受损而引起的漏气,按5.3.10的规定进行处理。如明显可见因轮胎受损开裂而引起的漏气,应终止试验,并用5.1.4规定的图像记录设备对漏气的裂口位置进行记录。若轮胎受损和轮辆受损均不明显,则宜在撞击点做标记后卸下试验轮胎轮辑组合体,检查轮胎;若轮胎检查出受损,应终止试验,用5.1.4规定的图像记录设备记录受损位置;若轮胎未检查出受损,重新装配(允许更换轮辆)后按5.2.4规定的气压充气, 充气后15min, 重新检查轮胎是否开裂、测量气压和鼓包高度。
5.3.8 每次进入下一个试验点进行撞击前,应将试验轮胎气压重新调整到5.2.4 规定的气压(偏差应不超过±2kPa) , 同时检查撞击锤的紧固螺栓是否松动。
5.3.9 如果每个撞击点的鼓包高度均小于1mm, 应静置30min, 再次检查鼓包高度。
5.3.10 试验过程中如轮辆因撞击受损,应更换轮辆重新装配轮胎,按5.2.4的规定的气压充气,充气后15min, 重新检查轮胎是否开裂、测量气压和鼓包高度。
6 判定规则
被测试轮胎按5.3.1~5.3.10要求完成试验后,未出现下列情况之一的,判定为“通过”,否则判定为“未通过”:
a) 任意一个撞击点因轮胎受损出现漏气或3min内气压损失超过5.2.4规定气压的5%;
b) 任意一个撞击点,试验过程或试验结束后外观检查存在明显可见的脱层、崩花、接头裂开、龟裂或帘布层露出的;
c) 任意一个撞击点,试验过程中轮辆因撞击受损出现漏气,按5.3.10规定更换轮辋后充气过程中轮胎持续漏气, 或充气后15min检查气压损失超过5.2.4规定气压的5%或出现裂口或鼓包大于或等于1mm的;
d) 任意一个撞击点出现鼓包高度大于或等于1mm的;
e) 每个撞击点的鼓包高度均小于1mm, 但按5.3.9规定静置30min后, 任何一个出现鼓包高度大于或等于1mm的。
7 试验报告
试验报告宜包括以下内容:
a) 试验轮胎制造商名称、商标、规格、生产编号;
b) 试验轮胎负荷指数、负荷能力、速度符号、材料结构等;
c) 试验轮辋规格;
d) 实验室环境温度;
e) 试验标准编号、试验日期;
f) 试验气压;
g) 耐撞击试验轮胎各试验点的鼓包高度(含0mm)、耐撞击因子f和撞击能量;
h) 轮胎各试验点撞击后的气压,出现外观异常、鼓包、漏气时的照片;
i) 试验过程的其他意外情况;
j) 评价结果。
附 录 A(规范性附录)撞击锤、撞击锤支架和撞击锤组合体
A.1 撞击锤尺寸见图A.1。
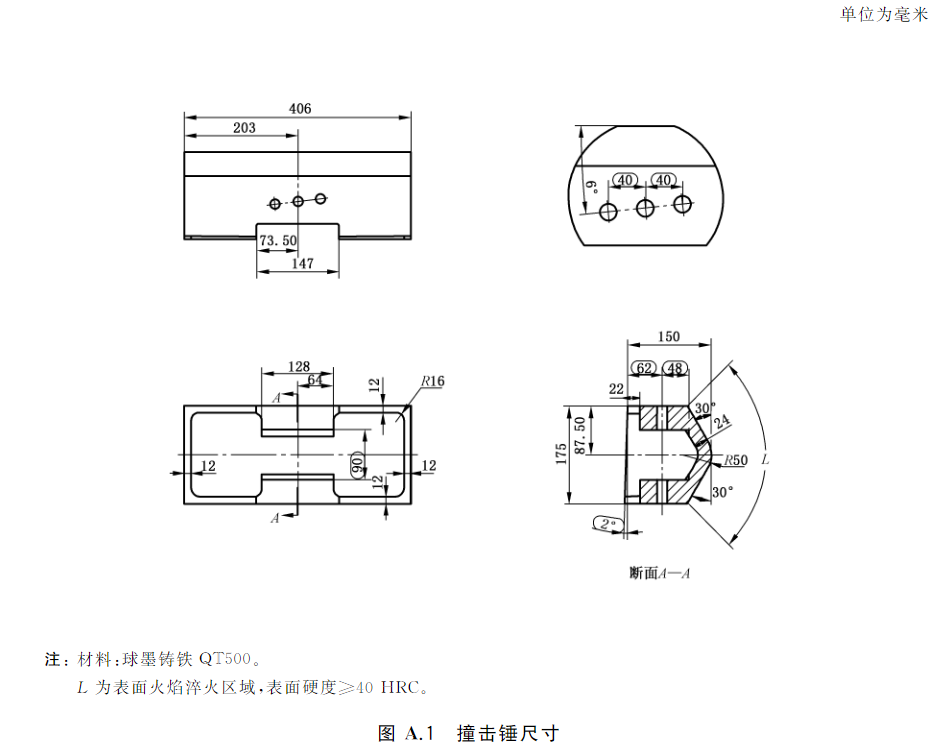
A.2 撞击锤支架尺寸见图A.2。
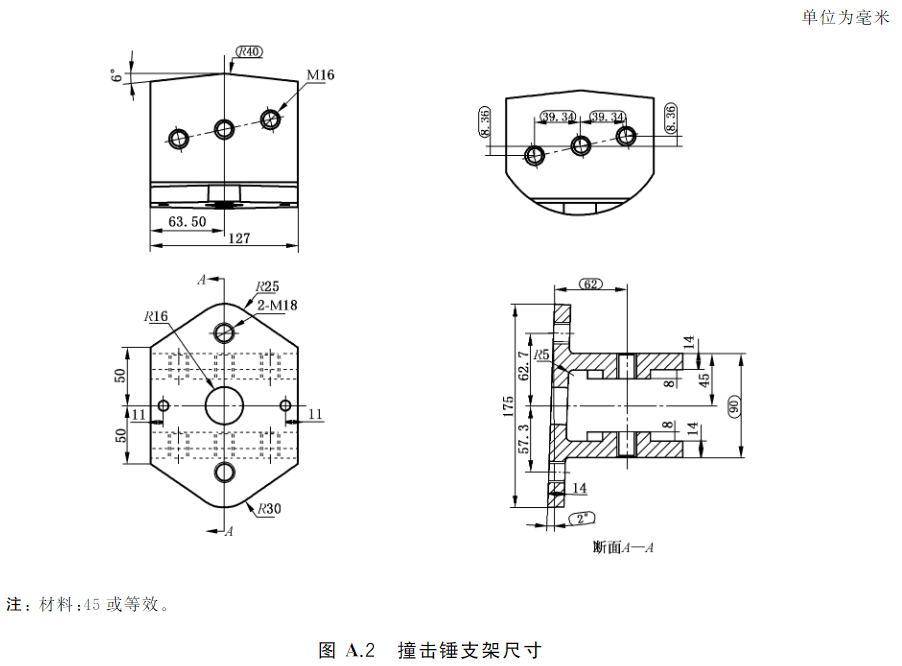
A.3 撞击锤组合体见图A.3。
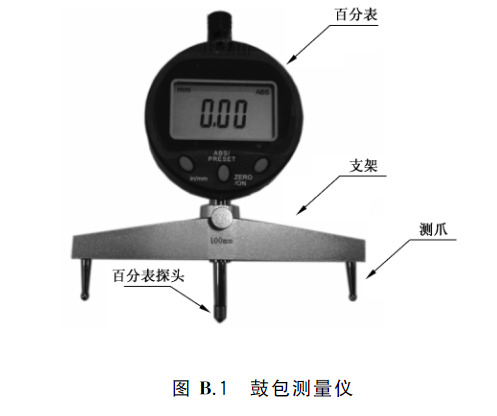
附 录 B(资料性附录)鼓包测量仪
B.1 组成
鼓包测量仪包括百分表(一级)和支架,示意图见图B.1。
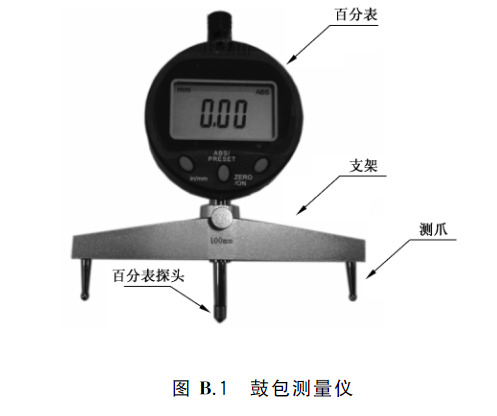
B.2 校正
使用鼓包测量仪前在撞击位置做好标识,将其探测头与标识位置对齐并校正(图B.2),探头和测爪垂直于轮胎表面。
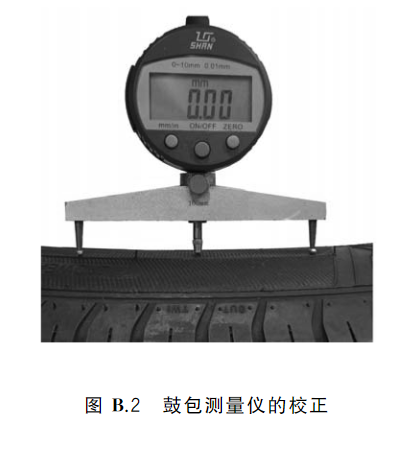
B.3 鼓包测量
轮胎受撞击后,目视发现有或不确定有鼓包的,使用鼓包测量仪对鼓包位置进行检查,见图B.3。
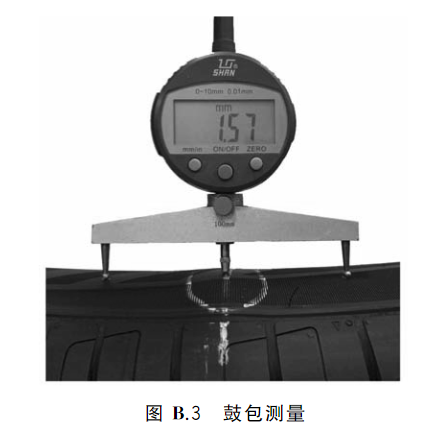
B.4 量程及尺寸要求
百分表量程:10.00mm。测爪间距离见图B.4。
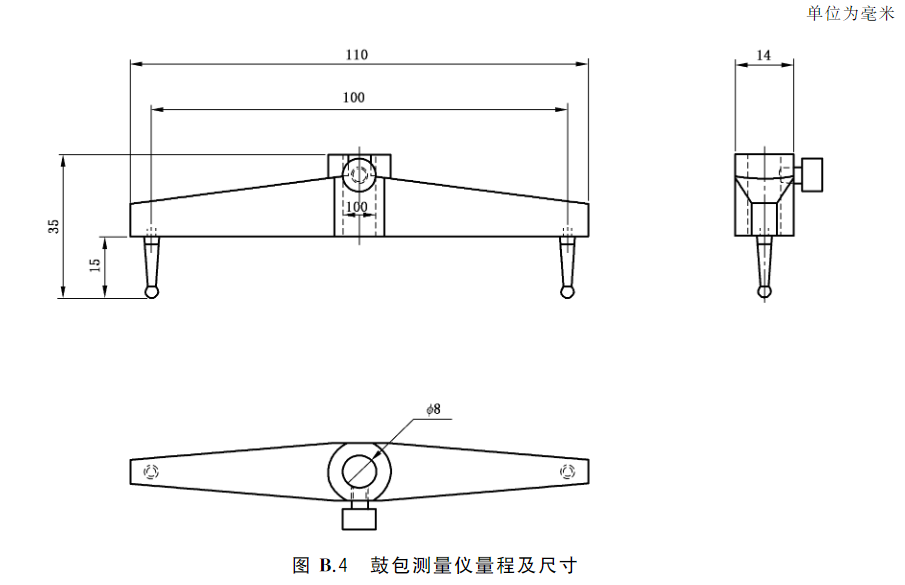
整理:汽车测试网
- 下一篇:整车性能试验验证
- 上一篇:汽车风噪声及抖振主动控制综述
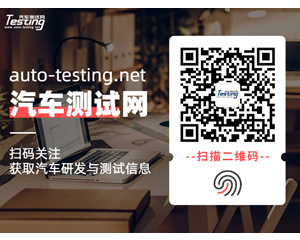
最新资讯
-
商用车及工程机械行业专场:NVH 及语音音频
2025-08-01 17:12
-
理想i8和重卡对撞测试引争议,东风柳汽发声
2025-08-01 15:52
-
艾德克斯IT-N2100 系列太阳能阵列模拟器
2025-08-01 15:43
-
ITECH重磅发布IT2705直流电源分析仪,重构
2025-08-01 15:34
-
现代汽车新一代混合动力系统:以技术革新引
2025-08-01 15:32