干货 | 集成48 V电机的内燃机设计与开发研究
内燃机电气化是未来汽车发展的重要技术路线。内燃机电气化可以通过再生技术回收废能,降低影响内燃机效率的各种损失。介绍了1款可以集成在柴油机上的电机,采用48 V弱混系统实现内燃机的电气化。电气化内燃机设计的首要任务是考虑其扩展性,即车辆增加的空间最小化并可以配装在其他不同车型上。与皮带传动起动/发电一体化电机替代前端轮系中的发电机的48 V弱混系统不同,将电机集成到曲轴上可以取消一些功能重复的零部件,如起动机和附件皮带系统,并可以有效克服一些在实际行驶中内燃机难以克服的缺点。动力总成电气化技术的应用结合未来车内通信或者自动驾驶技术可以进一步降低车辆行驶中实时信息传输中浪费的能量。随着技术的发展,制氢和发电将不再产生温室气体,也不再利用化石燃料,这有利于环境保护。但在此之前,提高内燃机效率和采用电气化以弥补内燃机的缺点仍然非常重要。___
0 前言
内燃机电气化可以提高车辆的燃油效率,现代汽车开发了1款柴油机飞轮集成电机(下文称为“P1系统”),可以在已量产的前驱车型上应用。这款集成电机直接与曲轴的后端相连,将电机转子和飞轮集成在一起。通过采用P1系统,发电机、起动机、皮带轮系等功能重复的零部件可以被取消,同时采用电动水泵和电动空调压缩机。另外,在皮带传动起动/发电一体化电机的48 V弱混系统(下文称为“P0系统”)中,只是发电机被取代了,而P1系统可以通过降低附件传动产生的损失和根据不同的控制策略对制动能量进行回收,从而进一步提高燃油经济性。在传统内燃机上难以克服,以及需要高成本去改进的缺点可以通过电机以不同的方式进行弥补。例如,在涡轮迟滞时进行转矩助力,利用电机反相控制进行振动控制,通过内燃机起停控制提高燃油经济性,通过转矩调节降低氮氧化物(NOx)峰值等,配装内燃机的车辆性能因此得到了进一步提升。特别是在采用集成电机取代了驱动齿轮型起动机后,在使用起停功能时,动力总成通过控制低速振动和改善驾驶性能,极大提高了乘客的舒适性。
对于前轮驱动车辆,由于周边零部件的限制,内燃机和变速器的安装空间非常有限,同时驱动轴距离内燃机也非常近。现代汽车开发了1种二阶定子铁芯结构,替代了传统形状的定子铁芯结构,从而避免了内燃机与驱动轴的干涉。
为了让现代内燃机更加高效,在将48 V电压进行标准化前,宝马(BMW)公司已经开发了1款42 V曲轴直接驱动的电机,并将其应用到了柴油机上,在新欧洲行驶循环(NEDC)工况下,可以提高11%的燃油经济性,同时改善了涡轮迟滞效应,降低动力总成的振动。在通常情况下,业内普遍认为柴油机直接驱动电机(P1系统)相对驱动电机直连变速器(下文称为“P2系统”)缺点更多,诸如制动能量再生时须克服内燃机的阻力等。然而,P1系统取消了附件轮系,在能量再生时的诸多问题可以通过降低附件损失得以克服。高压混合动力汽车(HEV)在进行系统布置时,电池和电机需要更大的空间,因此其需要采用专用平台或开发全新的安全零部件。
48 V弱混汽车(MHEV)可以用来应对全球变暖和降低能源消耗,其主要任务是在车辆开发时以少量的投入最大化提高燃油经济性。要想达到这个目的,最合适的系统就是P0系统和P1系统,而P2系统和P4系统(电机安装在后轴)由于需要对车辆作更多变更,同时投入巨大的费用,与其带来的效果不匹配。同时,48 V系统有助于提高车辆的电气化水平,诸如采用自动驾驶、座舱娱乐系统和车辆控制设备等。
1 电机的开发
研究人员在进行P1系统的电机开发时设定了最大功率、额定功率和最大转矩目标。考虑到取消了齿轮型起动机,在本研究中,P1电机的起动转矩依据起动机驱动齿轮比和2.2 L柴油机的怠速扭矩确定。从用户安全考虑,冬天用户在室外停车时要能用P1电机起动车辆。基于48 V系统的特性考虑,电机功率设定在20 kW以下。基于内燃机功率考虑,在既能助力又可以取消传统起动机的情况下,本研究中的电机功率和转矩分别设定为15 kW和150 N·m。表1示出了该电气化内燃机的基本参数。
表1 电气化内燃机的基本参数
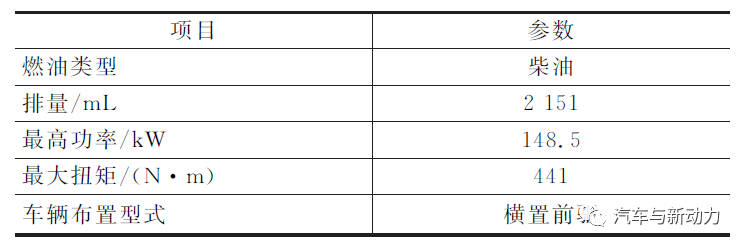
2 开发目的
为了降低快速电气化带来的巨大风险,48 V电机系统是未来环境友好型车辆的中间桥梁。虽然配套48 V电机系统的动力总成的性能表现、燃油经济性和市场可接受度有待提升,但因其价格提高较小,与顾客需求和制造商的设计理念是相符合的。这有利于整车厂开发出比高压HEV系统价格更低,对顾客更安全的车辆,这是因为即使人体触碰到60 V的电压没有触电风险。如果电压超过60 V(包括电压偏差),需要依法设计绝缘冲击防护和碰撞安全措施,以保证用户的安全。
同时,这也有利于提高车辆的电气负载供应。由于车辆附件增多,以及自动驾驶技术的开发,车辆用电量大幅增加,目前在用的12 V系统和24 V系统已经到了极限,48 V系统是未来发展的替代选择。
2.1 弱混汽车飞轮集成P1电机的设计方案
对于前驱横置动力总成,曲轴直接连接电机作为单独的模块,在内燃机和变速器之间布置通常会非常困难。同一车辆平台,副车架之间的空间是有限的,内燃机和变速器安装到车辆的装配间隙有严格的要求。为了在内燃机和变速器之间增加电机,并且最大化缩短长度,这就需要整合诸多功能重复的零部件。取消附件皮带系统可以补偿增加电机带来动力总成长度的增加。
如图1所示,研究人员将飞轮与转子集成设计并首先应用在手动变速器上,将转子集成到飞轮上,对定子和旋转变压器重新设计,使缸体后端面的凸出长度最小。
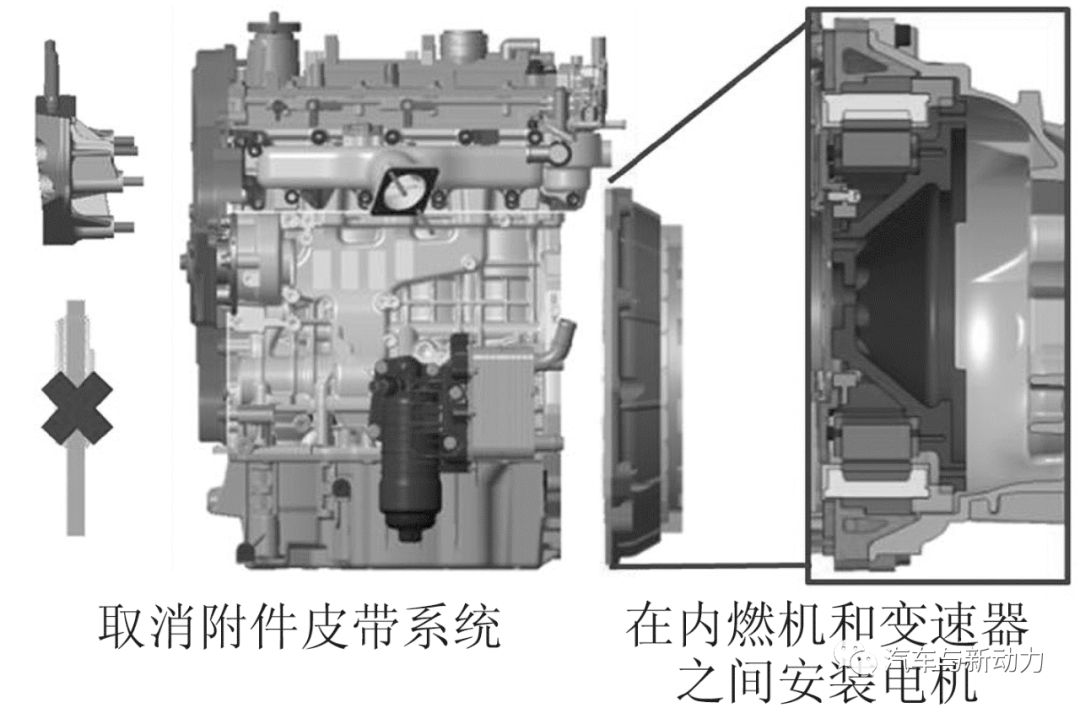
图1 配装手动变速器时飞轮集成电机示意图
另外,研究人员对变速器的离合器壳体形状进行了优化,以减少动力总成的长度。即使增加了电机,采用集成设计的动力总成的总长度仅增加了28 mm,电机增加的长度与原附件皮带系统的长度相当。在高性能内燃机中,为了消除变速器接合时的内燃机的扭矩波动和冲击,通常会采用双质量飞轮(DMF)。转子铁芯和磁铁集成在飞轮上可以大大提高飞轮的惯性质量。增加的惯量质量可以用于降低曲轴的旋转振动,其减振效果比现有的双质量飞轮更好。表2示出了内燃机开发时转子和飞轮集成后的转动惯量。从中可以看出,集成后的转动惯量比手动变速器的转动惯量大,因此随着转动惯量的增大,角速度波动随之降低。
表2 各种变速器的转动惯量

2.2 前驱车辆的电机设计
考虑到驱动轴的间隙要求,前驱车辆通过增加外径,应用同轴P1电机以满足功率要求是非常困难的。如图2所示,驱动轴和曲轴的距离不能改变,因此要控制电机的外形尺寸以避免干涉。
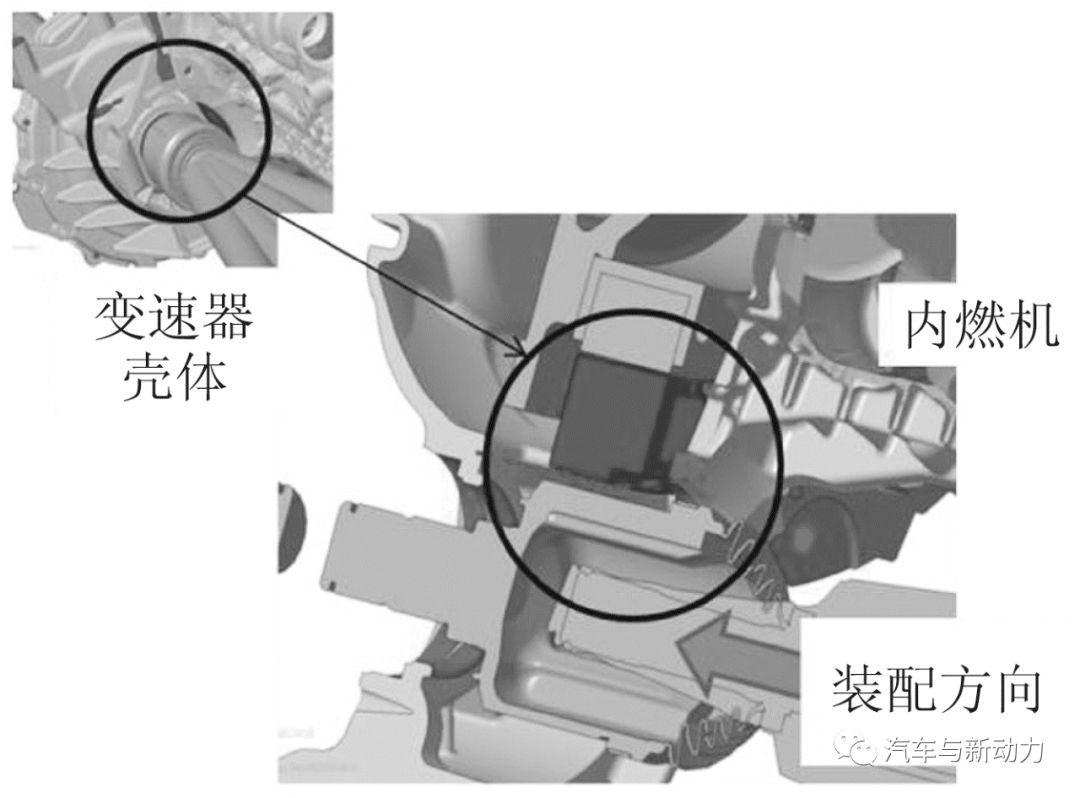
图2 驱动轴和电机之间的距离
为了达到设定的功率和转矩,研究人员需要优化电机的长度和外径。然而,增加轴向长度就会缩短周边零部件与内燃机的间隙,增加外径则会带来布置问题,即驱动轴和电机的间隙减小。后驱车辆在内燃机周围没有驱动轴,电机的外径只受限于内燃机本体尺寸,因此其布置相对容易一些,如Daimler公司直列6缸柴油机。如图3所示,研究人员分析了3种型式的电机,基于量产和功能考虑,最后选择了二阶电机方案。
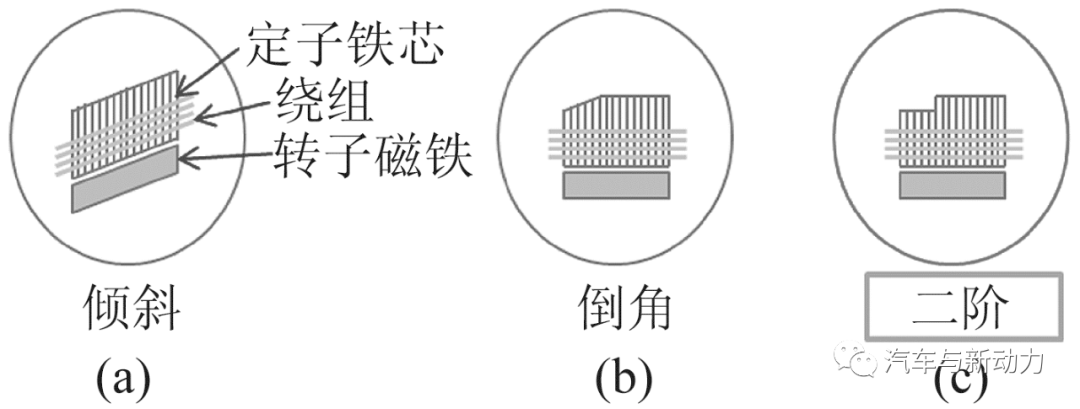
图3 3种型式的电机绕组概念
在优化电机轴向长度和外径的同时,为了达到设定的功率和转矩,现代汽车开发了1款电机,定子采用二阶电机方案(图4)。通过对安装驱动轴的周边形状进行仔细研究,采用这种设计可以使定子外径最大化。
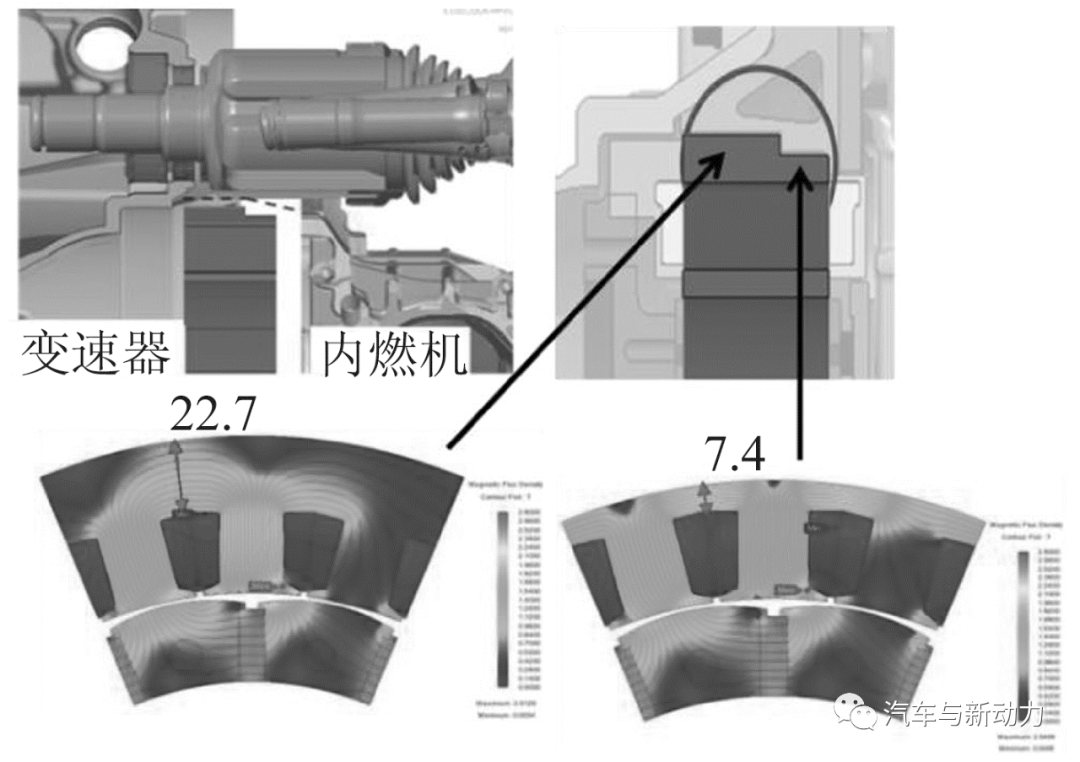
图4 二阶电机仿真结果
当定子采用二阶电机方案时,研究人员通过外形设计,分析计算了电机的功率损失和轴向力。考虑到驱动轴的安装,研究人员采用二阶定子,重新开发电机,在增大外径的同时缩短了轴向尺寸。如图5所示,转矩计算结果表明,偏移量为4 mm以下时,驱动转矩只会出现部分降低的情况。电机的转矩降低很少,转矩目标可以满足设定要求。
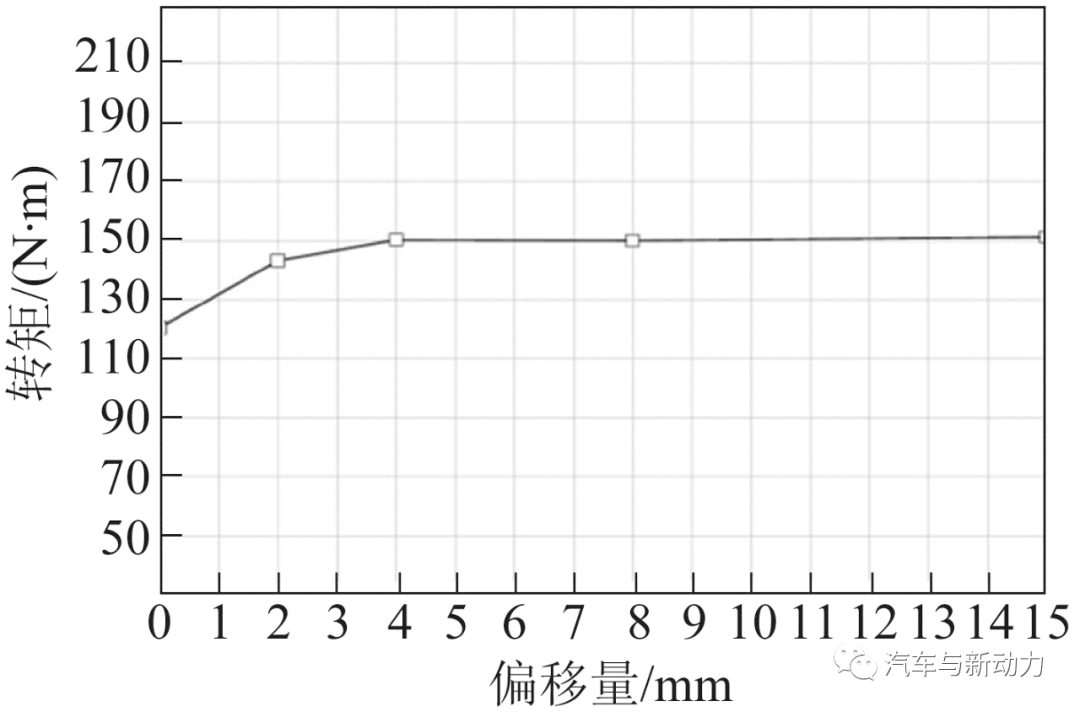
图5 二阶电机仿真转矩
2.3 匹配内燃机前的电机台架试验结果
为确认设计阶段仿真的目标性能和效率是否达标,研究人员将电机安装在底盘测功机上进行转矩测量。如图6所示,测量的逆变器效率高达92.3%。如图7所示,测量的电机效率高达98.3%,在实际运行区间效率甚至超过90.0%。如图8所示,电机性能测量结果表明,制造零部件前通过仿真设定的目标可以达到。
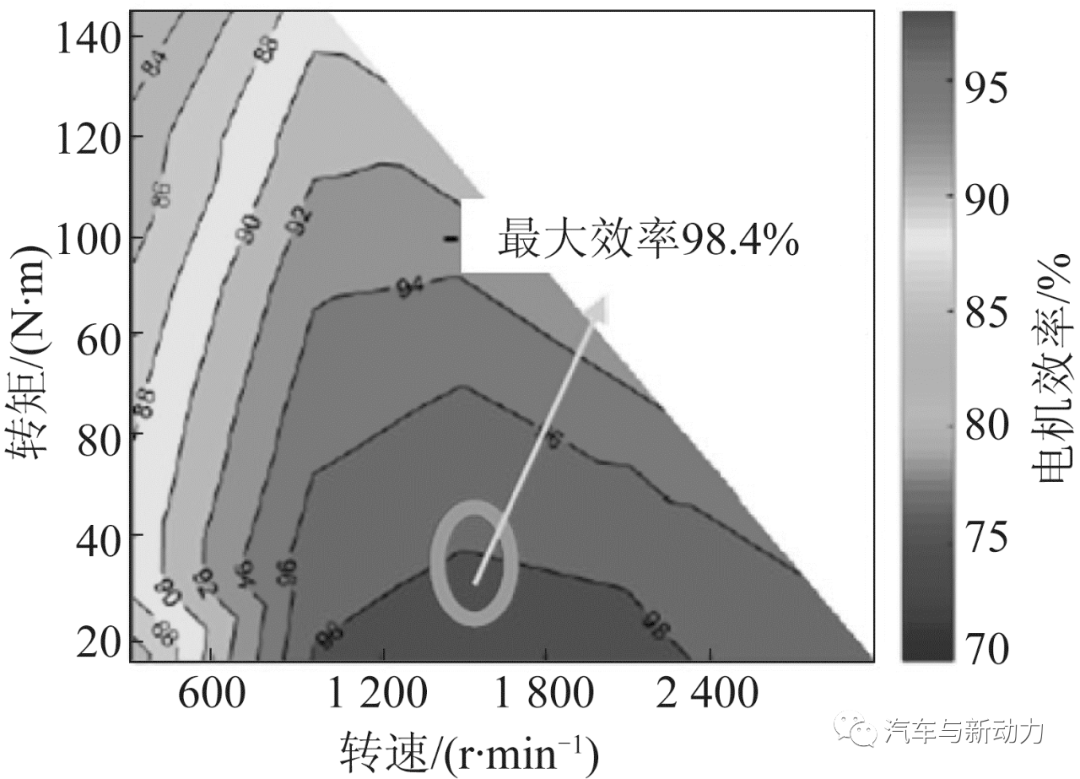
图6 测量的逆变器效率
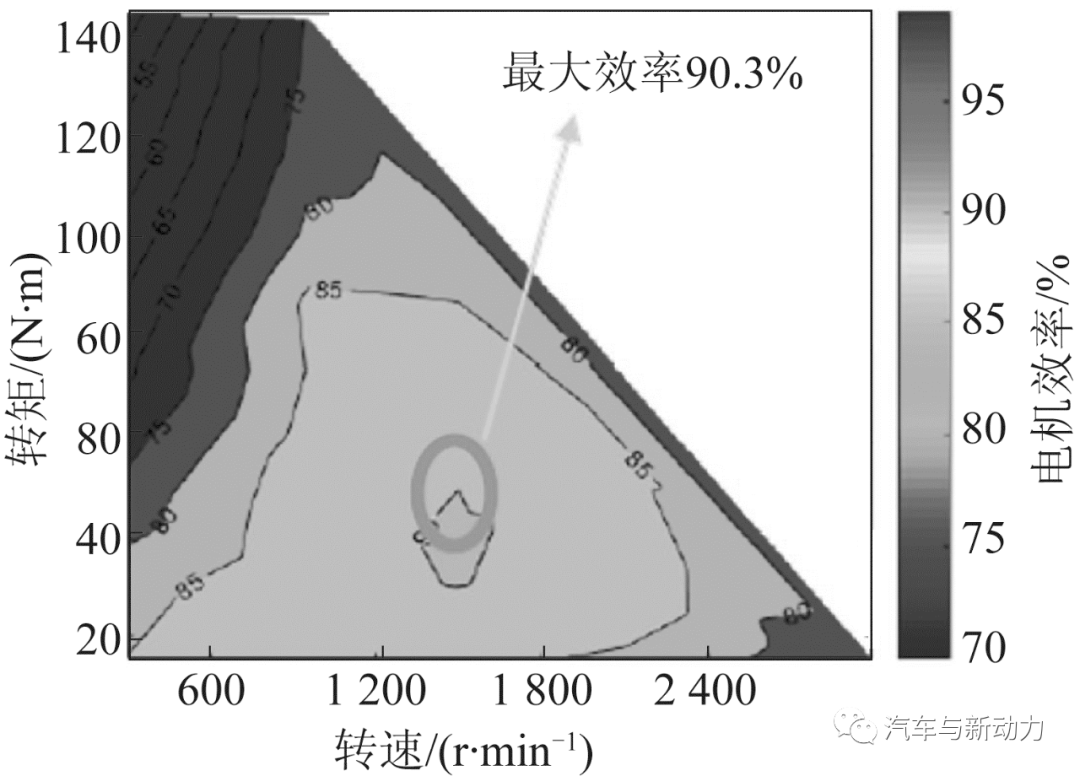
图7 测量的电机效率
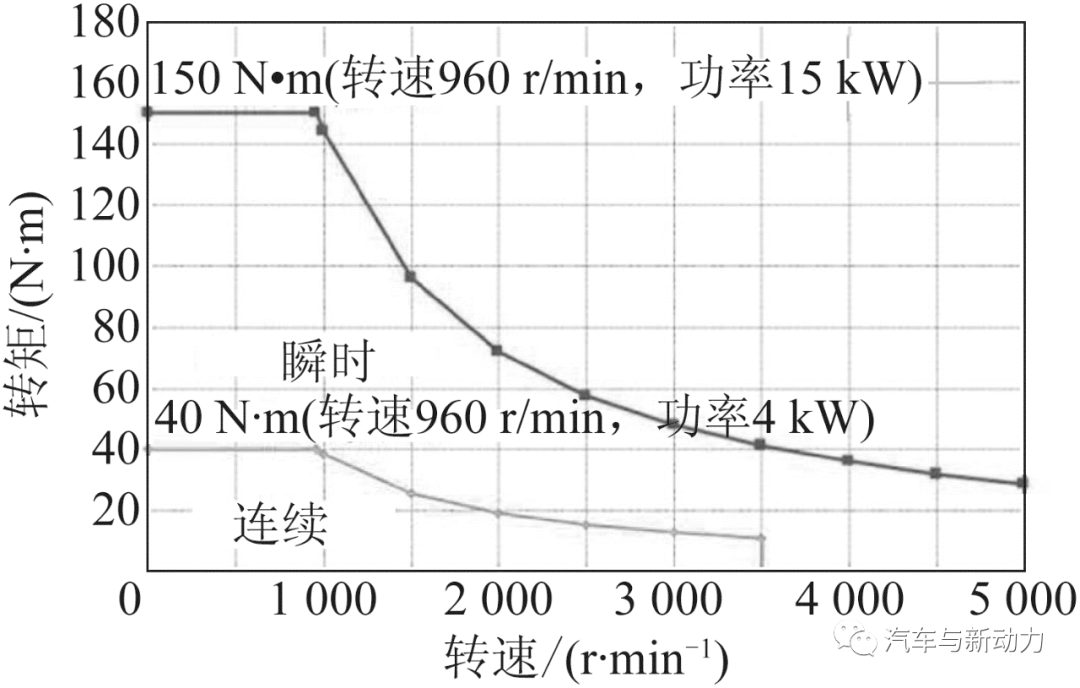
图8 测量的集成电机性能
2.4 匹配双离合变速器(DCT)和自动变速器(AT)的集成电机设计
在车辆开发时,P1电机布置的最大障碍是安装布置,其需要克服不同变速器的轴向安装尺寸的限制,如图9所示。为了缩短内燃机长度,研究人员采用内燃机集成电机设计,并对不同变速器的电机转子形状进行了优化。与P2电机、P3电机(电机安装在变速器和差速器之间)和P4电机结构不同,P1结构的电机安装在离合器后的变速器侧。单质量飞轮、双质量飞轮、外减振器和变矩器的共同要求是要满足变速器的匹配安装,这对P1电机结构非常重要。
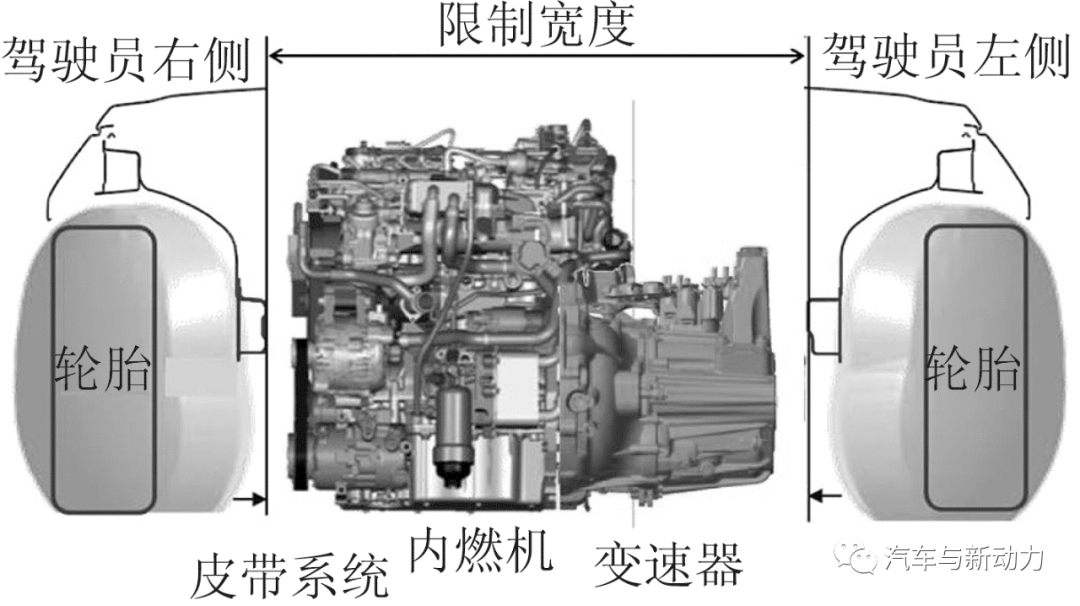
图9 传统电机在DCT和AT变速器中的应用
在P1电机结构中,电机转子要集成设计的零部件分别是DCT的外减振器、手动变速器(MT)的飞轮和AT的变矩器。飞轮集成设计转子相对容易,但是包含弹簧和减振结构的外减振器需要重新设计,以保证减振性能和转矩传递。至于变矩器,需要采用创新设计以重新检验内离合器和环面结构,并将其置于转子的空余空间。因此,开发费用和零部件费用大大增加。如图10所示,对于DCT和AT动力总成,直接在离合器位置前布置电机,将增加内燃机长度,并且存在安装困难的问题。
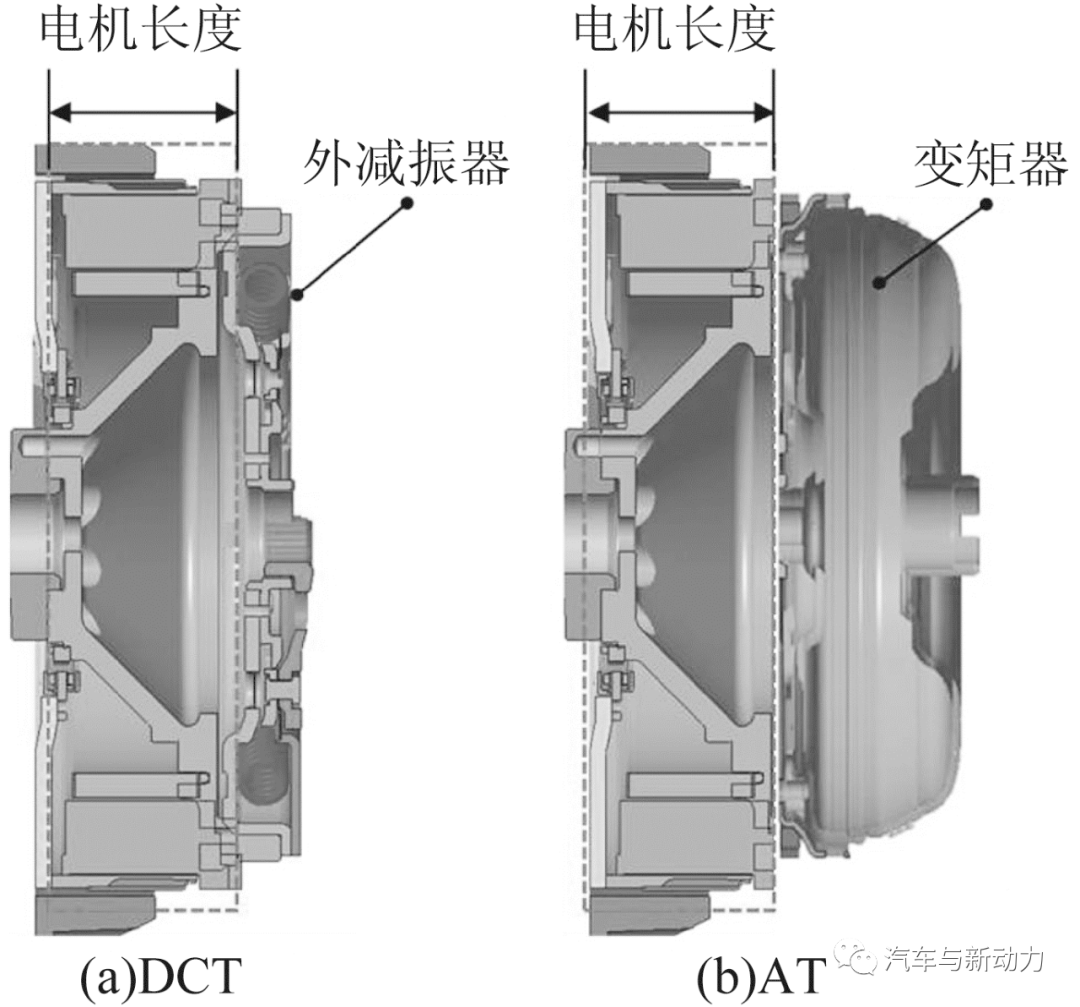
图10 传统电机在DCT和AT中的应用
Daimler公司发明了集成转子的变矩器,可以应用于P1电机,并且可以根据装配需要进行特殊设计变更。对于手动变速器来说,该变矩器通过简单集成设计可以节省空间,但是对于AT和DCT变速器需要进一步开发,因为需要在固定的空间内集成减振器或者变矩器的功能。
2.5 P1电机逆变器和电气架构的开发
48 V P1电机系统的控制器局域网络(CAN)通信和电气连接如图11所示。为了控制电机,故障保护功能在电机控制器(逆变器)中实现,电机运行模式可以通过CAN 通信由发动机控制单元(ECU)控制和连接。电机运行模式共分为4种策略:空档、电机助力、发电和转矩控制。每种策略中通过CAN通信确认ECU传递和接收的信号无误后实施内燃机和车辆评估。由于电机粘连保护试验在台架上无法再现,故障保护试验可确认除电机粘连保护以外的功能,通过其他功能试验可以评估电机失效或者传感器故障的发生。
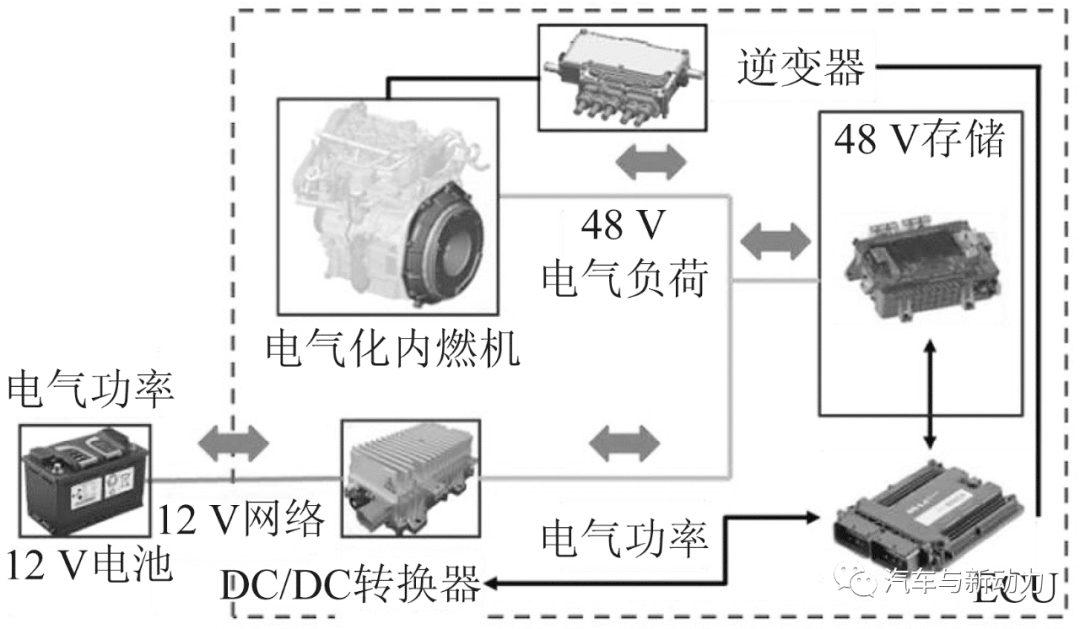
图11 48 V弱混系统的控制和网络示意图
2.6 P1电机的燃油济性
通过应用P1电机系统提高燃油经济性,可以从3个方面进行分析。第一,通过取消附件皮带系统可以达到无皮带连接内燃机的效果;第二,通过制动再生进行能量存储;第三,通过电机助力避免瞬时多余燃油消耗。除了上述3方面因素外,应用P1电机系统的集成起动/发电一体化电机(ISG)在一定程度上可提高燃油经济性。
电气化内燃机可以通过开发诸多控制逻辑持续改善以最大程度提高燃油经济性。在D级乘用车上,转矩仪安装在减振皮带轮上,用于测量附件系统的损失。在高速行驶工况下,内燃机平均驱动扭矩损失为7.6 N·m。考虑到内燃机平均扭矩每损失1 N·m 会带来1.0%~1.5%的燃油经济性差异,因此取消附件皮带系统有望对燃油经济性带来5%的收益。研究人员使用P1电机直接连接到曲轴,很容易根据发电机的效率调整内燃机负荷。对于应用最多的皮带传动的P0电机系统,发电效率是85.0%,电机效率是80.0%。通过P0系统分担内燃机负荷以提高燃油效率相对比较困难。
对于P1电机和P2电机系统轴向电机的应用,电机的直径可以设计得比P0电机和非轴向型式电机的直径大,发电效率可以达到95.0%。在不同模式下,与低负荷区域发电时的燃油消耗相比,中负荷或高负荷区域采用转矩助力有利于燃油经济性的最大化。提高电机效率有助于更主动地调整内燃机负荷,从而提升燃油经济性。
对于采用P1同轴电机的中型运动型多功能车(SUV)自动变速器车辆,评估结果表明,在全球统一轻型车辆测试循环(WLTC)工况下的燃油经济性提高了7%。
2.7 P1同轴电机性能
相较于P1非同轴电机或P0电机,P1同轴电机在功率传递过程中没有损失,因此电机功率可直接用于动力总成输出。不同于内燃机,即使在低速时,电机产生的转矩也不会有延迟,这解决了发动机扭矩响应迟滞的问题。基于电机在低速时,转矩特性无时间延迟,48 V电池可以为内燃机的动力输出产生助力,这也极大提高了电气化动力总成的响应性,图12为电气化内燃机的扭矩输出曲线。图13为电气化内燃机的功率输出曲线。
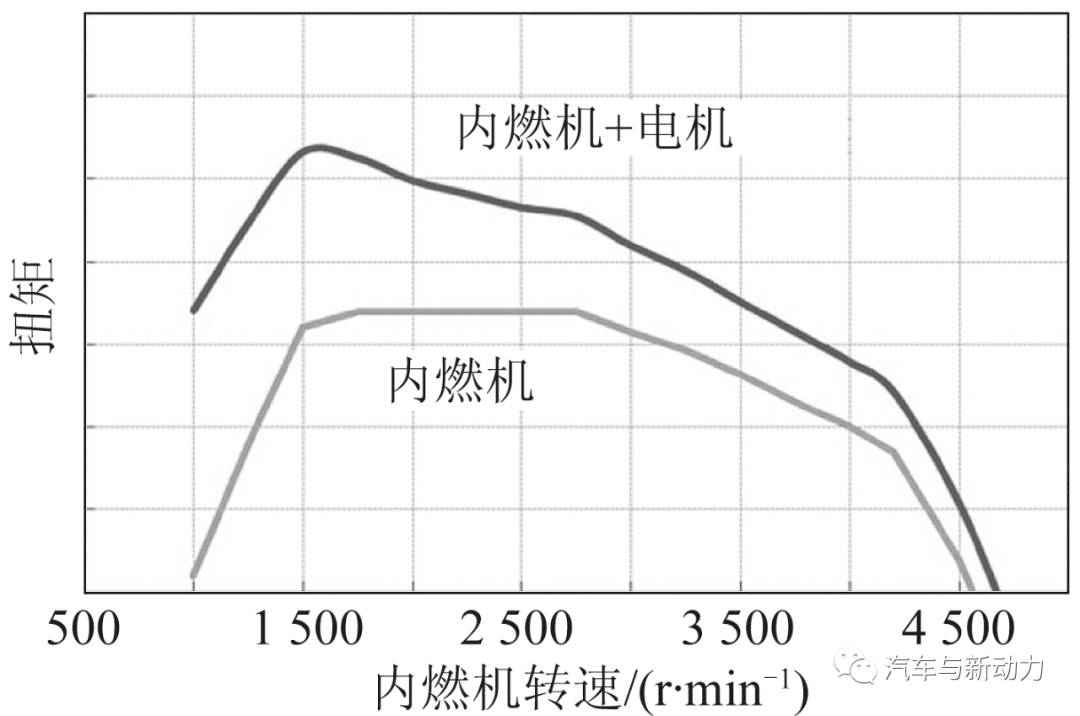
图12 电气化内燃机的扭矩输出曲线
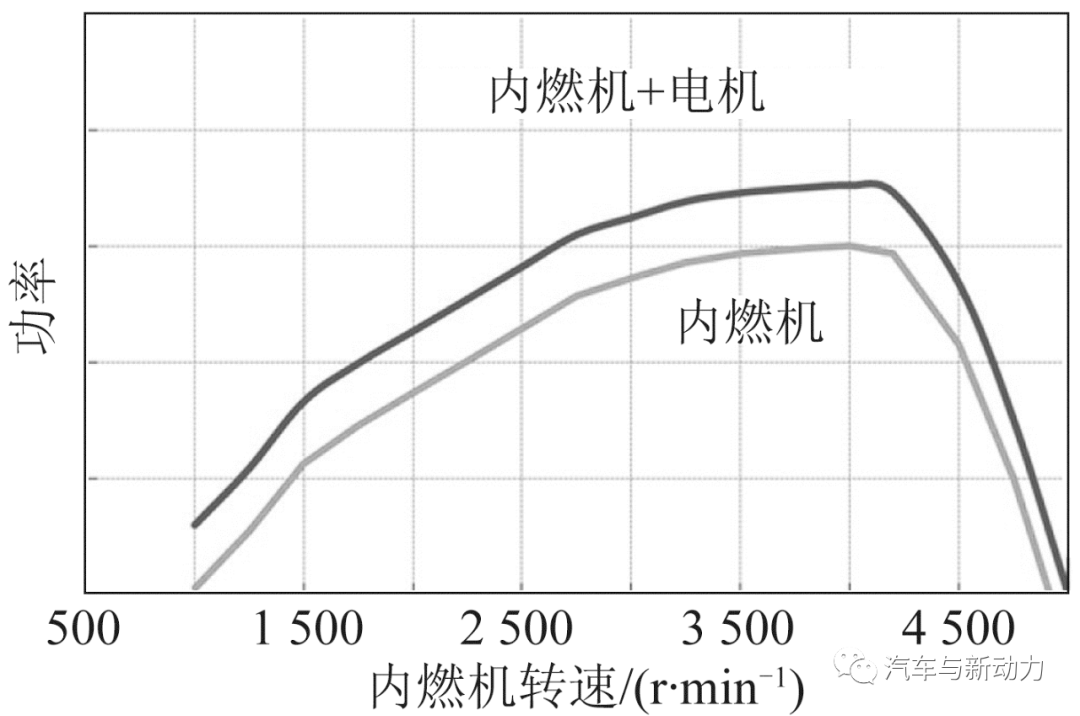
图13 电气化内燃机的功率输出曲线
3 结语
通过优化P1电机,整机厂可以开发出电气化内燃机。研究人员将48 V P1电机与曲轴相连,取消了皮带系统、发电机、起动机和飞轮等多余零部件。相较于P0电机系统,P1电机系统取消皮带系统附件,可以减少内燃机性能输出损失。通过开发制动再生和转矩平衡等控制逻辑,相较于现有配装传统内燃机的车辆,匹配P1电机系统的电气化内燃机的燃油效率得以提高。并且,在应用电机后,研究人员可以开发出更多控制逻辑,以实现更多功能来弥补内燃机的缺点,如提高燃油经济性,通过反相位控制衰减二阶振动,通过转矩平衡改善NOx排放峰值,通过电机转矩助力改善内燃机起动性能。
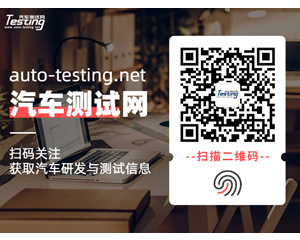
最新资讯
-
商用车及工程机械行业专场:NVH 及语音音频
2025-08-01 17:12
-
理想i8和重卡对撞测试引争议,东风柳汽发声
2025-08-01 15:52
-
艾德克斯IT-N2100 系列太阳能阵列模拟器
2025-08-01 15:43
-
ITECH重磅发布IT2705直流电源分析仪,重构
2025-08-01 15:34
-
现代汽车新一代混合动力系统:以技术革新引
2025-08-01 15:32