某纯电动车型热管理系统开发
【摘要】在本公司某车型的系统热管理概念设计阶段,通过采用一维和三维耦合仿真分析方法及三维CFD仿真分析方法对发动机舱的总布置方案及各零部件热参数进行模拟分析优化。在车型开发后期通过整车环境模拟试验验证了仿真分析的正确性。该仿真分析方法不仅缩短了开发周期,而且为高效热管理系统开发提供参考。
1 前言
为应对纯电动汽车对整车低阻力的要求,需严格控制散热格栅的开口面积,这就对整车热管理的难度提出了更高要求。传统方法无法开发出高效的热管理系统,并且开发时间长,开发成本昂贵。随着计算机仿真技术的发展,数值计算变得更加可靠,从而使得精确的整车热管理系统开发工作提前到概念设计阶段。
汽车热管理数值计算方法分为一维和三维,三维CFD计算可以考虑更多的细节,并能直观给出空气的流动状态,但需要庞大的计算资源及精确的输入数据,在现有的设计开发流程中很难做到。而一维软件虽然不能考虑所有的细节部分,但需要的计算资源少,计算时间短,不需要太多复杂的数据,而且使用三维CFD计算中没有使用的热传递计算公式,较适合冷却系统的前期匹配计算。
在本公司领志纯电动汽车整车热管理系统开发中,为了提高整车热管理的效率,借助CCM+、AMESim等软件采用一维三维耦合仿真计算的方法,对整车热管理进行计算,并在此基础上改进该款车的冷却系统。
2 冷却系统结构及一维仿真分析
2.1 冷却系统结构
领志纯电动汽车热管理系统主要由3个热交换系统及电控系统组成,3个热交换系统为整车散热系统、乘客舱制冷系统、乘客舱加热系统,其主要零部件为HVAC总成、冷凝器散热器总成、电动压缩机总成、空调制冷管路总成、高压PTC总成、水泵总成、膨胀水箱总成、水管、控制面板、空调控制器总成等,如图1所示。
该车型的电池散热系统采用风冷方式,所以对乘客舱的制冷系统和加热系统的设计不造成影响。整车散热系统的设计以发热量从小到大的顺序为原则,冷却液依次冷却充电机、PCU、电动机;设计目标是在考核的工况下,冷却液温度≤65℃。根据纯电动车型的性能和使用习惯,制定高温考核工况如表1所列。
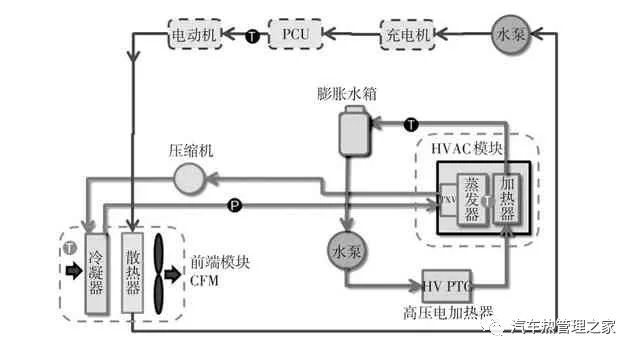
图1 整车热管理系统原理示意
表1 高温环境考核工况
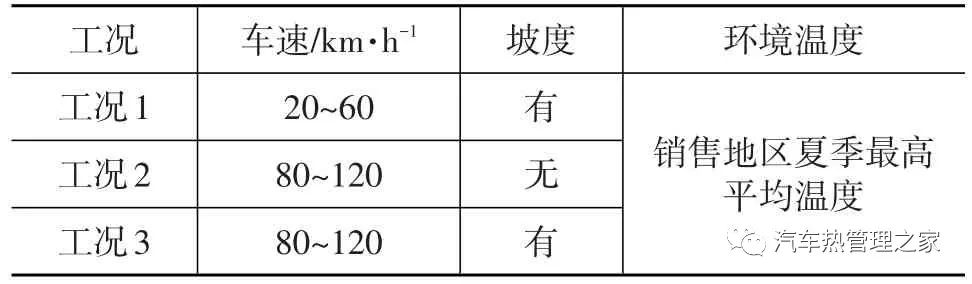
2.2 冷却系统一维仿真分析
该车型一维整车热管理系统分为空气侧和水侧两大部分,空气侧由前端空气压力、散热器模型,水泵模型,电机及PCU热模型等部件构成,而水侧是以冷却液循环、润滑油循环和空调循环等构成。该冷却系统空气侧模型如图2所示。
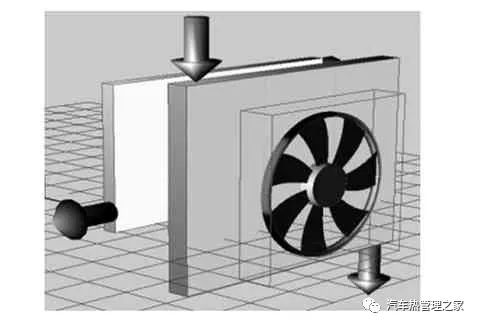
图2 车辆冷却系统空气侧模型
3 前舱三维CFD分析
3.1 物理模型设定
整车热管理需要考虑冷却系统和零部件的工作温度范围,整车CFD模型需要保留影响计算结果的部件细节。机舱模型示意如图3所示。
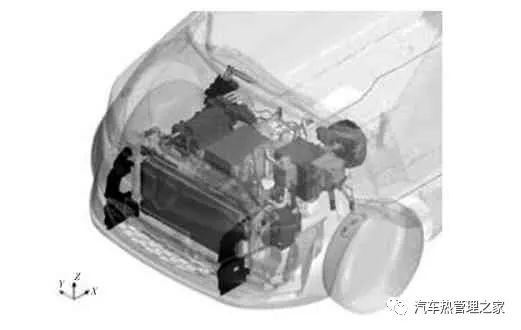
图3 机舱模型示意
本文整车网格划分主要是在Hypermesh中完成几何清理和面网格划分(图4),体网格主要在CCM+软件中完成,在计算敏感区域(汽车发动机舱内、散热器组等)使用密度盒加密,以达到局部网格细化来提高计算精度的目的。
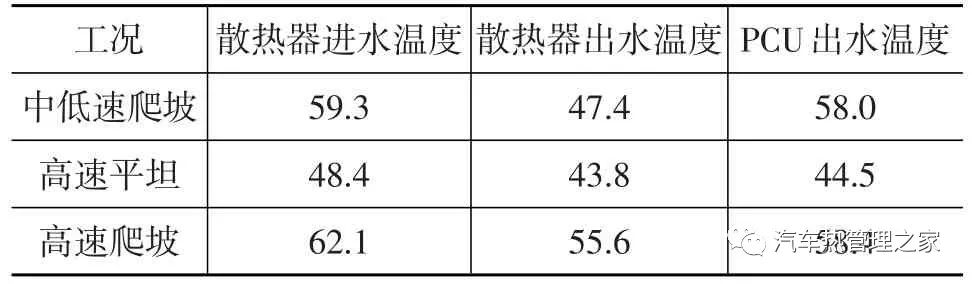
图4 面网格划分示意
三维计算中采用的边界介质为空气,环境温度40℃。换热器等复杂结构体积的简化模型以多孔介质模型来代替。多孔介质的设置要根据试验得到的冷凝器、散热器的阻力曲线获得。散热风扇采用MRF模型,风扇转速为中低速1 900 r/min、高速2 300 r/min。物理模型采用Realizable k-ε模型。
3.2 CFD计算结果
三维CFD计算使用商业软件CCM+,通过计算可以很直观的显示发动机舱的空气流动以及温度分布,同时得到通过散热部件的冷却空气的压力损失和流量。图5和图6分别为低速工况下发动机舱的空气速度和温度分布的Y截面示意图。前端模块的进气量和进气温度利用一维软件进行耦合计算,以提高计算的精度。表2为在CFD计算中各散热部件的进风流量。
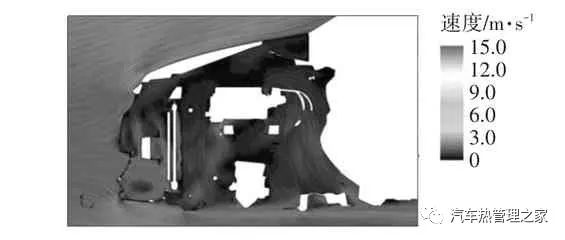
图5 机舱截面速度流线示意
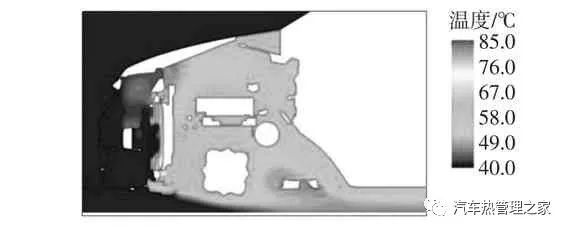
图6 机舱截面温度分布示意
表2 CFD计算的进风流量m3/h
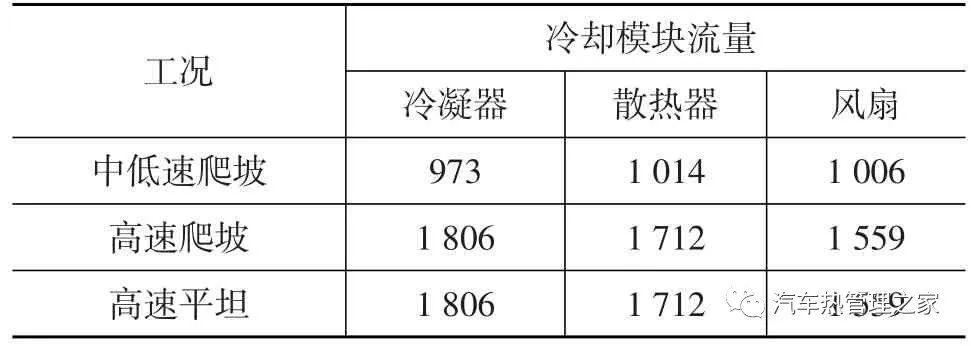
4 冷却系统一维三维耦合分析
三维CFD计算得到的散热器出风面的速度分布云图如图7所示。把速度矩阵导入AMESim软件中换算成相应的阻力矩阵,在计算中考虑散热器表面速度分布不均匀的影响。图8为从CFD导入AMESim中的散热器表面速度分布一维计算结果。图9为加入阻力矩阵后散热器表面速度分布一维三维耦合计算结果。
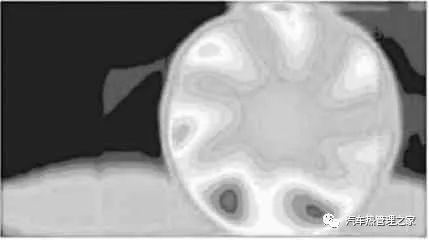
图7 散热器的速度分布云图
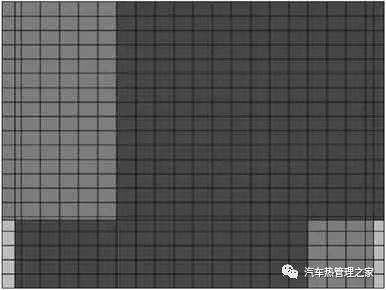
图8 散热器表面速度分布一维计算结果
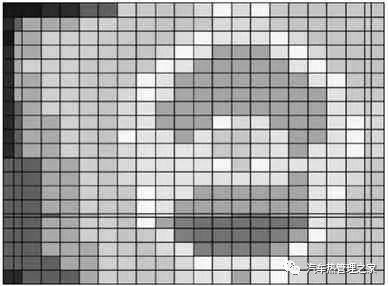
图9 散热器表面速度分布一维三维耦合计算结果
由图9可知,由于考虑三维计算结果的影响,散热器表面的速度分布发生了变化,提高了一维仿真的精度。不同工况下一维计算结果如表3所列。
表3 不同工况下一维计算结果℃
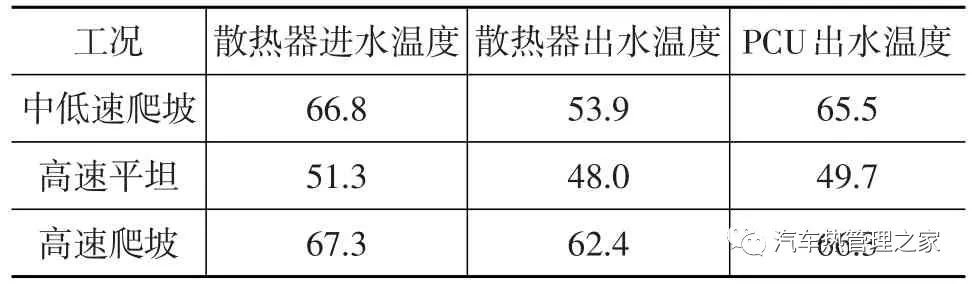
由表3可知,中低速爬坡工况下,由于散热器前温度稍高,导致散热器换热能力下降,散热器冷却液进水温度为66.8℃,超过电机冷却液进口温度范围-30~65℃;高速平坦工况下,由于PCU及电机散热量与中低速爬坡工况相当,而散热器前温度相比中低速工况下略有降低,散热器前风速远大于中低速工况下散热器前风速,散热器入水温度为51.3℃;高速爬坡工况下,PCU及电机散热量远大于中低速爬坡工况与高速平坦工况,散热器前温度与中低速及高速平坦相比没有明显增高,由于散热器散热能力有限,导致散热器入水温度达到67.3℃,超过了PCU及电机最佳冷却水温范围。
5 冷却系统的优化设计及试验验证
中低速爬坡和高速爬坡工况下,由于散热器散热能力有限,导致水温超过PCU及电机最佳冷却水温范围。需要考虑改善散热器的冷却进风量和进风温度以降低冷却水温。而要改进高速情况下的进风情况,单靠提高风扇的转速效果不是很明显,而且风扇高速旋转会损耗大量功率并带来噪声,图10为冷却风扇转速和流量的对应关系。
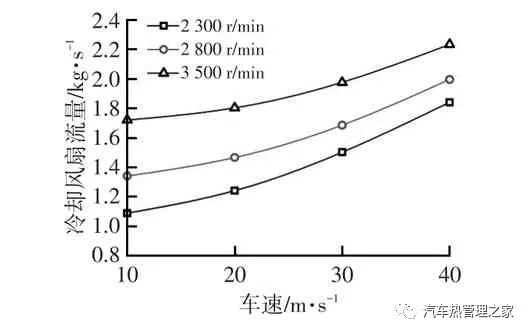
图10 冷却风扇流量随风扇转速变化关系
通过CFD计算分析,低速段时风扇转速对冷却风流量影响较大,高速段时风扇转速对冷却风流量影响较小。由图10可知,随着车速以及风扇转速的提高,冷却风扇的流量有所提高,但低速段风扇对冷却风流量影响较大,而高速段影响较小。
根据CFD结果中的截面流线图(图11和图12)可知,在前保险杠后部有一定区域的回流,产生了上下两个明显的漩涡,这对进气效率有一定影响;并且较多冷却风直接从前端模块的两侧和底部流走,没有被充分利用到散热器组中去。因此,提出改进冷却系统的方案。
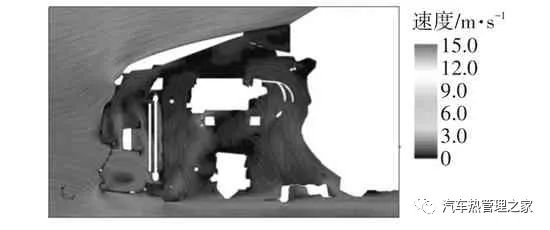
图11 前端模块Y截面流线图
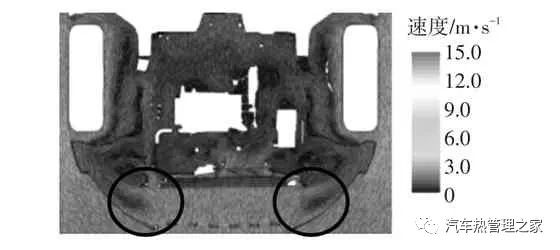
图12 前端模块Z截面流线图
5.1 导流板的改进设计
在前端模块的两侧和底部加导流板,改变冷却风进风角度,使更多的冷却风通过散热器组,提高散热器组的进风流量,并且能在低速工况和怠速工况下阻挡热风回流。安装的位置和角度如图13所示。
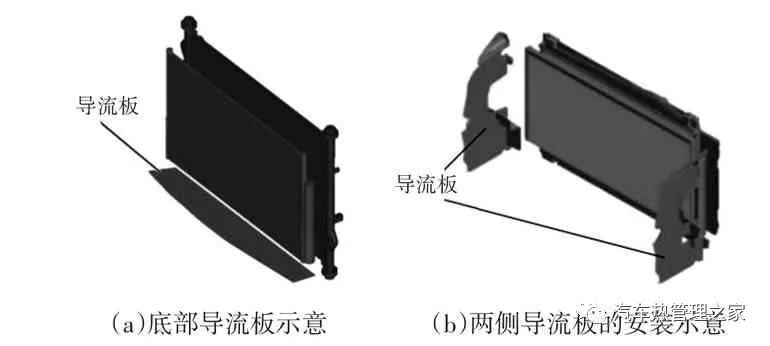
图13 导流板改进方案示意图
两侧导流板优化方案Z截面流线图如图14所示。由图14和图12对比可以看出,下进气格栅的进风角度改善后,从前端模块两侧流走的冷却风流向了散热器组,更多的冷却风提高了冷却效率。
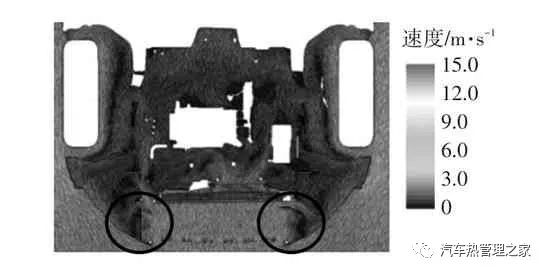
图14 两侧导流板优化方案Z截面流线图
改进前后的进风量对比如图15所示。散热器在中低速的风量提升5.05%,高速工况下风量提升6.7%。参数输入AMESim中进行计算,得到的结果如表4所列。可知,散热器出水温度降低明显,高速爬坡的最高水温降低到62.1℃,比原来降低7%,其它工况也在设计要求的范围内。
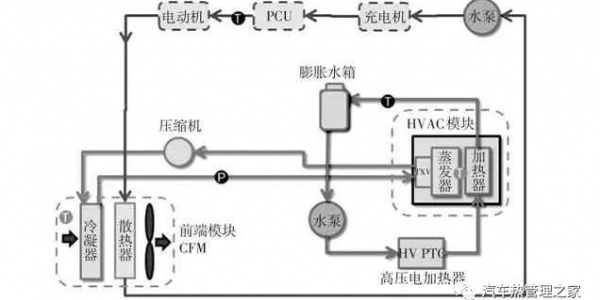
图15 导流板优化方案风量增加百分比
表4 优化后不同工况下一维计算结果℃
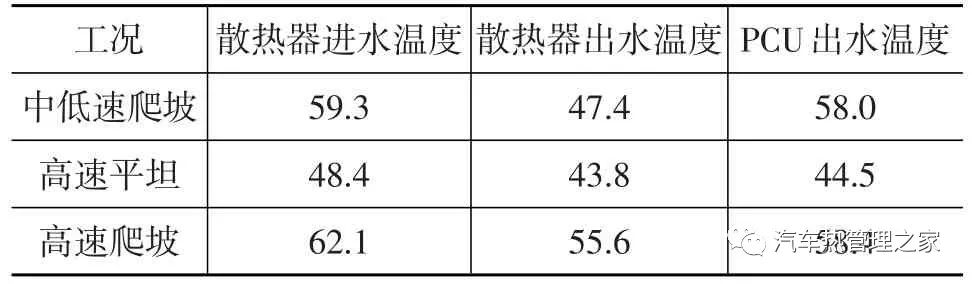
5.2 试验验证
将优化后的整车冷却系统安装在试制样车上进行热环境试验验证。
对前端测量冷却模块进行冷却风量测试,对比仿真和试验数据发现,低速工况冷却风量的误差为2.3%,高速工况下误差为2.8%;试验测试的冷却风量偏低。分析原因为热环境仓的流场稳定性低于CFD仿真设定,会造成一定的偏差。对比水温和PCU的出水温度可得,散热器的水温和PCU的水温都比计算值偏小3.5%,分析原因是环境仓的环境温度不稳定以及整车浸车温度无法达到平衡。但计算误差均在工程应用的范围内。在试验条件允许的情况下,可以考虑在热环境风洞中进行试验,保证流场的均匀性,并在试验前充分的浸车,从而提升试验数据的准确度。
6 结束语
a.利用数值计算方法可以在汽车开发的前期阶段对汽车冷却系统和发动机舱的气流进行研究,缩短开发时间,降低开发成本。结合一维和三维的计算分析方法,证实该方法有效,适用汽车开发前期的热管理计算。
b.,在汽车下进气格栅加入导流板,改进冷却风的进风角度,增加散热器组冷却风的进气流量,从而改善散热系统的性能。
c.通过最终的试验验证,车型整车热管理系统达到整车性能要求。
作者:柳文斌1 袁侠义2 赵力1 林卉2 吴风盛1
单位:
1.广汽丰田汽车有限公司
.广州汽车集团股份有限公司汽车工程研究院
- 下一篇:基于Racelogic VIPS的室内NCAP测试
- 上一篇:理解雷达的基本概念
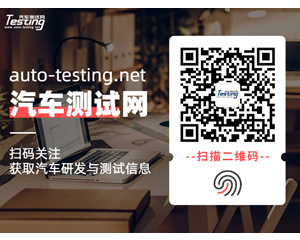
最新资讯
-
商用车及工程机械行业专场:NVH 及语音音频
2025-08-01 17:12
-
理想i8和重卡对撞测试引争议,东风柳汽发声
2025-08-01 15:52
-
艾德克斯IT-N2100 系列太阳能阵列模拟器
2025-08-01 15:43
-
ITECH重磅发布IT2705直流电源分析仪,重构
2025-08-01 15:34
-
现代汽车新一代混合动力系统:以技术革新引
2025-08-01 15:32