电动汽车和动力电池托底安全测试方法改进
2018年以来,各品牌电动汽车起火事故接连发生,国外电动汽车品牌特斯拉、国内造车新势力代表蔚来均牵涉其中,新能源汽车快速发展背后危机重重。
调查显示,特斯拉自燃车辆的动力电池曾遭遇托底。而据蔚来官方微博公布,蔚来自燃车辆在送修前底盘曾经遭受过严重撞击,即发生托底,导致动力电池左后部外壳与冷却板大面积变形,电池包内部结构在被挤压的状态下经过一段时间后形成短路,最终引发火情。
目前,行业内普遍采用整车刮底试验和动力电池底部球击试验对电池系统进行托底安全性验证,要求试验后不起火不爆炸,动力电池的托底耐久性并没有得到充分评估与保证。
2 托底
托底,是指汽车底盘零件与地面或地面的突起物发生接触,汽车的底部受到撞击。汽车过减速带、撞击路沿、上坡顶、走坑洼路以及压过路面上的石头或砖块,都可能发生托底。
图1所示几种托底事故较为常见,如果动力电池频繁发生损坏或引发安全事故,会给消费者带来损失与困扰,继而会对公司品牌造成负面影响,因次,发生此类托底事故时,既要保证电池的安全性,不能出现起火爆炸现象,也要保证电池的托底耐久性,电池可以继续使用,不能存在安全隐患。
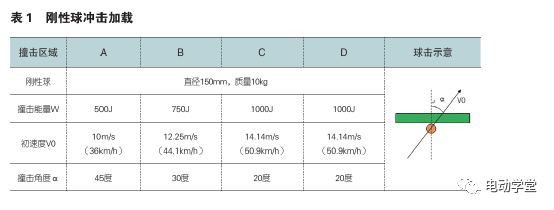
对传统燃油车,托底的危害主要是油底壳变形、排气管变形、悬架部件变形和传动机构损伤,通常不会对乘员造成人身伤害,因此,传统燃油车的碰撞安全性能开发中一般不考虑托底工况,只是将托底作为气囊标定的误作用工况来研究。
对电动汽车,动力电池布置在乘员舱的下方或者偏后方,电池底面不受车身结构的保护,是整个电池系统最薄弱的部分,托底的危害主要是剐蹭或撞击动力电池,造成安全隐患。一般而言,电动汽车比传统燃油车更重,车身悬置压缩量更大,整车离地间隙更小,更容易发生托底,而托底造成的损伤在电池底部,不易察觉,具有隐蔽性,有些托底事故虽然当时未发生起火,车辆还能继续行驶,但电池包已严重变形,如果未及时发现处理,电芯和高压器件持续处于挤压状态,电池包在一段时间后可能发生自燃。
托底主要有两种模式,一种是刮底模式,一种是撞底模式。刮底是指动力电池的前端和底部受到前后方向的剐蹭,载荷以水平方向为主,也有一些垂向成分,一般会造成电池前边框和电池底壳前半部变形,严重时甚至会将电池壳体从前到后划开。撞底是指动力电池底面受到向上的挤压或撞击,以垂直方向载荷为主,可使车轮一轮或多轮离地,通常会造成电池底壳垂向变形,严重时会将电池底壳顶穿后进而刺破内部电芯。通常情况下,撞底事故对电池包损伤更加严重。
3 电动汽车和动力电池托底安全测试与设计
3.1 托底安全测试
托底主要有刮底和撞底两种模式,相应的,在电动汽车和动力电池设计过程中,整车企业和电池供应商一般采用整车刮底和电池包底部球击两个标准工况来模拟。
3.1.1 整车刮底试验
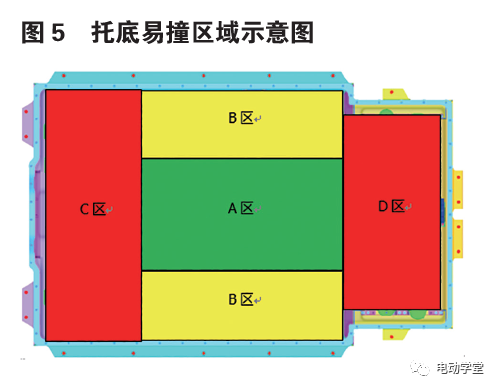
在地面固定一金属刚性块,高度设置为与动力电池壳体下底面在Z向有30mm左右的重叠量。整车采用基准质量(整备+100kg),以不低于每小时30公里的速度驶过刚性块。刮底试验共进行三次,刚性块分别对准电池包的左侧、右侧和中心线。要求试验后电池包无爆炸、起火、析气、冒烟、漏液等严重危险现象。
3.1.2 电池包底部球击试验
用直径150mm的金属球头,以不高于1mm/s的挤压速度,挤压电池包底部薄弱位置,挤压力达到20kN或者测试对象对应车型满载重量110%的载荷后(以最低值为准),停止挤压并保持1min。
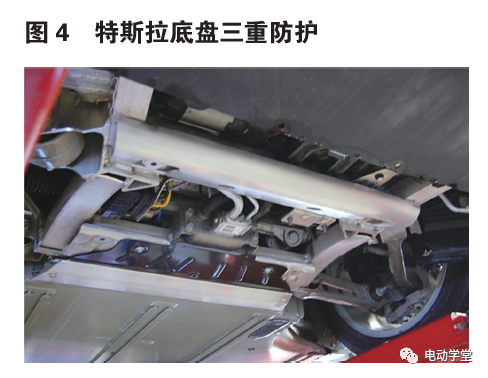
电芯/模组在测试过程中无外部短路、无内部短路,允许电芯/模组外形结构发生变形,但无危害现象产生。允许电池系统产生结构性能变化(如模组、固定结构、支架、连接排、箱体结构与原状态比发生破损、断裂;冷却管路破坏除外),但无危害现象产生。测试后要求绝缘电阻值不小于500Ω/V。
3.2 托底安全设计
动力电池底面不受车身结构的保护,在整车刮底和底部球击工况下,容易发生较大变形并产生危害现象,为满足工况考察指标要求以及整包轻量化要求,可以考虑增加电池包防护梁和底护板。
3.2.1 电池包防护梁设计
整车刮底工况导致的电池包损伤主要集中在电池包前部区域。在动力电池包前布置一道防护梁(防护梁安装在车身上,其最下缘比电池包底面低10mm以上,与电池包前端的X向距离控制在100-150mm左右),能够有效保护电池。防护梁有圆管截面、矩形截面、三角形截面和平板型等多种形式,其中圆管梁工艺简单,成本低廉,刚强度好,应当是电池包防护梁的首选。

3.2.2 电池包底护板设计
整车刮底和撞底工况下,电池底面都有可能损坏,增加底护板是非常有效的防护手段。
底护板一般采用1.2mm左右厚度的钢板或者2mm左右厚度的铝板,需要涂装防石击涂层,也可采用非金属材料,如玻纤复合材料,料厚通常需要在3mm以上。
为保证防护效果和整车NVH对底护板模态的要求,还需要在底护板上设计合理的加强筋,且底护板两侧和前后都应有固定点,中部还应有不低于4个的固定点与电池底壳相连接。此外,底护板与电池包之间需安装密封圈以满足IPX7水密要求,否则底护板应设计多个泄水孔,以保证在涉水工况下底护板不发生破坏。
4 试验改进建议
文中所述的整车刮底试验和动力电池底部球击试验,都是要求试验后电池系统无爆炸、起火、析气、冒烟、漏液等严重危险现象出现,这只是对电池系统进行了托底安全性验证与要求,而电池的托底耐久性并没有得到充分评估与保证。
从用户角度出发,发生轻微托底事故时,既要保证动力电池的安全性,不能出现起火爆炸现象,也要保证动力电池的托底耐久性,电池要可以继续使用,不能存在安全隐患。
4.1 评价指标优化
对常见的、较为轻微的托底事故作为耐久工况保护,建议将整车刮底和电池包底部球击工况的考察指标设定如下:
a)加载后电池包壳体结构不破碎、无可见裂纹。
b)电池包壳体无明显变形(建议加载过程中壳体最大侵入量小于25mm,卸载后壳体永久变形量小于3mm)。
c)内部冷却系统和管线、插接件和芯体等无损伤。
d)动力电池功能正常,可继续使用。
4.2 底部球击试验方法改进
4.2.1 准静态加载
准静态加载是目前行业内普遍采用的试验方法,虽然不同厂家的评价指标各有差异,但基本类似,一般采用直径150mm的金属球头,以不高于1mm/s的挤压速度,挤压电池包底部薄弱位置,当挤压力达到20kN或者其它厂家设定的值时,停止挤压。
建议在当前基础上,增加挤压球头位移限制:采用直径150mm的金属球头,以不高于1mm/s的挤压速度,挤压电池包底部薄弱位置,当挤压力达到20kN时,停止挤压,或者当金属球头位移量超过25mm时,停止挤压,此时应判定试验不合格。
改进后的试验方法对动力电池的底面刚度提出明确要求,对电池底面达到一定承载力时的变形量加以约束。
4.2.2 刚性球冲击加载
准静态加载试验方法简单,可重复性强,但与实际托底事故有较大差异。实际托底事故以刮底和撞底为主,而通常撞底事故对电池包损害更大,因此,建议电池包底部球击试验由准静态加载改为刚性球冲击加载。
另外,汽车发生托底时,动力电池不同部位被撞击的概率不同,如图9示意,A区被撞击的可能性较小,B区被撞击的可能性较大,C区和D区最容易被撞击(本图仅为示意图,根据被撞击概率的不同进行区域划分,需要以大量的事故统计作为基础)。建议根据不同区域被撞击的概率不同,制定不同的试验方法和评价标准。
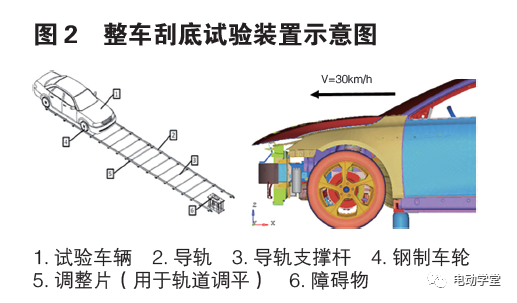
刚性球冲击加载具体试验方法是,使用一个直径150mm,质量10kg的刚性球,以初速度V0和撞击角度α,撞击电池包底部,对不同的区域,如表1所示,撞击能量、初速度、撞击角度各不相同。
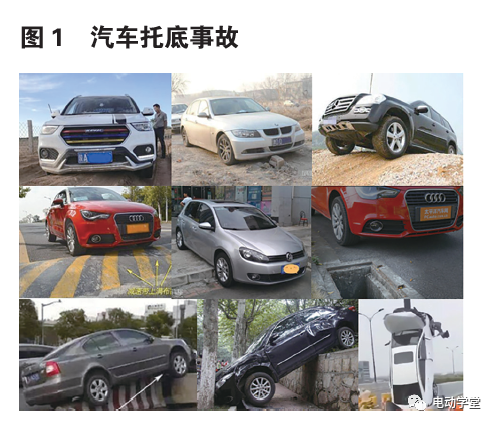
5 结论
常规托底事故较为常见,发生事故时,既要保证电池的安全性,不能出现起火爆炸现象,也要保证电池的托底耐久性,电池可以继续使用。
为此,在设计环节,可考虑增加电池包防护梁和底护板,加强电池包底部安全防护;在测试环节,建议探索使用刚性球冲击试验代替现行底部球击试验,同时增加球头位移限制,对电池底面达到一定承载力时的变形量加以约束。
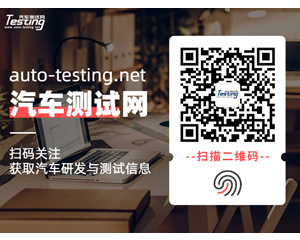
最新资讯
-
商用车及工程机械行业专场:NVH 及语音音频
2025-08-01 17:12
-
理想i8和重卡对撞测试引争议,东风柳汽发声
2025-08-01 15:52
-
艾德克斯IT-N2100 系列太阳能阵列模拟器
2025-08-01 15:43
-
ITECH重磅发布IT2705直流电源分析仪,重构
2025-08-01 15:34
-
现代汽车新一代混合动力系统:以技术革新引
2025-08-01 15:32