子午线轮胎凸块冲击特性仿真分析与评价
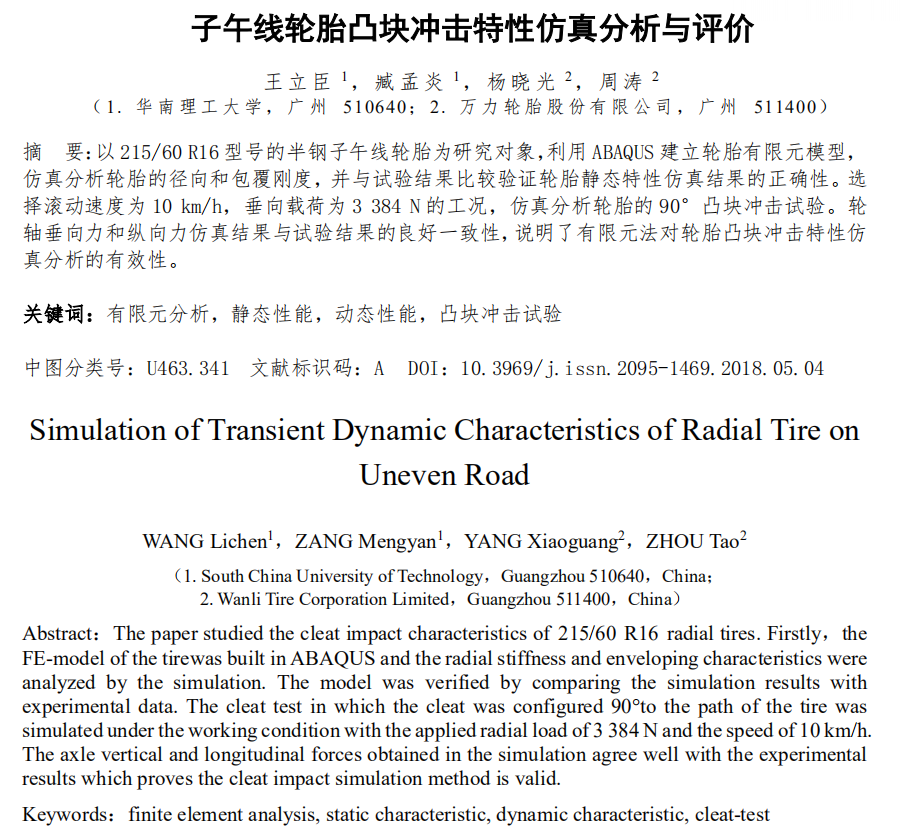
轮胎的减振作用作为整车减振系统的第一环节,其性能对整车的操纵性、舒适性有着重要的影响。在轮胎的设计阶段,不仅要考虑轮胎的静态特性,还应考虑轮胎的瞬态特性。凸块冲击试验是轮胎瞬态特性试验最为重要的试验之一[1] ,通过获取各个速度工况下轮轴力的响应,可以进行轮胎瞬态特性的评价。因此,对该试验进行仿真分析具有重要的工程意义。管迪华等[2] 系统介绍了用于轮胎凸块冲击特性仿真分析的多种模型,包括F-Tire模型、SWIFT模型、有限元模型等。费瑞萍[3]以F-Tire模型为基础,利用ADAMS软件对轮胎的凸块冲击特性进行了仿真研究。李俊浩[4] 基于刷子模型,利用ADAMS对轮胎瞬态冲击性能进行了研究。相比于其它模型,有限元模型可以详细表达轮胎的内部结构,具有计算精度高,获取结果信息详尽的优点。特别是近年来,随着计算机技术的高速发展,有限元理论不断完善,使用有限元方法研究轮胎瞬态冲击特性的效率大幅提升。WE等[5]和KAO[6]利用有限元方法对轮胎的瞬态特性进行仿真分析,但轮胎有限元模型过于简化,也没有考虑轮辋的影响。
本文以215/60 R16型号的轮胎为研究对象,利用有限元软件ABAQUS建立轮胎有限元模型,进行轮胎径向刚度和包覆刚度的仿真与对标。在确定轮胎有限元模型静态特性合理性的基础上,对轮胎凸块冲击试验进行仿真分析,并通过与对应试验结果的比较,确认轮胎瞬态性能有限元仿真分析方法的正确性。
1 轮胎有限元模型的建立
1.1 轮胎有限元网格模型
首先,在ABAQUS中采用轴对称方式建立轮胎二维有限元模型,并在二维模型中完成轮辋安装和轮胎充气(0.21MPa)。
然后通过*SYMMETRIC MODEL GENERATION,REVOLVE命令旋转生成三维有限元模型,并将二维计算结果进行传递。此时,二维轴对称橡胶单元转变为三维实体橡胶单元,单元类型由CAX4R与CAX3转变成C3D8R与C3D6。采用fluid-cavity方式定义轮胎内压,需要在胎圈与网格化的轮辋之间建立一层薄壳单元,使轮辋与轮胎内表面形成封闭腔。带束层、冠带层等橡胶部分内嵌的钢丝、尼龙帘线采用 rebar单元建模。旋转生成的轮胎三维有限元网格模型如图1所示。
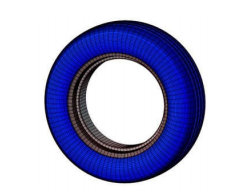
图1 轮胎三维有限元网格模型
1.2 轮胎材料参数定义
轮胎的材料主要由三部分组成,分别为橡胶、帘线钢丝和帘线尼龙。由于本文涉及轮胎的静态特性和瞬态特性的仿真分析,所以既要考虑橡胶的超弹性特性又要考虑橡胶的粘弹性特性。
橡胶部分的超弹性特性采用YEOH模型进行定义,其应变能密度三次方程[7]描述为:
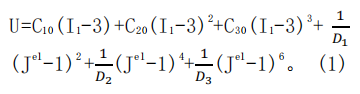
式中:U 为应变能密度;Ci0与Di 为材料常数,分别与橡胶的剪切特性与压缩特性有关;Jel为弹性体积比,不可压缩材料其值为1;I1为第一偏应变不变量。通过拟合橡胶单轴拉伸试验曲线可获得C10,C20,C30 等YEOH材料模型的参数值。采用归一化的prony级数[7]描述橡胶的粘弹性特性,时域归一化 prony级数描述为:

式中:gR(t)为归一化弹性剪切模量值;


钢丝帘线层与尼龙帘线层的材料参数与角度参数根据实测参数进行定义。
2 模型静态特性验证
轮胎的静态特性是研究瞬态特性的基础,考虑到凸块冲击试验中凸块尺寸比较小,轮胎越过凸块时会产生包覆凸块现象,所以轮胎有限元模型的静态特性评价包括径向刚度和包覆刚度。
2.1 径向刚度评价
径向刚度仿真方法[8],是在约束轮6个自由度的基础上,提升路面实现径向加载。提取轮辋中心点的径向支反力与路面位移,获得径向刚度曲线,如图 2所示。
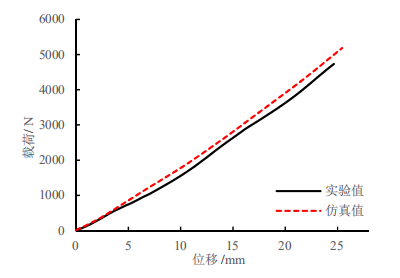
图2 径向刚度特性曲线图
载荷 F/N
位移 X/mm
由图2可知,轮胎径向刚度仿真结果与实验结果具有良好的一致性。
2.2 包覆刚度评价
轮胎的包覆刚度仿真方法[8] ,是首先约束轮辋6个自由度,然后提升路面实现轮胎径向加载后,单独提升凸块10mm,实现包覆刚度仿真分析。提取凸块提升阶段的轮辋径向支反力与凸块位移,获得图3所示的包覆刚度曲线。
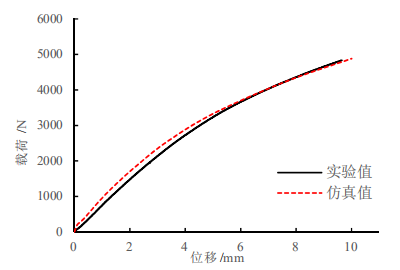
图3 包覆刚度特性曲线图
载荷F/N
位移X/mm
由图3可知,包覆刚度的仿真结果也与试验曲线具有良好的一致性。
以上分析验证了轮胎有限元模型静态特性的正确性,为后续轮胎瞬态特性仿真分析奠定了基础。
3 轮胎凸块冲击仿真分析和评价
3.1 凸块冲击试验
为了给仿真工作提供对标试验依据,在高速转鼓试验机上进行了轮胎的凸块冲击试验。转鼓试验机的原理如图4所示。
试验机转鼓的直径为2m,所以轮胎在转鼓上的越障响应可以近似模拟轮胎在水平路面上越过障碍物[9] 。转鼓中心A,轮胎中心B以及系统固定点C位于一条直线上,由转鼓转动驱动轮胎转动。安装在转鼓上的凸块尺寸为25×25 mm,足够的刚度保证与轮胎冲击时不发生明显变形。
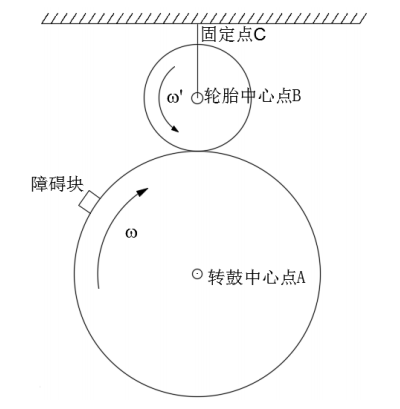
图4 转鼓越障试验机原理示意图
轮胎凸块冲击试验方法如下:
(1)将轮胎安装在轮辋上进行充气,充气压力为0.21MPa。静止5h 后,将轮胎安装在转鼓试验台上。
(2)参照图4,向转鼓中心方向移动轮辋,实现3384N 的径向加载并记录此时轮辋的位移量,然后释放位移以清除轮胎与转鼓之间的法向载荷。
(3)将凸块安装在转鼓上,转动转鼓使其表面切向速度达到10km/h,再移动轮胎直到轮辋的位移达到第二步中记录的位移值后,约束轮辋中心的垂向自由度。
(4)待轮胎进入自由滚动状态后,提取多个连续周期的轮胎轮轴力,取平均值获得轮轴力的时间历程即为轮胎凸块的冲击响应。
3.2 凸块冲击试验仿真方法
路面与障碍物采用解析刚体建模,并且将凸块固定在路面上。为提高仿真分析精度,对可能与凸块接触的部分轮胎网格进行了周向细化,以此建立的轮胎滚动越障仿真模型如图5所示。
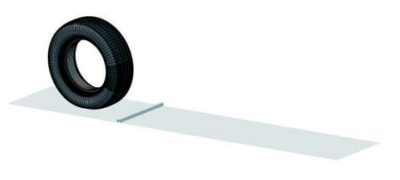
图5 轮胎滚动越障仿真模型
轮胎瞬态特性仿真分析需利用ABAQUS软件的显式求解方法。在轮胎显式滚动分析之前,采用ABAQUS/Standard中的稳态传输功能,利用拉格朗日- 欧拉混合算法,获得轮胎以特定速度滚动的自由状态[10] ,作为显式滚动仿真分析的初始条件。
在稳态传输分析模型中,用TRANSPORT VELOCITY选项定义轮胎材料通过模型网格的转动速度,用MOTION选项定义移动参考坐标系的水平运动速度,即轮胎的平动速度[11] 。进行一次制动与驱动分析,获得此过程中轮胎所受摩擦力为0或者轮胎纵向力为0时对应的转速,即轮胎自由滚动转速[12] 。在滚动速度为10km/h、垂向载荷为3384N的条件下,求得自由滚动角速度为 8.61rad/s,如图6所示。
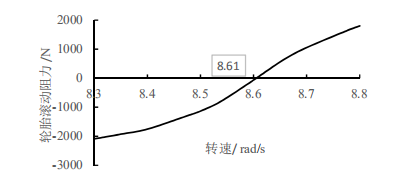
图6 在不同转速下的滚动阻力
轮胎滚动阻力F/N
转速ω/(rad·s-1)
获得轮胎的自由滚动状态后,通过数据传输(*import 关键字)功能将轮胎的自由滚动状态传递ABAQUS/Explicit中。
此时,轮胎在初始阶段即为特定速度的自由滚动。轮胎越障仿真分析流程如图7所示。
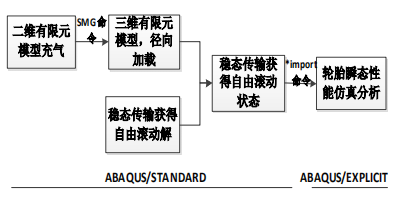
图7 轮胎越障仿真分析流程图
3.3 仿真结果及评价
采用图7的分析流程,进行在10km/h工况下的轮胎越障仿真分析,并从分析结果中分别提取轮胎越障过程的轮轴纵向力和垂向力。
轮胎越障过程的轮轴纵向力和垂向力的仿真与试验结果如图8所示。
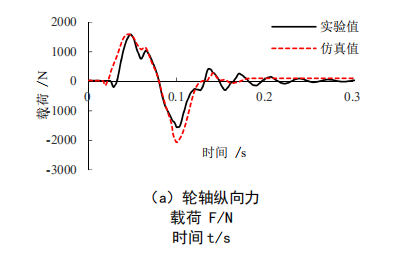
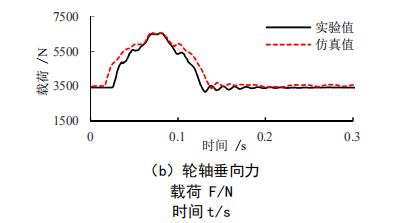
图8 轮胎越障过程的轮轴力时间历程
由图8可知,轮胎越障过程中,轮轴纵向力经历了一个周期类似正弦波的振动,而轮轴垂向力表现为半个周期的正弦波振动。轮轴垂向力与纵向力的仿真结果与对应试验结果基本一致,说明了轮胎瞬态特性有限元仿真分析方法的有效性。
4 结论
4.1 凸块冲击试验
首先,利用ABAQUS建立了轮胎有限元模型,使用有限元隐式分析方法进行了轮胎静态特性的仿真,通过刚度试验验证了轮胎静态特性的合理性。然后,使用有限元显式分析方法,对轮胎凸块冲击试验进行了仿真分析和评价。轮胎越障过程中,轮轴纵向力和垂向力时间历程与试验结果高度一致,说明了轮胎越障现象有限元仿真分析方法的有效性,为整车越障过程有限元仿真评价提供了重要基础。
参考文献
[1]DORFI H R. Tire Cleat Impact and ForceTransmission: Modeling based on F-TIRE and Correlation to Experimental Data[C] //SAE Technical Papers,2004-01-1575.
[2]管迪华,范成建. 用于不平路面车辆动力学仿真的轮胎模型综述 [J]. 汽车工程,2004,26(2):162-167.
GUA Dihua,FAN Chenjian. A Review of Tire Models for Vehicle Dynamics Simulation on Uneven Road [J]. Automotive Engineering,2004,26(2):162-167. (in Chinese)
[3]费瑞萍. FTire轮胎模型的仿真分析及试验研究[D]. 吉林:吉林大学,2011.
FEI Ruiping. Simulation Analysis and Experiment Study of FTire Model [D]. Jilin:Jilin University,2011. (in Chinese)
[4]李俊浩. 基于刷子模型的不平路面轮胎高频动态特性研究 [D]. 吉林:吉林大学,2006.
LI Junhao. Study Tire High Frequency Dynamic Properties based on Brush Model to Road Unevenness [D]. Jilin:Jilin University, 2006. (in Chinese)
[5]WEI Chongfeng,OLATUNBOSUN O A,YANG Xiaoguang. A Finite-element-based Approach to Characterising FTire Model for Extended Range of Operation Conditions [J]. Vehicle System Dynamics,2017,55(3):295-312.
[6]KAO B G. Tire Transient Analysis with an Explicit Finite Element Program [J]. Tire Society,1997,25(4):230-244.
[7]GHOSH P,SAHA A,BOHARA P C,et al. Material Property Characterization for Finite Element Analysis of Tires [J]. Rubber World,2006, 233(4):22-26,31.
[8]臧孟炎,许玉文,周涛. 三维非线性轮胎的五刚特性仿真 [J]. 华南理工大学学报 (自然科学版),2011,39(1):129-133.
ZANG Mengyan ,XU Yuwen , ZHOU Tao. Simulation Analysis of 3-D Model Nonlinear Tire’s Five Stiffness [J]. Journal of South China University of Technology ( Natural Science Edition),2011,39(1):129-133. (in Chinese)
[9]张绍国,高峰,徐国艳,等. 汽车轮胎与转鼓的滚动特性分析 [J]. 汽车工程2013,35(4):341-346.
ZHANG Shaoguo, GAO Feng, XU Guoyan, et al.An Analysis on the Rolling CharacteristicsBetween Tire and Dynamometer Drum[J]. Automotive Engineering,2013,35(4):341-346.(in Chinese)
[10]TAHERI S,SANDU C,TAHERI S. Finite Element Modeling of Tire Transient Characteristics in Dynamic Maneuvers [J]. Journal of Wildlife Management,2014,79(2):195-210.
[11]Abaqus,Inc.Abaqus Example Problems Manual,Version 6.13 [M]. Netherland:Abaqus,Inc.,2009.
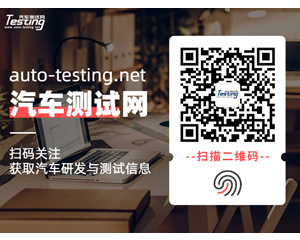
最新资讯
-
商用车及工程机械行业专场:NVH 及语音音频
2025-08-01 17:12
-
理想i8和重卡对撞测试引争议,东风柳汽发声
2025-08-01 15:52
-
艾德克斯IT-N2100 系列太阳能阵列模拟器
2025-08-01 15:43
-
ITECH重磅发布IT2705直流电源分析仪,重构
2025-08-01 15:34
-
现代汽车新一代混合动力系统:以技术革新引
2025-08-01 15:32