侧面碰撞防护中B柱设计概述
目前针对侧碰事故的评价工况主要有NCAP体系下的MDB/AE-MDB工况及IIHS/C-IASI体系下的MDB工况。各工况中壁障形式、冲击能量有所差异,但总体碰撞形式类似,均为模拟十字路口出现的垂直碰撞事故。该工况重点考察车辆的侧面结构尤其B柱刚度。

图1 NCAP/保险体系侧碰工况(来源SafetyCompanion-2020)
在热成型技术应用之前,车辆B柱一般采用高强度冷冲钢材料,并且为了满足开发要求,材料厚度一般都在1.8mm以上。这种设计一方面会带来较大的车身重量,另一方面大厚度高强钢的冷冲压成型工艺困难,成型过程中容易产生一系列问题。
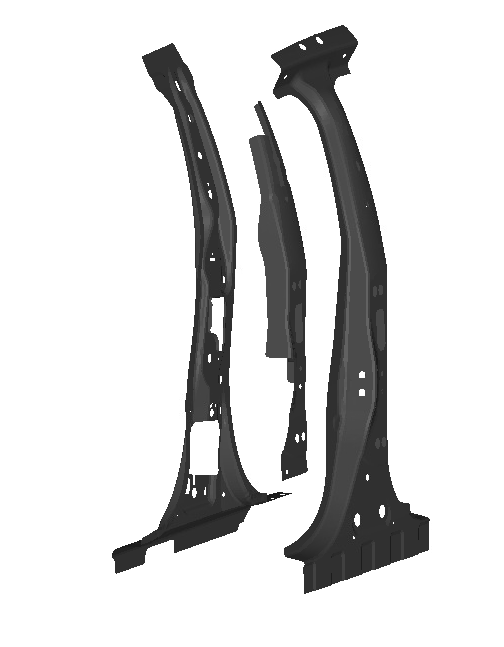
随着热成型技术的成熟,热成型钢在汽车中开始被广泛应用。
热成型B柱的应用对于NCAP及保险指数中侧碰工况的性能改善效果明显,它可以极大提升车辆侧面刚度,减小乘员舱变形,从而保护乘员安全。同时它也克服了高强钢冷冲压成型中的回弹、开裂等诸多问题,且轻量化效果显著。目前整车中多以普通等厚热成型的应用为主。
热成型B柱的广泛应用带来性能提升的同时,也带来新的问题。一方面,热成型整体强度较大,理想的变形模式不易实现。在日益严苛的侧碰工况中,靠增加加强板控制变形模式并不容易,且性价比不高。另一方面,热成型材料延伸率急剧下降,在大变形区域很容易出现焊点处脆化发生裂纹导致结构失效的问题。这些问题在难度不断升级的侧碰工况中(如60AE-MDB、下一代IIHS MDB等)变得愈发常见及突出。
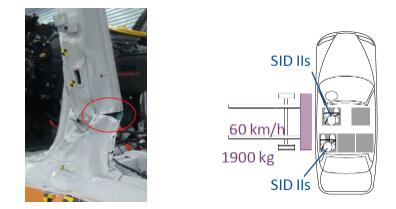
图3 热成型B柱失效 图4 IIHS MDB(2022)工况(来源SafetyCompanion-2020)
针对以上问题,目前也出现了一些新的解决方案,比如补丁板(B柱外板与补丁板预点焊,然后一体成型),差厚板,激光拼焊板,硬度分区的热成型(软区设计)等,目的是通过材料厚度或强度的差异化设计,使B柱下方更容易变形吸能,上方则仍保持足够的刚度,以控制B柱整体达到较理想的变形模式。
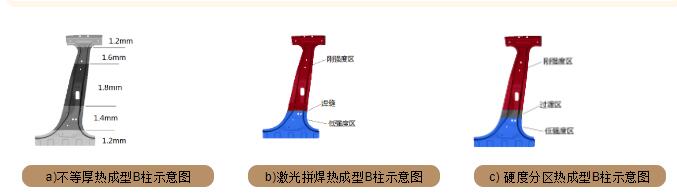
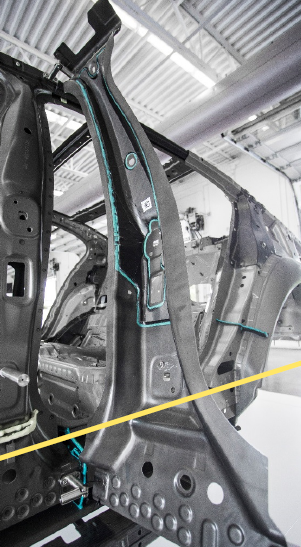
图6 BMW 7系碳纤维复材B柱加强板(来源EuroCarBody 2015)
除了传统的金属材料,增强型复合材料的身影也渐渐出现在车辆重要传力结构中,如碳纤维复合材料B柱加强板等。不难想象,随着材料技术的不断发展和轻量化需求的进一步深化,越来越多的轻量化新材料将在车身结构中得以应用,伴随而来的可能是一些新的问题及新的解决方案。
变化时刻在发生,但一成不变的是汽车安全人守护乘员生命安全的初心。
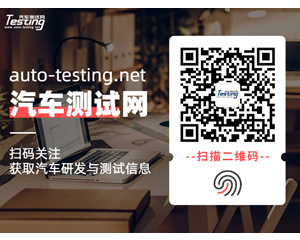
最新资讯
-
商用车及工程机械行业专场:NVH 及语音音频
2025-08-01 17:12
-
理想i8和重卡对撞测试引争议,东风柳汽发声
2025-08-01 15:52
-
艾德克斯IT-N2100 系列太阳能阵列模拟器
2025-08-01 15:43
-
ITECH重磅发布IT2705直流电源分析仪,重构
2025-08-01 15:34
-
现代汽车新一代混合动力系统:以技术革新引
2025-08-01 15:32