碳纤维复合材料疲劳寿命预测流程
关键词:碳纤维复合材料;力学性能测试;寿命预测流程
0 引言
CFRP,全称为Carbon Fiber Reinforced Plastics。碳纤维复合材料因其优异的力学性能,在诸如航天航空、能源建筑、军事工业等领域得到了越来多的重视和应用。而碳纤维复合材料相较于金属钣金材料,其在耐腐蚀、耐疲劳、比强度、比模量等方面的优势,也在汽车设计领域受到越来越多的青睐。
碳纤维复合材料的应用,也成为了汽车厂商在进行如轻量化、清洁能源使用探索等前沿应用领域中所不可缺少的环节。虽然碳纤维复合材料有诸多优势,但因其设计影响因素较多,尤其在疲劳载荷作用下的失效形式多样而复杂。由于其复杂的失效形式和实际载荷的多样性,建立碳纤维复合材料的疲劳寿命预测模型,便具有了其实际的工程应用价值和意义。本文基于准静态和疲劳力学性能试验,研究了不同载荷模式下的失效行为,进而基于Kawai CLD模型研究了碳纤维复合材料疲劳寿命预测方法,提出了横幅和变幅载荷作用下的碳纤维复合材料结构疲劳寿命预测流程,为后续结构设计提供了理论基础。
1 试验材料制备
由于碳纤维复合材料典型的拉压不对称及各向异性的特征影响,其力学性能因其层内力学性能呈现出特有的复杂性。所以目前的研究往往采用碳纤维复材的疲劳寿命曲线来描述这种疲劳行为,也是本次试验分为准静态和疲劳两部分的原因所在。
1.1 材料选取
碳纤维复合材料由基体和增强相所构成。针对其主要的成型工艺,一般按织造类型可大致分为:碳纤维无纺布、碳纤维预浸布、碳纤维编织布、碳纤维针织布等。这些不同种类的碳纤维材料的力学性能可参考图1所示。
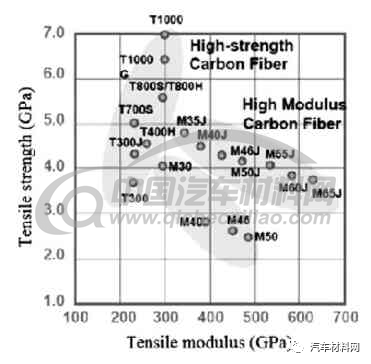
图1 各类碳纤维力学性能
样片取自单独制备的碳纤维平纹机织布上。碳纤维的单束选用3k纤维丝的型号,基材选用环氧树脂,其增强相及其基体材料的基本性能可参见表1。
表1 碳纤维和基体力学性能

1.2 样片制备
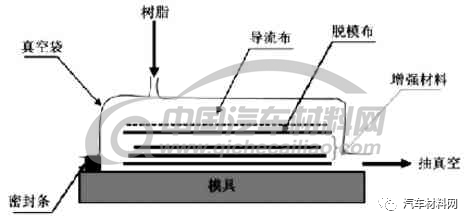
图2 真空导入工艺
作为样片基体的样布考虑到综合成本及成型复杂度,采用了常规的真空导入工艺进行。其导入工艺见图2所示。其基本原理为在模具上使用真空袋,当袋中的空气被抽取走时,使模具的型腔形成了一个负压,然后再通过预设的管路使树脂进入到纤维层中浸润。注入成形后,待树脂凝胶并脱模。在80℃下烘烤硬化5个小时,即可得到碳纤维复合材料层合板的制品。
表2 碳纤维和基体力学性能
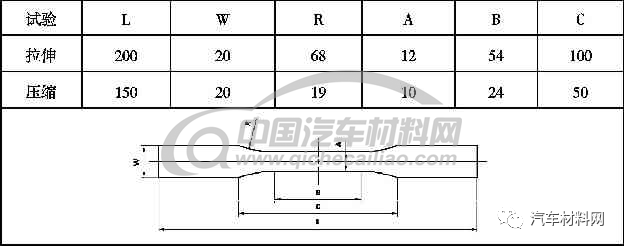
经如上步骤得到的复合材料样板,密度为1.47g/cm3,碳纤维的体积分数为45%。试验所需的样片尺寸主要参考标准ASTM D3039[2]及ASTM D3410[3]为主,采用水切割的方式从已制备的样片上裁取。为了满足试验机的加持需要,同时兼顾到准静态试验和疲劳试验的要求,用于拉伸试验和压缩试验的样片尺寸并不完全相同。因为考虑到尽量避免在压缩测试过程中可能出现的屈曲问题,所以压缩试验样片的长度比拉伸试验的样片缩短了 50mm。样片的整体形式采用的是哑铃状,其具体裁剪尺寸如表2所示[3, 4]。
2 力学性能试验
2.1 准静态力学性能试验
准静态力学及疲劳力学性能试验均通过液压力学试验机、机械式引伸计及激光引伸计等试验设备构成的测试系统完成。其中机械式引伸计用于测量样片的纵向变形,激光引伸计用于测量样片的横向变形。对于准静态力学性能试验,设计为 0°方向的拉伸为沿着样片轴线方向进行载荷的加载。压缩载荷测试的方向同样沿着轴向进行,加载的速率的均设定为 0.4mm/min,所有的拉伸机压缩测试的载荷均加载到零件出现失效破坏位置。另外,每组测试进行三个样片的有效数据,将采样的均值作为测试结果。0°的拉伸结果记录于表3。
表3 0°方向拉伸试验结果
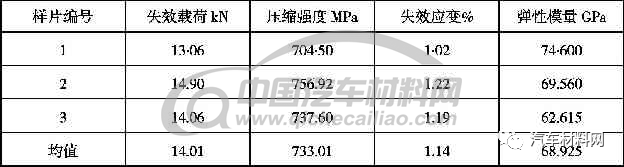
0°方向的压缩测试结果记录与于表4,由结果还可分别得到0°拉伸和压缩的均值。
表4 0°方向压缩试验结果
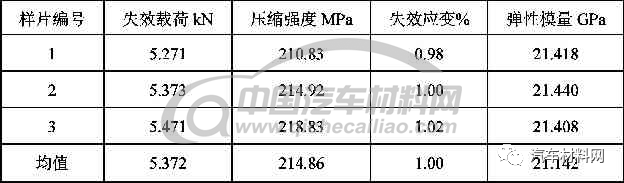
根据试验完成后的失效样片可以直观的观察到:拉伸样片的失效形式呈现出典型的脆性断裂特征。其断裂平面上的裂纹基本沿着加载方向的法向扩展,断口处有少量的纤维束被拉出(参见图 3a)。相对应的压缩样片的失效形式呈现为剪切断裂特征,其断裂平面的裂纹沿着与加载方向呈一定角度伸展,断口处能看到较为明显的分层剥落(参见图3b)。
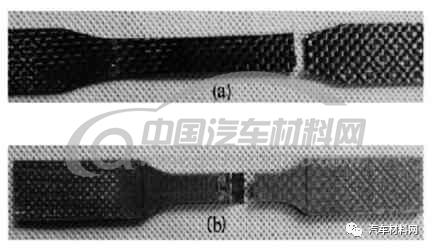
图3 准静态试验失效拉a.拉伸b.压缩
2.2 疲劳力学性能试验
因为损伤形式的多样性影响,这些失效形式的耦合作用使得碳纤维复合材料的疲劳失效与现有汽车产业使用的常规钣金材料有着很大的不同。以疲劳失效导致的裂纹为例,传统金属的裂纹扩展形式较为单一,而碳纤维复合材料的疲劳失效往往体现为裂纹场的扩展形式。所以疲劳测试的规划按照其物理意义,以一个加载周期为表征且用一个波形来表示。整个疲劳力学性能因规划为主要针对加载频率和碳纤维复合材料的疲劳寿命之间的影响关系。所以基于相同应力水平下,针对本文的碳纤维复合材料的样片进行不同加载频率的恒幅疲劳测试实验,其加载频率分别为:1Hz、5Hz和15Hz,与之相对应的疲劳性能试验可以按照典型的应力比分为拉伸载荷疲劳力学试验(R=0.1),压缩载荷疲劳力学试验(R=-0.5),其中拉伸载荷疲劳试验分为0°和45°两个方向进行,压缩疲劳试验为 0°方向进行。这些试验中,其测试样片与准静态力学试验所采用的相同。测试环境的设定根据 ASTM D3479标准模拟室温进行,温度设定在 20±5℃,湿度设定在45±5%。
在应力比R=0.1的应力水平下共进行了不同加载频率下的疲劳寿命试验。每组试验进行3个寿命样本的测试,试验结果如表5所列。本文所采用的碳纤维复合材料的疲劳极限为236MPa,其对应的最大应力与抗拉强度的比值(

表5 R=0.1疲劳力学试验结果
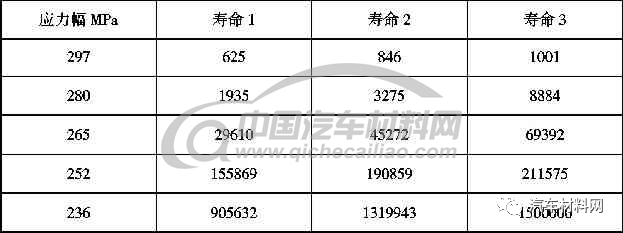
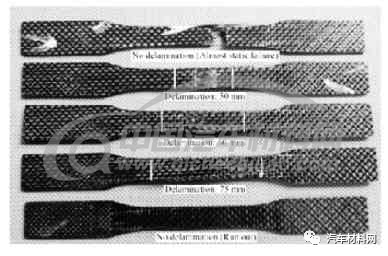
图4 R=0.1疲劳力学试验样片失效
试验后的样片图片可参见图 4,从失效样片的断口可以看出,由于不同的加载载荷所导致的应力水平不同,对于最高循环应力水平在疲劳循环的应力峰值(650MPa,相当于90%的抗拉强度)的失效样件,其断口呈脆性断裂的特征且有部分纤维束被拉出。而对于最低循环应力水平在疲劳循环的应力峰值(520MPa,相当于70%的抗拉强度)的失效样件,并未出现宏观失效。而其他几级应力水平的样片,分别出现了部分纤维断裂乃至分层失效等宏观表征。
应力比 R=-0.5的应力水平下共进行了不同加载频率下的疲劳寿命试验。每组试验进行3个寿命样本的测试,其试验结果如表6所示。
从试验后的样片图5可以看出,除了一组试样没有出现断裂的疲劳失效(对应于最低循环应力水平)外,其余几组试样都不同程度的出现了与准静态压缩试验后相类似的失效模式,即试样的断面与加载方向都呈现出了一定的角度。
表6 R=-0.5 疲劳力学试验结果
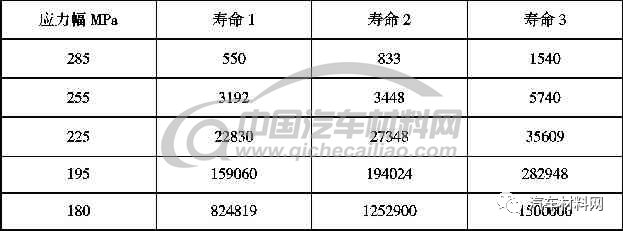
应力比 R=-0.5下的材料疲劳极限(180MPa)小于应力比R=0.1疲劳载荷下的疲劳极限(236MPa),即此碳纤维复合材料的拉伸疲劳性能要好于其压缩性能。
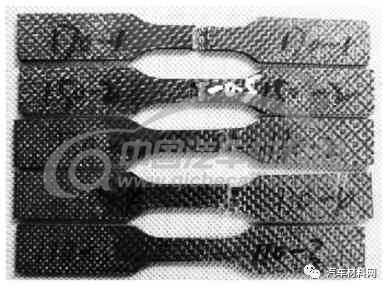
图5 R=-0.5 疲劳力学试验样片失效
3 恒幅疲劳寿命预测研究
由于碳纤维复合材料其疲劳失效形式具有复杂性,其影响因素不仅有复合材料本身层叠成形的原因,同时其疲劳性能也受制于复合材料铺层方向与载荷方向的角度。对于实际载荷工况为变幅的情况,需要基于恒幅载荷来将工况分析进行初步的简化,即本文针对碳纤维复合材料的疲劳寿命预测研究基础。
CLD(Constant Life Diagram)即恒幅寿命图,多作为对碳纤维复合材料进行材料疲劳寿命预测的工具。因为碳纤维增强复合材料往往具有各向异性的力学性能,所以基于本文已经进行了的准静态力学性能试验和材料疲劳寿命试验所获得的弹性模量、断裂强度及断裂应变等结果,采用CLD方法作为材料疲劳寿命预测的工具。典型的CLD模型如图6所示,其主要参数分别为应力比R、循环平均应力σm、循环应力σa等。横轴表示平均应力,纵轴表示应力幅值。上半平面被分为三个区域,从左至右分别为压-压载荷区(C-C)、拉-压载荷区(T-C)和拉-拉载荷区(T-T)。各区域的边界射线(从原点出发)代表特定应力比R的S-N曲线。而连接不同应力比下的S-N曲线上相同的寿命点,即可得此应力比下的恒幅寿命曲线。
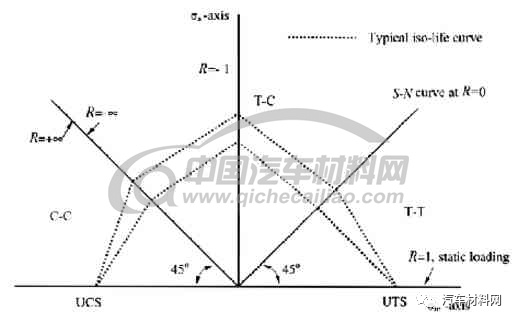
图6 典型恒幅寿命图
根据以往的文献报道,得到业界认可度较高的CLD模型主要分为:Goodman[5]、分段线性[5]、Kawai[6]。本文基于已有的研究,选取精度相对较高的Kawai模型作为本文预测碳纤维复合材料恒幅疲劳寿命的主要方法。
Kawai CLD模型以其发明者 Kawai而命名,又被称为CFL(anisomorphic constant fatigue life diagram)。该模型的使用特点为,首先定义了一个应力比R的临界值作为区域的分界线。进而在此应力比临界值两侧,再根据实际分析的需要,进一步细化出一到两个区域。通过连接已知S-N曲线上的等寿命点,即可得到此CFL模型的等寿命曲线(其方程如下公式所示)。
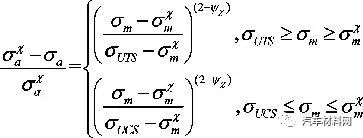
式中临界应力与S-N曲线的比值




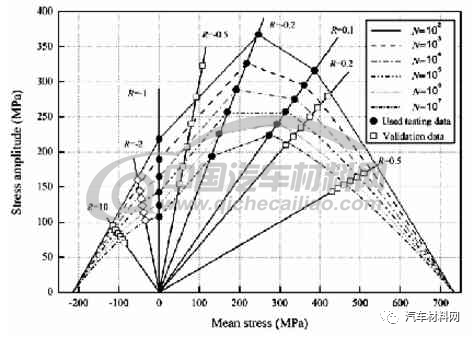
图7 基于CFL模型结果
基于图7所给出的CFL预测曲线,可实现对于任意横幅载荷下的碳纤维复合材料结构疲劳寿命的预测。
4 变幅疲劳寿命预测研究
本文通过准静态及疲劳性能力学试验、恒幅载荷预测模型应用为先导,同时基于以往的研究和积累,结合S-N曲线、变幅载荷处理、有限元模型分析及损伤累计准则等方法步骤,提出一套针对碳纤维复合材料变幅载荷疲劳寿命预测的流程(如图8所示)。
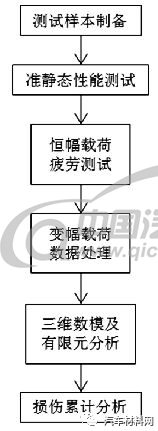
图8 变幅载荷流程图
包括了如下几个方面:
1)样片制备:其中包括了对于样片的纤维丝束选择,基材的选型及样片的成型工艺选择等方面;
2)准静态性能测试:通过此性能测试,可获得,如弹性模量、泊松比和比强度等性能参数,可作为后续的数值输入;
3)恒幅载荷疲劳性能测试:此试验的目的是为CLD模型获得典型应力比的S-N曲线,进而用于预测恒幅载荷疲劳寿命;
4)变幅载荷数据处理:使用如雨流计数法对变幅载荷进行修正处理,进而得到恒幅的载荷图谱(如图9所示);
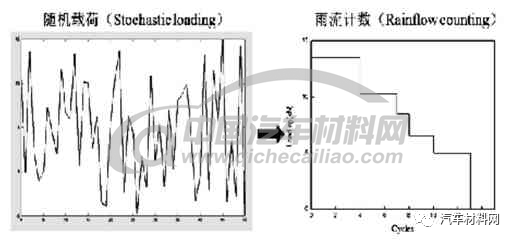
图9 雨流计数处理变幅载荷
5)三维数模及有限元分析:利用如Catia等建模软件得到碳纤维复合材料的三维模型数据,并根据设计要求完成有限元模型和静态失效准则预测结构的应力应变响应;
6)损伤累计分析:利用线性P-M准则,对系列恒幅载荷图谱的结构响应进行损伤统计,并最终得到总疲劳损伤值和寿命。
5 结语
本文提出了一套基于材料样片试验和 CLD预测模型为基础的碳纤维复合材料疲劳寿命分析预测的流程,可用于复合材料结构承受复杂实际载荷的工况,进而为碳纤维复合材料结构设计时,提供了一套疲劳分析流程方法。
来源:期刊-《汽车实用技术》;作者:张健,籍庆辉
(上海汽车集团股份有限公司前瞻技术研究部)
- 下一篇:路躁的优化该如何去考虑?
- 上一篇:一种平台化小偏置碰撞结构优化设计方法
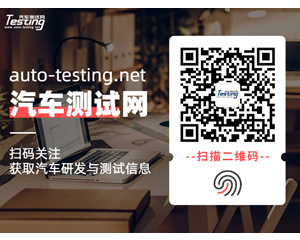
最新资讯
-
商用车及工程机械行业专场:NVH 及语音音频
2025-08-01 17:12
-
理想i8和重卡对撞测试引争议,东风柳汽发声
2025-08-01 15:52
-
艾德克斯IT-N2100 系列太阳能阵列模拟器
2025-08-01 15:43
-
ITECH重磅发布IT2705直流电源分析仪,重构
2025-08-01 15:34
-
现代汽车新一代混合动力系统:以技术革新引
2025-08-01 15:32