来源|制冷与空调 电动汽车是未来汽车发展的重要方向,随着技术的进步,电动汽车电机与电机驱动器的功率密度越来越高,其工作温度必然上升,这会对电机的工作效率和寿命造成不利影响。驱动系统能够有效散热是电动汽车热管理的重要内容,也是电动汽车性能开发
电动汽车是未来汽车发展的重要方向,随着技术的进步,电动汽车电机与电机驱动器的功率密度越来越高,其工作温度必然上升,这会对电机的工作效率和寿命造成不利影响。驱动系统能够有效散热是电动汽车热管理的重要内容,也是电动汽车性能开发过程中需要重点关注的内容。若散热不理想: 冷却液温度可能会一直上升,从而触发驱动系统的热保护而限制动力输出; 即便冷却液温度稳定,但电机等动力输出部件处于非最佳工作温度,也会影响整车动力性及经济性。
目前,电动汽车驱动系统主要采用强制风冷与液冷2 种冷却方式,其中液冷效果较好。液冷系统主要由水箱、水泵、电机冷却外套、控制器冷却外套、散热器及水管等组成,若忽略系统中各部件的辐射散热,则电机及其控制器产生的热量主要由散热器散出。所以,散热器的性能直接决定整个冷却系统的性能,从而对整机性能产生重要的影响[1]。笔者主要研究如何保证驱动系统有效热平衡。 常规电动汽车驱动系统所采用的液冷系统(见图1) 主要包括由冷却管路依次连接在一起的散热器、水泵、电机控制器、DC /DC 及充电机二合一、电机、膨胀水箱等,其中冷却管路内充满冷却液,散热器上装有加强冷却的电动风机。
冷却液流经各发热部件吸收热量,然后流经散热器处与空气进行热交换。如果驱动系统所产生的热量不能被冷却液有效地带离并及时足量地传递给空气,冷却液的热量就会出现堆积,温度持续上升,致使电动汽车驱动系统无法达到有效热平衡。作为电动汽车唯一驱动部件的电机,其发热量来源于电机内的各种损耗,因此确定电机的发热功率实质上是确定电机的各种损耗。在电机的各种损耗中,绕组损耗和铁芯损耗是发热量的主要来源,这些损耗都转化成热能,使电机内部温度升高,电机的物理、电气和力学特性随之发生变化,当温度上升到一定程度时,电机的绝缘材料会发生本质上的变化,最终使其失去绝缘能力。因此,在冷却系统选型过程中,要明确驱动系统发热部件的散热需求,以更好地做匹配分析。本研究涉及发热部件的散热需求及温度要求如表1。
2. 2 散热器设计
对于冷却系统而言,散热器是除了电机以外最重要的器件,散热器通过风机加快空气流动带走冷却管中冷却液的热量,使冷却液温度下降。为了准确确定发热部件散热需求,并保证其更贴合车辆在实际使用过程中的状况,散热器散热量( Qw1) 采用加权法(额定散热需求× 70% +峰值散热需求× 30%) 计算。其中充电机只在充电时需要散热且需求散热量小,在选型计算中忽略其散热量。散热器使用一段时间后,受周边环境的影响,通过散热器的气流会产生分布不均匀的现象,再加上散热器自身老化等因素,散热器散热能力会减弱。因此,散热器的散热量需有一定的储备余量。一般储备系数(β)取1.10~1.25,轻型车取下限,中型车取上限。本冷却系统β取1.10,即2. 2.2 散热器芯体迎风面积( Ff1)
电机和电机控制器( MCU) 为主要发热源,根据二者额定功率(额定功率约70 kW) 利用式( 2)求解[1]:Ff1=(0.0027~0.003 4)×Nemax ( 2)2. 2.3 散热器冷却液( 水) 进出口温差( Δt水1)
散热器进出水温差( 等于系统温升)为Δt水1,由热平衡方程可得,
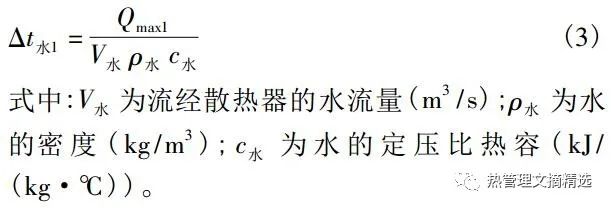
2. 2.4 散热器气液平均温差(Δt1)
根据水流方向,电机为最后一个发热部件,电机的出水温度即为散热器进水温度( t散进 ) 。而电机进水温度要求≤65℃,则根据上述电机散热量,利用式( 3) ,可得电机的进出水温差Δte。
2. 3 水泵匹配设计
水泵的主要功能就是加快冷却液在冷却管道中流动,以促进冷却液循环散热,因此水泵在冷却系统中是不可或缺的部件。2. 3.1 冷却系统水阻估算
冷却系统水阻为冷却水流经各个部件阻力之和,本冷却系统中冷却水主要流经水泵、冷却管路、电机、电机控制器、充电机及散热器。依据企业提供的相应零部件水阻测试结果可得DC /DC 及充电机二合一、电机及电机控制器水阻曲线,在水流量为10 L /min 时,水阻分别为2.4kPa、0.7 kPa和4.4kPa。冷却管路水阻依据相似车型冷却管路水阻取60kPa。综上所述,冷却系统水阻取为68 kPa。2. 3.2 水泵选型
根据上述计算结果,水泵选型主要依据流量10 L /min 和冷却系统水阻,确定水泵扬程需要不小于7 m。2. 4 风机风量分析
实现冷却系统的能量优化除元器件的合理布局外,风机的控制也是优化的重要内容。对于风机的优化除合理的参数配置,更重要的是控制风机的风量。2. 4.1 风量评估
风机风量( Va) 根据冷却系统应散出的总热量Qtot确定[5],即
在评估系统风量时,需要充分考虑冷凝器的最恶劣工况,根据经验,怠速状态时冷凝器工况最为恶劣,此时依据经验值,迎面风速须在3 m /s左右,冷凝器迎风面积约0.253m2,得到系统最低需求风量为0.759m3 /s。2. 4.2 风机静压计算
风机的供气压力,即静压,是根据冷却系统的类型、具体布置与结构确定的。由于类型、具体布置与结构的差异,风机需要克服的空气通道阻力不同。此处主要考虑怠速状态,冷凝器工况最为恶劣,迎面风速约为3 m /s。在该状态下,依据选型设计结果,散热器零部件供应商选取相似散热器做风阻试验,散热器风阻和冷凝器风阻的测试结果分别为40 kPa和53kPa。本系统匹配风机性能曲线见图2。
为验证系统设计选型结果,利用AMESim 仿真平台搭建电动汽车驱动系统所采用的冷却系统仿真模型,模型主要包括电机、电机控制器( MCU) 、水泵、风机等主要零部件[6]。3. 1 仿真工况
针对汽车在相对恶劣的山路爬坡工况 ( 车速60 km /h,坡度9% ) 进行模拟。车辆高温( 环境温度为40 ℃) 下满载运行,电池荷电状态( SOC) 运行到30% 为止,空调开至最高档且内循环模式。3. 2 仿真结果分析
利用AMESim仿真软件搭建驱动系统所采用的冷却系统仿真模型,如图3 所示。由图4和图5可以看出,电机和电机控制器的进/出水温度都处于比较合理的温度范围之内。
本试验研究的恶劣工况为所需冷却系统的散热量较大的长距离山路爬坡工况。试验在整车环境舱中进行(见图6) ,车辆在环境温度为40℃下满载运行,运行时间为电池荷电状态( SOC) 从80%一直运行,直至30%为止,空调开至最高档且内循环模式,并增加太阳辐射强度( 1 050 W /m2 ) 。环境舱模拟山路爬坡工况运行结束后,电机进/出水温度及电机控制器( MCU) 进/出水温度分别如图7和图8所示,可以看出,测试结束后,电机及电机控制器(MCU) 出水口温度分别约为54.5 ℃和51.5 ℃,该温度低于设计要求( 65℃及60℃) 。这说明冷却系统具有很好的散热性能,能够保证电机和其他发热部件的正常工作。
介绍了一种电动汽车驱动系统的冷却系统设计匹配思路,以驱动系统主要散热元件的散热需求为设计目标进行理论分析,为设计选型提供参考,有效减少设计工作量。利用AMESim 软件建立驱动系统冷却模型,进行一维仿真验算,再利用整车试验采集的温度数据对仿真结果进行验证对标。结果表明,通过前期有效的理论分析,在高温环境及较为恶劣的山路爬坡工况下,该冷却系统能够保证各部件有效工作,为电动汽车的可靠运行提供保障。———————————————————————————