某纯电动汽车电池包安装点结构设计
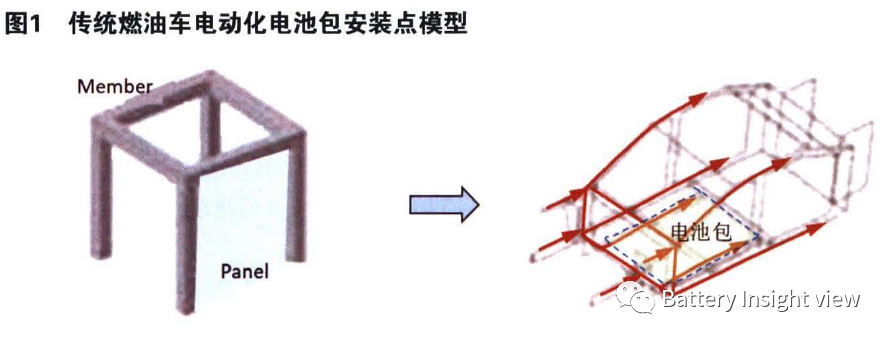
- 下一篇:某电动汽车动力电池挤压仿真与试验
- 上一篇:纯电动商用车电池热管理技术研究
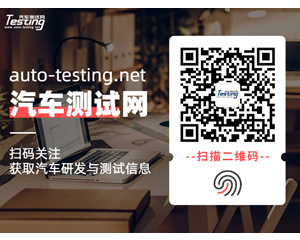
最新资讯
-
直播 | 如何对车载紧急呼叫系统进行测试?
2025-08-15 16:17
-
GB 45672-2025《车载事故紧急呼叫系统》标
2025-08-15 16:16
-
【展会邀约】置测全域,驱使未来 | HIOKI日
2025-08-14 16:31
-
直播 | 雅迅智联AECS解决方案
2025-08-14 16:29
-
AP多通道测试解决方案重磅升级 — 全面支持
2025-08-14 15:23