基于架构开发的汽车悬架控制臂优化设计
为有效解决汽车架构开发中悬架控制臂的疲劳耐久问题,研究了某架构项目后悬架下控制臂的设计优化方法。采用多体动力学、有限元方法、耐久评估、结构优化设计等技术,研究架构项目调试件参数对后下控制臂载荷和耐久性能的影响规律,找出架构带宽中对于控制臂设计最恶劣的参数组合,对其耐久性能进行仿真分析和优化,使其耐久性能可满足整个架构带宽的需求,并借助台架试验和整车路试对其疲劳寿命进行考核和验证。结果证明,文章提出的设计思路和方法有效,可拓展应用于其他底盘零件。
汽车行业的竞争日益加剧,为了把握高效率、高质量和低成本的开发与产品个性化间的平衡,各大车企均在重点研究整车架构的工程开发技术。汽车底盘悬架作为重要的架构零件,在设计阶段需充分考虑架构带宽对零件设计的影响,满足在架构平台上的共用性要求。文章基于某架构项目的后悬架下控制臂的开发工作,采用多体动力学、有限元方法、耐久评估、结构优化设计等技术,结合设计包络、标杆研究和设计制造经验进行控制臂的设计,采用仿真工具对其耐久疲劳进行预测分析并进行结构优化,利用台架对其耐久能力进行试验,并搭载整车路试完成疲劳耐久验证,进而实现架构项目控制臂的高效高质量设计开发。
1 架构项目控制臂开发简介
悬架系统为汽车底盘的重要组成部分,其与车身和车轮相连,汽车行驶时,承受来自车身的振动和路面激励等多重载荷。后悬架下控制臂是多连杆后悬架的重要受力部件,一般位于后悬架下方后侧,连接轮边和副车架,并承载减振器、弹簧和稳定杆等调试件,主要作用是承载垂向载荷并控制车轮运动时后轮前束和外倾的变化,因其布置空间受限,且受力复杂,路试中极易失效,其性能直接影响整车的安全性和可靠性。考虑架构平台的扩展能力,架构开发中多车型共用控制臂,但不同车型的调试件如弹簧、稳定杆等参数不同,底盘性能调试提出了稳定杆库、弹簧族的设计理念,较大地拓宽了底盘调试件的调试范围,而架构的调试带宽直接影响后悬架下控制臂的耐久性能,因此后下控制臂的设计需基于整个架构带宽,满足强度、刚度、耐久等零件设计要求,同时做到轻量化和低成本。
2 后下控制臂模型设计
本项目悬架形式为刀锋臂式四连杆后悬架,图1示出后悬架下控制臂装配关系图。后悬架下控制臂布置在副车架和车轮支架之间,同时为弹簧、减震器、稳定杆提供安装接口,为确定其设计边界,在CATIA里建立了后悬架的运动学DMU模型,并带入周边件。以下控制臂为参考,输出周边件相对下控制臂的运动包络,如图2所示。进而在CATIA装配模块下重新以下控制臂作为固定零件,将所获得的运动包络依次装配形成新的悬架模型,构成了下控制臂的空间包络约束。其中对下控制臂设计影响最大的是弹簧包络,本工作建立了精确的弹簧包络,保证下控制臂与弹簧之间的间隙,基于设计包络,结合设计经验及制造工艺经验,得到了下控制臂的参数化模型,如图3所示,后续基于此模型展开工作。
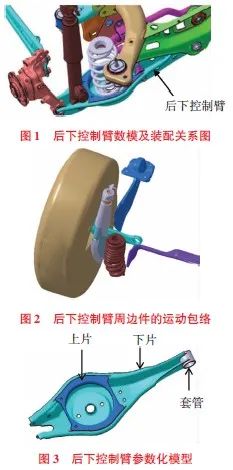
3 后悬架多体动力学模型
在项目开发前期,宜采用静态载荷工况用于底盘结构件静强度和疲劳的计算,指导零件设计优化。文章选用汽车行驶过程中的一些典型工况或工况组合计算悬架的载荷,如加速、制动、转弯、路障等,静态载荷主要包括垂向、纵向和侧向载荷。
为精确计算载荷,在ADAMAS/Car模块建立刚柔耦合的后悬架多体动力学模型,如图4所示。输入后悬架的各硬点坐标、建立各子部件、导入各柔性体、定义连接关系、输入弹簧刚度曲线和各衬套的刚度曲线等。为提高该动力学模型的精确性,副车架采用实际模型并进行柔性体处理,衬套参数采用实测刚度曲线。
根据后悬架动力学模型及理论受力载荷进行静载求解,由整车参数和标准静态载荷工况计算得到轮心六分力,最后将轮心力输入动力学模型,计算得到控制臂各硬点处的载荷。
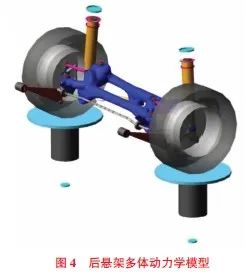
4 架构带宽对载荷的影响分析
影响悬架载荷的关键因素有以下4个方面:
1)轴荷;
2)硬点布置;
3)零件的质量、转动惯量和质心坐标;
4)柔性件参数:如弹簧刚度、辅簧刚度、辅簧间隙、减振器阻尼力、稳定杆直径、衬套刚度等。
在轴荷和硬点已定的条件下,调试件参数变化对载荷影响较大,不同调试件对底盘各结构件载荷影响存在不同的敏感方向。以对后下控制臂载荷影响敏感的弹簧刚度和稳定杆直径作为主要因素,研究架构带宽对载荷的影响规律,该架构项目根据整车操稳性能和平顺性能的目标值分解得到调试参数带宽,如表1所示。
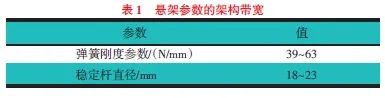
通过对多个疲劳工况和滥用工况的计算,得出调试参数对不同方向载荷的影响。图5~10示出部分工况的载荷计算结果,得出调试件参数对各向载荷的影响规律,可知弹簧刚度对垂向载荷影响较大,且弹簧刚度越大,垂向载荷越大;稳定杆直径对纵向载荷、侧向载荷和垂向载荷均有影响,且稳定杆直径越大,载荷越大。
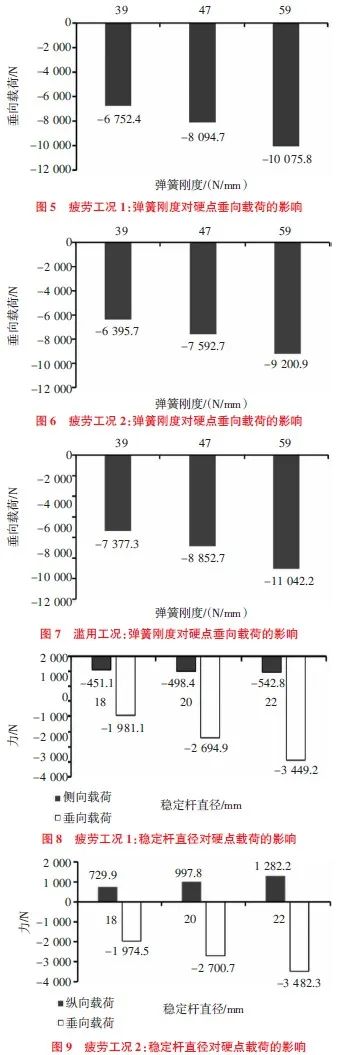
5 架构带宽对零件耐久性能的影响
不同弹簧刚度和稳定杆直径的组合,导致后下控制臂的各向载荷发生变化进而影响耐久性能。为研究架构带宽中调试参数对后下控制臂耐久性能的影响规律,进行了试验设计。针对不同参数组合定义DOE矩阵,采用不同参数组合下的载荷对后下控制臂数模进行耐久计算,最终寻求对后下控制臂耐久最恶劣的参数组合,作为耐久评估和结构优化的计算标准。因需在所有组合里筛选最恶劣工况且分析参数较少,文章采用全因子方法定义参数DOE矩阵。
底盘结构件主要的失效形式为疲劳失效,且为低周疲劳,因此在进行耐久评估时采用局部应力应变法进行损伤计算。根据损伤理论,在循环载荷交变作用下,零件疲劳损伤随时间逐渐累计,直至产生失效。Miner线形损伤理论认为每一段循环载荷都会产生对应的疲劳损失量,并对最终的疲劳极限有一定影响,即零件在经过一段不同循环载荷加载后即产生疲劳损伤。其表达式为:
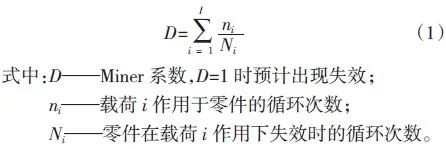
文章基于材料应变曲线及Miner理论,采取损伤计算方法评估后下控制臂耐久性能,并设定损伤值1作为疲劳上限。即通过有限元法求得零件所受应力,通过循环应力应变方程求得零件的应变,对于每一个循环周计算出零件各个区域的寿命,最后用Miner法则计算总疲劳损伤及寿命。
计算所有参数组合下零件的损伤值,结果如图11所示。可以看出调试参数对零件耐久的影响规律:弹簧刚度越大则零件损伤越大,稳定杆直径越大则零件损伤越大。而初始设计在整个架构带宽的调试参数组合里,不能满足全部零件疲劳损伤值小于1的耐久目标,其中对后下控制臂耐久影响最恶劣的参数组合为:弹簧刚度为63N/mm和稳定杆直径为23mm,需使用该参数组合下的载荷对后下控制臂进行设计优化,使其耐久性能满足整个架构带宽的要求。
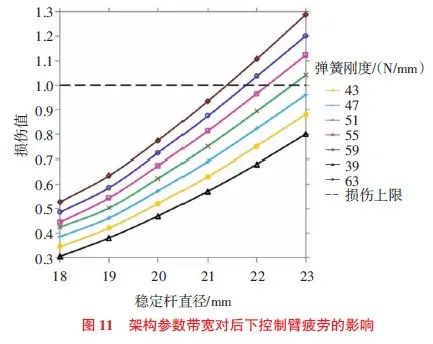
6 零件耐久优化
为了缩短计算时间以快速迭代,在耐久优化时,采用设计CAE的方法,在CATIAGPS模块计算模型在关键工况下的应力,通过对优化前后模型的应力对比,评判其优化效果,并对最终优化模型进行疲劳损伤和其他设计目标的验算。
基于初始模型典型工况的应力计算结果,如图12所示。结合应力分布和工程经验进行结构优化。为避免质量的大幅增加以及冲压难度增大,通过以下4个方面的措施进行设计优化以减小局部位置应力大的问题:
1)对上、下冲片进行板厚优化;
2)对上、下冲片的形面和走向进行优化;
3) 优化弹簧定位孔和漏水孔的位置和形状;
4) 在套筒附近翻边位置增加小的补片进行局部加强。优化后的模型,如图13所示。优化后零件应力明显降低,如表2所示。
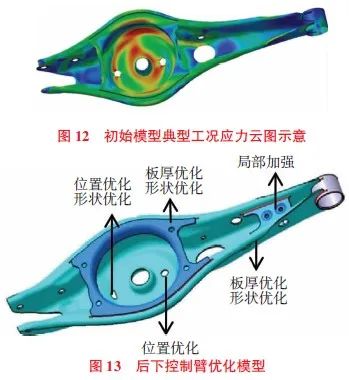
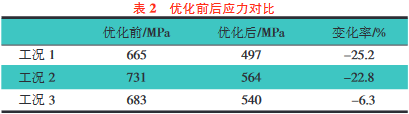
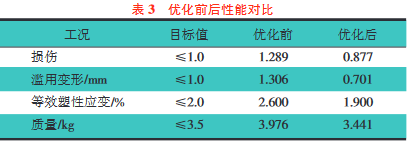
采用有限元方法对优化后的控制臂模型进行疲劳损伤、滥用变形、等效塑性应变等性能指标验算,满足设计目标值。优化前后的性能对比,如表3所示。
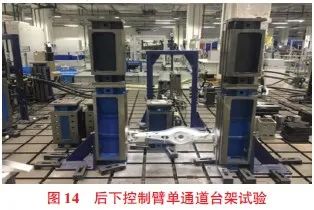
7 台架和路试验证
为实际验证后下控制臂的疲劳耐久性能,按照优化设计方案制成样件并开展耐久性能试验验证,底盘件的耐久性评估的试验方法分为试验室台架模拟试验和实车道路试验。
道路载荷谱是进行结构件耐久验证的有效方式,但路试采集的路谱信号很难直接用于零部件的结构疲劳台架试验,为了等效路试损伤并保证试验经济性,采用载荷块方法进行后下控制臂的台架试验。其原理是基于雨流计数统计法将道路采集时序数据转化为当量伪损伤程度的循环载荷,根据累计疲劳损伤、材料应力应变迟滞回线等原理,将汽车道路载荷谱转化为零件台架模拟试验加载谱。
文章实采汽车在试车场的路谱信号,基于以上方法,根据后下控制臂的受载特征,将实采路谱的轮心处载荷分解到后下控制臂,得到简化的多级载荷块,开发了后下控制臂的单通道台架试验,进行快速验证,零件通过单通道快速验证后,进一步搭载后桥系统多通道台架试验进行系统级的验证,在两侧轮心加载。零件级台架试验,如图14所示。系统级台架试验,如图15所示。在要求的试验循环里均无失效发生,验证了优化方案满足耐久性能。零件最终搭载多轮的实车路试,均无失效,满足设计目标。
- 下一篇:燃料电池商用车安全和热管理
- 上一篇:深度学习与汽车安全
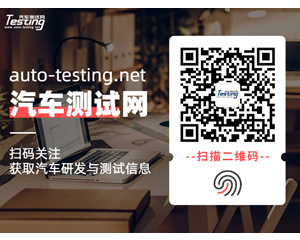
最新资讯
-
商用车及工程机械行业专场:NVH 及语音音频
2025-08-01 17:12
-
理想i8和重卡对撞测试引争议,东风柳汽发声
2025-08-01 15:52
-
艾德克斯IT-N2100 系列太阳能阵列模拟器
2025-08-01 15:43
-
ITECH重磅发布IT2705直流电源分析仪,重构
2025-08-01 15:34
-
现代汽车新一代混合动力系统:以技术革新引
2025-08-01 15:32