安全气囊织物发展现状
安全气囊一直是汽车行业及消费者关注的焦点之一,也是研究领域的难点。介绍了目前国内外汽车安全气囊织物的发展现状,包括了气囊织物的纤维原料、织物类型及各项性能要求。以安全气囊织物的发展历史为基础,分析了以聚酰胺纤维、聚酯纤维为主的原料选取、涂层对织物各方面性能的影响以及气囊在特殊工作环境下对织物结构、透气性、热学性能、力学性能的基本要求,并简要介绍了目前安全气囊织物的热点研究。
关键词:安全气囊;织物;纤维;涂层;发展现状
汽车的安全性能一直是人们关注的首要问题,安全气囊作为汽车部件中最为重要的安全部件之一,已成为迅猛发展的高新产业,是各国关注的研究重点。
根据汽车行业的调查报告,当汽车前部发生碰撞时,若汽车装有安全气囊,驾驶员死亡率明显更低,特别是大客车,死亡率降低 30%[1],能够有效减少交通事故伤亡。
全球安全气囊领域的知名企业有瑞典奥托立夫、日本高田、美国天合、德国采埃孚、美国百利得,产品市场份额也基本由这些企业瓜分。中国在汽车安全气囊领域的研发起步较晚,与国外安全气囊技术及产品相比尚缺乏优势,因而产品市场占有率一直较低。20 世纪初,瑞典奥托立夫率先在中国上海建厂,随后其他总成厂商和零部件供应商也纷纷来华,以奥托立夫为代表的跨国公司投资的企业占据了中国绝大部分的市场份额[1]。中国自主品牌方面主要为锦州锦恒、东方久乐和华懋科技等, 东方久乐是目前国内唯一掌握汽车安全气囊系统核心技术、拥有完全自主知识产权并实现产业化的本土企业。2018 年,已经申请破产的日本高田被宁波均胜集团收购,从此这个全球知名的安全气囊供应商就纳入了中国企业旗下。
本文将分别从安全气囊织物的纤维原料、安全气囊织物的类型及安全气囊织物的结构与性能要求这三个方面进行论述,简要介绍目前国内外汽车安全气囊织物的发展现状。
1 安全气囊织物的纤维原料
聚酰胺纤维
第一代气囊织物在 20 世纪 70 年代由美国通用汽车公司提出,以聚酰胺长丝纱为原料涂覆氯丁橡胶,然而实际使用证明,氯丁橡胶的涂膜耐用性差,涂层厚,涂层织物易变质,不便回收利用;第二代气囊织物将硅橡胶涂层附着于尼龙织物,环境变化时硅橡胶涂层可保持其特性不变,高温时性能仍很稳定,且硅胶涂膜具有润滑性,织物轻薄柔软[2];第三代非涂层气囊织物仍使用聚酰胺长丝纱生产,通过提高经纬纱密度,并采取后整理加工途径提高织物阻气性能;90 年代初产生的第四代气囊,是以聚酰胺纤维为原料的全成型安全气囊,在气囊的生产过程中一次性完成袋状加工,圆满解决了非涂层织物后期加工困难的问题。
由此可见,安全气囊织物发展的整个历史是以聚酰胺长丝纱为基础的,特别是锦纶 66,相比其它纤维原料,其性能表现更加理想。除最普遍的锦纶 66 外,锦纶 6 长丝也可作为安全气囊用原料,虽然其熔点、热焓更低[3],但其经特殊处理后制作的安全气囊与使用锦纶 66 相比,有较好的抗撕裂性和可折叠性,在冲击、老化和燃烧试验中的表现更优。
聚酯纤维
21 世纪初,随着非涂层气囊的发展,聚酯纤维也成为研究热点。高强聚酯长丝织物具有轻薄、强度高、耐化学性等优点,成本低,前后道加工更简便,易回收,且聚酯的回潮率比聚酰胺低,受湿度变化的影响不明显,相对不易变形,在 5~10 年后仍能保持较低的空气渗透率。德国 Hoechst 公司曾开发过一种高强聚酯丝,细度在 250~550 dtex 之间,织成的织物吸湿性较低,空气渗透性低,无需后整理就可直接用于生产安全气囊。
PA66、PA6、PET 的物理特性比较见表 1[4]。
表1 PA66、PA6、PET的物理特性比较

多组分原料
为改善气囊织物的综合性能,采用多组分原料也是一项行之有效的措施。
由不同组分或结构的多种纱线构成织物
例如在聚酰胺为主的织物中加入少量高伸长丝。日本东丽在以聚酰胺或芳族聚酰胺为主的织物中,加入重量比为 2%~3%,伸长率为 400%~1000%,线密度为 11.1~111 dtex 的聚氨基甲酸酯高伸长丝[4],大大提高了织物的机械性能,织物柔软性也更高。
由不同组分的纤维构成复合纱
用耐热性能好的纤维和热塑性纤维混合制成纱线,织成的织物在经过热整理后,透气性降低,织物既有较好的耐高温性能,也有较好的气密性。STRAHCE&HESS GMBH 曾采用耐热的间位芳族聚酰胺纤维与热塑性纤维混纺,在高温下用金属或玻璃划也不破裂。热纤维的应用有效解决了织物面密度降低却造成织物热容量降低这一问题。
由不同成分的聚合物构成复合纤维
聚酯的吸湿性比聚酰胺更低,聚酰胺的耐热性能更好,因此可以考虑将二者结合制成复合纤维, 聚酯作芯,聚酰胺作皮层,能够明显提升织物的尺寸稳定性和耐热性等性能。
2 安全气囊织物类型
根据是否有涂层,安全气囊可以分为涂层织物、非涂层织物和混合型气囊用织物。
涂层织物
氯丁橡胶是最早用于安全气囊的涂层原料,氯丁橡胶对外部环境的敏感性低,抗老化性能好,价格便宜,但氯丁橡胶受高热时分解产生有毒的氯化物气体,给织物带来酸性环境,使其脆化;在高温环境下易与强氧化剂反应,自身会发生老化,失去原有性能;从加工上考虑,氯丁橡胶与尼龙很难融合,且在尼龙织物上涂覆氯丁橡胶成本高昂。
20 世纪 80 年代,日本开始开发使用硅橡胶涂覆材料。硅橡胶具有优良的环境稳定性,和稳定的化学性能;耐磨、耐久性能好,触感好,便于折叠;硅橡胶耐极限热的能力强,比氯丁橡胶涂覆量小就可达到同样的耐热性[2]。
随着更深入的研究,液体硅橡胶材料各项性能有了进一步提升,其具有质量轻、折叠尺寸小、强度高、耐老化、成本低等特点,更适合生产。
非涂层织物
非涂层型安全气囊织物有缝制型和全成型两种,其通过织物本身的孔隙排出灼热空气,并且加工工序更少,成本降低,织物更加轻薄柔软。
缝制型气囊织物由两层不同规格、不同透气率的织物缝制而成。通常,朝司乘人员的一层具有较小的透气率,另一层的透气率较大,使气囊内大部分高温气体可以迅速从背面排出,减少对人体的伤害[5]。
全成型气囊在织机上直接加工成袋状,其织物是通过改变平纹组织的组织点位置来改变两层织物或织物中某一区域透气率的[6],生产效率较传统气囊织物更高,生产浪费少,单位成本更低,相应的生产效率也更高。近几年德国 GST 集团和法国 Lectra 公司合作,通过预生产软件和最新的激光裁剪技术,可以做到一开始便能生产出没有瑕疵的全成型气囊袋, 有效地减少了原料浪费;2015 年延锋百利得公布过一种主体采用异形截面纱,经编成型的全成型气囊袋[7];2017 年,厦门的华懋材料公司公布了其最新的研发成果,即由新型内腔织物构成的全成型气囊,该气囊内外的封边都根据位置特征进行了组织设计,内腔织物也由不同结缝区域连接构成[7],这样的织物结构在保证气密性的同时,提高了气囊的织物强度和缓冲能力,使其能更有效地承受气体冲击。
涂层织物与非涂层织物的特性比较[2]见表 2。
表2 涂层织物与非涂层织物的特性比较
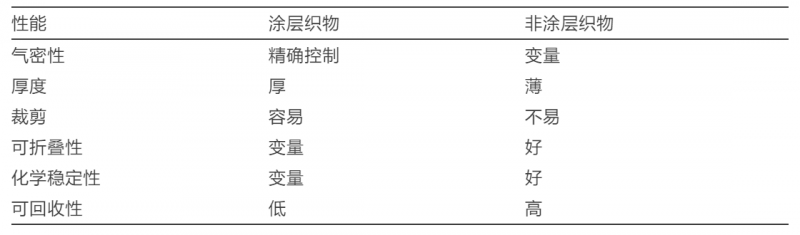
混合型织物
这种类型的织物在面向人体的一面采用涂层织物,保证气囊的气密性,在背面用透气良好的非涂层织物,用于排出灼热气体[6],使两类织物的优势得到更大体现。
3 安全气囊织物的结构与性能要求
当汽车发生碰撞并达到一定的冲击强度时,气囊在气体发生器的作用下迅速被高温高速气流充胀[8],并在瞬间排出气体保护乘员,因此气囊织物不能熔融燃烧,并且要有较好的力学性能和一定的气密性;特定的使用场所要求其能够在-35~85℃的环境下压缩保存 15 年[9]。因此,为了更好地实现安全气囊的安全性,气囊织物应满足下列要求。
织物结构
稳定的织物结构能够更好地保证安全气囊的安全性。
织物线密度
气囊织物常用的长丝规格是 470 dtex/120 根,以聚酰胺为原料的织物纱线线密度一般在 110~940 dtex 之间[4]。
织物组织
在相同条件下,1 上 1 下 平纹、2 上 2 下斜纹、2 上 2 下 重平 3 种不同组织的织物,斜纹织物的透气量最大,平纹最小。相比另外两个组织,平纹组织浮长最短,结构稳定性最高,织物硬挺,相同条件下透气量更小,织物强度也更大[10]。
平方米质量
气囊织物的平方米重量一般要求为 195~260 g/m2,在气囊包装上,要求体积足够小,因此织物需足够轻、薄,当织物经纬密度不变时,降低原料比重,可以降低织物平方米质量;气囊工作时,气囊袋对人体的冲击力大小受织物克重的影响。
织物厚度
织物单层厚度影响折叠尺寸的大小,且安全气囊的储存空间有限,一般要求其厚度为 0.28~0.38 mm [11] 。
透气性
非涂层安全气囊主要依靠织物本身的透气性来排气。根据 ASTM 标准,气囊织物的经向密度不小于 18 根/cm,纬向密度不小于 18.5 根/cm[10]。如果织物密度过低,气囊很可能起不了保护作用;密度过高,则织物透气性差[12],手感过于硬挺,气囊弹出时可能会伤害到人体。
发生碰撞时,气囊需要在 35 ms[12]以内快速膨胀至形状饱满,要求织物有足够小的透气量;气囊内气体在人体向前撞击的 10 ms[11]内迅速排出,防止人体反弹,这又要求气囊织物有一定的透气性, 因此必须要精确控制非涂层织物的透气量。在 500 Pa 的压差下,非涂层气囊织物的透气量要求:朝向人体正面织物为 5 L/(m2·min),背面为 10 L/(m2·min)[11]。
织物密度
织物密度能够在最大程度上影响非涂层织物的气密性。对于缝制型安全气囊织物,可根据上、下层织物不同透气率的要求,经纬纱可以采用不同特数、不同捻度或不同的织物经纱密度[5];对于全成型气囊,封边要考虑其可织性能和牢固程度,还要考虑到其和囊身相接处的气密性,在设计、织造时改变封边组织的经纬纱浮长或减少经纱每筘穿入数,可以改善封边的可织性[5]。
干热收缩率
非涂层织物的透气性也受到长丝干热收缩率的影响。对于织物的热定型处理,不同原料的热收缩率不同,热定型处理时,如果长丝的热收缩率较大,织物的收缩程度也会较大,织物密度增加,也在一定程度上改变了织物的透气性,因此,要根据原料的热收缩率来控制织物的变形程度,以此影响织物的透气率[13]。
力学性能
气囊织物力学性能要考虑的因素较多。在工作时,要求织物强度高、抗撕裂、弹性好、耐摩擦, 能够快速充、放气[5];由于气囊的可使用年限要求高,因此要求织物有良好的尺寸稳定性、抗老化性能。
撕裂性能
对于非涂层织物,织物撕裂强力与纱线强力成近似正比关系。织物发生撕裂时,纱线间相对滑移,形成撕裂三角区域,该区域的纤维共同承受撕裂强力。
当织物涂层后,撕裂强力由织物和涂层薄膜共同承担,由于涂层的渗透,纱线间和纤维间有所粘连,相对滑移减少,使切口处的应力更加集中,织物的撕裂强力降低。另外,织物组织、织物织缩、经纬密以及织物的后整理也对织物撕裂强力有较大影响[9],一般平纹组织织物的撕裂强力最小。
织物强力
安全气囊展开时一方面承受乘员瞬间撞击气囊所产生的冲击,另一方面承受高压高速高温气流对气囊本身的冲击和拉伸作用,因此要求其弹性好,初始模量低,伸长大[14],使气囊展开时织物伸长大,吸收冲击能量大。织物强度主要由其规格结构和原料本身的强度决定[15]。织物的经纬密合适,一般其强力不会过低,同时要注意织造过程的把控,尽量减少织造时的强力损失,保持织物经纬向强力均匀[13];若断裂强力不够,气囊引爆时织物易断裂引起气囊失效。对于涂层织物,降低涂层的硅胶黏度能够有效改善织物的拉伸性能。
不同规格气囊织物断裂强度[9]见表 3。
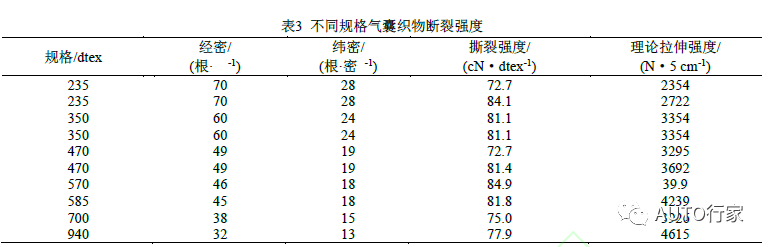
摩擦性能
织物良好的耐磨性可以保证气囊展开时产生的热量小,不易导致燃烧。气囊织物在后道加工工序中需要进行磨绒整理,要求气囊在摩擦后不能有明显的强力损失[11],所以织物的动摩擦系数应足够小。对聚酰胺气囊织物采取轧光整理和起绒整理,可以使纤维皱缩,填充织物间隙,使织物表面光洁,减小动摩擦系数,织物更加柔软,即使发生碰撞,也能避免更多的意外擦伤。在轧光整理时要注意参数的控制,合适的轧辊速度、压力和温度的合理配置,都有助于改善织物摩擦性能。
热学性能
当气囊充气时,瞬时达到高温,织物的耐高温性和阻燃性能要好。纤维的高熔点、高热焓值能使其有效地阻燃,在同样条件下,热焓值高的织物温度上升速度低,耐热性好,在这一点上锦纶纤维明显优于涤纶。标准 GB 8410-2006《汽车内饰材料的燃烧特性》规定,汽车内部的织物燃烧火焰在 60 s 内自行熄灭,燃烧长度不超过 50 mm,对气囊织物的阻燃要求要更高。气囊织物的耐热性主要由原料本身决定,其次也受到涂层性能和后道加工的影响,比如阻燃后整理[13]。
4 安全气囊织物的结构与性能要求
对安全气囊织物的基本情况及发展进行了简要分析。通过对锦纶 66 长丝、高强聚酯丝的性能, 其他纤维和涂覆材料的延伸,以及气囊织物在工作场景下各方面性能要求的分析,得出的结论是目前安全气囊织物的原料选取仍然以聚酰胺为主,辅以其他性能优异的纤维;在织物性能方面,主要要求织物组织结构稳定,气密性好,织物轻薄柔软,热学性能优异,强力高,伸长性能、耐摩擦性能好, 耐老化。目前安全气囊织物除了材料以外,主要的研究方向包括智能化、高强度、良好的耐热性、低气密性以及低成本等,它是环境友好型产品,从长远的角度看,中国企业的各方面发展空间更好。
参考文献
[1] 亢旭阳, 王丽梅, 白银慧, 等. 发展我国安全气囊袋用纤维的思考[J]. 企业技术开发, 2011,30(21):112-113.
[2] 朱俊伟, 方虹天, 庞明军, 等. 聚酯安全气囊的长丝优选及织造探讨[J]. 现代丝绸科学与技术,2010, 25 (3):4-9.
[3] 毕海峰, 张玉梅, 王华平. 汽车安全气囊的技术发展[J]. 现代纺织技术, 2001, 9(1):53-56.
[4] 王叔丽. 国外汽车安全气囊涂覆织物的进展[J]. 特种橡胶制品, 2000, 21(1):9-11.
[5] 方一芳, 蒋世祥. 安全气囊织物的研制与开发[J]. 丝绸, 2000, 45(11):28-32.
[6] 王坤. 汽车安全气囊概述[C] “润力杯”全国织造科技创新学术研讨会暨 2013 织造年会论文集. 江苏:中国纺织工程学会,2013:162-164.
[7] 张丹. 一体成型安全气囊的专利技术综述[J]. 专题与论述, 2019,48(5):42-43.
[8] 谢伟平, 穆国宝, 何凯欣, 等. 浅谈被动安全系统对汽车安全性能的作用及未来发展趋势[J]. 汽车零部件, 2018 , 13(7):90-93.
[9] 季莹, 胡国伟, 胡飞侠. 安全气囊气袋的技术现状及发展趋势[J]. 汽车与配件, 2010, 30(10):34-37.
[10] 茅惠伟, 叶宏武. 织物性能及整理工艺对非涂层安全气囊透气性的影响[J]. 浙江纺织服装职业技术学院学报, 2008 , 7(2):19-29.
[11]侯大寅, 卜佳仙. 汽车用安全气囊织物的质量标准及测试方法[J]. 上海纺织科技, 1998, 26(6):54-56.
[12]刘春娜, 王新厚. 安全气囊织物动态透气性的测试研究[J]. 测试技术学报, 2007, 21(5):396-399.
[13]程晓伟. 汽车安全气囊织物生产工艺探讨[J]. 江苏纺织, 2009,28(1):47-50
[14]马鹏程, 庄源, 孙永明, 等. 一种高网络、大强度安全气囊用涤纶工业长丝的制备[J]. 合成纤维,2017, 46( 3):28- 31.
[15]庞明军, 朱俊伟, 方虹天. 安全气囊涤纶长丝拉伸性能测试分析[J]. 现代纺织技术, 2011,20(2):43-46.
- 下一篇:燃料电池电堆模块详解
- 上一篇:Model3声学性能概述
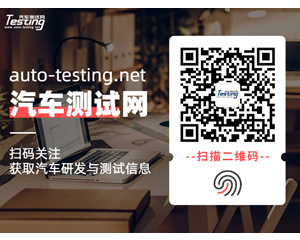
最新资讯
-
商用车及工程机械行业专场:NVH 及语音音频
2025-08-01 17:12
-
理想i8和重卡对撞测试引争议,东风柳汽发声
2025-08-01 15:52
-
艾德克斯IT-N2100 系列太阳能阵列模拟器
2025-08-01 15:43
-
ITECH重磅发布IT2705直流电源分析仪,重构
2025-08-01 15:34
-
现代汽车新一代混合动力系统:以技术革新引
2025-08-01 15:32