应用于电池热管理的均温板的温度特性研究
为了减小电池冷却器与动力电池换热界面之间的扩展热阻,可在两者之间放置均温板。均温板可看做一种特殊型式的热管,其内部充有气液相变介质。当均温板的一面受热时,分布于受热面的液体工作介质蒸发成为蒸气,并吸收热量。蒸气在另一面受冷凝结成为液体,在重力或毛细作用下回到蒸发面,形成循环。
均温板能够将集中的热源/冷源的热量/冷量传递到更大的面积。将均温板应用于电池热管理,有助于实现动力电池表面温度的均匀性,增强电池冷却器与动力电池之间的换热效果。
目前对于均温板热性的研究较多,学者对均温板结构、材质、热性能方面做了大量的工作,但对于将均温板应用于电池热管理领域的研究较少,也尚未有针对R1233zd均温板的研究。
本文设计加工了一款具有内部流道的均温板,并向其中加注环保工质R1233zd。将均温板置于电池冷却器与PTC加热片之间,利用均温板改善冷源与热源之间的换热效果和温度均匀性。通过理论与仿真对均温板表面温度分布进行了分析,通过实验获得了均温板温度分布状况,对于研究均温板在热管理领域的应用具有一定的借鉴意义。
1 理论分析
1.1 均温板设计
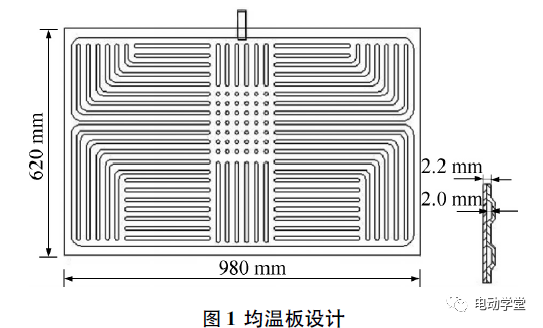
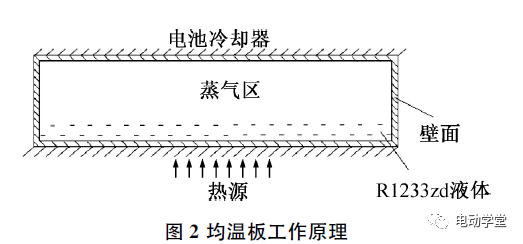
1.2 均温板内部热力学过程的相关假设
相关假设如下:
1)换热过程为稳态过程;
2)均温板内部的R1233zd液体与蒸气均分布均匀,且流动均为层流;
3)热源对均温板的加热效果作用在均温板整个平面,并视为均匀热流;
4)忽略均温板内部蒸发和冷凝热阻;
5)均温板内相变介质不发生烧干。
1.3 数学物理描述
电池冷却器与均温板的换热过程,如图3(a)所示,可视为有内热源常物性二维稳态导热过程。
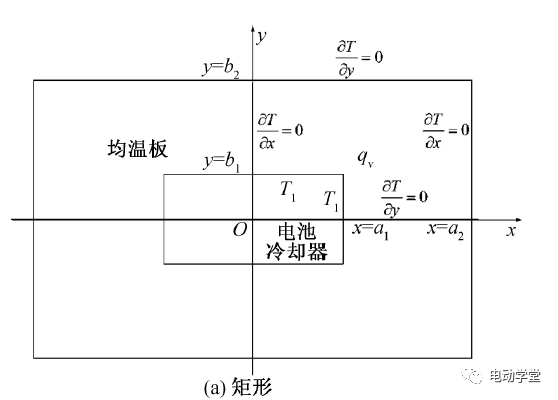

边界条件为:
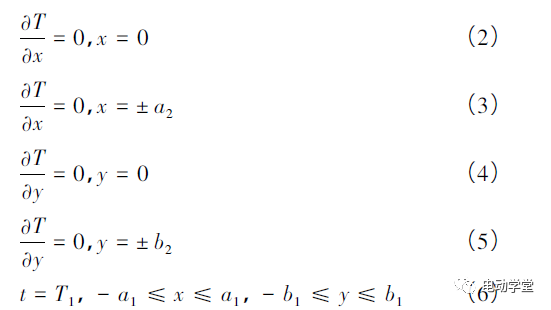
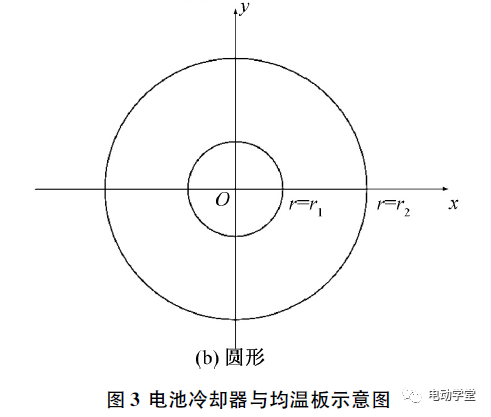



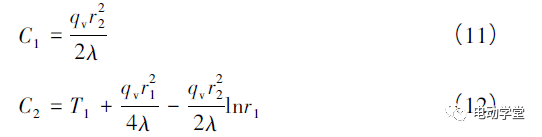

为得到均温板表面更为直观的温度分布,本文利用商业仿真软件COMSOL对均温板进行仿真。首先建立三维模型,均温板、电池冷却器、导热垫的布置如图4(a)所示。生成网格如图4(b)所示。
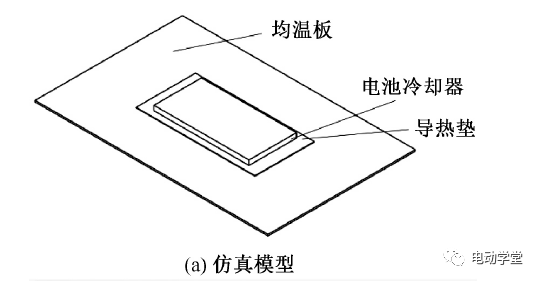
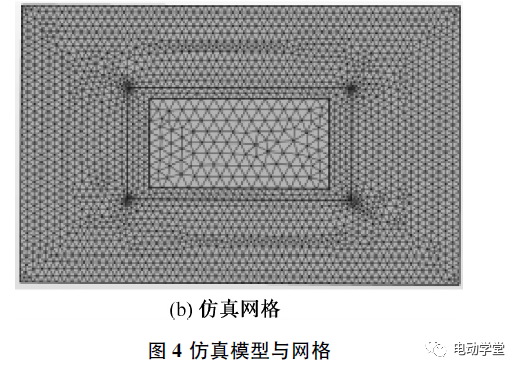
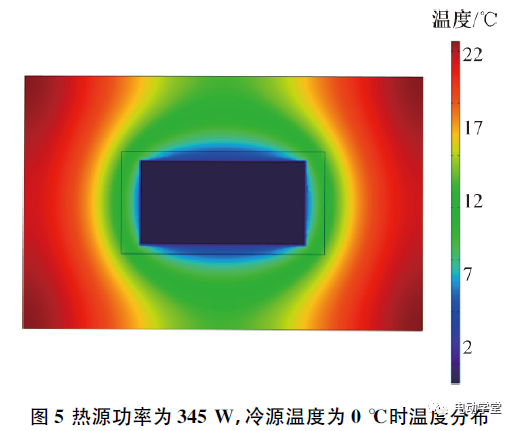
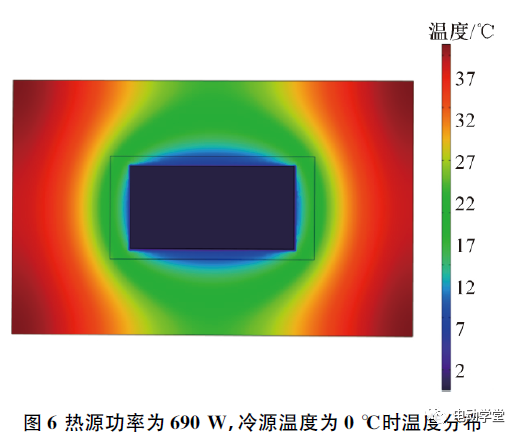
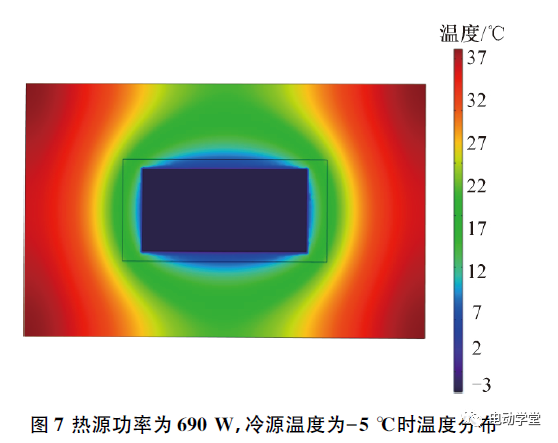
1)当热源功率上升时,均温板表面平均温度升高,表面温差增加。
2)当冷源温度降低时,均温板表面平均温度降低,表面温差降低。
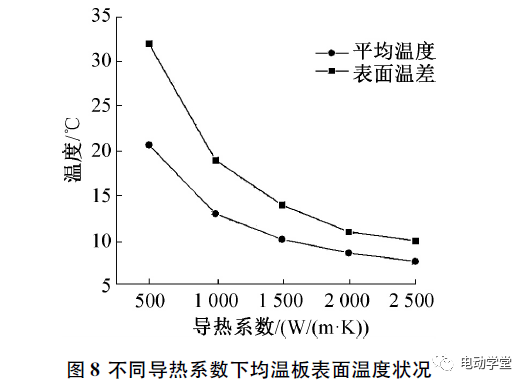
3 实验
3.1 实验装置
1)均温板性能测试实验台
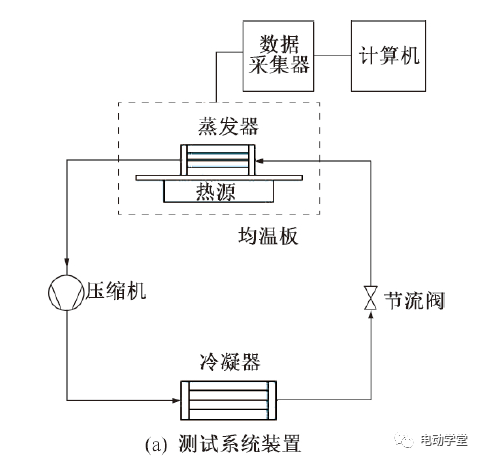
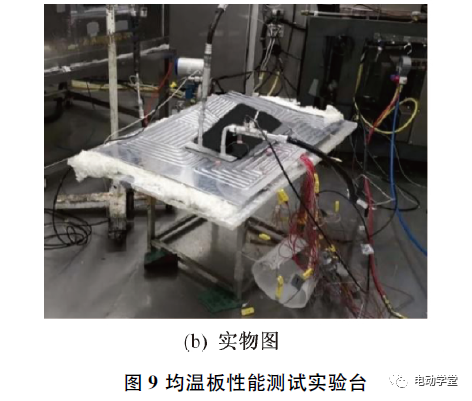
2)均温板与蒸发器
实验用均温板采用吹胀加工工艺,实物如图10所示。
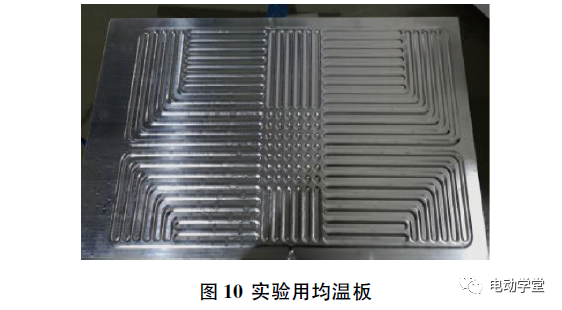
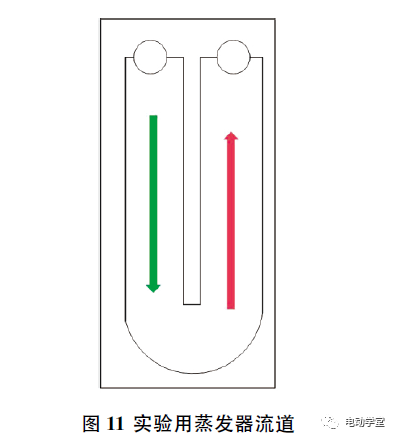
为简便起见,在实验中用硅橡胶加热板代替动力电池作为热源。实验用硅橡胶加热板尺寸为350mm×150mm,单片加热板最大发热功率为115W。为模拟真实动力电池的生热情况,将6片硅橡胶加热板布置均匀地贴于均温板平整的一侧,如图12所示。为获得均温板温度分布情况,在均温板与蒸发器表面布置若干精度为±0.2℃的T型热电偶。热电偶布置如图13所示。
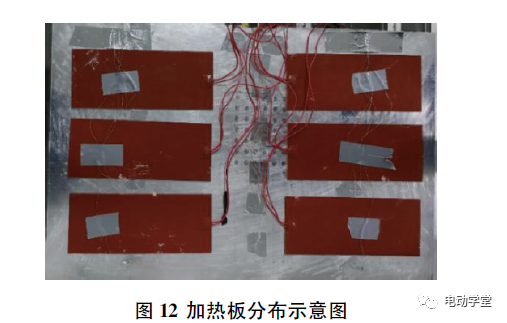
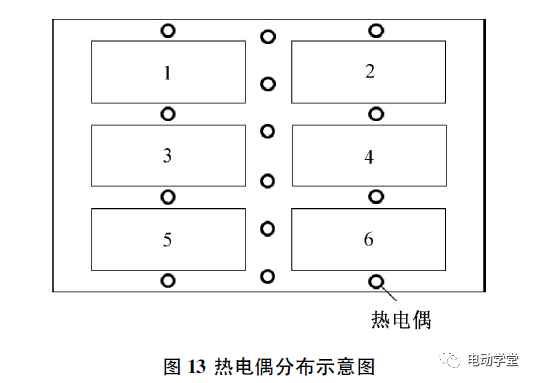
均温板性能实验的变工况参数为橡胶板加热片发热功率与蒸气压缩制冷循环系统的蒸发器入口温度。实验的全过程在环境温度可控的环境室中进行。实验工况如表1所示。
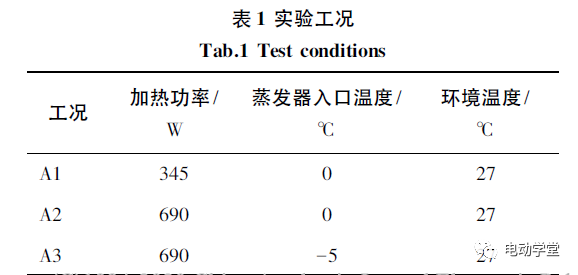
3.3 实验结果
1)热源功率为345W,冷源温度为0℃。
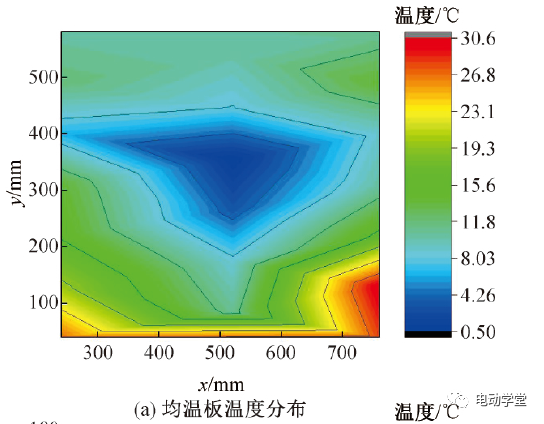
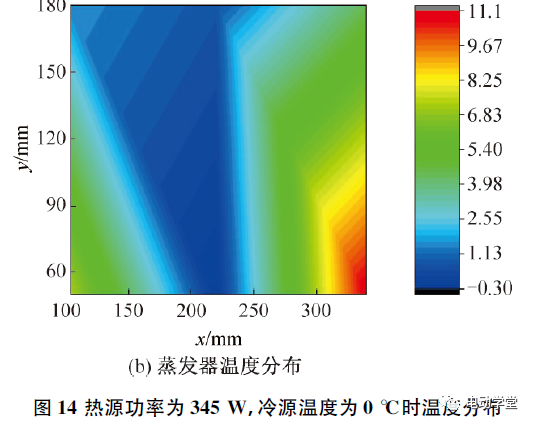
2)热源功率为690W,冷源温度为0℃。
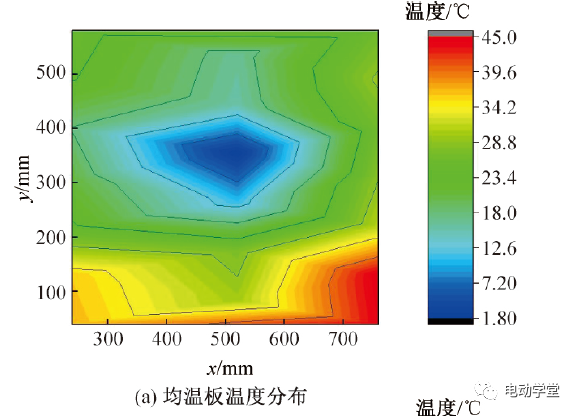
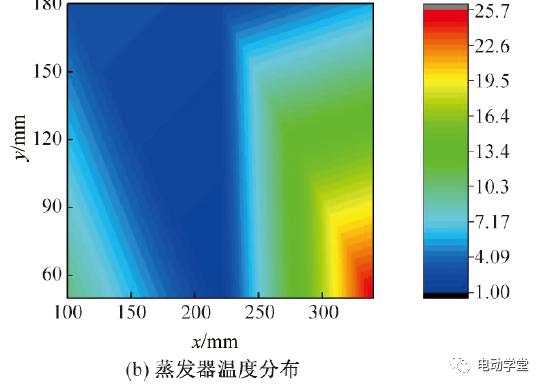
3)热源功率为690W,冷源温度为-5℃。
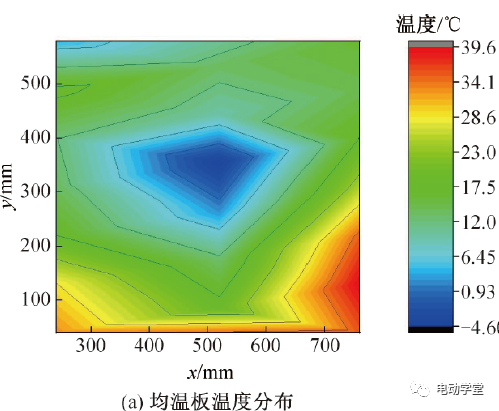
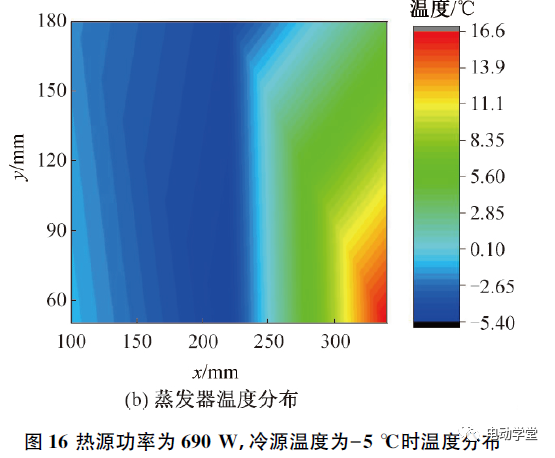
3.4 热阻分析
均温板热阻:

热源侧温度:

冷源侧温度:

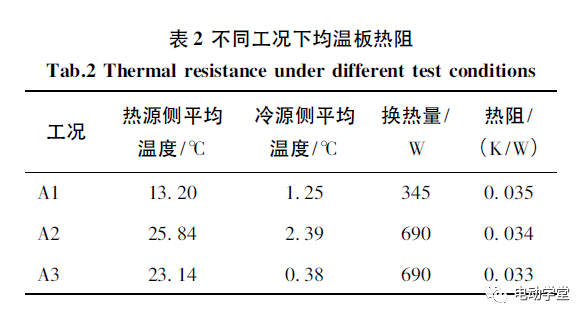
本文搭建了均温板性能测试实验台,研究了在不同热源功率、不同冷源温度下的均温板表面温度分布情况。其中,热源功率有345W和690W两个工况;蒸发器进口温度有0℃和-5℃两个工况。通过观察在不同工况下的均温板温度分布情况,得到如下结论:
1)均温板表面温度分布与蒸发器表面温度分布具有一致性。均温板表面温度在与蒸发器贴合处最低,并向周围逐渐升高。均温板表面温差是由蒸发器表面的温差与均温板内部温度梯度造成。
2)热源功率越大,均温板表面温度越高,温差越大。当热源功率由345W升至690W,而蒸发器入口温度保持0℃不变时,均温板表面平均温度由13.20℃升至25.84℃,表面温差由11.10℃升至25.70℃;冷源温度越低,均温板表面温度越低,温差越小。当蒸发器入口温度由0℃降为-5℃,而热源功率保持690W不变时,均温板表面平均温度由25.84℃降至18.15℃,表面温差由25.70℃降至16.60℃。
3)仿真模拟与实验结果在温度分布上具有良好的一致性,两者之间的差异是由于在实验中蒸发器与均温板之间存在接触热阻导致。由温度分布云图可知,在蒸发器温度均匀布的区域,均温板所对应的区域均温性良好,可认为均温板具有较好的均温效果。在不同工况下,均温板热阻约为0.03K/W,具有良好的导热性能,对提升热管理领域中冷热源之间的换热效果具有积极意义。
- 下一篇:新能源皮卡能量流测评与低能耗开发技术
- 上一篇:汽车电子:拥抱软件或落后
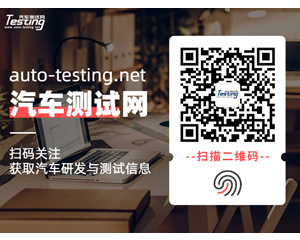
最新资讯
-
商用车及工程机械行业专场:NVH 及语音音频
2025-08-01 17:12
-
理想i8和重卡对撞测试引争议,东风柳汽发声
2025-08-01 15:52
-
艾德克斯IT-N2100 系列太阳能阵列模拟器
2025-08-01 15:43
-
ITECH重磅发布IT2705直流电源分析仪,重构
2025-08-01 15:34
-
现代汽车新一代混合动力系统:以技术革新引
2025-08-01 15:32