某MPV加速声品质优化
摘 要:某MPV全负荷加速过程车内出现异响,严重影响整车声品质。应用LMS公司的Test.Lab振动噪声分析系统对车内噪声、动力总成系统进行振动、噪声数据采集,通过主观评价、传递路径分析、模态分析和频谱分析,确定加速异响传递路径为发动机后悬置,副车架约束模态与后悬置存在共振风险。运用Abaqus软件对后悬置-前副车架进行模态仿真计算,提出调整后悬置橡胶静刚度方案,实现后悬置与副车架模态解耦。进一步试验发现,车内加速噪声异响问题得到明显改善。为优化MPV加速噪声提供一种借鉴方法。
关键词:声品质;传递路径;模态分析;后悬置;静刚度
汽车的噪声、振动和舒适性(Noise,Vibration and Harshness)性能是评价整车动态性能重要指标之一,汽车的所有结构设计几乎都涉及 NVH问题[1]。在所有用户抱怨的汽车问题中,约有1/3的问题与NVH相关,NVH性能水平高低直接影响产品的市场竞争力。近年来,MPV已经成为我国汽车市场一个重要的细分领域,研究整车NVH性能对于提高MPV的市场竞争力具有重要意义。
汽车加速过程中,发动机和动力传动系统工作粗暴,容易将噪声振动传进车内,其主要频率集中在50-400Hz范围内[2]。目前,针对汽车加速噪声产生机理的研究方法有传递路径分析、模态分析和频谱分析[3],运用试验和CAE仿真相结合的手段,确定噪声的激励源和传递路径。加速工况的降噪优化,通常在传递路径上采取隔断手段[4],主要措施有在悬置、副车架、进排气系统等与车身的连接处提升动刚度,改变子系统的模态分布,改善传动半轴的振动特性以及前围加强隔音等。
本文针对某新开发前置前驱MPV在样车试验期间,在急加速过程中车内出现“咚咚”异响声的现象进行研究。采用试验和CAE仿真相结合的方法,分析引起“咚咚”声异响问题的原因,多方案验证,提出降低异响的措施,有效提高该MPV的加速声品质。
1 加速噪声激励源分析
1.1 加速噪声主观评价
在样车试验期间,测试人员主观感受急加速时车内前排可听到“咚咚”声异响,在2500-3000rpm转速区间内尤为明显,声品质较差。
1.2 阶次分析原理
周期负荷作用下的单轴或者多轴的旋转系统的激励通常是叠加的正弦波,且激励的频率为基本频率的整数倍。这些频率倍数称之为谐波相对于该基频的阶次,即阶次指的是被分析发动机曲轴每转内发生的循环振动的次数[5]。
试验车所搭载动力为直列四缸四冲程
发动机,阶次与频率、转速的换算关系:
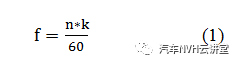
1.3 试验方法
试验设备采用LMS振动噪声分析系统,对试验车振动噪声进行数据采集及处理,所用的试验设备如表1所示。
表1 试验设备
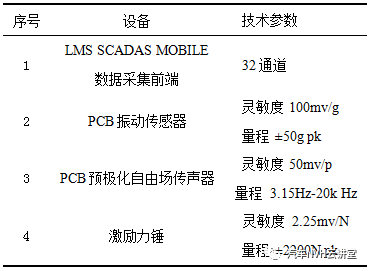
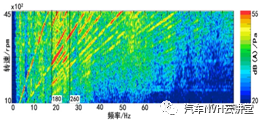
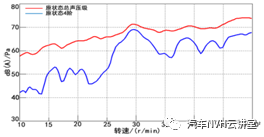
从原车车内噪声频谱图可以看出,共振带能量主要集中在180-260Hz范围内,为加速“咚咚”声主要贡献频段。原车车内声压级图显示,3000rpm 附近4阶阶次噪声峰值和总声压级峰值对应关系吻合,判断可能与发动机激励有关。由式1换算3000rpm峰值对应频率为200Hz,处于噪声频谱图共振带范围内,该峰值为“咚咚”声的主要贡献量。
2 噪声源排查
2.1 激励源分析
为准确判断车内噪声180-260Hz共振带的激励源是否与发动机有关,需要采集3档全油门工况下发动机本体附近及其附件的振动频谱,与原车噪声频带进行对比分析。
试验测点为压缩机支架、变速箱壳体、发动机油底壳,测试分析结果如图3所示。
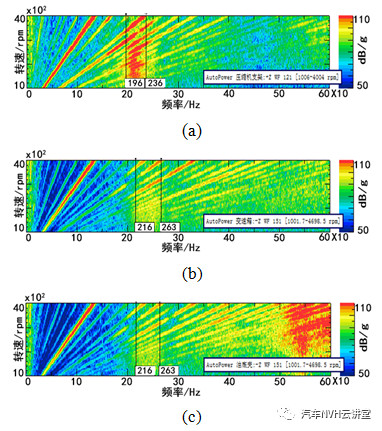
由图3测试分析结果可知,压缩机支架共振频率为210Hz左右,变速箱及油底壳存在210~260Hz共振带与车内噪声问题频带较为吻合。以上分析说明,车内噪声峰值激励源与发动机有关。
2.2 传递路径分析
按照传递方式的不同,车内噪声可分为空气噪声与结构噪声。其中,以发动机为主体的动力总成为激励源所产生的结构噪声,通常以悬置元件、副车架、连接衬套作为传递媒介,最后向车内辐射噪声[6]。因此,为确定加速噪声共振频段的传递路径,需对动力总成与车身连接部位进行传递路径分析。
2.2.1 悬置加速振动测试分析
本文试验车悬置系统为三点式布置,其中后悬置通过前副车架与车身连接。利用LMS振动噪声分析系统采集发动机悬置车身侧的振动频谱,工况为3档全负荷加速。
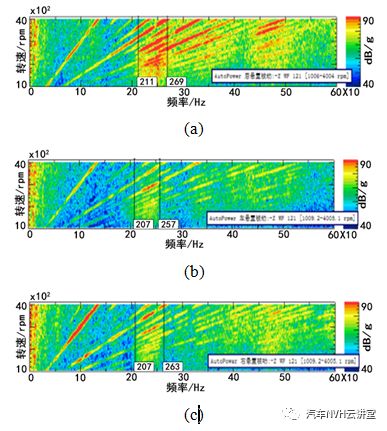
由图4可知,在噪声峰值问题频段后悬置振动能量最大,右悬置其次。因此,判断后悬置为主要传递路径,其次为右悬置。
2.2.2 副车架模态测试分析
发动机作为激励源,其激励频率与车身结构模态频率耦合,导致振动量级放大,是急加速工况车内出现噪声共振峰值的因素之一[7]。
为确定是副车架与后悬置是否存在固有频率耦合的风险,利用LMS Test. Lab中的Impact Testing模块对试验车副车架进行模态测试。测试边界条件为整车安装状态,采用力锤激励法,得到副车架测点频响函数,经计算得到前5阶约束模态频率及其振型,描述如表2所示。
表2副车架前5阶模态振动频率及振型描述
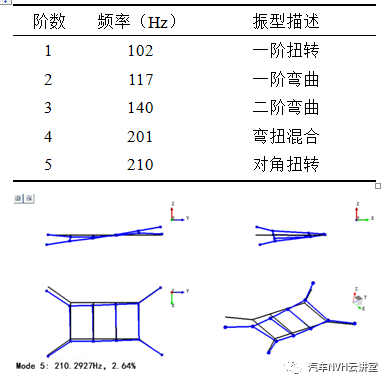
试验结果显示,在整车安装状态下的副车架存在对角扭转模态,频率为210Hz,处于车内噪声180-260Hz共振带范围内。
2.3 副车架质量验证
单质量系统的自由振动频率可简单表示如下[8]:
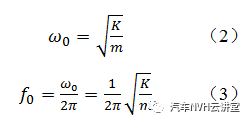
根据传递路径分析可知,副车架210Hz约束模态与后悬置存在模态共振风险。由式(3)可知,副车架增加质量有助于其整体模态的降低。
如图9所示,在副车架底部附加10kg质量块,验证是否能实现后悬置-副车架模态解耦,降低车内加速噪声。车内噪声测点为驾驶员右耳,增加副车架本体振动测点,测试工况为3档全负荷加速。
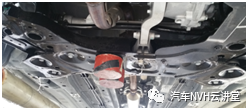
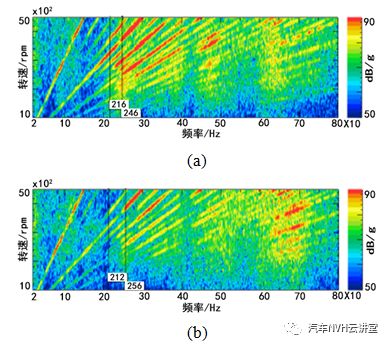
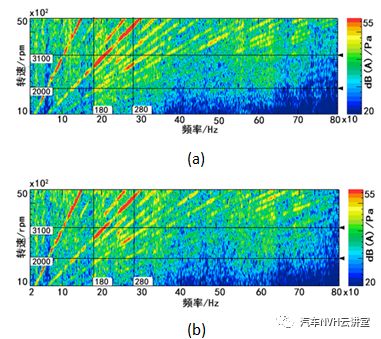
由副车架振动频谱图可知,副车架振动能量相对原状态210Hz左右有较大的降低,250Hz左右频段降低较少。由图11可知,副车架附加10kg质量块后,驾驶员右耳位置210Hz左右共振带能量降低较大,250Hz频带能量略有降低,与副车架振动能量变化趋势一致。因此,副车架增加质量对抑制传递路径具有一定效果。
通过激励源分析,传递路径分析与副车架质量验证可知,加速“咚咚声”激励源为动力总成,频率200Hz左右。噪声峰值主要通过后悬置及副车架向车身传递,副车架210Hz约束模态与后悬置存在共振风险。
3 降噪方案
3.1 仿真分析
改变副车架模态,存在更改周期较长的困难,还涉及到诸如可靠性、耐久性以及成本因素等,难以在车型研发后期实施。因此,采取调整后悬置橡胶静刚度措施,以改变后悬置模态,达到与副车架模态解耦效果。原后悬置橡胶静刚度为149N/mm,新方案调整橡胶静刚度为210N/mm,其他设计保持不变。
利用非线性仿真分析软件Abaqus建立后悬置-前副车架仿真模型,边界条件为车身侧固定约束,计算后悬置-副车架弹性模态。表3为两种橡胶刚度方案前6阶模态频率计算结果统计,单位为Hz。
表3 仿真计算频率统计
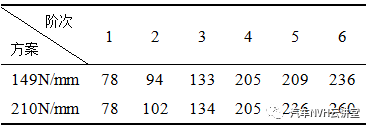
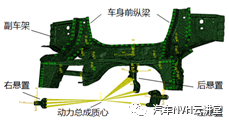
计算结果显示,两种橡胶刚度方案均在第4阶出现副车架局部模态,频率为205Hz,和测试值210Hz相差2.4%。第5阶为悬置模态,原方案悬置模态为209Hz,和副车架205Hz比较接近,存在模态耦合风险。
新方案后悬置模态频率提升至236Hz左右,避开了副车架模态。因此,提高后悬置橡胶刚度有利于提高后悬置模态,实现后悬置-副车架模态解耦。
3.2 试验验证
试验车更换新样件后悬置,使用LMS振动噪声分析系统进行3档全负荷加速,车内噪声测点为驾驶员右耳。
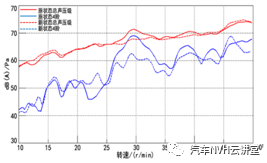
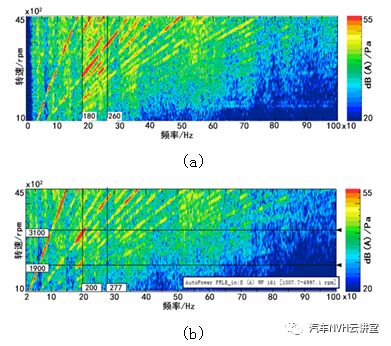
由改进前后车内噪声声压级图可知,发动机后悬置静刚度由149N/mm提升至210N/mm后,车内3000rpm左右的声压级峰值消除,相对原状态下降3dB,二阶阶次噪声相比原状态下降6dB。改进后的车内噪声声压级曲线走势平缓,符合线性听感要求。
由图8可知,对比原状态驾驶员右耳的180-280Hz频段内共振带能量降低明显。主观感受2000-3000rpm范围加速声品质改善明显,降噪效果可接受。因此,提升后悬置静刚度为降低试验车加速咚咚声的可实施方案。
4 结语
本文通过试验测试与仿真计算相结合的方法,降低了某MPV加速车内“咚咚”声,得出以下几点结论:
(1)调整后悬置橡胶静刚度为实现后悬置-副车架模态解耦的有效手段。
(2)后悬置与副车架模态共振容易导致发动机传至车身的振动量级放大。
(3)计算副车架后悬置模态时应当包含动力总成的相关参数,发动机激励对计算副车架后悬置模态具有重要意义。
(4)商业仿真分析软件计算与试验手段相结合,是解决工程实际问题的有效方法。
参考文献
- 下一篇:整车耐候性研究的仿真辅助
- 上一篇:用于商用车柴油机的高低压组合式废气再循环
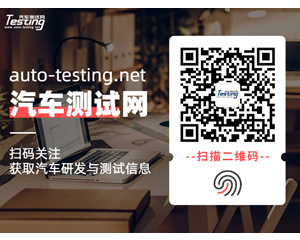
最新资讯
-
商用车及工程机械行业专场:NVH 及语音音频
2025-08-01 17:12
-
理想i8和重卡对撞测试引争议,东风柳汽发声
2025-08-01 15:52
-
艾德克斯IT-N2100 系列太阳能阵列模拟器
2025-08-01 15:43
-
ITECH重磅发布IT2705直流电源分析仪,重构
2025-08-01 15:34
-
现代汽车新一代混合动力系统:以技术革新引
2025-08-01 15:32