电动汽车动力电池的支撑结构轻量化设计研究
降低车辆整体质量,是目前新能源汽车隐藏的一大问题。在动力电池突破种种技术瓶颈之前,唯有进行整车的轻量化研究,而整车轻量化的重点之一就落在了车身的轻量化上。本文以某电动汽车为例,以车身结构质量的最小化为目标,通过优化车身的动力电池框架支撑结构,从而实现车身结构的轻量化。
1 汽车轻量化
汽车轻量化是指在维持原有品质指标不变的基础上,有针对性地通过结构优化设计、提高现有材料强度、使用新的轻质材料、改进制造工艺,以达到减重、节能、减排、安全的综合指标,促进汽车产业健康发展,满足国家能源安全战略需要。
当汽车质量降低10%时,燃油消耗率可提高6%~8%;汽车整备质量每减少100kg,百公里油耗可降低0.3~0.6L;当燃油消耗每减少1L,CO2排放量减少2.45kg。国家规划的节能减排目标是2020年新车的油耗要下降到5L/100km,2025年,降至4L/100km。在汽车产品同质化愈加严重的当下,轻量化技术将成为未来汽车行业发展的突破口之一。
实现汽车轻量化的手段,行业主要有3类:结构、工艺、材料,即优化汽车设计、改进制造工艺、提高现有材料强度、采用轻质材料。国家在“九五”期间进行铝合金材料和铸件生产成套工艺技术的开发研究,取得了较大进展,其中重庆汽车研究所、东北大学、湖南大学和一汽都进行了铝合金板材的成形性研究。国家在“十五”期间启动了镁合金开发应用及产业化项目,初步建立了从镁合金前沿研发到产业化技术开发的研发体系,培育组建了一批有关镁合金及制品的股份制公司,形成一批镁合金产业化基地,逐步制定镁合金使用标准。国内于2007年成立的国家汽车轻量化技术创新战略联盟通过多年的产学研一体化,对轻量化材料成形技术、关键共性技术、材料应用进行了研究,建立了轻量化材料数据库,制定相关标准和规范,使得轻量化技术获得长足发展。在量产车市场阶段,目前已实施轻量化路径的层出不穷。
宝马i3的电动车,减重目标是250kg,比传统的电动车减17%。宝马5系采用全铝合金的前舱结构,比同结构的钢制前舱节省了30%的重量。奥迪A2采用全铝车身,汽车自重只有895~990kg。奥迪A8的ASF全铝车身框架结构,比钢制车身具有40%的轻量化优势。奔驰C级轿车车身的48%使用铝合金材料,使车身重量减轻了70kg。上海大众桑塔纳轿车变速器壳体采用镁合金来实现减重。
众所周知,汽车的4大行驶阻力(滚动阻力、坡度阻力、加速阻力和空气阻力)中有3个与车重成正比。通过这些轻量化的手段,汽车拥有了更加高效的行驶性能和更加优良的动感表现。
2 动力电池模块的一般支撑结构设计
通常的动力电池模块,根据容积的大小主要布置在后地板备胎舱下,或前地板中央通道下,主要靠前、后地板的骨架(如纵梁)来实现支撑。
当动力电池模块布置在后地板备胎舱下时,由于动力电池模块较小,可以通过传统轿车的前、后地板的骨架来实现支撑,但这种布置的动力电池模块,在一定程度上限制了电动轿车的续驶里程。为了保证动力电池模块的连接强度、抗扭转性能、后碰保护,备胎舱做了一定程度的加强,见图1。
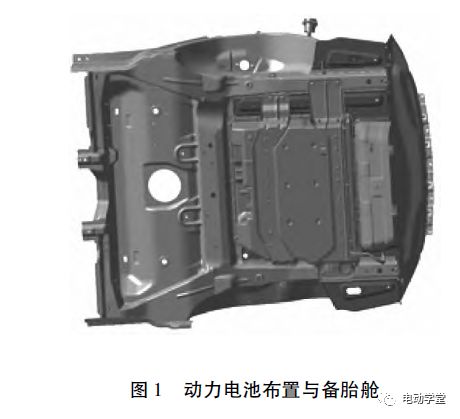
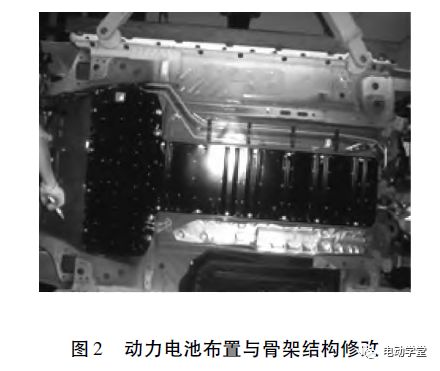
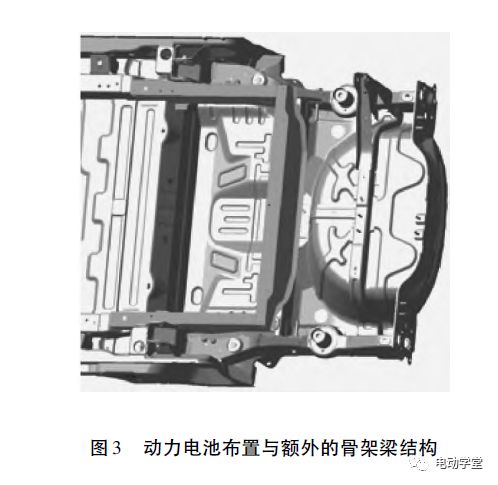
3.1 通常车身轻量化设计
不可否认,作为汽车轻量化最突出最直接的一个方式是使用新兴材料,但是受限于成本因素的影响和制造工艺的约束,新兴材料一般使用于高端汽车,对于普通的汽车,效果好的新兴材料取代传统的高强度钢板,会是一个较为漫长的过程。
通常汽车车身结构的轻量化设计,就是使零件薄壁化、中空化、小型化和复合化,并且普遍采用高强度钢。每年的欧洲车身年会上代表车型,高强度钢用量已达50%。
3.2 电池框架支撑结构的轻量化设计
在“中国制造2025”战略中,“节能和新能源汽车”与“新材料”均被列为10个大力推动突破发展的重点领域,轻量化被列为其中的重要方面。如果能实现轻量化预期目标,每年有望减少石油需求0.45~0.63亿t。
梁柱结构是车身骨架的基本承载单元。传统车身上梁单元结构众多,因为车身结构需要大平面来给整车各个系统部件做安装点、支撑面,对碰撞安全性起到很好的保障作用。为了提高弯曲和扭转刚度,通常需要增加梁的矩形截面的高度和宽度,从而不可避免地增加了重量。柱单元结构具有非常良好的圆筒截面特性,经碰撞测试结果,其安全性比传统的冲压焊接总成更好,能大幅度降低整车质量。通过增加圆筒截面的直径就可提高弯曲和扭转刚度,具备高刚性、高稳定性。通常柱单元结构的制造采用液压成形技术来完成,如底盘的一些架构零件,它不但减少了模具费用投入,还大大缩短了模具制造周期,而且避免了材料变薄,提升了零件材料利用率。
本文不仅使用了柱单元结构,满足了电动汽车动力电池的支撑结构的强度和刚度及安全要求,并且另辟蹊径,通过将钢管式框架支撑结构的多处管状转弯半径设计为一致,使其摒除液压技术,直接在单头弯管机上实现制造,并且采用了市面上普及的弯管直径大小,大大降低了制造成本和零件单件成本,如图4所示。
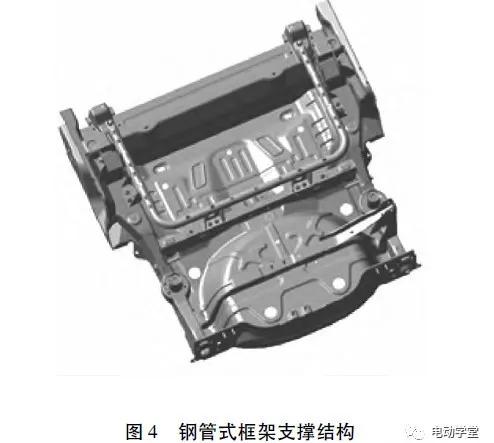
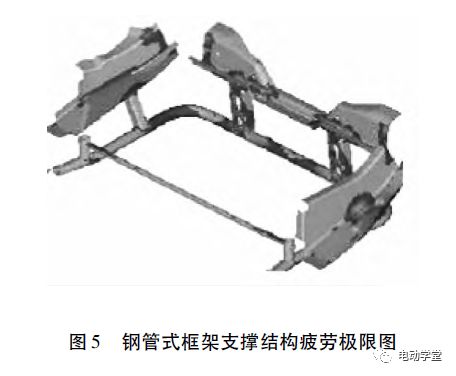
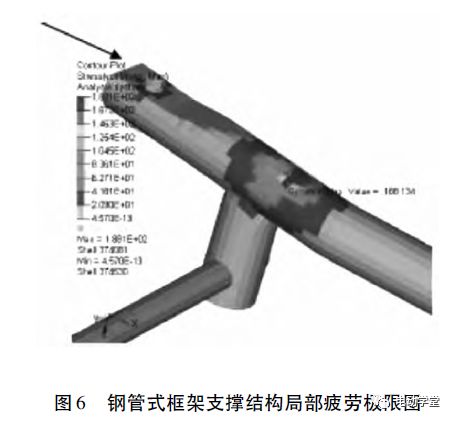
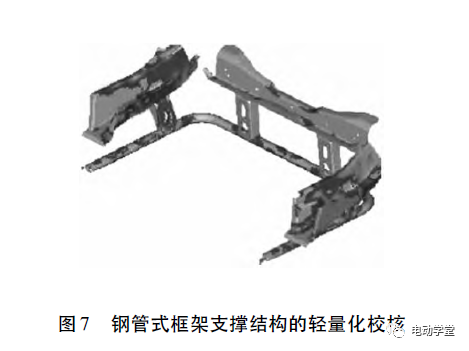
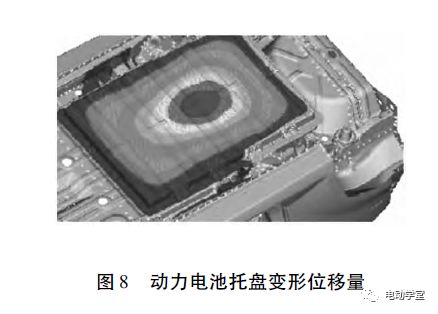
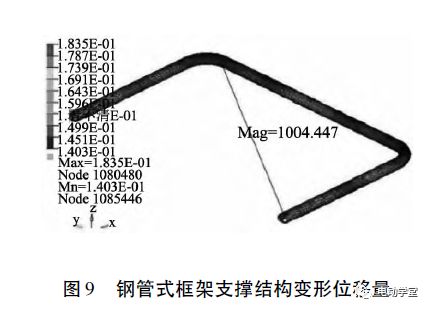
在车身后部未安装吸能盒、碰撞横梁以及泡沫等结构下,进行车身尾部碰撞模型分析,结果显示动力电池托盘边缘受到轻微挤压,动力电池本体未发生明显变化,最大应力满足设计要求,无塑性应变。后纵梁末端压溃较好,整体变形模式可接受。由此可见,钢管式电池框架支撑结构设计,满足50km/h尾部碰撞目标要求。实车试制后,通过尾碰试验验证,与有限元计算的结果基本一致。
4 结语
本文以有限元仿真模型为基础,通过考核疲劳强度和安全性能,对电动汽车的动力电池连接处进行优化计算,实现电动汽车动力电池的支撑结构轻量化设计,减轻的质量为原来的骨架梁结构的50%,实车试制成功并通过试验验证。
钢管式结构可以省去冲压设备的投入,降低生产制造成本的同时,更容易进行局部加强,在充分利用空间、赢得更大弯曲和扭转刚度的同时,大大减轻了质量。在寻求车身结构轻量化的道路上,值得推崇。
- 下一篇:凯美瑞双擎车电子无级变速器详解
- 上一篇:纯电动汽车动力电池降温性能研究
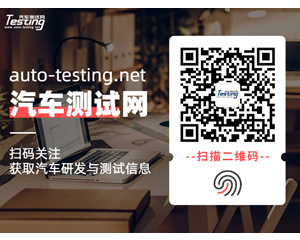
最新资讯
-
商用车及工程机械行业专场:NVH 及语音音频
2025-08-01 17:12
-
理想i8和重卡对撞测试引争议,东风柳汽发声
2025-08-01 15:52
-
艾德克斯IT-N2100 系列太阳能阵列模拟器
2025-08-01 15:43
-
ITECH重磅发布IT2705直流电源分析仪,重构
2025-08-01 15:34
-
现代汽车新一代混合动力系统:以技术革新引
2025-08-01 15:32