某动力电池热失控安全设计
新能源汽车行业蓬勃发展,自2014年产量大幅上升达到84900辆,2015年猛增至37.9万辆;2016年累计生产新能源汽车51.7万辆,同比增长36.4%。动力电池作为新能源汽车核心零部件,其发展紧随整体市场趋势。从动力电池历年出货量看,2015年开始动力电池跟随新能源汽车产销量崛起,从2014年的3.7Gwh的出货量跃居至2015年15.7Gwh,同比增长超过3倍。2016年1-10月有产量的新能源汽车搭载电池总量达13.9Gwh,与去年同期相比增长78%,与去年全年动力电池出货量相差无几。
随着电动汽车的存量增加,电动汽车安全事故明显增多,成为关注热点;据中国电动汽车百人会研究成果《电动汽车安全报告》不完全统计数据,2015年发生电动汽车安全事故14例,而2016年发生35例;这些发生的安全事故中,动力电池热失控引起的事故占比最大。动力电池热失控安全技术研究引起国内外学者广泛重视。
在电池单体热失控安全技术方面,发展出如下技术方面突破:电解液改进,正极材料改进,隔膜改进,表面包覆,泄压阀及PTC电阻等。在电池成组热失控方面,国内外主要在如下方面展开研究:结构安全设计,BMS安全,冷却系统,主动安全技术等。电池系统及成组结构安全设计主要包括热传播阻断设计,阀泄通道设计,PTC电阻及熔断器设计等;BMS安全包括参数检测,BMS均衡技术等;冷却系统包括空气冷却,液体冷却,相变材料冷却等;主动安全技术包括灭火,防爆设计等技术。
电池单体热失控研究取得很大进展,但国内外仍时有安全事故发生。电池系统成组技术在其中的作用需进行深入研究及实践验证。基于大量热失控安全试验及电池系统成组设计实践,为解决电池热失控安全问题,在产品设计中采用了主回路熔断器防护,采集回路过流防护,安全爬电距离、电气间隙设计,分布式电芯外短路保护设计,多维模组热扩展结构防护,透气防爆装置,主动灭火装置等结构、电气、主动安全措施。通过大量安全措施的研究及应用,电池系统安全性能得到大幅提升。产品开发过程中,通过热失控安全试验对安全性能进行了验证,确认了热失控安全设计的效果。
2 热失控及传播原理
动力电池热失控可由单体内部因素及外部因素引起。内部因素一般为过充、低温充电、负极缺陷等导致负极形成的化合物穿透隔膜引发短路,或电池内部杂质刺穿隔膜引发短路等;外部因素包括正负极短路,大电流放电,高温,挤压、针刺等。由于单体内部或外部因素的发生,电池单体温度持续升高;以锂离子电池为例,单体高于60℃时,SEI膜开始分解,全部分解后露出负极表面;随着电池温度的提升,电池隔膜高温收缩,正负极活性物质接触,发生短路,瞬间释放出大量的热量。短路点高温进一步导致正极氧化物分解,释放出游离状态氧,并与有机电解液发生氧化反应,释放出更多的热量,最终导致电池发生起火爆炸。
电池单体发生起火爆炸后,一方面通过模块连接部分向其它单体进行热传导,另一方面通过热对流、热辐射向其它单体进行传热,模块或电池系统的散热装置也将起到传热的作用;而单体的持续升温将导致热失控发生,从而热失控从一个单体扩展到其他单体。一个单体的热失控短路将引起其它单体的外短路,而短路继续引起其他单体温度升高,从而引起单体的热失控扩散。一个单体热失控起火爆炸后的火焰和喷射出的内部物质将直接对其他单体产生瞬间加热作用,造成其他单体的短路和温度升高,从而引发热失控。单个电芯的爆炸起火还有可能引起其他线束、覆盖件的起火,从而再次引发其他电芯的温度升高,发生热失控现象,见图1。
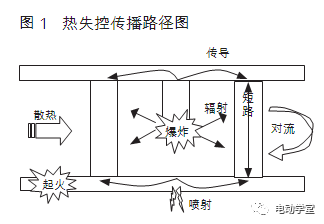
根据电池热失控及传播机理,可提高单体电池性能,防止热失控的发生;同时在成组技术方面可采取热失控阻断技术,在单个电池热失控时不扩散到其它单体。热失控阻断技术主要在热传播和扩散的路径进行处理,以达到阻断电池单体发生连锁热失控反应的目的。例如阻断或降低热辐射、对流、传导对周围单体的影响;使用散热系统或主动安全技术对单体进行快速降温;使用喷射导流技术防止喷射物对其他单体的影响;使用过流防护、短路防护、熔断技术防止一个单体的短路影响其它单体;通过阻燃材料的使用防止单体周围材料的燃烧引起单体热失控连锁反应,通过对电气件安全爬电距离,电气安全间隙的设计防止外短路的发生等。根据引起热失控的内部因素和外部因素,可针对性的设计相应防护措施,从单体-模组-电池包三个级别逐级控制,在热失控传播路径上形成安全防护网,达到保证整车安全的目的,见图2。
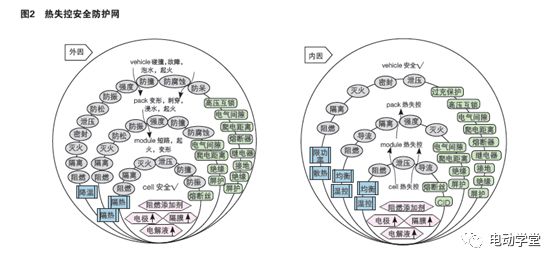
3 热失控安全设计
3.1 结构安全设计
某动力电池系统成组设计过程中,采用多维模组热扩展防护结构设计,有效解决电池单体热失控向外扩展问题。基于喷射导流技术,设计电池单体热失控火焰喷出点热扩散防护结构。通过喷射导流装置将热失控散发的火焰及热量导出到模组外部,并通过逐级降温避免了喷出的高温气体和火焰等热量传递到周边电池单体,见图3。多维模组热扩散防护结构在电池单体安全阀位置增加阻燃隔热层,并在隔热层中间设计一定间隙,单体热失控后高温气体和火焰会通过隔热层间隙导出到模组外部。由于隔热层阻燃及隔热作用,高温气体和火焰不会对周边单体造成影响,避免了周边单体热失控条件的达成。阻燃复合材料的使用在热扩散防护结构中起到关键作用,同时还广泛应用于动力电池系统中,例如模组支承结构,电池包上盖,高低压线束等。其中结构件的阻燃等级100%达到UL94-V0等级;电气件的阻燃等级均达到UL94的V-1等级以上,关键电气件UL94-V0等级覆盖率100%。通过阻燃复合材料的使用,不仅增加了动力电池系统的安全性能,同时起到了轻量化的作用。通过阻燃复合材料的动力电池系统应用,电池系统整体降重10%。
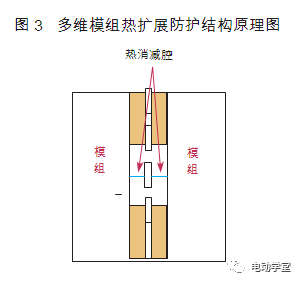
3.2 电气安全设计
电气安全设计是电池系统安全设计中最重要的部分,通过设计覆盖整个电池系统的电气安全防护体系,有效解决电气安全问题。首先,对电气系统整体进行电气间隙及爬电距离优化,为电气奠定安全基础;其次,在高压安全方面,通在主回路中设计主熔断器、主继电器、模组过流保护、电芯过流保护等过流分级防护,消除因系统外部和模组与模组间短路失效造成的危害,有效防护高压系统电气安全;再次,防止因电池包浸水和采集回路导线及连接器失效造成的短路对电压采集回路进行伤害,对系统内所有电压采集回路进行保护。
3.2.1 电气间隙及爬电距离优化
电气间隙和爬电距离是电气安全设计的基础,如果动力电池内部带电部件与外壳之间距离过小,很容易造成短路或者击穿,使动力电池壳体带电;如果不同电位的带电部件之间电气间隙或爬电距离过小,同样可能造成短路引发火灾。动力电池电气间隙和爬电距离设计首先需要遵照国家标准(GB/T18384.1)进行设计;在国家标准的基础上,还需根据环境因素所带来的影响对电气间隙及爬电距离的参数进行修正,例如导体周围绝缘材料电极化现象,以及导电部件之间或导电零部件与设备防护界面之间击穿现象等。在某动力电池系统设计过程中,通过模组及线束布置优化,电气间隙达到55mm以上,爬电距离达到200mm以上。
3.2.2 高压系统安全
为解决高压线路末端电池单体外短路问题,进行分布式外短路保护设计。本设计主要作用是防止系统滥用的情况下,外部短路电流对电芯进行短时间大电流充电;该短时大电流充电将造成电池单体内部热失控,导致起火爆炸。通过在每个单体通电回路中串联一个大电流通电熔断装置,当单体外部由于其他保护元器件失效导致瞬间大电流通过串联熔断装置的单体回路,熔断装置进行动作切断异常回路,避免大电流破坏单体,造成单体热失控的发生。
为防止主回路过载发热和短路危险,在电气系统主回路中设置快速熔断器,在熔断器选型中考虑系统最大电压峰值冲击电流的频率和时间等因素,保证产品生命周期内不因为疲劳老化过早失效,正常工作时不发生误动作。主回路熔断器的设计,达到了在主回路发生短路时电池单体不被损坏,以及导线烟化前进行熔断保护的目的。在熔断器回路设计和布置过程中为降低摸组间短路发生的机率,将主熔断器布置于模组串数的1/2处,见图4。

3.2.3 低压系统安全
动力电池管理系统需要对每一个单体电池电压进行检测,由于电压采集线数量多,成线束后由于连接器失效、导线绝缘皮破损等问题容易造成短路引起线路起火,另外,当电池箱体密封失效时电池箱体内部进水也有可能造成短路,为防止电压采集线的短路故障,在电压采集线电源端设置采集线路过流防护熔断器,当发生上述故障时起到有效防护,见图5。
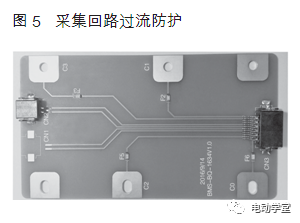
3.3 主动安全设计
动力电池系统使用环境/运行工况非常复杂,安全性能可能遭受各种问题的考验。电池包PACK根据国家标准防护等级达到IP67,在这种环境下除非真空,否则正常工作中会发热膨胀,这时需要平衡内外气压,通过防爆阀应用可解决以上问题。在电池系统机械、电气等安全措施失效时,可通过主动灭火技术应用,为乘客留出一定的逃生时间,甚至将较小火势扑灭,防止热扩展的发生。
3.3.1 防爆装置开发及应用
防爆装置的应用能够在达到IP67的防护等级和平衡内外气压的基础上大幅提升安全系数。目前国内市场上主要是EPV防爆阀,其存在两个问题:一是透水气:EPV防爆阀为透气性防爆阀,防水等级为IP67,但是不能有效隔离水气进入电池包,容易造成电池包内部零件腐蚀、电气短路、绝缘阻值降低,报绝缘故障;二是防爆作用:EPV防爆阀爆破压力为25-30KPa,而电池包满足IP67要求的内外压差为10KPa,因此在电池包内部热失控后,密封失效和防爆阀爆破的顺序有待验证。
为更有效防止电池包爆炸,开发设计利用簧片的弹性特点,根据爆破压强设计簧片临界反转点的机械非透气性防爆阀。防爆阀工作过程中存在3个状态点,分别是原始状态(A)、临界状态(B)、防爆开启状态(C)。在电池箱体内气压增大时,当压强大于15kpa,防爆阀由A状态开始启动,阀的开口面积与压强成正比。随着压强进一步增大,当达到20kpa时,簧片位置已经由原始状态A点到达了临界状态B点,此时簧片瞬间反转,到达防爆开启状态C点,阀的通气面积瞬时增大,从而达到防爆的效果,见图6。
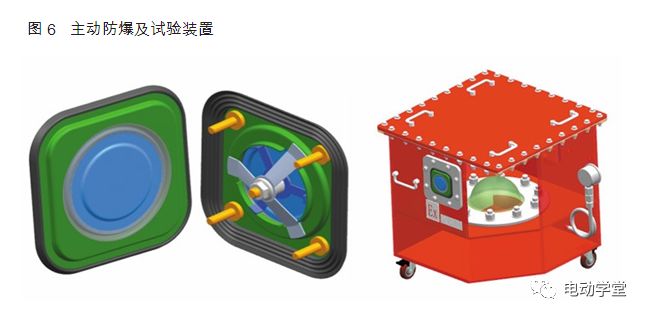
3.3.2 主动灭火装置开发及应用
动力电池灭火技术是一项主动安全技术,前期主要在大型客车及公交车上推广,在新能源乘用车上尚未开始应用。通过研究开发,将其在乘用车动力电池系统中应用。
主动灭火装置开发的核心是灭火材料的选用,决定最终灭火最终效果及装置本身的轻量化、可靠性设计;本动力电池灭火装置采用清洁、无毒、可清理的灭火材料,该灭火材料不会对动力电池系统造成破坏,经过维修更换失火模块后可动力电池继续使用;该灭火材料是无毒的,不会对乘客造成影响,也不会对地球生态系统造成污染;该灭火材料存储有效期长,稳定性高,可保证电池系统生命周期不需维修更换。灭火装置另一重要部分为火灾探测装置,决定灭火装置能否适时启动,及时灭火;本主动灭火装置采用多种火情探测机制,即使在车辆驻车断电状态仍可为动力电池的安全性能提供保障,见图7。
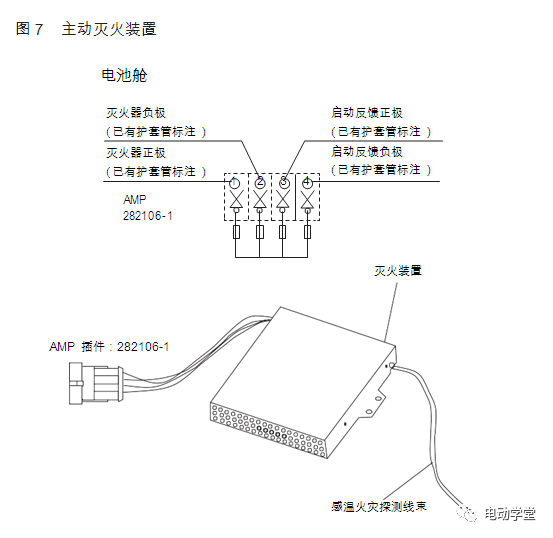
4 热失控安全试验研究
动力电池热失控及其安全技术发展很快,安全设计后其效果需实际试验验证。针对应用了大量安全设计技术的某款动力电池包,进行热失控安全试验,对比安全设计技术的实际效果。为利于试验观察及对比,针对未采取任何安全设计的模组和增加了安全设计的模组进行同时进行热失控试验,对比二者的差异。试验前将电池模组充满电,按图8的方式将电加热电阻丝缠绕至最容易热积聚的模组中间位置电芯上,直至电芯发生热失控(温度骤升同时伴随电压骤降以及起火现象),见图8。
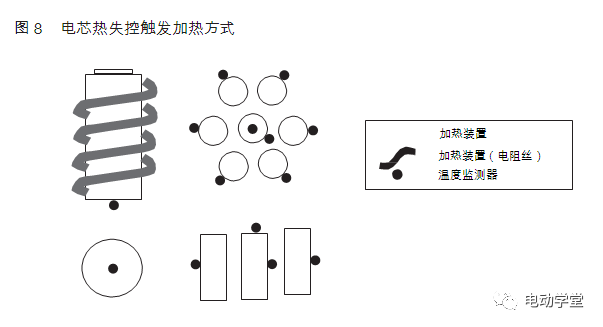
该模组采用的安全设计方案包括:使用了多维模组热扩展防护结构,选用阻燃复合材料设计模块支承架等结构安全措施;同时设计了分布式熔断装置。可以发现未采用安全设计的模组持续剧烈燃烧,发生多次爆炸;而增加安全设计后的模组在强制同时加热2支电芯至热失控后,未产生热蔓延,见图9。
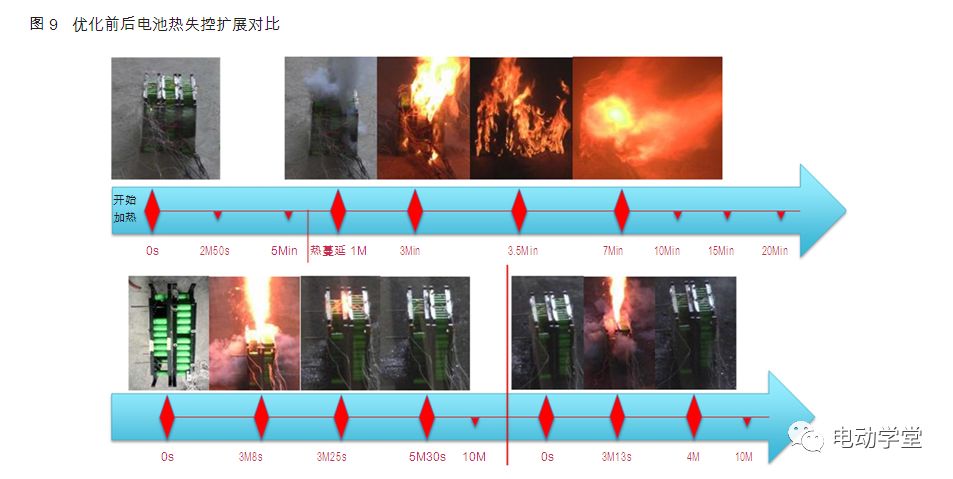
5 结论
电池单体热失控研究取得很大进展,但国内外仍时有安全事故发生。电池系统成组技术在其中的作用需进行深入研究及实践验证。基于大量热失控安全试验及电池系统成组设计实践,为解决电池热失控安全问题,在产品设计中采用了主回路熔断器防护,采集回路过流防护,安全爬电距离、电气间隙设计,分布式电芯外短路保护设计,高阻燃材料应用,多维模组热扩展结构防护,透气防爆装置,主动灭火装置等结构、电气、主动安全措施。通过大量安全措施的研究及应用,电池系统安全性能得到大幅提升。产品开发过程中,通过热失控安全试验对安全性能进行了验证,确认了热失控安全设计的效果。
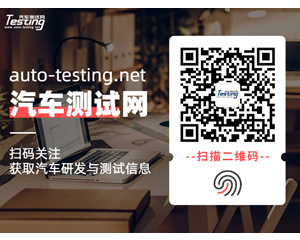
最新资讯
-
商用车及工程机械行业专场:NVH 及语音音频
2025-08-01 17:12
-
理想i8和重卡对撞测试引争议,东风柳汽发声
2025-08-01 15:52
-
艾德克斯IT-N2100 系列太阳能阵列模拟器
2025-08-01 15:43
-
ITECH重磅发布IT2705直流电源分析仪,重构
2025-08-01 15:34
-
现代汽车新一代混合动力系统:以技术革新引
2025-08-01 15:32