汽车研发:整车电路系统试验验证方法!
随着纯电动汽车电子化程度不断提升,电子设备越来越多,车辆在开发过程中需要对整车的电路系统进行多轮的检测及试验验证,接下来就由漫谈君带大家一起来探讨整车电路系统需要做哪些测试,又是如何进行验证?
二、整车电路检测
整车电路检测指对竞争车型不进行拆解,而进行的功能分析和部分性能分析,就电路系统来说主要可以进行检测:整车功能检测、起动性能检测、电平衡检测、温度场检测。
1、整车动静态功能分析
1) 动力系统
电压的检测
电喷系统在电压9V~16V时,可以正常工作,功能完全正常;在6~9V时,部分功能正常,可以启动;超出此范围以外则不能正常工作。所以应该检查如下点的电压。
电瓶正极电压:蓄电池的电压通常在12.4~12.8V。
(注:在发动机不启动时,启动发动机后,蓄电池电压应该为发电机输出电压,详细参数由负责发电机的工程师提供,一般在14.4±0.5V)。
接地点电压:电瓶地、传感器地、功率地。
风扇控制的检测
风扇通常有两种控制方式:两档控制和连续控制,风扇的开启温度由电喷系统设定。
风扇的工作与水温、空调系统的压力、车速、发动机转速、变速箱等有关,其中水温和空调的压力为最重要的两个参数,在不同的电喷系统中有不同的控制策略。用数据采集仪检测水温。
两档风扇,首先将发动机启动,不开空调时,检测风扇的低速档开始工作时的水温T1,风扇高速档开始工作时的水温T2,水温在升高后会逐渐降低,然后到降低到高速关闭,低速打开,水温继续降低,然后再升高,达到一个平衡的状态;在开空调时,风扇会自动在低速档工作,然后根据水温的变化同上,在带中压开关的空调系统中,如果空调压力达到1.6MPa,风扇的高速也会启动。
在连续风扇中,ECU会根据水温、空调压力、车速、转速、变速箱等相关的参数来确定风扇的转速,其本的原理同上。
2) 空调系统
手动空调
a. 鼓风机处于工作档位时,A/C才有效,打开时,压缩机工作。
b. 内外循环开关,切换内外循环工作状态。
c. 混合风门旋钮,对乘客舱内温度进行冷暖调节。
d. 模式旋钮,切换吹面、吹面吹脚、吹脚、吹脚除霜、除霜模式状态。
e. 后风窗加热按钮,按下后,启动后风窗加热功能。
自动空调
a. 内/外循环按键:内/外循环按键每按一次,内/外气执行器转换一次内/外气工作状态。
b. 温度调节按键(或旋钮):对乘客舱内温度进行冷暖调节。
c. 室外温度显示按钮:旋钮按下后显示外部温度,持续3秒后恢复。
d. AUTO按键:在OFF状态下,按下此按键启动系统工作系统自动记忆用户上次设定的工作。在空调工作状态(非自动),按下此件后,空调处于自动工作状态。
e. OFF按键:关闭系统。
f. MODE按键:改变吹风模式。
g. AC按键:开/关空调压缩机。
h. 除霜按键:切换成强制除霜。
i. 风量按键:调节风量。
j. 后除霜加热按键:按下后,启动后风窗加热功能。
3) 灯光系统
判断整个灯光系统的构成,一般包含近光灯、远光灯、位置灯、牌照灯、雾灯、转向灯、危险报警、制动灯、倒车灯、室内顶灯、行李箱灯、礼貌灯、门槛灯等。分析整车灯光系统的控制逻辑。
4) 雨刮洗涤系统
雨刮系统
手动雨刮:手动雨刮分为三档:间隙档、低速档、高速档。
自动雨刮:雨刮根据雨量传感器的信号来开起关闭雨刮,同时调整与刮的间隙时间。
洗涤系统
风窗洗涤:打开洗涤开关,洗涤泵工作,同时雨刮刮两下或三下。
5) 音响系统
收放机
按下开机键,进入工作,可通过按键进行搜、存台,插入磁带可放音。
CD机
具备收音、CD功能,有六碟CD和单碟CD之分,立体声4音路输出,高低音、平衡、响度设置。
DVD
具备收音+DVD /VCD /MP3 /CD /CD~R /CD~RW功能,方向盘按键控制,可扩展免提电话,兼容其音频放大与信息显示及来电静音等;可扩展停车雷达辅助系统,兼容数据显示。
6) 仪表
仪表主要显示以下内容:车门、冷却液位、档位信号、机油压力、转速、ABS、充电指示、安全气囊、停车制动信号、安全带指示、排气故障、油位指示、左转向灯、冷却温度、右转向灯、大灯、刹车故障、车速、停车灯、发动机一般故障、发动机需维护、CVT等。
2、启动性能检测
1)常温起动性能试验
步骤1
在正常室温环境下进行起动试验,试验用蓄电池分别采用新的蓄电池和行使里程超过10000公里车辆中的蓄电池,分别将两个蓄电池充满电,检测充电前后蓄电池的端电压、以及蓄电池的内阻。
步骤2
将电量充足的新、旧蓄电池分别装载到两辆状态良好的车上,放置1h(便于部分控制模块进行自学习);利用电流钳、分流器、温度传感器以及数据采集仪采集起动时的电压曲线、电流曲线和水温。
步骤3
对进行上面试验步骤1、试验步骤2的新、旧蓄电池分别进行如下试验,在室温时,打开点火开关(不超过10s),起动车辆,起动后立即关闭,停放一段时间,整个周期为60s;按照以上次序循环进行,直至打开点火开关10s不能正常起动,停50s后还是不能起动。纪录整个试验中正常起动的次数(不包括试验步骤2的那次起动)。
2)低温起动性能试验
由试验部统一更换机油、冷却液,布置热电偶。将试验车辆在设定好温度的冷库中放置18~24h,然后进行冷起动试验,需要用万用表、蓄电池测量仪检测冷冻前后蓄电池端电压及其他可检测参数(如CCA等),试验过程中需要监测环境温度和水温,并做出纪录。
冷起动的最低环境温度可以根据目标市场的实际情况定义为~30℃~40℃之间。
充电
为获得指定容量的蓄电池,按照下图所示对蓄电池进行充放电处理。
放电
按照下图所示进行连接电路,以20Ah率电流的恒定电流对蓄电池进行放电,根据下面公式计算所需要的放电时间:实际放电时间=需要放的实际容量/20Ah率电流。
在实际放电过程中,电流是实时改变的,但我们可以通过观测电流表的变化来实时调节变阻器来保证放电电流保证在20Ah率电流左右进行放电,控制好放电时间,即可控制蓄电池的实际容量。建议用100%电量、90%电量、80%电量的蓄电池进行试验(根据试验资源和试验时间可以灵活安排),根据试验结果判断匹配效果。
3)试验数据记录与处理
需要检测的数据有:车辆进入低温舱前的蓄电池端电压;蓄电池内阻;冷冻18~24小时后的蓄电池端电压、蓄电池内阻;起动瞬间的电流曲线、电压曲线;起动时间;起动时的机油温度、水温;起动后的蓄电池端电压、蓄电池内阻。
根据以上纪录的数据和曲线分析蓄电池与起动器的匹配性能,并将检测的数据和曲线图做成图表,作为分析的依据,同可以为以后的设计提供参考依据。
3、电平衡检测
整个试验分几个阶段进行:1、怠速电平衡试验,2、城市路况电平衡试验,3、高速公路工况电平衡试验。下面分别介绍各个试验的试验方法。
试验中,利用数据采集仪、分流器、电流钳或电流传感器分别采集发电机、蓄电池、空调、冷却风扇、音响系统、灯具系统、雨刮系统的电流曲线,蓄电池、发电机的电压曲线,蓄电池、电器盒、保险丝盒的温度,并每分钟输出一次数据。将试验数据按照不同工况单独采集。将试验数据按照不同工况单独处理。
1)怠速电平衡试验
整个试验过程的环境温度为室温,车辆的电器负载的工作状况分别如下表所示。
先将车辆预热20分钟(对于连续试验的可以不进行预热处理),再开始数据采集,每个工况数据采集周期为1h。
2)城市路况电平衡试验
在城市路况下,经常出现堵车、限速等等情况,下表所示工况主要模拟城市工况的车辆运行状态。
试验时对路况进行如下设定:试验时间安排在交通高峰期,一般定义为7:20或者16:30开始试验,如上下班高峰期。试验期间雨刮需要运行5min以上。
试验中,利用数据采集仪、分流器、电流钳或电流传感器分别采集发电机、蓄电池、空调、冷却风扇、音响系统、灯具系统、雨刮系统的电流曲线,蓄电池、发电机的电压曲线,蓄电池、电器盒、保险丝盒的温度,并每分钟输出一次数据。
将试验数据按照不同工况单独采集。数据捕捉前需要按照规定工况预热20分钟,对于联系试验的可以不预热,直接进行数据采集。
3)高速公路工况电平衡试验
通过以上试验可以分析起动、怠速、频繁刹车等工况下各用电设备以及蓄电池的工作状况,我们还需要通过试验验证车辆在高速公路或者车辆稀少的路面上,以中高速行驶时各用电设备以及蓄电池的工作状况;我们可以按照以下试验来模拟该状态。在该运行情况下车辆的状态表如下表所示。
试验中,利用数据采集仪、分流器、电流钳或电流传感器分别采集发电机、蓄电池、空调、冷却风扇、音响系统、灯具系统、雨刮系统的电流曲线,蓄电池、发电机的电压曲线,蓄电池、电器盒、保险丝盒的温度,并每分钟输出一次数据。将试验数据按照不同工况单独采集。数据捕捉前需要按照规定工况预热20分钟,对于联续试验的可以不预热,直接进行数据采集。
4、温度场检测
温度场试验的目的是为了验证整车线束、蓄电池等产品工作温度设定是否合适,并根据温度场试验的结果对设计进行修正,保证产品的设计性能。温度场试验的试验方法如下。
1)试验工况
试验室要求:环境温度45度,太阳辐射950W/m2,水温小于118度,机油小于150度;试验工况一般规定如下:
130km/h 3% 坡度20分钟(5档)
40km/h 12% 坡度20分钟(2档)
40km/h 全油门20分钟(2档)
注:所有工况空调均开到最大档,全冷,内循环。
2)试验测量点
根据线束的走向,需要在整个线束、蓄电池中选择一些可能存在高温风险的点,布上温度传感器,通过温度传感器将在上面所述的工况的温度捕捉并加以纪录。为今后线束在机舱内导线选择以及线束和用电器在机舱内的分布提供一个参考元素。
3)实验数据分析
对于所有的数据采集点进行拍照,结合试验纪录的数据加以分析,对于接近或者超过的设定温度的线束或部件需要采取相应的措施,如重新布置,增加隔热装置,采用耐高温的材料等。
三、设计验证试验
下面来看看设计验证试验的主要内容。
1、单元电路控制逻辑验证
1)试验方法
在本试验中将分别验证各个单元电路原理,包括灯具单元电路、雨刮单元电路、音响单元电路、模块单元电路、仪表单元电路、开关单元电路、空调单元电路、底盘单元电路、动力总成电控单元电路、内外饰单元电路。
根据最终确定的整车电路原理和单元电路原理,模拟各单元电路,对各单元电路测试。
2)试验步骤
在实验台架上搭建电路,要求搭建的电路与单元电路原理图的控制逻辑一致,对于部分控制模块,可以利用开关等来模拟实现,整个控制策略必须与单元原理图一致;按照单元电路原理,模拟出理论上的控制策略;按照模拟出的理论上的控制策略,在搭建的电路中加以验证;纪录试验中各种控制策略的实际控制效果,验证各个电器零部件可以实现的电器功能以及可能存在的失效模式。
3)试验数据记录与处理
根据实际试验中,检测记录的控制策略,校对单元电路设计,并优化其中的不足,使得单元电路的控制策略更安全、更适用、更能体现人性化;同时根据验证的各电器零部件的功能,和实验中暴露的各种可能存在的失效模式,制定相对应的解决措施。对试验中的控制策略、零部件的功能定义等方面出现的问题加以分析,对于通过试验验证的比较合理的控制策略和功能定义,也要作详细的记录,并将优点描述充分,将试验中的优缺点整理,作为后期设计的参考数据库,为以后的设计服务。
2、线路设计验证
1) 验证保险丝的设计
试验目的
根据保险丝的设计计算说明书,验证设计的合理性和可行性。通过前期的试验,排查后期装车中可能出现的问题;同时可以为以后的设计提供数据库,作为以后设计的参考。
试验前准备
按照电器原理图中的保险丝的设计值选用保险丝,准备一个具有阻燃性的试验平台。
试验操作规范
具体的实验步骤如下:
按照单元电路原理,搭建实际电路,同时计算各个单元电路的负载功率所对应的电流值,以及所选择的导线所能承受的最大电流值;通过负载箱或者滑动变阻器等方法调节流经保险的电流值,将电流值控制在负载额定功率所对应的电流值;误差范围:100A(含100A)以下误差不超过0.2A,100A以上误差不超过0.5A。
下图为利用万用表、安培表、红外线温度计分别检测通过保险丝后的电压降、流经保险丝的电流、保险丝带载后的温度;必要时可以利用数据采集仪适时采集通过保险丝后的电压降、流经保险丝的电流、保险丝带载后的温度(120分钟内的温升);通过负载箱或者滑动变阻器等方法调节流经保险的电流值,将电流值控制在所选择的导线所能承受的最大电流值的±1%范围内.
利用万用表、安培表、红外线温度计分别检测通过保险丝后的电压降、流经保险丝的电流、保险丝带载后的温度;必要时可以利用数据采集仪适时采集通过保险丝后的电压降、流经保险丝的电流、保险丝带载后的温度、导线的温度(120分钟内的温升);各项试验中观测电器盒、保险丝盒壳体的外观,检测壳体温度,验证耐温等级以及阻燃性(接触部位温度)。
试验数据记录与处理
根据以上检测方法,记录带各种负载状态下的数据,并建立各种负载状态下保险丝电压降、流经保险丝电流、保险丝温度与带载时间的曲线图,通过实验数据和曲线图分析判断保险丝设计的合理性及可行性。
2) 检测电器盒、保险丝盒负载试验
试验目的
本试验主要验证电器盒、保险丝盒的热性能,防止因为电器盒、保险丝盒的热性能不稳定而导致电器系统的故障。
试验前期准备
分析单元电路图以及保险丝盒、电器盒的原理图,绘制试验图纸,准备一个具有阻燃性的试验平台。实验温度定义为室温。下图是保险丝试验的示意图。
试验操作规范
在本试验中需要模拟电器盒、保险丝盒在全负荷工况下的工作状态,具体的试验步骤如下:
a. 按照试验图纸,在具有阻燃性的平台上搭建试验电路;
b. 按照保险丝盒(电器盒)的负载功率,建立一个模拟负载,给保险丝盒(电器盒)中的所有保险丝(包括继电器)带上相应的负载;
c. 利用数据采集仪检测保险丝盒(电器盒)各点的温度正常带载n小时后,若保险丝盒(电器盒)没有达到图纸要求的最高温度,可以增加负载,验证保险丝盒(电器盒)达到图纸要求最高温度后的状态;
d. 检测保险丝盒(电器盒)表面被烧蚀的表面温度和负载功率。
试验数据记录与处理
a. 纪录保险丝盒(电器盒)带正常负载的情况下,保险丝盒(电器盒)表面温度和时间
之间的对应关系,并绘制曲线图;
b. 纪录保险丝盒(电器盒)表面温度到图纸要求的最高温度时的时间和负载功率;
c. 纪录保险丝盒(电器盒)表面发生烧蚀的时间和负载功率。
根据以上数据和曲线图,分析保险丝盒(电器盒)的耐温性能建立数据库,为保险丝盒(电器盒)的优化和今后的设计提供参考依据。
3、各电气件功能检测
1) 样件尺寸检测
对于供应商提交的所有样件必须附带尺寸报告,在供应商自荐报告合格的前提下,我们应该按照下发给供应商的图纸检测样件的尺寸,并出具尺寸检测报告。
2) 样件功能测试
样件要求
在项目开发P3阶段后期或P4阶段前期,电路系统工程师需要向项目组提交电路系统台架检测样件需求清单及到件时间要求。此清单应根据整车配置状态及整车EBOM来确定。
具体样件到位时间根据整车试制计划来确定,原则在样车总装前15天(或更长)测试样件要到位。此清单电路系统工程师及时更新,把到件情况及时反馈给项目及部门领导。电路系统工程师需要按照检测样件清单跟踪每个件的到件情况,对存在风险的样件要及时提出预警,并把相关情况反馈给项目组。
样件功能检测方法
电路系统工程师需要根据所负责车型各电器系统的功能规范制定相应的电路系统检测方法。此检测方法需要整车各电器系统工程师评审并会签。电路系统工程师负责搭建测试台架。测试台架应简洁、美观并易于操作。
台架搭建完毕后,电路系统工程师与各系统电器工程师一起按照前期制定检测方法对各电器系统进行测试,并对检测的情况进行总结,完成台架测试问题清单。此清单需要根据测试进展及时更新,并提交给部门室主任以上领导。测试完成后电路系统工程师要提交测试报告,测试报告需要各电器系统工程师及其科室领导签字。检测方法可以按照下相应格式填写。
样件功能检测方法
各电器系统测试完成后,电路系统工程师应针对样件检测的结果组织此次测试的评审工作。评审需项目经理、各相关电器系统工程师、电器部室主任以上领导参加。对测试中出现的问题进行分析,并要求文体责任人提出解决措施,以及具体更改计划,并保证装车样件的功能能够满足前期的设计要求。
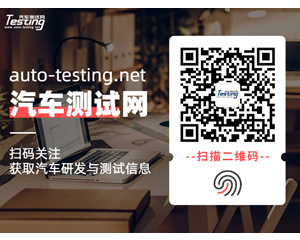
最新资讯
-
商用车及工程机械行业专场:NVH 及语音音频
2025-08-01 17:12
-
理想i8和重卡对撞测试引争议,东风柳汽发声
2025-08-01 15:52
-
艾德克斯IT-N2100 系列太阳能阵列模拟器
2025-08-01 15:43
-
ITECH重磅发布IT2705直流电源分析仪,重构
2025-08-01 15:34
-
现代汽车新一代混合动力系统:以技术革新引
2025-08-01 15:32