1 定义
汽车制动系统中摩擦副的摩擦振动使制动零件或车身产生共振并行程噪音和振动。
制动尖叫声和制动不平顺性是典型的制动噪音&振动问题,在北美乘用车市场有将近占比至70%的客户抱怨。
2 制动噪音&振动基础理论
2.1 胡克定理
F=-kx
2.2 静&动摩擦力
当滑动速度增加时,摩擦系数和摩擦力变小,不稳定的摩擦副状态导致了制动噪音和振动。
2.3 粘滑振动
胡克定理:
Fs=-kx
摩擦力Ff=u·mg
摩擦力是相对速度的函数
静摩擦力:Ff>|Fs|
动摩擦力:Ff<|Fs|
2.4 频率范围
3 制动噪音&振动分类
3.1 呻吟噪声(groan noise)
发生条件和噪声频率:
1)当制动踏板松开且车辆开始前进的一瞬间;
2)发生在低速和制动压力较小时:0.2-2rpm,2-5kg/cm³;
3)摩擦片动静摩擦力不同的影响;
4)噪音频率:50-300Hz。
对策:
1)选择和调试摩擦片材料
3.2 嗡嗡噪噪声或呻吟噪声(humming noise)
发生条件和噪声频率
1)当制动踏板松开后车辆开始很缓慢的移动或车辆转弯时;
2)尤其是发生在后制动盘;
3)噪音频率:200-400Hz
对策:
1)减小拖滞力矩;
2)增加悬架系统刚度
3.3 隆隆噪声或咆哮噪声、刺耳噪声
(Rumbling Noise或Roaring Noise, Grinding Noise)
发生条件和噪声频率
1)一般制动工况;
2)摩擦片表面凹陷引起,摩擦力相对制动盘发生了材料转移;
3)噪声频率:50-300Hz
对策:
1)改变摩擦片材料;
2)摩擦片切口调整
3.4 咔哒噪声(或当啷噪声、咕噜噪声)
Clicking Noise (ClunkingNoise, Grunt Noise)
发生条件:
1)一般制动工况,尤其是停车后的倒车行驶;
2)摩擦片垫耳撞击钳架的卡簧时;
对策:
优化摩擦片垫耳与钳架卡簧间得到间隙
3.5 咯咯噪声 (卡钳滑动的咯咯噪声, 摩擦片咯咯噪声)
Rattle Noise (CaliperSliding Pin Rattle, Pad Rattle)
发生条件:
1)松开制动踏板,在不平或粗糙路面行驶时金属零件彼此撞击的声音
对策
1)优化摩擦片间隙;
2)优化销轴与销孔的间隙。
3.6 尖叫噪声(Squeal Noise)
3.6.1 发生条件:
1)制动尖叫声是一种动态不稳定性现象,发生于制动系统的一个或者更多的固有频率上;
2)由制动系统生产的1-16Hz的噪音;
3)低频尖叫(1~3 kHz)一般涉及零件:钳体、钳架、转向节和悬架、摩擦片和制动盘;
4)由于人耳对1-4Hz的噪声很敏感, 低频尖叫被认为最为令人厌恶的制动噪音;
5)摩擦片和制动盘耦合主要产生中高频的尖叫噪声(4~16kHz)。
3.6.2 噪声特点
很难复现,这个现象基于如温度、湿度、速度和制动踏板力等多种因素条件形成。
例: 尖叫发生在天冷或湿度较高的天气条件下,一般条件下发生频率并不高,很难找到相应的对应措施。
3.6.3 影响低频尖叫噪声的因素
3.6.4 影响高频尖叫噪声的原因
3.6.5 尖叫噪声对策方法
调查、分析和验证方法:
1)整车试验;
2)台架试验;
3)模态试验;
4)有限元模拟分析。
对策:
1)减少激励,优化摩擦片的倒角设计;
2)增加阻尼,阻尼消音片选择;
3)改变零件的自然频率(制动盘、钳架、卡钳和制动底盘)
4 调查、分析和验证
4.1 整车试验
成功解决噪音问题的最终判定
北美的一般测试过程:
1)洛杉矶市交通测试:标准制动噪音和摩擦片磨损试验,对每个原装车辆不同路线的测试;
2)底特律郊区交通测试(DST)主:要用于DTV测试;
3)来自主机厂和供应商的其他测试:用于噪音研究和快速确认。
驾驶者的噪音主观评分、噪音记录、声压级数据和加速度数据在试验中被收集。
典型的 LACT 噪音测试结果:
1)尖叫事件可以在傅里叶频谱中识别;
2)噪音发生的次数和振幅被统计记录;
3)顾客其他额外的计算要求。
4.2 台架测试
1)提供噪音验证的可控环境;
2)相对整车试验,成本较低;
4.2.1 测试过程:
1)SAE J2521-AK测试基础上增加了增加了惯量制动
2)AK–起源于欧洲的测试程序(主要拖曳制动)
3)模LACT–一系列类似LACT驾驶条件的制动
4)以上几种测试的组合。
5)声压级数据一般在测试过程中收集。
典型的台架测试结果:
噪声发生可以根据频率、温度、压力和速度变化进行识别。
4.2.2 制动NVH试验的可重复性和可复现性
1)整车与台架试验的关联性;
2)由于更多零件的参与,整车和台架的低频噪声很难实现重复性和可复现性。环境因素,如天气、温度、湿度和道路粉尘都会影响试验结果。
改善制动NVH试验可重复性和可复现性的一些建议:
1)采用正确等级的测试硬件;
2)设置正确的测试参数;
3)确保测试零件的连贯性;
4)记录测试过程中所有的变化和有意义的事件;
5)适当的收集和分析数据。
4.3 模态试验
1)提供对部件和制动系统的结构动力学特性的理解;
2)零件模态测试测试了自然频率、模态阻尼比和摩擦片、制动盘、衬片、卡钳、钳架和转向节等的模态振型;
3)系统模态测试在整车制动系统上台架制动系统上测试。
4)锤击测试:快速且成本低;
5)激光测振:更加精确但昂贵
模态振型测试
扰度变形测试
典型的模态测试结果:
1)自然频率和模态阻尼比可以从测量的频率响应(加速度/力)函数曲线中推导;
2)由于系统零件耦合,单个零件的尖叫频率可能不同。
4.4 有限元模拟分析
干摩擦产生的制动力导致摩擦力有微小的起伏变动,这导致摩擦片周边零件的共鸣。摩擦力的起伏进一步放大则引起零件表面的相对振动并引起空气振动发出噪声。
制动尖叫的影响因素:
1)摩擦材料的物理特性,如摩擦系数的速度敏感性、制动盘热变形的热力因素和制动盘振动的结构因素等;
2)这些因素往往都是相互影响的。
4.4.1 有限元模拟分析
目前制动尖叫的主流分析主要集中在结构因素上,主要是制动零件的共振特性。
有限元模拟分析可以反复进行迭代设计优化,不需要制作样件试验。
两种分析模型:
1)制动系统不稳定模型(复域特征值分析)
包含所有的单边制动系统零件
2)摩擦片-制动盘-卡钳支撑模型(频率响应模型分析)
包含摩擦片、制动盘和卡钳,适合中高频尖叫分析。
有限元模拟分析,优化摩擦片举例:
5 采用阻尼垫片的方法减少尖叫噪声
在物理学中,阻尼可以减少任何振荡系统中的振动的振荡运动;
在力学中,摩擦力就是这样一种阻尼效应。
零速度初始条件下,取决于系统的阻尼值:
欠阻尼(蓝色曲线);
临界阻尼(绿色曲线);
过阻尼(粉色曲线)
在摩擦片上增加垫片或隔音材料是一种增加制动系统阻尼的方法,增加阻尼是减少共振的一种方法。
5.1 选择适当的阻尼材料的过程:
第一步:在台架上用不同的数据形成制动噪音生成模型和制动基准声压级地图;
第二步:通过模态分析下选择合适的阻尼材料;
第三步:在第一步中的噪音生成模型中验证选择的阻尼材料
5.1 在台架上用不同的数据形成制动噪音生成模型和声压级地图;
基准制动试验: 最高的SPL (声压级) 发生在7Hz, 温度约为 150°C ,声压级为25 bar
5.2.1通过摩擦片模态分析选择合适的阻尼材料
5.2.2通过制动盘模态分析选择合适的阻尼材料
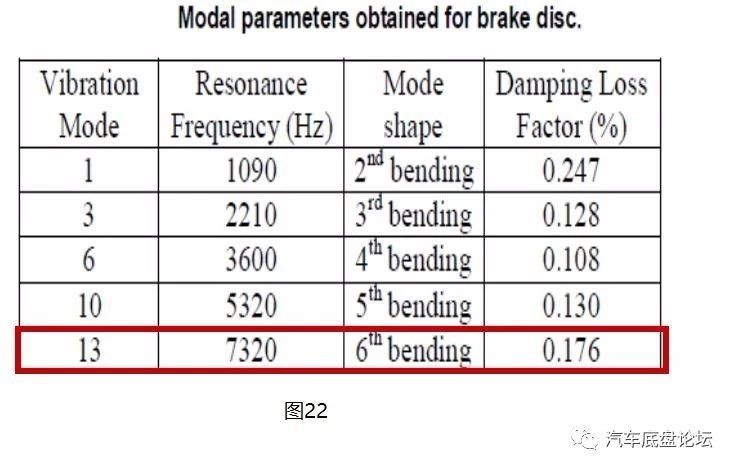
5.2.3 通过制动盘和摩擦片总成模态分析选择合适的阻尼材料
5.2.4通过摩擦片和制动盘总成模态分析选择合适的阻尼材料(在压力和温度下制动零件的振动响应)
当制动系统零件在一定温度和压力下工作时,零件的动态特性变发生了变化。
由于摩擦材料特性,摩擦片的变化比制动盘更明显
5.2.5通过摩擦片和制动器总成模态分析选择合适的阻尼材料(制动零件特性与温度的关系)
当温度上升时制动盘的刚度减小,则制动盘的响应频率趋于减小。
左侧视图展示了制动盘对不同温度的频率响应(基于一阶和二阶弯曲模型)。
5.2.6
尖叫噪声是制动盘和摩擦片弯曲振动模型耦合产生的,当这两个零件开始共振时,由于制动盘和摩擦片间阻尼减小,系统共振的系统阻尼便减小。可以通过采用约束阻尼层来获得额外的阻尼。
3)选择/验证消音片
将不同的阻尼垫片联结在摩擦片上,在烘箱内测试其频率响应函数以评估损失因子的变化。
在150°C时,#2 阻尼垫片在摩擦片损失因子上表现出最好的性能。
5.2.7制动系统总成分析
当系统发生耦合时,现代技术可以分析系统阻尼。
制动系统总成分析说明#2阻尼垫片是最好的选择,为了验证阻尼垫片选择结果。需要进行新的台架试验。
6 制动不平顺性(震动)
6.1 定义
驾驶员或乘客感受到的整车振动、痉挛或震动
发生时机:发生在制动停止时
感知方式:
——方向盘
——地板或前壁板
——座椅
——制动踏板
由制动力矩变化产生
——一般范围为5-60Hz
——频率随车速变化而变化
——一般每转一圈有1-2个脉冲,但可以增加到10个脉冲
6.2制动不平顺性的严重程度取决于:
制动力矩变化的幅度和频率
车辆敏感性
——转向系统和悬架系统的传递路径;
——共振频率和车辆零件阻尼。
制动不平顺性也称为震动或颤抖,通常用具体环境条件来细分制动不平顺性
热震动:制动盘温度> 200°C
冷震动:制动盘温度< 100°C
未磨损不平顺性:新制动盘
湿不平顺性:浸水
高速震动:制动速度>130km/h
6.3 高温震动(热震动)
制动盘在制动过程中变热,热碰撞引起盘在旋转方向上的波浪变形,导致制动力矩波动和振动
对策:增加制动盘的刚度和热容。
6.4低温震动(冷震动、老化震动)
车辆释放制动行驶,但制动拖滞引起制动盘磨损,导致制动盘厚度发生变化。当车辆行驶10000-20000公里后,制动盘会发生几微米的厚度变化。这种情况下制动会引起制动力矩波动,导致制动震动。
6.5低温震动原理
当制动盘较厚的部分通过摩擦片时,制动钳活塞和棘爪被压回,增加制动液压力;当制动盘较薄的部分通过摩擦片时,制动液压力减小。制动时制动液压力波动导致了制动力矩的波动,在悬架和转向系统中形成激励源,产生震动。
6.6 震动原因鱼骨图
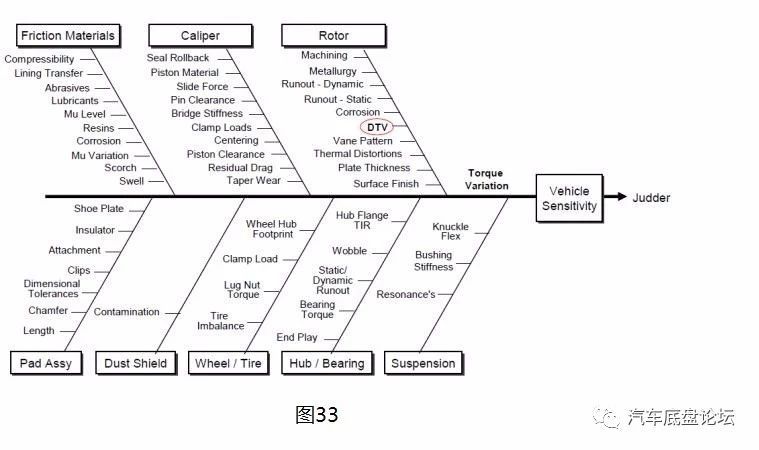
6.7 制动力矩变化
T = Fr·r = 2μ·FN·r = 2μ·P·A·r = c·μ·P·r
从制动力矩公式中可以看出影响制动力矩变化的因素
△T = c·μ·△P·r + c·△μ·P·r + c·μ·P·△r
虽然影响制动力矩变化的因素有三个,但制动液压力是主要影响因素。而制动盘厚度变化引起制动液压力变化
Fr:制动力
r:等效制动半径
μ:摩擦系数
P :制动液压力
A :活塞作用面积
C = 2A
6.8制动盘厚度变化影响因素
摩擦片材料转移至制动盘
热变形
腐蚀
制动拖滞导致制动盘的不均匀磨损
高速制动时摩擦盘接触面积变化导致的制动盘不均匀磨损是产生制动不平顺性的主要原因。制动盘磨损可以是单边磨损或双边磨损。
制动盘厚度变化范围为15-20um,是人体头发直径长度的一半,可以产生制动力矩50Nm的变化,这很容易引起制动不平顺性问题。
6.9行驶时制动或不制动引起制动盘不均磨损的因素:
1)制动盘装配公差(轴承、装配机械等)——期望为零
2)卡钳间隙(密封圈滚动、侧滑力、棘爪刚度等)——期望较高值
3)摩擦片材料攻击性和摩擦片尺寸——期望较低值
4)转向节和卡钳的负载变形——期望为零
需要考虑制动系统其他要求,如制动踏板感、制动盘防腐、车轮防腐等,最小化制动不平顺性最好考虑制动系统所有涉及零件的交互影响而不是其中一两个零件的影响。
6.10减少震动的对策
1)最小化制动系统中的激励
2)最小化车辆的响应
——在悬架中增加隔离或阻尼;
——在车身和转向管柱中增加阻尼零件;
——改变车辆零件的共振频率。
7 总结
1)近些年乘用车的低频噪音问题较多,NVH问题成为车辆开发过程中的主要问题;
2)制动噪音和振动出现在不同的使用环境和工况当中;
3)制动噪音和振动发生的概率与使用条件相关,如制动盘温度、制动液压力、摩擦片材料物理特性、磨损程度和驾驶者输入。这也是为什么现代科技仍无法完全解决制动噪音和振动问题。
4)在设计阶段需要提前对制动噪音和制动问题进行设计规避;
5)试验分析技术和噪音&振动仿真技术是汽车制动设计不可或缺的手段。