电池箱静强度分析的简化和精细分析方法
电池箱是电动汽车的核心部件之一,设计高强度、高刚度、高安全性、高轻量化的电池箱,对电动汽车的发展具有重要意义。文献为电池箱的强度分析和结构优化提供了有益的参考,但是,这些研究大多是建立粗略的电池箱模型,采用均布载荷或质量点的形式进行加载,并没有考虑电池组的内部结构、电池组与箱体的接触非线性、BMS等电气附件对箱体变形的影响,力的传递路径与实际情况并不吻合。相关研究表明,过于简化的电池箱模型会导致响应的严重失真,进而影响后续的结构优化。
为了精确地分析电池箱箱体的结构响应,保留了电池组内部电芯、电芯压杆、螺柱等传力部件,建立了考虑电池组、托架、压板、加强板、紧固螺栓、BMS电气附件以及外壳的精细化模型,分别采用质量点模型和精细化模型研究电池箱的静态性能。通过对比,精细化电池箱模型的结构响应更符合实际。
1 电池箱精细化有限元模型
目前已有的研究大部分采用质量点模拟电池组,虽然建模速度快,计算时间少,但是电池组对箱体冲击力并不是均匀分布在箱体上,箱体变形并不符合实际。因此,有必要建立考虑电池箱内部电芯、托架及BMS等电气附件的精细化有限元模型。电池组内部有许多电芯、压板、隔板、电芯连接片、模块连接片、固定螺栓,结构十分复杂,考虑到仿真的难度和准确度,该精细化电池箱模型主要体现在以下方面:
1)电芯数量过多,考虑到建模的时间、计算量、接触面,将12个电芯组成的电池组视为一个实体,传力的大小和路径比质量点更精确;
2)保留电池组主要的传力部件,例如上压杆、内压杆、固定螺栓和外壳,保证电池组的惯性冲击力按精确的路径作用到箱体底板;
3)考虑电池组与底板、压杆与电池组之间的接触非线性,保证电池组的惯性冲击力按精确的大小作用到箱体底板。
4)简化程度低,仅仅忽略对静强度影响不大的电芯连接镀镍铜片、模块连接片等。
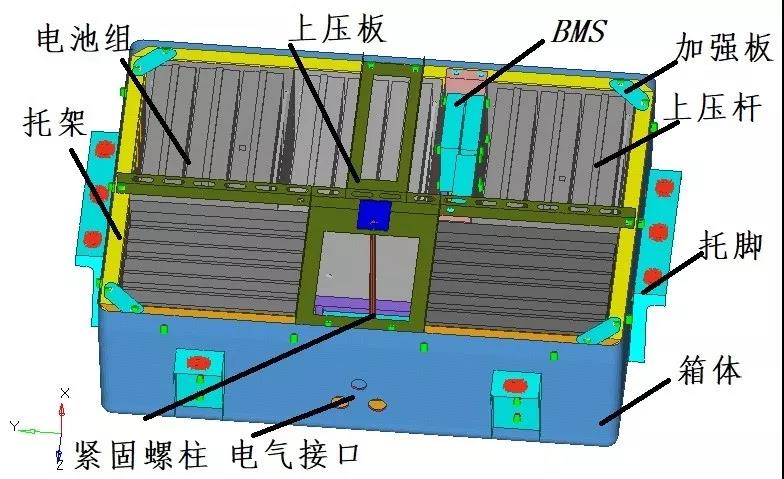
由于箱体、压杆、底板等部件多为板壳类结构,所以采用壳单元模拟;电池组采用六面体单元模拟;电池组内部的固定螺栓不承载电池组载荷,采用CBEAM梁单元模拟;上压板与底板的紧固螺柱起局部加强作用,采用六面体单元建模;托脚与箱体、箱体和箱盖、托架和压板等之间的螺栓连接认为不发生强度失效,采用REB2刚性单元模拟;电池箱托架之间的点焊、加强板的焊接等采用焊接单元CWELD模拟;电池组与托架、托脚与箱体、托架与箱体之间的接触均建立非线性接触。电池箱的精细化模型如图所示,单元尺寸为5mm×5mm,共计单元289503个,节点325832个,雅克比最小为0.7,质量非常高。
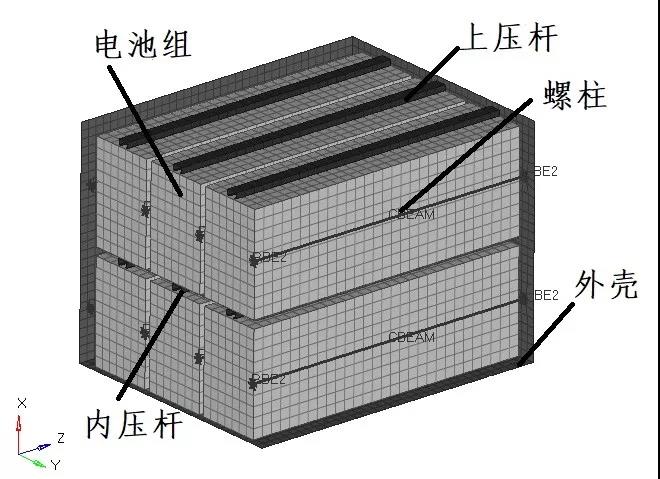
2 电池箱静强度的对比分析
电池箱静强度分析的加载方式主要有均布力、均布载荷、质量点等,这三种方式往往需要很大的动载系数,电池箱的应力和变形十分保守。为对比不同加载方式的响应差异,分别采用质量点模型和精细化模型进行加载。电动汽车行驶工况繁多,不可能穷尽。有文献选取了垂向颠簸、左转弯、右转弯、前进制动、倒车制动五种工况,分析表明垂向颠簸工况下电池箱的应力状况最恶劣,安全系数最小,为1.54。故本文以颠簸工况为参照,对整体施加垂向加速度3g(X负方向)。电池箱通过托脚和螺栓连接在车架上,故约束托脚螺栓孔处中心点X、Y、Z的平动和转动自由度,模拟与车架的固定连接。
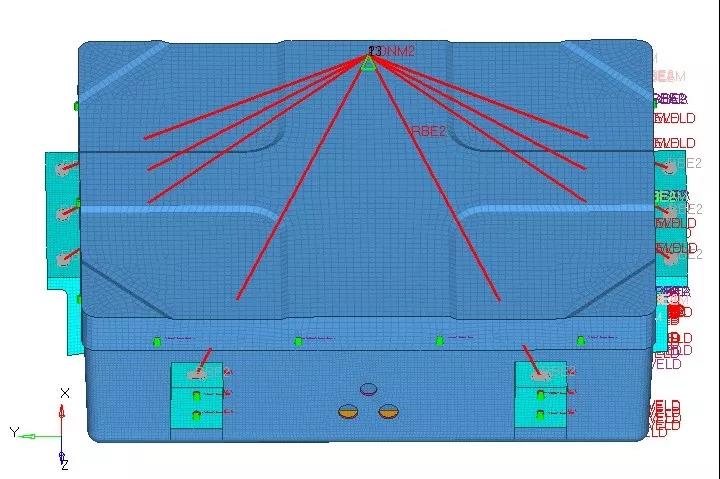
2.1 形变分析
1)质量点模型。在质量点模型中,由于箱体和箱盖仅仅起到密封、绝缘的作用,并不直接承受电池组载荷,所以重点研究托架的变形和应力。采用质量点模型的形变分布如图2所示,从图中可知,托架的整体变形表现为底板a、压板b中心的垂向弯曲,形变量由底板a中心位置向外呈辐射状减小,最大形变量为0.58mm;模型的柔度为568mm/N。
2)精细化模型。采用精细化模型的形变分布如图3所示,从图中可知,托架的最大形变发生在底板C处,最大形变量为0.12mm。形变主要表现为底板C、纵梁A以及BMS的垂向弯曲,并没有呈现出图2所示的中心向外辐射状。底板C、纵梁A处形变较大,是因为该侧布置了三个电池组,惯性冲击载荷较大。模型的柔度为22mm/N,刚度大幅提高。
由于质量点模型和精细化模型的传力大小和路径的不同,导致最大形变出现的位置和大小也不同,精细化模型的形变更符合实际。
.jpg)
图2 质量点模型形变云图
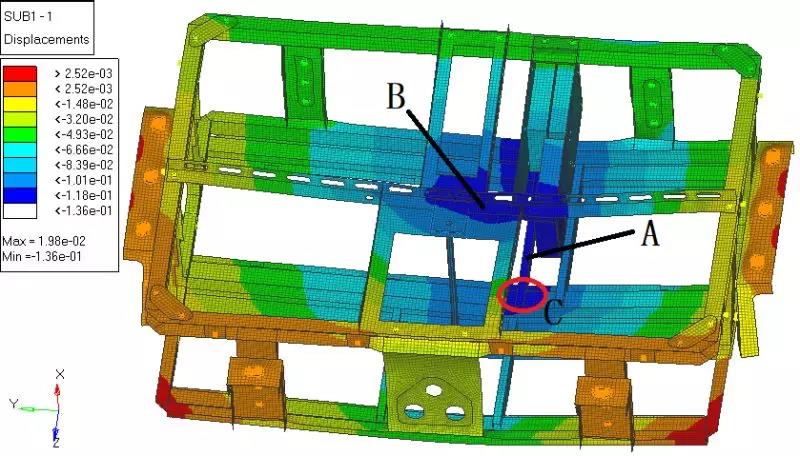
图3 精细化模型形变云图
2.2 应力分析
1)质量点模型。采用质量点模型的应力分布如图4所示,从图中可知,底板的应力分布很不均匀,最大等效应力出现在d处托脚螺栓孔附近,为101MPa,安全系数为2.3。
2)精细化模型。采用精细化模型的应力分布如图5所示,从图中可知,托架底板整体的应力较低,最大等效应力为102MPa,出现在D处所示的托脚螺栓孔附近,安全系数为2.3。
这两种模型的最大等效应力很接近,均出现在托脚的同一个螺栓孔处;底板中部肋上的应力值也很接近,约为25MPa。这说明质量点模型和精细化模型的托脚螺栓孔、底板的应力分布差异较小。
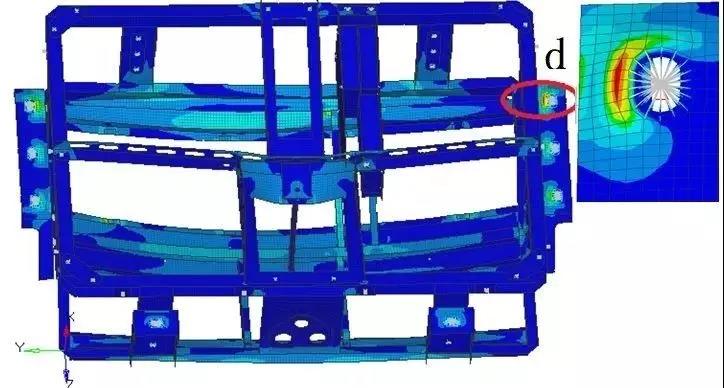
图4 质量点模型应力云图
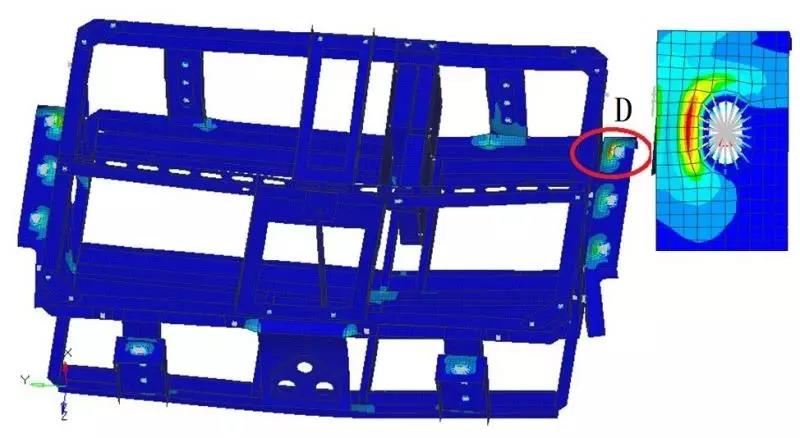
图5 精细化模型应力云图
2.3 电池箱静强度综合评价
根据材料力学理论,在一般的静强度分析中,塑性材料的安全系数一般取1.5~3.2。黄明昌等人依据多年的汽车动力系统领域研究的经验,对电池箱的静力学形变给出参照,在3g加速度载荷下,电池箱内结构件的形变量不得超过3mm。由前面的分析可知,质量点模型和精细化模型的最大形变、最大应力均满足要求,精细化模型的形变和应力分布更符合实际,应采用精细化模型的响应作为结构优化的参考。
3 结 论
采用质量点模型和精细化模型对电池箱的静态性能进行对比分析。与传统的质量点模型相比,全接触式的精细化电池箱模型的传力大小和路径更为准确,得到的形变和应力更符合实际。对后续的尺寸优化、形貌优化最大变形节点、最大应力节点的选择具有积极意义。
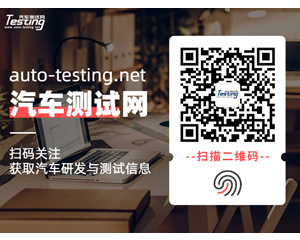
编辑推荐
最新资讯
-
商用车及工程机械行业专场:NVH 及语音音频
2025-08-01 17:12
-
理想i8和重卡对撞测试引争议,东风柳汽发声
2025-08-01 15:52
-
艾德克斯IT-N2100 系列太阳能阵列模拟器
2025-08-01 15:43
-
ITECH重磅发布IT2705直流电源分析仪,重构
2025-08-01 15:34
-
现代汽车新一代混合动力系统:以技术革新引
2025-08-01 15:32