集成软件方案解决齿轮啸叫的重要性
齿轮啸叫的系统分析
齿轮啸叫是一种NVH现象,通常来源于齿轮啮合时产生的传递误差(TE)。理论上,一个具有理想渐开线形状、无限刚度且没有错位的齿轮副将以设计的速比精确地传递角速度。然而,现实中,没有齿轮是理想的,例如,轮齿弯曲和系统变形引起的错位都将使齿轮处于非理想状态。
TE是输出轴在理想和实际运转状态下角位置的差异(参考1)。其他潜在的、但不常见的、基频与齿轮啮合频率相同的,齿轮啸叫的来源,包括:轴向往复力,其中合力的轴向位置在整个啮合周期内波动,导致在齿轮上产生波动力矩;摩擦力,来自齿轮在啮合时的相对滑动(参考2)。
传递误差可以被认为是在齿轮啮合线上,由非理想啮合条件引起的一个周期性的相对位移。TE可以通过从齿轮啮合、到轴和轴承、再传递到变速器壳体的路径来动态激励变速器。齿轮啸叫是从壳体发出的音调噪音,或由壳体传递、从其他部件发出的噪音。因此齿轮啸叫不应该仅被视为齿轮问题,而应被视为由齿轮激励的系统问题。
作为一个典型的来源-路径-响应动态现象,齿轮啸叫问题有时很难解决。通常的解决方案是通过齿轮微观修形使激励最小化。尽管控制传递误差能够降低齿轮啸叫———通常这也是最好的办法———但是如果系统中的其他部分对齿轮啮合激励高度敏感,那么传递误差最小化后的齿轮啮合仍可能引起齿轮啸叫问题。激励过程中的每个阶段都应该被考虑,以用于寻找潜在的解决方案。此外,可以通过针对齿轮啸叫优化齿轮宏观参数和通过考虑支撑结构和壳体的刚度和质量等来拓展解决方案的空间,以便达到更好的改进效果。
由于齿轮啸叫是一个系统层次的NVH问题,为了对系统激励的各个阶段进行仿真并对潜在解决方案进行虚拟测试,需要一个全面的系统的建模和分析的方法。
全面的测试和仿真方法
为了解决NVH问题,需要将经验与正确的工具相结合,以便找到花费最低成本和最少时间的解决方案。高效的NVH解决办法需要相应的流程:在该流程中,精确的测量和详细的CAE仿真可以共同进行,测试和分析团队之间可以使用集成软件方案进行数据处理和无错传输。SMT提供的齿轮啸叫NVH集成软件解决方案,能够在集成环境下,完成无缝数据传输、进行测量数据采集和分析以及相应的系统层次的仿真(图1)。
本文的目的是讨论这些集成软件在解决齿轮啸叫问题过程中扮演的角色,而描述完整的问题解决方法超出了本文的范围。
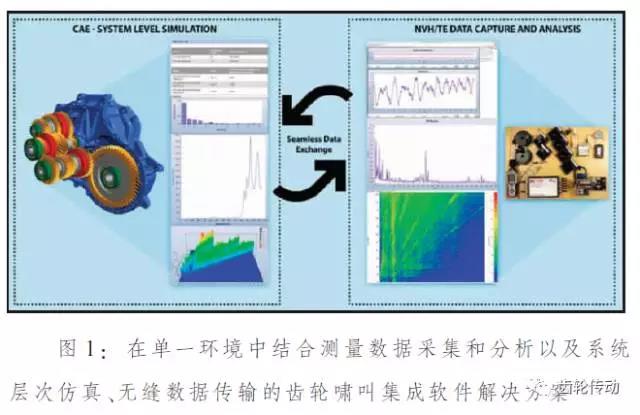
建议第一步首先检查制造和装配质量。如果质量差,例如超出了要求的公差,那么TE可能会高,这些问题需要在设计步骤之前得到解决。软件在这个阶段扮演一个重要的角色:用SMT的MASTA软件(参考3)进行圆柱齿轮制造仿真,可以帮助提升制造质量并改善其产生的TE;此外,MASTA软件还可以进行参数研究来确定和调整制造公差,从而减小组件之间传递误差的变化。
软件在进一步的解决过程中扮演两个非常重要的角色:
1)在测试环境下需要进行高保真数据记录来采集测试结果,并需要使用数据分析工具对测试结果进行有效分析,以便确定相关特性以及产生这些特性的主要系统因素。
2)在仿真环境下,需要先进的系统层次的仿真工具来对系统进行多方面详细仿真,相关详细内容将在本文稍后部分进行描述。建立起仿真和测试的关联性后,仿真模型因此能够在虚拟环境下被用于评估潜在方案对需求和目标的影响。在虚拟环境下改变组成部分的参数是快速、低成本的方法,并能够最大限度的减少对昂贵且耗时的硬件试验和试错循环的需求。
集成软件解决方案可以使这些任务在一个单一的软件环境下进行。在测试阶段,可以用专门的、便携式的、进行噪音和振动及传递误差测量的硬件来采集数据,然后使用SMT的TE和NVH数据采集及分析软件--MEASA进行后处理和分析。进一步地,数据分析工具可以连接到SMT的变速器设计分析软件MASTA(参考3),在相应系统分析模型中潜在的激励阶次可以被传输到MASTA中,以便在处理测量数据的同时能够更容易地确定来自变速器零件的贡献。在仿真环境下,MASTA可以对齿轮啸叫问题进行多方面分析,在该软件(图2)中可以方便地建立一个单一系统模型。
通过使用自动构建的不同保真层次的分析模型,一组参数化输入可以用来对一系列的失效模式和感兴趣的现象进行分析。针对齿轮啸叫相关的分析包括:在一系列工况下的完整系统的静态分析,用于计算系统变形以及对零部件耐久性的影响;加载齿轮啮合接触条件下的准静态分析,用于计算接触应力、齿根应力、传递误差和往复力;整个系统的模态分析,用于计算系统固有频率、振型和模态能量;整个系统的齿轮啸叫分析,用于计算系统由于传递误差激励所产生的动态响应。
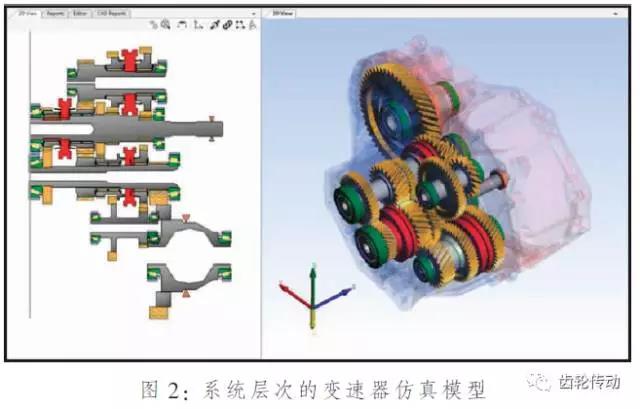
测试数据采集和数据分析软件
典型的齿轮啸叫测量包括:通过麦克风进行噪音测量,通过加速传感器进行壳体振动测量,通过角编码器进行传递误差测量。
齿轮啸叫测量应包括整车试验,这样可以在不同油门开度的车辆加速和滑行状态下采集完整运转范围的数据,而台架试验应该在隔离并了解变速器和传动系统噪音来源的条件下进行。在将台架测试结果和整车测试以及原始主观噪音问题关联在一起时要十分小心。相对于整车,台架上不同的边界条件可以显著地改变系统的动力学以及问题区域的频谱(参考4)。
精确的数据采集需要经过校准的麦克风、加速传感器和高保真度的数据记录。此外,还需要一个精确的转速信号用于分析部件的阶次。测量数据可以使用MEASA数据采集和分析软件进行采集和分析。数据分析工具允许用户以多种方式处理数据。通过连接到变速器系统模型,潜在的激励阶次和零件以及相对应的谐波可导入到数据分析工具中,这样可以方便的识别出指定阶次和总噪音/振动的主要成因。关键图包括瀑布图和阶次切片,提供对于总噪音具有特殊来源和音调的噪音的定量结果(图3)。
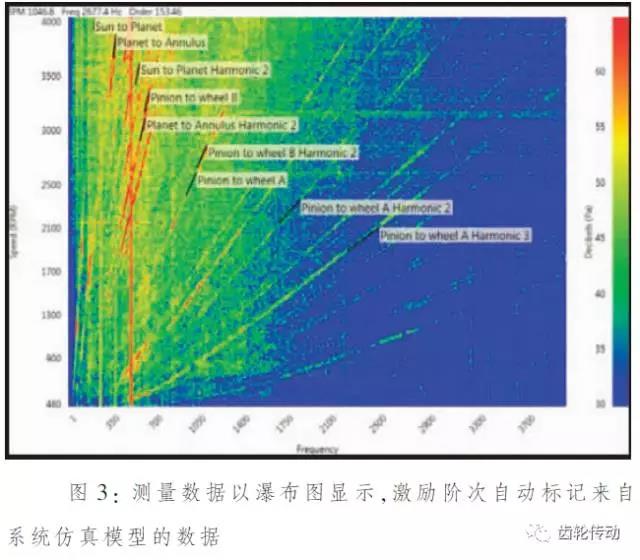
尽管没有噪音和振动测量那么常见,齿轮啸叫的来源———加载下的传递误差,可以使用角度编码器进行测量。对于测试台架上的变速器或传动系统,编码器可安装在输入和输出轴上以便测量整个变速器,也可跨坐安装于子系统之上以便测量该子系统。与噪音和振动测试结果相同,MEASA软件能够采集和分析TE测试结果。傅里叶分析用于识别不同阶段的主要因素,而TE值能通过齿轮基圆半径将角度转换为线性值。通过与系统模型相连,能够在数据分析工具中导入齿轮啮合阶次和相应的谐波,以便快速识别。
通过使用这些测量和数据分析技术,能够对噪音问题的性质进行量化,并且可以识别变速器中潜在激励的贡献。但是如何进行设计变更,评估对噪音问题的影响,以及找到经济有效的解决方案?这就是先进的仿真软件在解决问题方法中扮演的角色。
完整的系统仿真
一旦通过测量和数据分析技术确定齿轮啸叫的成因,仿真软件在有效地评估潜在的解决方案时起着至关重要的作用。齿轮啸叫是一个系统层次的问题,解决方案可以从齿轮的宏观参数设计,齿轮微观修形设计,系统的刚度和质量,TE传到壳体的传递性等方面进行考虑,先进的软件进需要能够完成不同侧重的分析。需对设计变更进行有效的评估,不仅要考虑对噪音问题的影响,还要考虑其他设计重点,例如,不能降低耐久性。耐久性、加载轮齿接触和动态响应分析可使用单独的商业FE软件包进行。但这个方法有问题,因为它需要不同保真度水平的模型来进行各方面计算,然而,模型的建立非常困难,并且很难通过模型快速地分析设计变更带来的影响。
另一方面,集成CAE软件,如MASTA,为工程师使用单一的模型和参数进行这些分析提供了工具。此外,快速创建模型,为复杂设计变更提供了灵活性,并能在无缝联接的工作流程中即时获得结果。分析速度足够快可以进行参数空间DOE研究,包括在考虑制造和装配公差的基础上评估设计变更产生的鲁棒性变化。
齿轮啸叫问题的相关分析可以在系统层次模型中进行。首先,通常在完整运转范围内进行一系列静态分析,以便计算系统变形,包括齿轮啮合的错位量,零件的耐久性等。获得耐久性基准结果,并和设计变更后的结果进行对比,用于确定在耐久性方面没有做出让步。基于FE的系统变形模型包括:轴,视为Timoshenko梁单元;轴承由考虑到了全部几何信息、间隙、预紧等的专门的非线性接触方程计算的模型代表;齿轮啮合由专门的非线性接触模型代表;壳体和复杂的异形轴以从全有限元模型中进行动态缩聚获得的刚度和质量矩阵的形式包含到模型中。轴承、齿轮、轴和其它的耦合零件的耐久性是通过该零件变形和载荷的分析结果是否能通过相关国际标准来确定的(参考5-7)。
齿轮啸叫问题的解决方案并非总是优化齿轮微观修形,但因为它相对容易一些,所以通常将其作为首先研究的区域。在开发过程的后期,由于对制造过程影响最小,需要的工具最少,这是最容易实施的方法。TE的计算可以使用加载轮齿接触分析(LTCA),扭矩、错位量、齿轮宏观参数和微观修形作为输入条件。精确的LTCA对确保TE的计算精确性是十分重要的。有限元和赫兹接触的程序被用来精确捕捉每个接触位置的刚度,同时提供适合评估微观修形参数变化和公差鲁棒性的快速计算(图4)。这样的计算在精度上堪比全有限元接触分析,同时速度上快了许多个数量级。
软件中可以自动建立齿轮宏观参数的有限元模型,该模型用于在考虑轮齿间啮合的基础上,获取齿轮轮齿的弯曲和旋转刚度。通过结合弯曲刚度与赫兹线接触刚度,可计算任意潜在接触点的总刚度。潜在的接触线被分成条状,根据力平衡和匹配性条件建立方程并求解(参考8),以便计算啮合时的载荷分布和输入扭矩下的传递误差。LTCA可以用于优化齿轮微观修形和宏观参数以使传递误差最小。必须考虑到在整个载荷范围内,推荐设计的鲁棒性将随载荷变化而变化,而错位量也将随齿轮微观修形在可制造公差范围内的变化而变化。
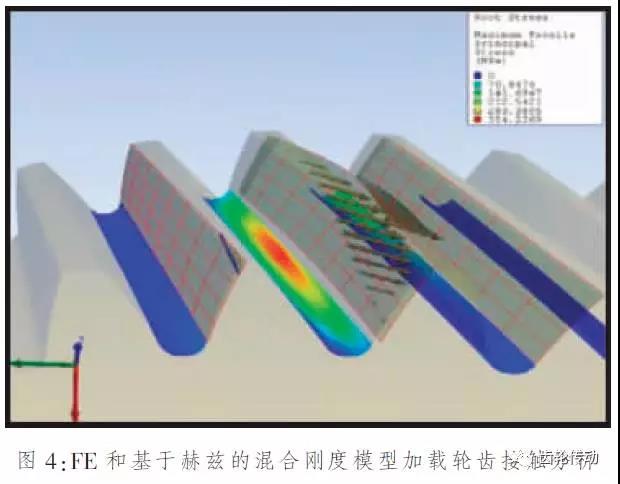
在上述分析工作流程中,假设系统变形影响轮齿接触,但是轮齿接触条件不会影响系统变形。因此,如上述假设,使用一个静态系统层次模型进行错位量的计算,这些错位量,假设在整个啮合周期内都是恒定不变的,作为轮齿接触计算的输入。这些假设大部分情况下是有效的,但也有例外。在一些重要的情况下,例如行星轮的轮齿接触条件,行星轮啮合间的相互作用意味着系统变形量和轮齿接触条件需要通过耦合计算解决。在这样的计算中,上述假设不再成立,并且计算了错位量的变化。此外,行星系统的接触条件可能随着行星架旋转而改变,因此需要进行耦合计算。在此讨论的软件解决方案也提供了这样的计算。
轮齿接触分析结果可以很好的验证分析模型是否正确建立。接触斑点试验是一个简单和常用的试验,接触斑点试验结果可以直接和分析结果进行对比(图5)。如果关联性好,这样对分析模型就有把握,说明计算的错位量,微观修形输入,在测试的载荷下计算的载荷分布都是正确的。如果进行TE测试,测量的和计算的TE可以直接进行对比。
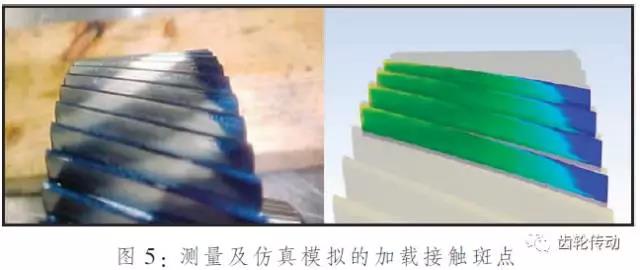
系统动力学的分析可以通过模态和频率响应分析进行。对于系统给定载荷输入的模态分析,可自动建立该载荷下的非线性静态分析模型的线性化模型。因此可以在计算得出不同工况下的固有频率和相应的振型。坎贝尔图用于识别潜在的系统激励,例如,齿轮啮合频率或其不同谐波与系统固有频率相交。更进一步地,通过振型的能量分布可以直观的识别出可能引起共振的主要零件(图6)。目标是尽量减少工作频率范围内的固有频率的数量,并将出现在范围内的固有频率彼此分离。
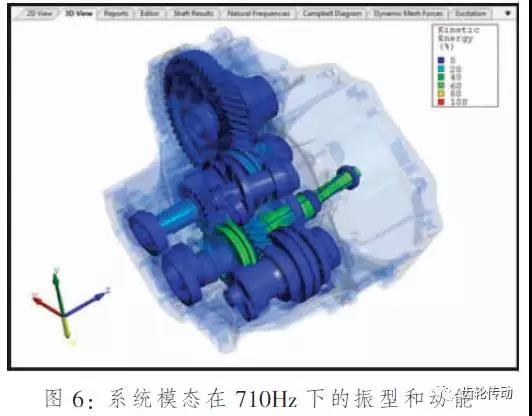
由Steyer等人引入的计算传递误差系统响应的方法可以用于计算在虚拟加速传感器位置的壳体加速度(参考9)。由于激励是周期性的,加载情况下的刚度可以认为是线性的,在频域下计算可以运行得非常快速。静态传递误差是系统假定的激励输入,第一步是计算齿轮啮合时的动态力,这个动态力导致啮合处的相对位移,而该相对位移由传递误差给定。这个动态啮合力,由齿轮啮合时每侧的动态柔度计算得出。动态啮合力作为激励施加到系统模型上,用于计算系统中任意一点对此激励的响应。瀑布图可以绘制模型上任意一点的动态响应(图7),并可以与噪音和振动测试所获得的加速传感器和/或麦克风数据进行对比。
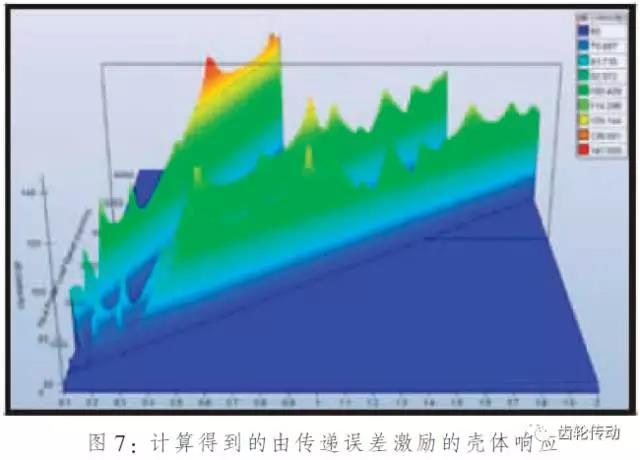
一旦虚拟模型与测试数据相关联,可以通过瀑布图和固有频率识别出对问题频率响应的模态。然后可以通过振型和能量贡献识别出这些模态中引发齿轮啸叫的零件。获得结果后,可以对这些零件的设计进行调整来改进分析模态的动态响应。一旦在虚拟环境下获得了需要的结果,可以在样机上对设计做出相应的变更,并测试用来确认是否达到改进期望。
使用集成软件方法解决齿轮啸叫的优点:
*在虚拟测试环境下使用目标方案减少了产品开发时间
*通过减少零件测试降低产品开发成本
*在产品发布之前可以对产品变化进行研究并使其最小化
总结
变速器开发周期是一个复杂并且昂贵的过程。随着市场,如EV和HEVs,对低噪音变速器和动力传动系统的需求不断增加,设计人员和分析人员面临更大的压力,设计人员需要设计出低噪音的产品,分析人员需要快速有效地解决已知的齿轮啸叫问题。通过结合可靠的方法、经验和正确的软件工具的方式可以获得快速经济的解决方案。
软件在这一过程中扮演重要的角色。在集成的CAE环境下评估、控制和微调设计来解决齿轮啸叫问题,如SMT所提供的产品,测试数据采集和数据分析,加上先进的仿真方法,两者无缝集成,为工程师提供了灵活自由的办法来获得新的高品质产品,而不再单独依靠昂贵又耗时的物理样机。
参考文献
1.Smith,J.D.GearNoiseandVibration,SecondEdition,MarcelDekker,Inc,2003.
2.D.R.Houser,D.R.etal.“DeterminingtheSourceofGearWhineNoise”,GearSolutions,February2004.
3.www.smartmt.com/masta
4.Meinhardt,G.etal.“CorrelationofAxleEnd-of-Line(EOL)NVH Performance and Laboratory Dynamometer Performance,”SAE2005NoiseandVibrationConference,005-01-2306.
5.BSISO 6336-2;2006 (E).CalculationofloadCapacityofSpurand HelicalGears-Part2:Calculation of SurfaceDurability(Pitting),2006.
6.BSISO 6336-3;2006 (E).CalculationofloadCapacityofSpurand HelicalGears-Part2:Calculation of ToothBendingStrength,2006.
7.ISO/TS16281:2008(E).RollingBearings:Methods forCalculationtheModifiedReferenceRatingLifeforUniversallyLoadedBearings, 2008.
8.Conry,T.E.andA.Seireg.“AMathematicalProgrammingMethodforDesignofElasticBodiesinContact,” J.A.M.ASME,2,1971
9.Chung,C.andG.Steyeretal.“GearNoiseReduction Through Transmission ErrorControland Gear BlankDynamicTuning,”SAENoiseandVibrationConference1999-01-1766
- 下一篇:扭矩测量的重要性
- 上一篇:齿轮仿真需要Simpack的原因
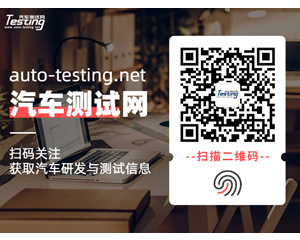
最新资讯
-
商用车及工程机械行业专场:NVH 及语音音频
2025-08-01 17:12
-
理想i8和重卡对撞测试引争议,东风柳汽发声
2025-08-01 15:52
-
艾德克斯IT-N2100 系列太阳能阵列模拟器
2025-08-01 15:43
-
ITECH重磅发布IT2705直流电源分析仪,重构
2025-08-01 15:34
-
现代汽车新一代混合动力系统:以技术革新引
2025-08-01 15:32