电池的碰撞安全,这车是近几年最好的设计
大压铸和复材虽然是车身结构创新的方向,但是短期内都很难在普通车型上普及,常规的车型结构也很难出现颠覆性的创新。所以现阶段新能源汽车车身领域的创新和竞争都集中在资源整合上,谁能更好的从整车的角度去规划结构的设计、去精准的分配底盘、电池、车身的能量和性能需求,谁就能最大化提升整车的竞争力。
01
—
bz4x充分发挥了e-TNGA平台资源整合的优势
丰田推出全新的TNGA平台之后,产品整体的开发理念和竞争力都得到了大提升。这一点可以被其销量和各种安全评价成绩所佐证。在汽车上销量上丰田持续霸榜全球各大细分市场的榜单,产品安全评价的成绩也基本上横扫了E-NCAP和IIHS等顶级安全评价规程。
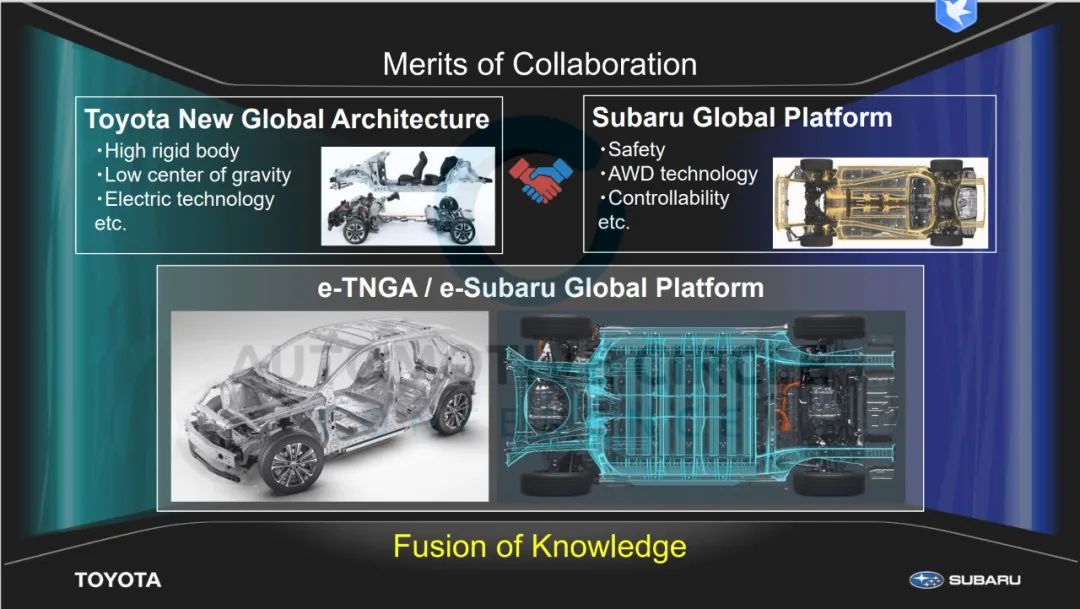
但是我们仔细去研究丰田TNGA的数据和核心理念后,会发现它并没有什么远超行业发展水平的数据,也没有像大众各大平台一样夸张的零件部件通用率。它所呈现的更像是一种开发理念,为提升产品竞争力而固化的一种理念:1、高刚性的车身;2、更低的重心;3、电子化的技术等。整车的布置和设计都要围绕以上可提升车型产品力的出发点来开发,并不强调所谓的零部件通用率,毕竟通用率更适合套娃式的造型和固化式的供应体系,对于想要把产品打造好、把车卖好并没有太大的意义。
我们结合丰田现阶段的产品来分析,会更能体会丰田TNGA平台开发出的产品与当前行业主流新能源汽车产品的差异,比如在电池的碰撞安全防护上。
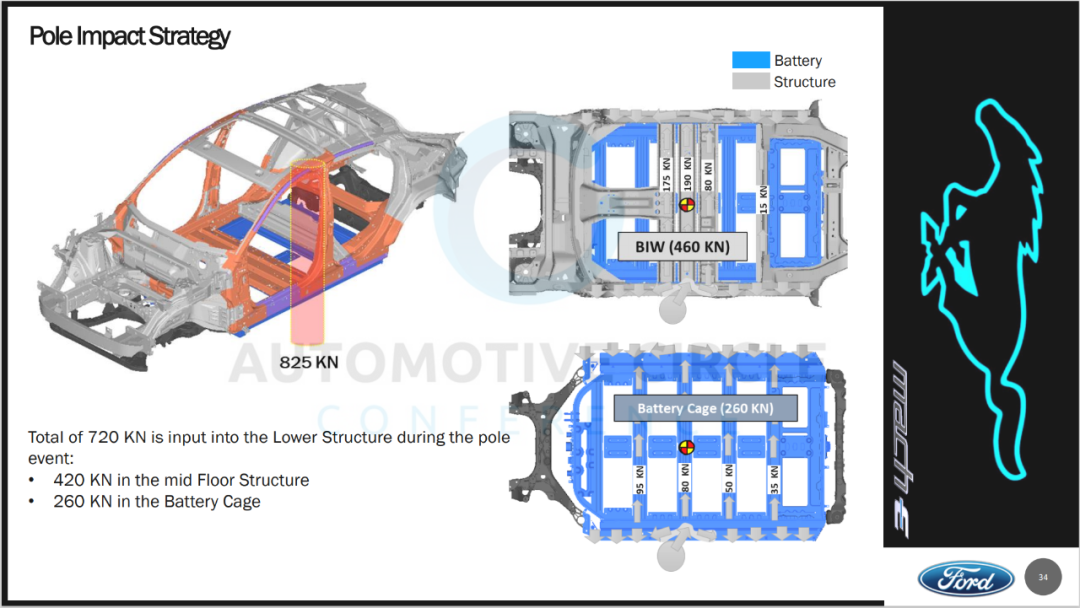
现阶段大多数车企在电池碰撞安全的设计上,都是将车身作为主要的防护结构,电池包处在车身门槛、纵梁等主要框架结构件的呵护下,这源于这些车企的电池开发部门过于强势,不允许电池包参与到碰撞安全的结构能量传递中去,当然也可以理解为企业集成安全开发部门能力较差。仅有福特等少数车企能精准地对侧碰、柱碰工况下车身框架结构和电池包壳体进行碰撞能量分配。
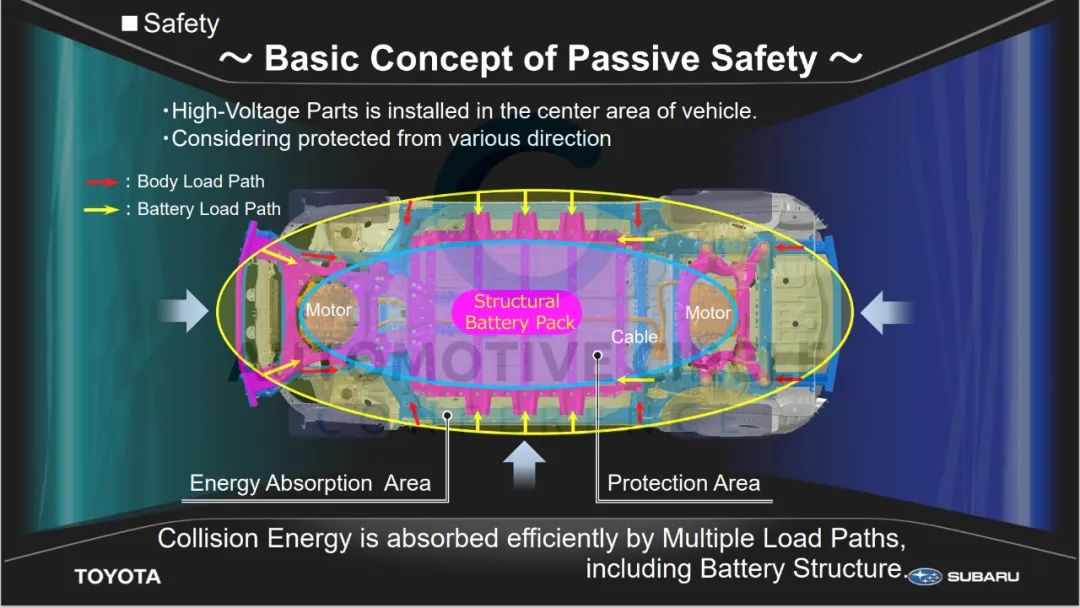
而丰田e-TNGA平台打造的bz4x在电池碰撞安全的结构设计上,对正碰、侧碰、柱碰、后碰等工况,分别对车身、底盘、电池包壳体进行了精准的能量传递的划分、以及在路径的设计上都打破了彼此的边界,让各条路径的结构变得更整体化、结构传递能量更为顺畅。
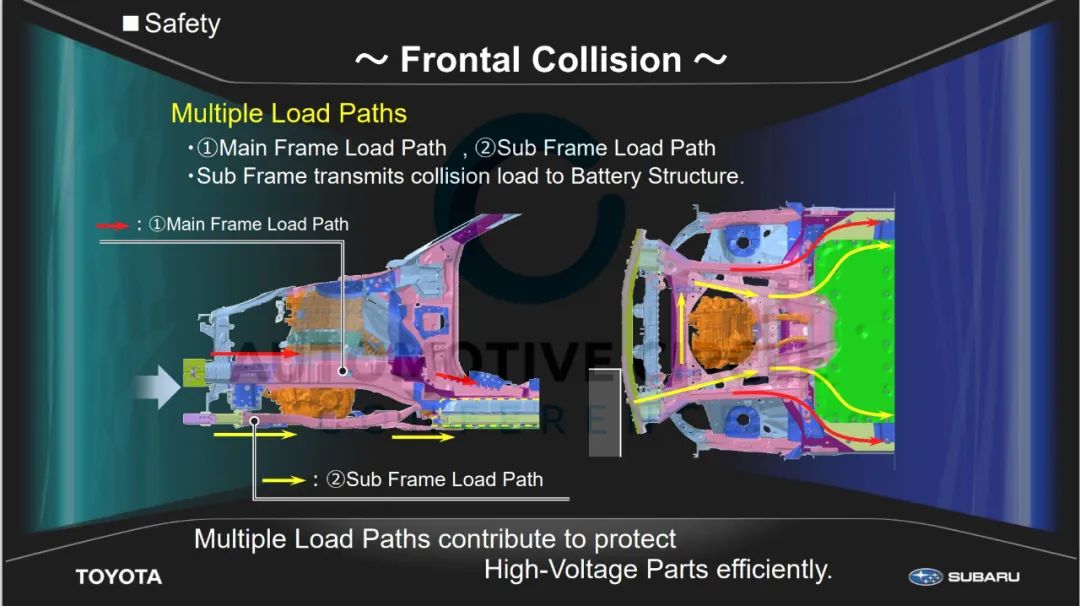
比如在正碰的电池安全设计上,bz4x除了充分考虑了电池的布置防护外,还将碰撞能量传递做了分解,能量从前防撞梁、车身纵梁、副车架再传递到电池壳体之间,是一个连贯的路径,副车架后端与电池壳体设计成了刚性连接结构。而一般车型只是将车身框架和电池包之间设计成刚性连接。
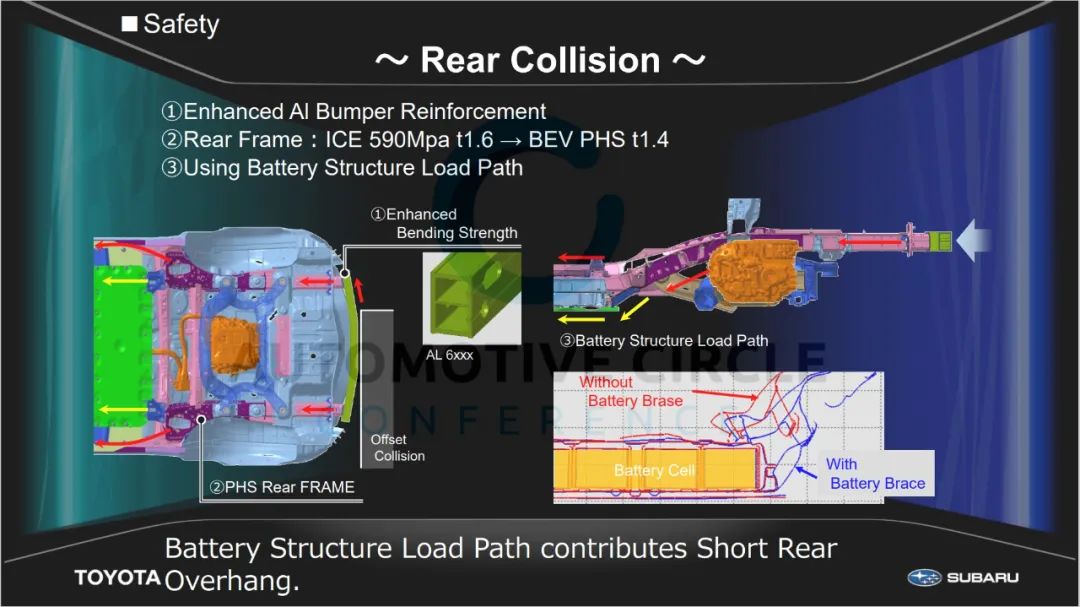
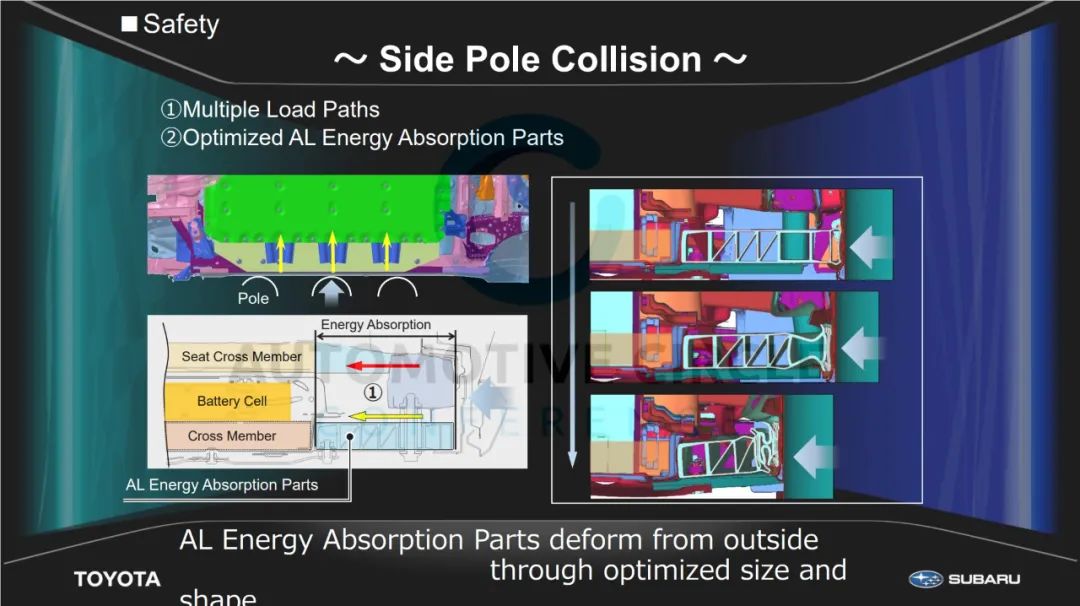
比如在侧面和后部碰撞安全的设计上,bz4x的能量传递路径也都将电池壳体和车身规划为一个刚性的整体,既要部分参与吸能(bz4x电池包两侧设计一段挤出铝工艺车型的吸能结构),也要参与能量传递,终极目标都是通过结构的整合和多重防护,防止内部电芯受到挤压而产生事故。
这种“资源整合式”的设计,将车身、底盘、电池结构整合为一个整体结构,实现了各系统之间的协调作战,避免各自为政导致的性能过剩和结构过升级,可以从根源上降低整车的重量和制造成本。
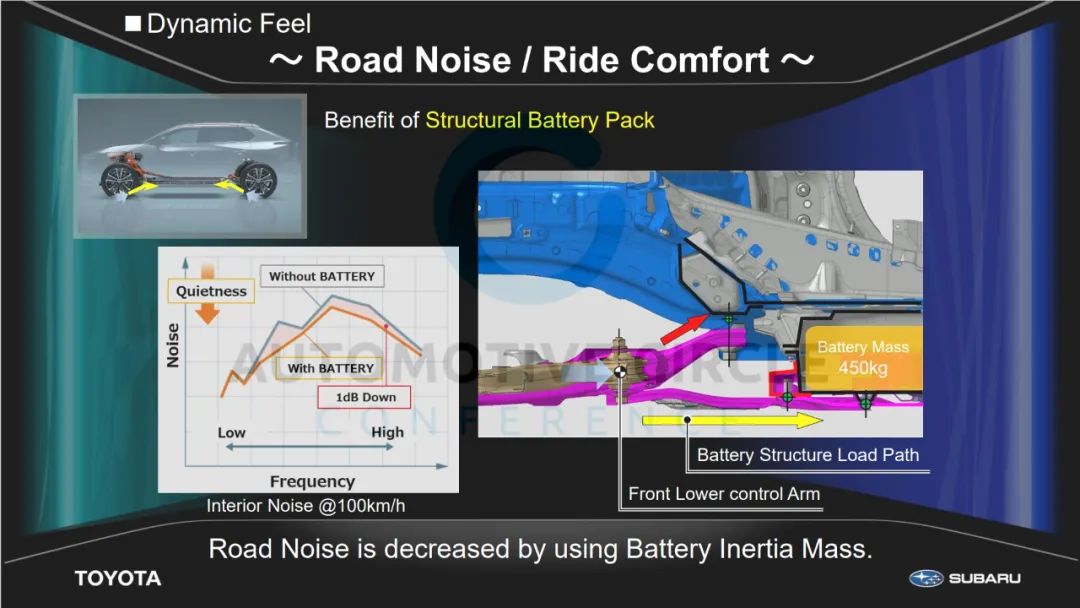
此外,车身、底盘、电池之间结构衔接更为整体,既能提升整车的刚性、提升操稳等,还能提升底盘和车身各关键连接区域的动刚度,降低路躁等,提升整车的舒适性。
02
—
行政壁垒是很多企业里阻碍“e-TNGA理念”发展的关键
事实上很多企业都能意识到,这种整体式规划设计的好,也有企业的团队尝试去做这样的产品开发规划,但是最后都发现受限于各个系统之间的“行政壁垒”,而不得不放弃“整合”的念头。
比如说集成安全在做碰撞路径的规划设计中,希望电池包、底盘等系统能协助车身来承担一部分碰撞的能量,而电池系统会拿出各种电池安全性的标准和行业中的电池起火案例。这种跨系统之间的技术碰撞,在目前各研发企业内部会存在很大的行政阻力,也就是我们常说的“部门墙”。
而当问题上升到更高的决策层时,假如企业的管理层本身就不具备深厚的技术背景和职业担当(在国内的汽车企业这应该是普遍现象),在面对电池系统提出的一系列骇人的安全风险时,很难去选择共担“风险”,一锤定音。
所以,与其说丰田TNGA开发理念有多先进,不如说是丰田管理层整合资源的能力更强,产品开发层面的行政壁垒更少,专业事情的决策权交给了专业者。
当然,如果企业团队的产品开发体系和技术开发能力还没有发展到行业一线的水平,那就是另当别论了。
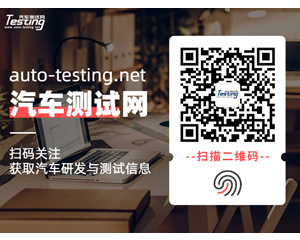
最新资讯
-
GRAS 发布全新座舱测试支架 AutoArray:PR0
2025-08-05 22:06
-
HBK重磅升级!FUSION-LN硬件平台 + BK Conn
2025-08-05 21:37
-
2.5T+双电机 ,新一代帕里斯帝中国首秀演绎
2025-08-05 17:31
-
TSI® 服务计划确保卓越运营:基于客户的视
2025-08-04 20:59
-
imc STUDIO使用进阶培训及范例演示,明日开
2025-08-04 20:58