揭秘红旗E-HS9实现“国内首次”的背后
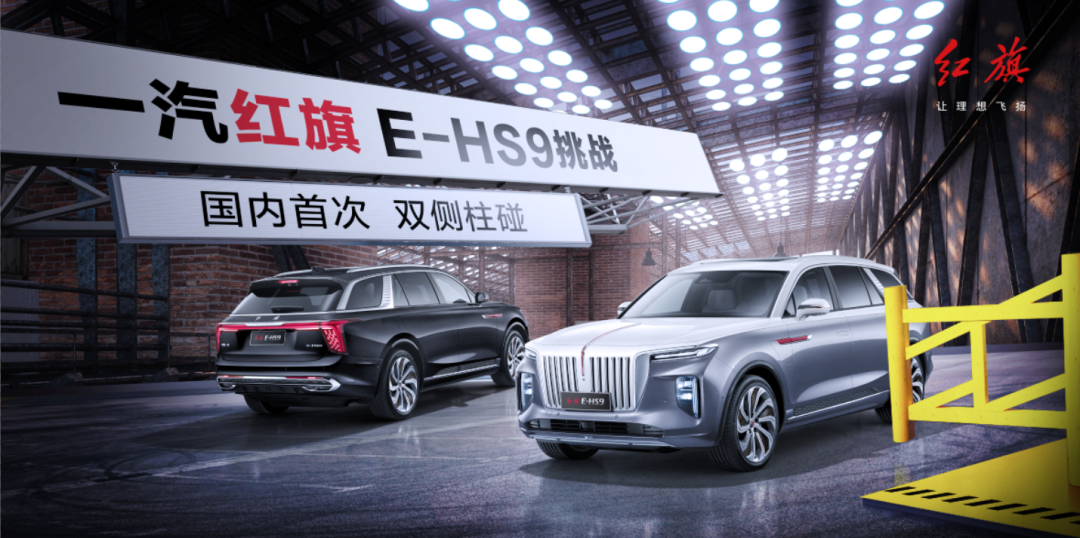
近日,全新红旗E-HS9 在国内首次的双侧柱碰公开试验中交出了亮眼的成绩单,征服了一大批车友。
其实,在项目开发初期,整车安全性能远不如预期。面对现状与目标的差距,全体研发人集思广益、群策群力,突破一项项瓶颈,解决一个个难题,最终不负使命,打造了国车安全典范。
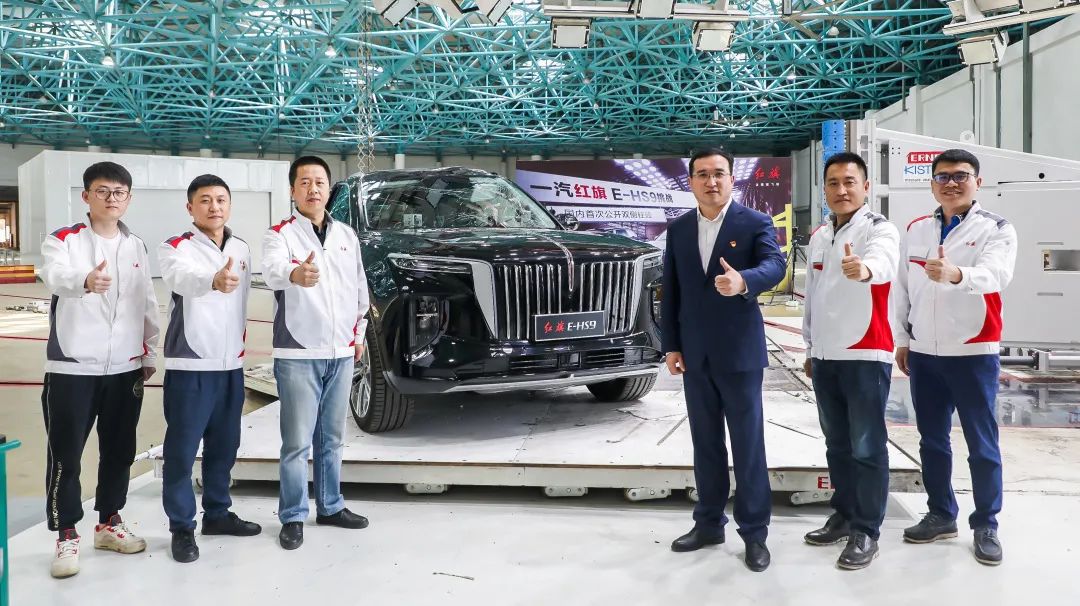
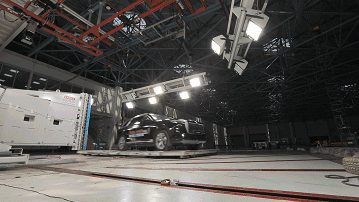
技术创新,挑战“无人区”
初版的电池防护结构只能实现局部保护,不能满足侧面柱碰无差别防护的要求。面对棘手的技术难题和日益趋紧的项目节点,安全研发人选择迎难而上。
时间紧迫,项目团队积极协作,从食堂就餐到班车乘坐,他们不放过任何一个交流机会。经过一轮又一轮的技术研讨,最终创新性地提出“超高强热成型钢管全维防护”结构,实现动力电池的侧面无差别防护。但是,超高热成型钢管结构与工艺装配间隙之间存在明显冲突,一时间又陷入了停滞状态。
项目负责人郝玉敏在没有任何案例支撑的情况下,大胆地提出全新方案:“取消粘胶点与焊点,保留5mm间隙,保证4mm装配公差!”该项试探性方案得到项目经理王君君、研发总院副院长王立军等领导的鼎力支持。
在车身、新能源、电子电器、线束等各专业的大力配合下,全体研发人迎难而上,从材料、结构等多方面着手,优化结构,改进设计,最终通过独创的全覆盖式侧面电池防护结构,对电池模组前后左右形成360°防护,成功突破该难题,并据此获得国家专利授权。
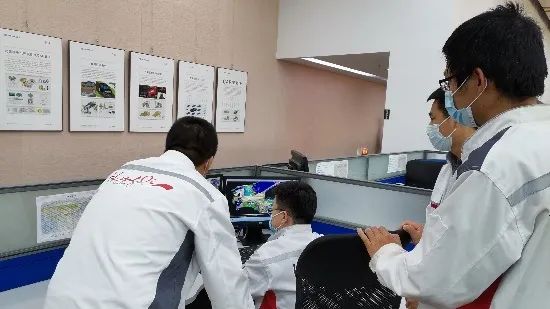
日夜兼程,极限“加速跑”
开发周期短,是E-HS9面临的又一大难点。24个月敏捷开发对研发人已是不小的挑战,再加上法规升级、难度加大导致的项目过程矛盾重重,冲突不断,更对项目周期带来剧烈冲击。
每一个研发人都牢记“敏捷开发”的理念,和时间赛跑。侧面柱碰的主要责任人娄方明,充分发挥党员先锋模范作用,通常是下午接到分析任务,连夜加班修改模型计算,保证第二天一早就能给出结论。为了保证项目节点,他日夜兼程,妻子怀孕也未能好好照顾。正是这种忘我的拼搏精神,保证了计算平台不停歇,关键问题不过夜。
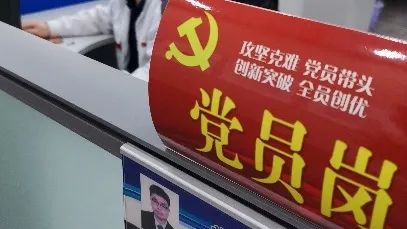
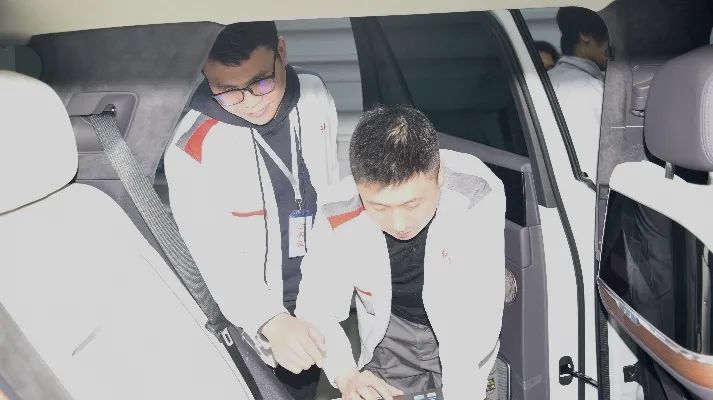
每一项重大成果,都是“群星拱月”的结果。E-HS9取得的优秀成绩,同样离不开丁宇、南海、姜辉等车身、电池系统、电子电器、线束等各专业同事的理解与支持。为达成安全目标,大家齐心携手一次次地挑战标准边界极限,反复试验验证参数可靠性,共同铸造了安全基石。
不尝试,永远不会进步。E-HS9成功实现“国内首次”的背后,是红旗研发人秉持敢为人先的创新精神和舍我其谁的奉献精神,忘我地奋斗在岗位一线,正是因为有这样一群敬业奉献的研发人,红旗事业必定越来越辉煌!
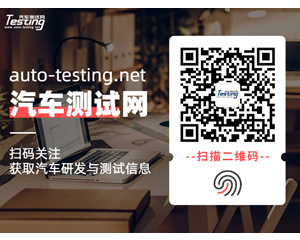
最新资讯
-
商用车及工程机械行业专场:NVH 及语音音频
2025-08-01 17:12
-
理想i8和重卡对撞测试引争议,东风柳汽发声
2025-08-01 15:52
-
艾德克斯IT-N2100 系列太阳能阵列模拟器
2025-08-01 15:43
-
ITECH重磅发布IT2705直流电源分析仪,重构
2025-08-01 15:34
-
现代汽车新一代混合动力系统:以技术革新引
2025-08-01 15:32