动力蓄电池包挤压失效仿真与实验
动力蓄电池包挤压试验中,高强度铝合金的较低断裂延伸率造成挤压过程中的材料损伤断裂,失去部分承载力,而未考虑材料失效的有限元仿真结果与实际结果差异较大,因此有必要将材料失效加入动力蓄电池包的挤压仿真分析。大量的研究证明金属的延性破坏由金属的承受应力三轴度决定。
笔者通过样件拉伸试验与有限元仿真获得了材料的延性损伤参数,同时进行了型材三点弯曲试验、动力蓄电池包挤压试验与有限元仿真的对标,结果表明:输入延性损伤参数的有限元仿真结果与试验结果误差小,能较为准确地模拟铝合金损伤对结构承载性能的影响;不考虑材料失效的结果与试验结果误差较大。
1动力蓄电池包材料失效参数
1.1延性损伤准则
延性金属的断裂行为与应力三轴度(延性金属最常用的应力状态参数)有很大关系。动力蓄电池包的结构材料铝合金6061-T6属于延性金属,其断裂行为与应力三轴度有很大关系,故将延性损伤准则引入到动力蓄电池包材料失效研究。应力三轴度η和平均应力三轴度ηavg分别为
塑性失效准则延性损伤准则中的断裂应变为
研究内容为准静态加载,因此不考虑应变速率的影响。
由式(3)可知,要获得材料延性损伤参数,最少需要3个不同应力三轴度下的断裂应变,因此开展了单轴拉伸试验、纯剪切试验与缺口件拉伸试验,利用有限元仿真获得5个不同应力三轴度下的断裂应变,进而拟合得到材料延性损伤参数。
1.2样件试验与有限元仿真
动力蓄电池包所用材料铝合金6061-T6实验样件如图1所示,样件厚度为2.4mm。试验均在instron5982拉力试验机上进行,夹具夹住样件一端,另一端加载速度为1 mm/min。样件均从型材上采用线切割机切割而成。
通过安装应变传感器的方式很难测量到断裂应变,故将有限元仿真引入到研究中,利用有限元方法计算获得断裂应变。有限元仿真时,须输入精确的应力应变曲线,工程实际中通常利用拉伸试验获得应力应变曲线、弹性模量、屈服强度、抗拉强度、断裂延伸率。工程应力应变曲线不能直接用于有限元仿真,需进行修正。考虑颈缩现象,本文铝合金拉伸试验过程可分为线弹性阶段、应力强化阶段、分散型颈缩阶段、局部颈缩阶段。
应力强化阶段应力应变曲线公式为
对于线弹性阶段、应力强化阶段,可采用下式将工程应力应变曲线转换为有限元可用的真实应力变曲线。
颈缩阶段,因颈缩后样件截面变形,故式(5)~式(7)不能适用,本文利用有限元仿真获得颈缩段的真实应力应变曲线。颈缩段真实应力应变曲线公式为
颈缩阶段的真实应力应变曲线与网格尺寸有关,图2为有限元仿真单轴拉伸力位移曲线与试验曲线,不考虑颈缩阶段应力应变曲线的有限元结果与试验结果差异较大,说明颈缩阶段不可忽略,为确保仿真精度,须获得颈缩阶段的应力应变曲线。
应力应变曲线输入相同(a=-0.3)时,网格尺寸对结果有较大影响,单元尺寸为1.2mm(厚度方向两层网格)的力大于单元尺寸为0.8mm(厚度方向三层网格)和单元尺寸为0.4mm(厚度方向六层网格)的力。为减小网格尺寸对结果的影响,本文所有结果基于abaqus explicit0.8mm全积分单元C3D8获得。
根据式(8),通过实验得到εTu=0.07066,σTu=301.29MPa,通过有限元计算,得到a=-0.3,从而获得材料精确的应力应变曲线。
获得材料的应力应变曲线后,通过有限元仿真对标获得样件的断裂应变。5组试验各重复4次,选择最接近平均值的1组试验数据进行标定。在有限元模型输入修正后的应力应变曲线以及不同的断裂应变,对比仿真和试验的拉伸力与标距位移曲线,迭代获得样件有限元断裂应变以及断裂之前的平均应力三轴度。计算采用尺寸为0.8mm的八节点六面体全积分单元C3D8建模,求解器为abaqus explicit。拉伸力与标距位移如图3所示。试验后的部分样件见图4。
有限元求解得出的各样件试验断裂单元的断裂应变、有限元平均应力三轴度与初始应力三轴度如表1所示。
1.3延性损伤准则参数确定
由得到的5组不同平均应力三轴度下的断裂应变,根据式(3),利用最小二乘法拟合得到某动力蓄电池包结构所用铝合金6061-T6延性损伤参数得到的延性损伤准则曲线见图5,其中回归系数R=0.9974。
2动力蓄电池包挤压试验与有限元仿真
2.1型材三点弯曲试验与仿真
设计铝合金6061-T6型材的三点弯曲试验,利用有限元仿真对获得的延性损伤参数进行标定与修正。试验工况如图6所示,上端挤压圆柱半径为18mm,加载速度为1mm/min,下端2个承载圆柱半径为44mm,固定支撑型材。型材取自某动力蓄电池包下箱体,长度为275mm。试验中,传感器监测挤压柱挤压力与位移。试验的有限元模型如图7所示,边界条件参照试验工况。为缩短计算时间,上端挤压圆柱加载速为356mm/s,固定下端2个承载圆柱,型材采用尺寸为0.8mm的八节点六面体全积分单元C3D8建模,共计303752个单元,上端挤压圆柱与下端2个承载圆柱设置为刚体,求解器采用abaqus explicit,采用质量缩放方法加速计算,质量增量控制在5%以内。
挤压柱挤压力与挤压柱位移的试验曲线与有限元仿真曲线见图8,试验最后即挤压柱位移为35.6mm时,挤压柱的挤压力试验值为6639N,输入延性损伤参数的有限元结果为7586N,相对误差为14.2%,不考虑材料失效的有限元结果为11100N,相对误差为67.2%。试验曲线与仿真曲线的差异原因主要是因为试验过程中发生局部滑移,而有限元无滑移。
试验与有限元仿真断裂区域如图9所示,输入延性损伤参数的有限元仿真结果与试验结果一致性较好,能够准确捕捉到裂缝产生位置以及裂缝展开情况。
2.2动力蓄电池包挤压试验与有限元仿真
GBT31467.3《电动汽车用锂离子电池安全要求》中的8.2.4款规定,电动汽车用锂离子动力蓄电池包须承受半径75mm半圆柱体的X向与Y向挤压(汽车行驶方向为X向,另一垂直于行驶方向的水平方向为Y向),挤压力达到100kN或挤压变形量达到挤压方向的整体尺寸的30%时停止挤压,动力蓄电池包不能起火爆炸。
根据规定要求,利用有限元对某纯电动汽车锂离子动力蓄电池包进行挤压分析,加载工况如图10所示,约束刚性墙的6个自由度,约束挤压柱除挤压方向外的5个自由度,为缩短计算时间,挤压柱加载速度设置为1m/s,采用质量缩放方法加速计算,质量增量控制在5%以内。有限元模型共有2572944个单元,其中,挤压区域采用330858个尺寸为0.8mm的八节点六面体全积分单元C3D8建模,非挤压区域实体结构采用1956524个尺寸为5mm的十节点四面体缩减积分单元C3D10M建模,钣金结构采用172168个尺寸为5mm的四节点四边形缩减积分单元S4R建模,模组采用113664个尺寸为10mm八节点六面体缩减单元C3D8R建模,挤压柱以及挤压墙采用设置为刚体。
有限元计算得到的挤压柱力和位移与试验结果如图11所示,损伤失效区域变形有限元结果与试验结果如图12、图13所示。挤压试验中,挤压柱挤压力达到100kN时,挤压柱位移为6.3mm, 此时输入本文延性损伤参数的有限元仿真结果为98kN,相对误差为-2%,挤压区域加强筋已经开始断裂,与试验结果一致。挤压柱位移为6.3mm,此时不考虑材料失效的限元仿真结果为110kN,相对误差为10%,无法模拟材料失效对结构承载力的影响。
分析结果表明:输入延性损伤参数的挤压仿真结果与试验结果一致,能较为准确地模拟材料失效对电池包结构挤压性能的影响;不考虑材料失效的有限元仿真结果与试验结果误差较大。
3结论
(1)通过设计材料静态拉伸试验,利用有限元仿真获得某动力蓄电池包的结构材料铝合金6061-T6的单轴拉伸试验、纯剪切试验与缺口件拉伸试验的断裂应变以及断裂平均应力三轴度。
(2)利用获得的断裂应变与断裂平均应力三轴度,根据延性损伤准则,拟合获得高强度铝合金6061-T6的延性损伤参数。
(3)型材三点弯曲试验、某纯电动车型动力蓄电池包挤压试验与有限元仿真结果表明:输入延性损伤参数的有限元分析结果与试验结果误差较小,能较为准确地模拟铝合金损伤对结构承载性能的影响,其中,型材三点弯曲挤压柱挤压力的仿真值与试验值相对误差为14.2%,电池包挤压力的仿真值与试验值相对误差为-2%;不考虑材料失效的有限元仿真结果与试验结果误差较大,其中,型材三点弯曲挤压柱挤压力仿真值与试验值相对误差为67.2%,电池包挤压力仿真值与试验值相对误差为10%。
文章来源:广州汽车集团股份有限公司汽车工程研究院
- 下一篇:特斯拉鬼影哪里来?到底有没有救?
- 上一篇:某电动汽车动力电池挤压仿真与试验
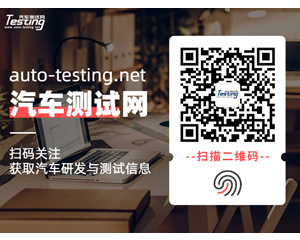
最新资讯
-
计量中心揭秘丨氢品质分析试验室
2025-07-16 09:20
-
L2功能需要LKA么?
2025-07-16 09:19
-
OXTS高精度定位解决方案Oxford Technical S
2025-07-16 09:17
-
用于虚拟里程测试的NPC 模型生成方法
2025-07-16 09:16
-
理工雷科公司荣获2025年CICC科学技术进步奖
2025-07-15 14:46