电动汽车轮边减速驱动系统转矩检测方法
关键字:转矩检测,轮边电驱动,力传感器,偏心套
引言
转矩检测技术在汽车上广泛应用于对发动机、变速箱、传动轴、工作油泵、油马达等系统的功率及效率试验,以及ECU (electronic control unit, 电子控制单元)、EPAS (electric power assistant steering,电子助力转向系统)、TVD (torque vectoring differential) 等技术[ 1-3 ].转矩检测方法主要分为平衡力法、能量转换法和传递法.平衡力法转矩测量装置又称作测功器,主要应用在发动机功率试验中,但它仅适合测量匀速工作情况下的转矩,不能测量动态转矩[4].能量法依据能量守恒定律,通过测量其他形式的能量(如电能、热能参数等)来测量旋转机械的机械能,进而获得与转矩有关的能量系数(如电能系数)来确定被测转矩大小的方法,例如,通过测量输入旋转机械的电功率和转轴转速求得转矩,能量转化法为间接测量法,测量误差比较大[5].传递法精度较高,应用最广,传递法是指利用弹性元件在传递扭矩时物理参数的变化与扭矩的对应关系来测量扭矩的一类方法.文献[6]提到的变速器效率试验使用的转矩仪,文献[7]提出了基于应变电桥的发动机转矩检测方法,通过在传动轴上粘贴应变片进行转矩检测,文献[8]中提到英国福特公司委托南安普大学机械工程系为其研制了一种电容式扭矩传感器可用来连续监测汽车发动机或齿轮箱传动轴的扭矩测试,都属于传递法.其他类型的转矩检测方法如文献[9]中提到了一种新型基于光电原理的高分辨率转矩传感器,能够对高转速轴的转矩进行实时检测,不需要数模转换以及不存在电磁干扰,文献[10]提到的一种基于力致发光原理的转矩传感器以及文献[11]提到的一种基于螺旋式差动变压器的转矩检测方法都能够实现非接触式转矩检测。
电动汽车驱动电机转矩信号的获得通常是根据电机电压、电流及转速信号,按照能量转换法间接估计出电机瞬时转矩,精度较差.对电动汽车轮边驱动系统进行转矩检测有利于驱动电机的高效控制,改善电动汽车的能源利用率和行驶性能.为此,针对轮边驱动系统进行了改良设计,综合现有转矩检测方法,设计合理的转矩检测机构,添加到轮边驱动系统上组成具有转矩实时检测功能的轮边驱动系统,通过机 构受力分析、仿真、以及机构样机的试制和试验,对此转矩检测方法进行可行性分析。
1 轮边减速驱动系统
具有转矩实时检测功能的轮边减速驱动系统的结构如图1所示.该系统主要由轮边电机、轮边减速器和转矩检测机构三部分组成.通过在轮边减速器上合理布置转矩检测机构,在保证基本传动要求的前提下,可实时检测出轮边减速器输入轴的转矩,并以电信号的形式输出,从而用于驱动系统的控制。
2 转矩检测原理
2.1 转矩检测机构设计
将转矩检测机构布置于单级减速器,如图2所示.转矩检测机构主要由偏心套筒、摆臂、力传感器、偏心套筒轴承等部件组成.改变减速器输出轴左端轴承直接支撑于减速器壳体的支撑方式,将其与偏心套筒的内圈配合,支撑于偏心套筒,偏心套筒外圈通过偏心套筒轴承内圈支撑于减速器壳体。偏心套筒内孔轴线与其外圈轴线并不重合,两者在输出轴齿轮受到的径向力方向存在偏心距e。摆臂与偏心套筒通过平键连接,力传感器通过两端的螺柱分别拧入摆臂和减速器壳体相应的螺纹孔内,力传感器可同时承受拉力和压力。减速器工作时,偏心套筒会受到来自输出轴左端轴承、偏心套筒轴承和力传感器的力,其将处于静平衡状态,此时输出轴将绕其自身轴线转动,而没有其他运动,从而保证齿轮的正常传动。
2.2 转矩检测公式推导
根据输出轴受力及力矩平衡关系,可得输出轴左端轴承处的受力
在此转矩检测机构中,假设输出轴受到的轴向力全部由输出轴右端轴承承受,输出轴左端轴承不承受轴向力。输出轴左端轴承受到来自输出轴的作用力将由偏心套筒平衡,由此可得到偏心套筒的受力情况,如图3所示。
为简化受力分析,将输出轴左端轴承、偏心套筒和摆臂作为整体研究对象,其将受到输出轴在水平竖直两个方向的作用力FX和FY。FX和FY的方向必然通过偏心套筒内圈圆心O1,整体还将受到偏心套筒轴承的作用力FX1和FY1。FX1和FY1的方向必然通过偏心套筒外圈圆心O2,同时整体还将受到来自力传感器的作用力Fk。受安装位置约束,力传感器的轴线与Y轴方向(即齿轮切向力方向)始终保持平行,故力传感器作用于偏心套筒力的方向始终与Y轴平行。
减速器工作时,偏心套筒始终处于静平衡状态,根据偏心套筒的受力平衡条件(忽略重力影响),可得
式中:Lk为力传感器轴线到偏心套筒外圈圆心 O2连线的距离;Tf为输出轴左端轴承和偏心套筒轴承作用于偏心套筒的静摩擦力矩。
3 样机试制
3.1 样机模型
根据上述结构方案对单级减速器转矩检测机构的样机进行试制,其三维模型如图4所示.为了简化加载和负载装置,用扭力扳手手工加载代替驱动电机加载,平衡力矩机构提供纯扭矩代替负载装置,对单级减速器的输入转矩进行静态检测.样机的实物模型如图5所示
3.2 样机设计参数
所设计的简易试验样机的设计参数如表1所示。将表中参数带入公式(10),得到比例系数k=0.46。
根据样机参数在CATIA软件中建立简易单级减速器的转 检测机构模型,导入ADAMS(automatic dynamic analysis of mechanical system, 机械系统动学)中,如图6所示。利用ADAMS/View模块进行动力学分析,设定输入轴转速1000r·min-1为仿真初始条件,输入轴驱动转矩为T,为保证输出轴匀速转动,在仿真时需对输出轴施加负载力矩Tload=(z2/z1)T,仿真得到在不同输入转矩下,拉压力传感器受力的数值,如表2所示。
对仿真数据进行相关性分析,计算输入转矩T与传感器检测力Fk之间的相关系数r=1。可见两者之间为强正相关关系.基于最小二乘法对实验数据进行一元线性回归分析[12],回归方程为
如图8所示采用扭力扳手对减速器输入轴手工施加扭矩,所加扭矩值可直接从扭力扳手读出,扭矩从5N·m逐渐增加到40N·m,同时记录力传感器显示的数值,从而得到力传感器的受力情况.为了提高试验的准确性,减小误差,进行多次加载试验,剔除存在粗大误差的试验数据,对试验数据取平均值,整理试验数据如表3所示。
对所测试验数据进行相关性分析,计算输入转矩T与传感器检测力Fk之间的相关系数为r=0.9981。可见两者之间为很强的正相关关系.基于最小二乘法对试验数据进行一元线性回归分析。
将理论计算、仿真以及试验结果进行汇总,表4为三种情况下输入转矩T与传感器检测力Fk的比值关系,三种情况下的比值比较接近.对比分析可以得出结论,该转矩检测方法能够实现较为精确的转矩检测。
6 结语
针对轮边减速驱动系统,提出了一种转矩检测新方法.在轮边减速器轴承端部布置转矩检测机构,通过对机构进行力学分析推导转矩检测公式,进行ADAMS虚拟样机的仿真分析,以及机构样机试制和试验测试.结果表明所研制的转矩检测系统具有较高的精度,为准确检测轮边减速驱动系统输出转矩,提供了简明实用的新方法.将该转矩检测方法应用于电动汽车轮边驱动系统有利于驱动电机的高效控制,改善电动汽车的能源利用率和行驶性能。
参考文献
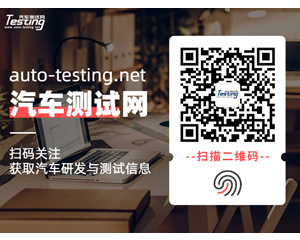
最新资讯
-
商用车及工程机械行业专场:NVH 及语音音频
2025-08-01 17:12
-
理想i8和重卡对撞测试引争议,东风柳汽发声
2025-08-01 15:52
-
艾德克斯IT-N2100 系列太阳能阵列模拟器
2025-08-01 15:43
-
ITECH重磅发布IT2705直流电源分析仪,重构
2025-08-01 15:34
-
现代汽车新一代混合动力系统:以技术革新引
2025-08-01 15:32