电池模组动态冲击介绍
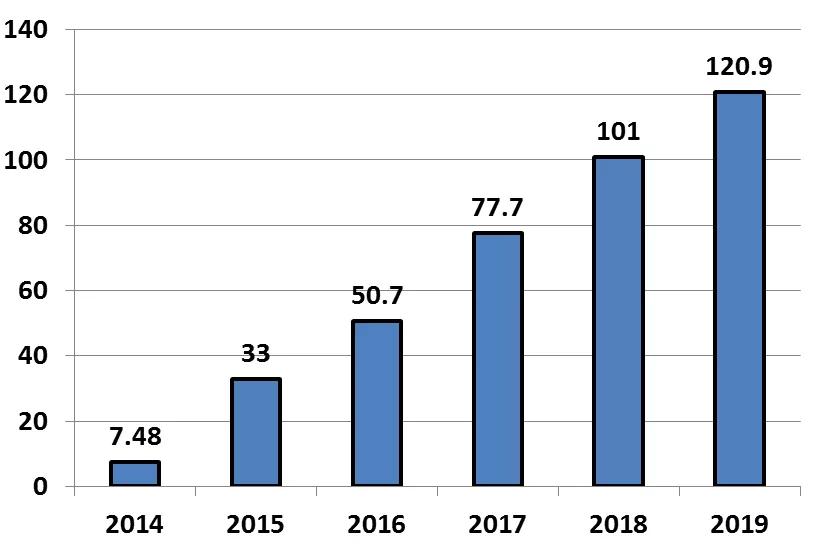
电池系统作为纯电动及混合动汽车的重要动力来源,能量密度和功率较高,其可靠性及安全性直接决定整车的安全。目前,全球主要国家及地区都对电动/混动汽车碰撞安全以及动力电池有相应的法规要求,见表1。
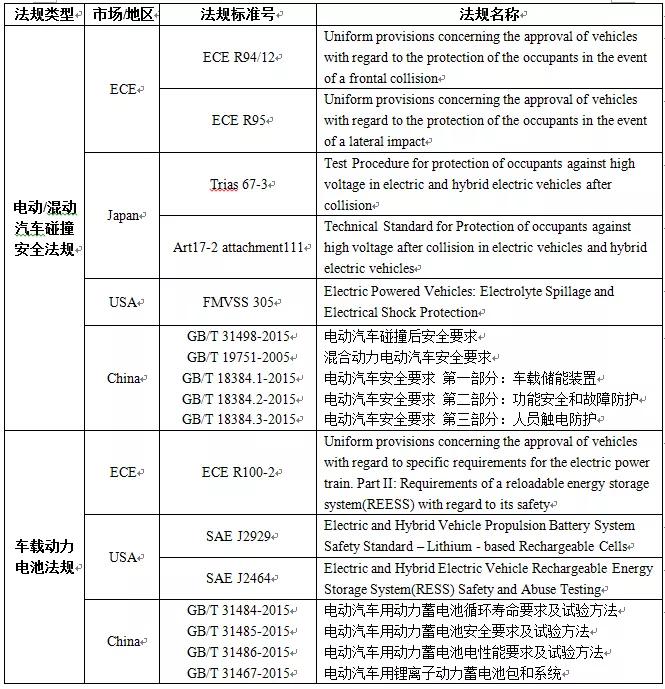
相关统计表明[1],2010到2019年发生的电动汽车燃烧事故中,由于车辆碰撞导致电池包燃烧起火的事故占16%,主要原因有以下几点:①正面或者追尾碰撞导致电池包X向发生变形;②侧面碰撞导致电池包Y向变形;③车辆托底引发的电池包Z向变形。因此,有效地评估电池碰撞的力学和电学特性对避免新能源汽车发生严重安全事故意义重大。
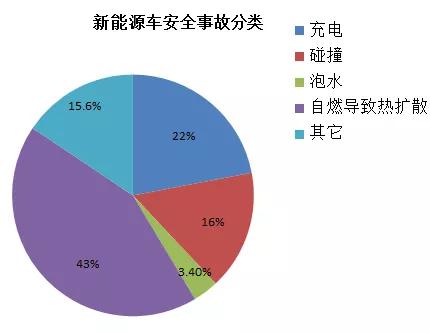
本文针对一种电池模组在典型碰撞工况下力-位移-电行为进行研究,采用圆弧冲头对电池模组的三个方向进行动态冲击试验,模拟整车高速碰撞中电池系统受到的撞击的工况,对电池的力学和安全性能进行了评估,确定电池受碰撞冲击载荷的极限,进而指导整车开发设计。
1 电池模组试验设计
1.1试验材料
本文试验用电池模组含有八块电池单体,(见图3)。
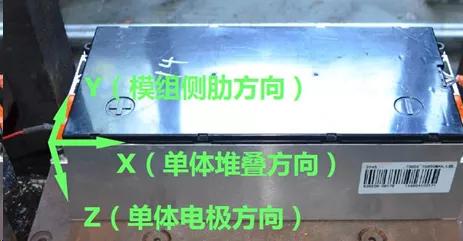
定义电池模组方向与整车X、Y、Z方向对应(见图4),通过X向和Y向的冲击试验模拟电池模组在整车碰撞过程中的受力工况,Z向的试验则对应整车碰撞中地板等结构变形挤压电池模组上盖的情况。
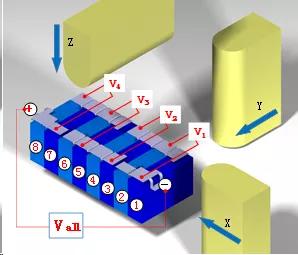
1.2试验测试方法
试验在落锤试验机上完成,如图5所示。三个方向试验中的电池模组均靠其自身的安装螺栓固定,以尽可能反映其在实车中的安装方式。
该试验中载荷传感器安装在电池模组的支撑平板下面。通过测量贴于传感器侧壁的应变片的电压变化,获取试验中电池模组所受的载荷。通过超动态应变仪高速采集卡采集载荷传感器的电压信号及电池模组电压。使用非接触测量技术测量冲击头的位移(即电池模组的侵入量)和冲击速度[2]。
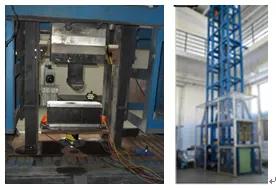
2 电池模组动态冲击试验
2.1 物理现象及特点分析
基于落锤试验台,完成了X、Y和Z方向的动态冲击试验,试验后的电池模组如图6所示。三个方向试验后的电池模组在试验后均发生持续冒烟,但未产生起火。X方向动态冲击试验后,电池模组顶部铝合金框架发生变形和断裂,离锤头最近的1#单体和2#单体受冲击破坏严重,内部电芯被挤出。其余单体均有不同程度的变形损伤,见图6a。电池模组Y向冲击造成模组的铝合金框架、电路板、底部塑料板和4#和5#电池单体变形严重,电池单体铝壳被破坏,电芯外漏,见图6b。Z方向冲击试验后模组被劈开,铝制框架和塑料底部发生破坏,电路板折断,4#和5#电池单体挤压变形严重,电极连接片脱落,见图6c。
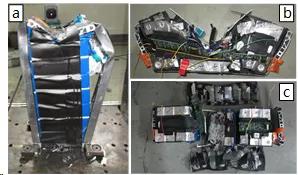
2.2 动态冲击试验数据分析
图7展示了电池模组三个方向冲击载荷作用下的载荷、侵入位移和总电压随时间变化曲线。X方向载荷呈现双峰形状,当模组承受载荷达到第一峰时,出现内部短路,总电压从10V持续下降到7.5V。其原因是1# 电池组的破坏导致电压下降到0V。载荷达到第一峰后,外层铝制框架破坏,载荷下降,锤头进一步挤压模组,各电池单体为主要承载部件,载荷曲线上升第二峰值,1#和2#单体电芯被挤出铝壳后,载荷曲线开始下降至0。
Y向和Z向载荷在经历了上升的阶段后均达到75kN左右水平的载荷平台,锤头持续挤压4#和5#电池单体的Y向和Z向。电压曲线的变化表明两种工况下均较早地发生了内短路,这可能是由于Y和Z向的冲击试验过程中,更容易对电池模组内部的电路板造成破坏,造成内部提前短路。
使用单体电压下降时刻的侵入位移和冲击载荷两个参数指标作为损伤容限来评价电池模组的安全性能,相比Y和Z方向,X方向的承载能力和抗侵入能力更强;Y方向的抗侵入能力最小;Z方向的承载能力最弱。
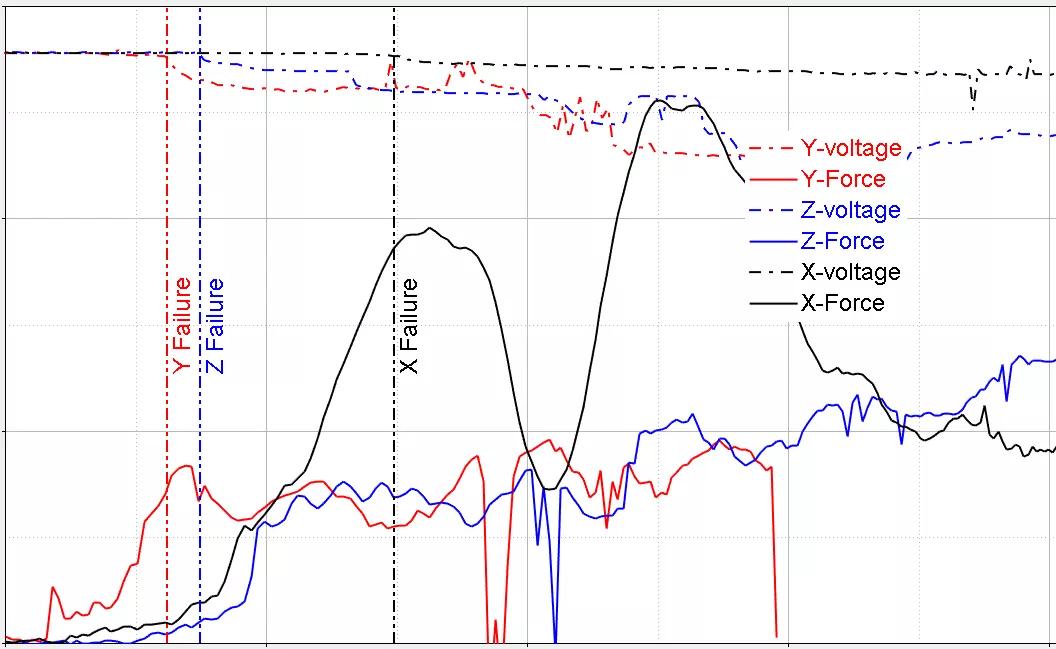
3 结束语
研究结果表明:电池模组在动态冲击试验过程中出现内短路和热失控现象,试验的模组外层铝制框架破坏,单体外壳破坏,电芯外漏。电池模组的承载能力和损伤容限表现出明显的方向特性。高速工况下,X方向的承载能力最强,Y方向抗侵入能力最弱,而Z方向的承载能力最小。
在新能源汽车电池系统的安全设计中,需要考虑电池模组在高速工况下的特性,同时综合考虑和利用电池单体不同方向的承载能力和损伤容限,以求达到最佳的轻量化和碰撞安全设计。
参考文献 :
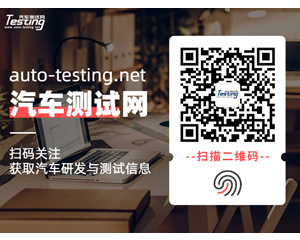
最新资讯
-
商用车及工程机械行业专场:NVH 及语音音频
2025-08-01 17:12
-
理想i8和重卡对撞测试引争议,东风柳汽发声
2025-08-01 15:52
-
艾德克斯IT-N2100 系列太阳能阵列模拟器
2025-08-01 15:43
-
ITECH重磅发布IT2705直流电源分析仪,重构
2025-08-01 15:34
-
现代汽车新一代混合动力系统:以技术革新引
2025-08-01 15:32