三元锂离子电池盖板安全装置研究力神动力电池系统
1 实验
1.1 过充及短路保护原理
此安全装置是盖板的一部分,包含压力膜及溶断装置s压力膜是通过模具制作出来后焊接到盖板上,其材质是铝,熔断装置是在盖板的下极板上冲压出铝丝的形状后,用PPS进行注塑(见图1),保证铝丝的结构不被破坏,铝丝的熔断电流等于锂离子单体电池盖板的短路电流,熔断原理见图2,熔断电流走向示意图见图3。
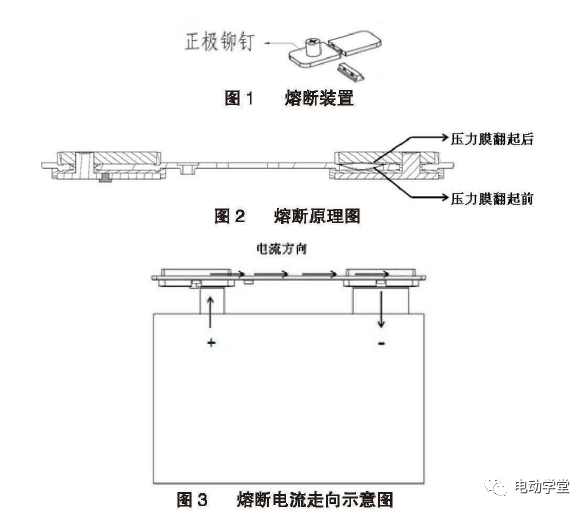
在锂离子单体电池发生过充时,其电压会超过三元材料的设计电压4.2V,—直上升到5V左右,此时锂离子单体电池内部会发生剧烈的副反应,正极的化学结构坍塌,并且会在正极极片的表面出现析锂,析出的锂离子刺穿隔膜,造成短路,极组温度会急剧上升到8(TC,极组还会大量产气。由于锂离子单体电池是一个封闭的腔体,内部空隙非常小,所以产气后内部压力急剧上升,当压力超过一定值,锂离子单体电池会发生爆炸。带安全装置的锂离子单体电池,当内部压力达到膜翻起的临界点0.4MPa时,压力膜被顶起。同时,正负极短接,电路电流达到1000A左右,从而将熔断装置中的铝丝熔断,将极组回路与外界充放电回路断开,起到过充时保护极组的作用。
在对锂离子单体电池进行短路实验时,极组、外部电阻、熔断装置组成串联回路,假定满荷电态单体电压3.8V,外接短路电阻约是3.5mfl,锂离子单体电池的内阻为0.6mfl左右,那么锂离子单体电池的短路实验电流会达到1000A。这么大的电流会使极组发热,迅速升温到8(TC以上,隔膜会发生收缩失去隔离作用使极组内部短路,同时发生副反应,压力会瞬时上升到1MPa以上,超过铝壳体的拉伸强度,发生爆炸。如果盖板安装了安全装置,当短路电流超过1000A时,铝丝自行擦断,使极组与盖板和盖板外短路点隔离,防止锂离子单体电池持续短路,从而保护了电极极组。
1.2 电池制作
分别使用带安全装置的电池盖板和不带安全装置的电池盖板,以三元材料为正极材料,采用正常的生产工艺进行电池制作,将制作完成的电芯进行短路及过充测试,来验证带安全装置的锂离子单体电池盖板是否可以对电池过充和短路起到保护作用。
1.3 测试流程
(1)过充测试:单体蓄电池按照GB/T31485-2015的方式进行充电,电池满电后,以1A电流恒流充电至电压达到企业技术条件中规定的充电终止电压的1.5倍,即6.3V,或充电时间达lh后停止充电。
(2)短路测试:单体蓄电池按照GB/T31485-2015的方式进行充电,将单体蓄电池正、负极经外部短路10min,外接电阻应小于5Ω。
2 过充与短路实验
2.1 过充实验对比测试
(1)未安装安全装置盖板的锂离子单体电池
过充对比测试中,按照GB/T31485-2015,首先对没有安全装置的锂离子单体电池进行充电,锂离子单体电池充满电后,在过充后的2500S发生了剧烈爆炸。锂离子单体电池的表面温度高达8(TC,内部的温度足以使隔膜变形收缩,使极组短路,并且会发生产气严重的副反应,所以内部的温度、气压会进一步急剧上升,导致热失控,电芯在2500s以后发生爆炸。实验时未安装安全装置盖板的电池过充测试曲线见图4。
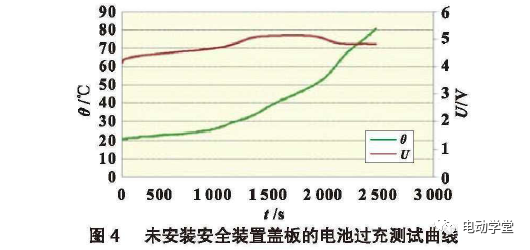
(2)安装安全装置盖板的锂离子单体电池
安装过充保护装置的锂离子单体电池在充电后,开始进行过充实验,电芯在984S时电压骤降,温度急速上升,从40℃上升到50’C左右后开始下降。从图4中可以看出温度从730S开始上升,说明过充后较强烈的副反应开始了,在副反应发生了一段时间后,在984s左右内部压力达到0.4MPa,压力膜变形至压力膜翻起后的位置(如图2中标注的压力膜翻起后位置),导致正负极之间短路。电压骤降至0V,这时盖板将极组与外界充电设备隔离,极组的副反应无法持续,产热结束,没有严重的热失控发生,实验测试曲线见图5。
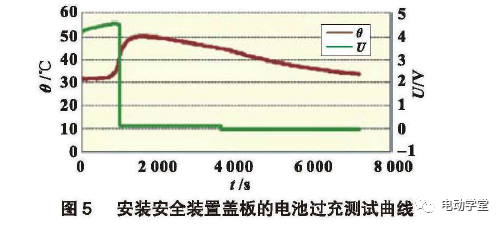
2.2 短路实验对比测试
(1)未安装安全装置盖板的锂离子单体电池
首先进行短路测试,对没有安装此安全装置的电芯进行测试。在测试中短路电流非常大,反应过于剧烈,在锂离子单体电池的正负极柱表面有火星,然后在非常短的时间内锂离子单体电池爆炸,所以无法检测到数据,图6为实验现场照片。
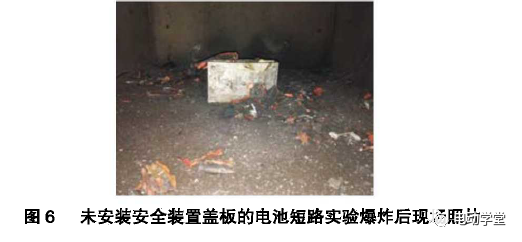
(2)安装安全装置盖板的锂离子单体电池
安装了短路安全装置的锂离子单体电池,在设备对电芯进行短路后的5s,熔断装置彻底断路,将极组与外界隔绝。在后面观察的2500s没有发生温度急剧上升的情况,电压也没有升高,说明在短路后的2500s后极组没有发生热失控现象,熔断装置也没有恢复,彻底断开了,所以短路测试通过,实验数据见图7。
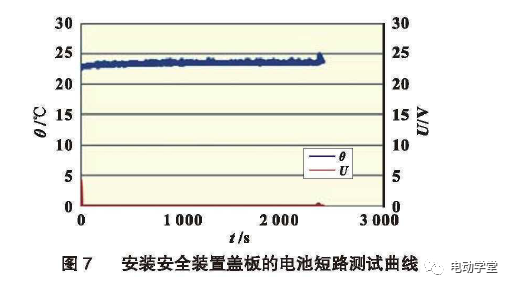
在过充、短路实验中,使用没有安全装置的电池盖板的电池爆炸了,使用了有安全装置的电池盖板的电池未爆炸。这说明三元体系的锂离子电池一般很难直接通过安全性实验,加装了带有安全装置的盖板后,电池的安全性测试能够顺利通过。
通过实验验证了安全装置在短路或过充时能够切断与外接负载或充电设备连接的外回路,可防止热失控发生。安全装置对处在短路、过充实验状态下的锂离子电池有保护作用,但仍然存在熔断与翻转不同步不匹配的现象,这需要进一步优化参数,改进安全装置设计。
3 安全装置设计参数优化实验
3.1 压力膜实验
为了提高锂离子单体电池通过安全测试的一致性及可靠性,达到上述效果,需要进行多组实验对比,来针对此款电芯优化出最佳的安全装置设计参数。
安全装置由压力膜和熔断装置两部分组成,所以参数按照装置动作的先后顺序进行确定。先进行压力膜参数的确定,锂离子单体电池内部压力通常在0.1MPa左右,而且防爆阀开启压力下限在0.6MPa,所以在0.2~0.5MPa范围内分别进行测试。压力膜的压力值通过硬度去控制,压力膜从各个压力批次中去选择。根据压力值设计4组实验,每组20只锂离子单体电池,压力膜压力实验数据见表1。
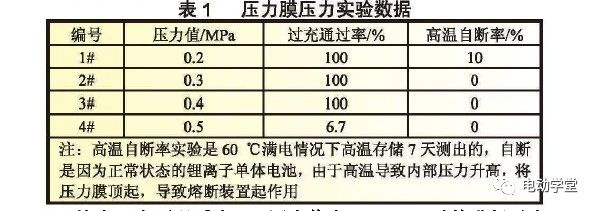
从表1中可以看出;1#压力值在0.2MPa,对其进行过充,通过率达到100%,但是在高温存储6(TC过程中会发生锂离子单体电池自断路的情况,所以此压力值偏低;2#和3#实验在过充和高温自断率方面均达到要求,没有出现过充热失控或高温存储中内部熔断的情况;4#在过充中,只有3只锂离子单体电池通过了过充实验,不满足设计要求。因此,从此批次的实验中看出,压力膜在0.3~0.4MPa之间是满足设计要求的。
3.2 熔断丝截面积选择
熔断丝截面积越小,其过流性能越差,过流时发热量越大,越容易熔断。由于溶断装置为较细的铝丝,强度较弱,为了保证熔断装置强度,所以将熔断装置设计为两根,用来增加结构强度,熔断及过流测试是直接对两根熔断丝进行测试,这样能和实际情况完全一致。
对熔断装置的要求是:熔断丝截面积最大,4C过流后温度不高于60℃,在1000A下瞬时溶断、压膜翻转10s内可培断。
电芯发生过充时,压力膜未翻起,熔断装置应可通过4C的电流,熔断丝不熔断;当压力膜翻起后,熔断装置可以熔断;无论压力膜翻起还是不翻起,当电流大于1000A时,熔断丝应熔断。
此款电池的容量为51Ah,若以4C电流放电,放电到截止电压2.7V需15min左右,在此期间要测量电池温升。
根据各大车厂的要求,在通过4C电流放电后,完成放电的电池温度应低于6(TC。假设溶断丝截面积在0.8~2m㎡区间,那么:
如果0.8m㎡截面积的熔断丝能通过4C的电流,且温度超过60’C,则不再进行低于0.8m㎡熔断丝的实验;如果4C电流可以通过,且温度未超过60’C,则对更小面积的熔断装置进行实验,直至有一个条件不通过为止。如果2m㎡截面积的熔断丝在1000A时不能够瞬时熔断,则不进行更大截面积溶断丝实验,要向减小截面积方向进行实验,直至1000A能够熔断为止;若1000A过流瞬时能够熔断,在压力膜翻起后10s内也熔断,则对更大截面积的熔断丝进行实验,直至1000A过流时不熔断为止。
这样就可以针对某一型号电池筛选出“溶断丝截面积最大,4C过流后温度不高于6CTC,在1000A下瞬时熔断,压膜翻转10s内可熔断”的熔断丝截面积设计参数。
3.3 —体化部件实验
前面做了截面积选择单项实验,下面组合起来,进行部件实验。
电池安全实验的“过充实验”是按GB/T31485-2015中过充实验所规定的条件进行。熔丝高温自断率实验是60℃满电情况下,高温存储7天测出的。熔丝自断现象是因为正常状态的锂离子单体电池,由于高温导致的内部压力升高,将压力膜顶起,导致熔断装置起作用的过程。高温自断率通过的标准是高温存储过程中,翻转阀不动作,熔断装置不发生熔断。
熔断装置的参数确定:在实验中,压力膜的开启压力设定为0.3~0.4MPa可以保证在过充及短路时将压力膜翻起,并且在6(TC满电情况下高温存储7天没有因为高温导致的内部压力升高,将压力膜顶起,导致熔断装置起作用的情况,即高温不会发生自断现象。所以压力膜的翻起压力值在0.3~0.4MPa,为了保证强度将熔断装置设计为两根铝丝,将每根的熔断面积确定为0.8~2m㎡,设计6组实验。先进行实验,如果都能熔断则再做单根0.8m㎡以下的实验和2m㎡以上的实验,实验数据见表2。
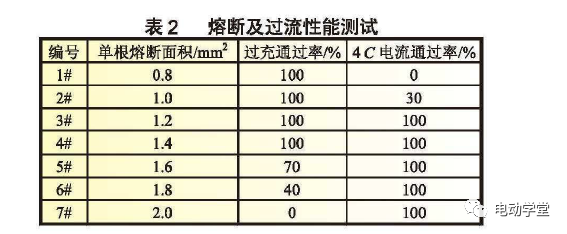
由表2可知,1#~4#均可以完成过充实验,不发生热失控的情况,5#~7#实验的过充通过率大大降低至无法通过实验,发生防爆阀爆喷爆炸等情况。但是通过表2中4C电流通过率可以看出1#和2#电芯会有超过60℃的情况,3#~7#均可以通过4C测试。从此实验中可以得出,熔断面积选定两根溶断丝截面积1.2~1.4m㎡为最佳值,可以较好地匹配此款电芯。
对锂离子单体电池盖板的熔断装置单独进行焙断时间测试,使用ARbin5V2000A测试系统,该设备可提供最大电流2000A,把培断装置连接在设备上,连接方式见图3,加载的电流按600~1800A递增。通过实验,熔断丝截面积为1.2~1.4m㎡的安全装置的盖板部件可以满足要求。然后在此基础上,选择1.3m㎡为截面积选择的中值,用该尺寸的熔断丝进行溶断时间测试。在600、800、1000、1200、1400、1600、1700、1800A的短路电流下,熔断时间分别为112.211、20.780、6.000、4.501、2.490、1.410,1.320、0.990s。
可以看出熔断电流越小,熔断时间越长。当熔断电流大于1000A时,即模拟压力膜翻转后,将正负极导通发生短路,熔断时间满足各大整车厂对锂离子单体电池安全装置的设计要求,所以每根焙断面积1.3m㎡可以达到要求。
4 结论
过充短路安全装置可以明显地改善锂离子单体电池的安全注,提升安全实验的通过率,安全装置因与锂离子单体电池的容量、内阻特性相关,所以在使用前应针对每款电池通过实验调整部分设计参数,做到专款专用,将压力膜硬度和熔断的截面积参数与锂离子单体电池匹配好,做到最优。
- 下一篇:保护行人的利器-行人保护气囊
- 上一篇:耐久异响正向开发技术方案
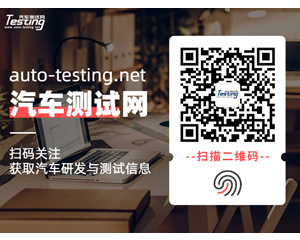
最新资讯
-
【展会专访】Chroma 致茂电子:以马达测功
2025-09-02 15:22
-
投资31亿!赛力斯全球研发中心项目曝光!
2025-09-02 15:21
-
深信科创获“年度智能辅助驾驶创新技术奖”
2025-09-02 10:14
-
打破营销内卷:小红书以“车生活场景”重塑
2025-09-01 19:18
-
2025汽车测试展回顾:你错过的研华科技亮点
2025-09-01 10:58