Simcenter 3D车辆机电实时仿真
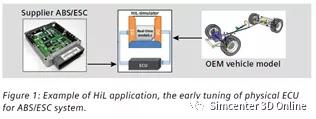
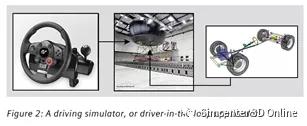
高精度模型在机械系统中的典型应用是用于离线分析。为了获得精确的仿真结果,多自由度的模拟方案往往是必须的。例如,用于预测弹塑性运动学特性的汽车悬架模型往往需要包含像部件之间衬套力单元的非线性柔性建模。由于其高复杂性,绝大多数高精度模型因此很容易就达到150个以上的自由度,这给绝大多数多体系统动力学求解器带来巨大的性能挑战。对于这样的现状,目前的行业惯例是使用高性能多体系统模型的简化版来用于控制系统的设计与验证,驾驶模拟器也一样。典型的模型简化就是去除部件以及自由度,直到模型的复杂程度能用于实时仿真。对于悬架,CAE分析往往使用简化的运动副代替柔性连接,甚至用复杂查表方式来代替弹塑性运动学特性曲线。这些曲线包括在车轮在大位移(车轮垂向运动、转向角度)以及车轮载荷(纵向、侧向以及回正力矩)驱动下的位置与方向。通过这些简化,可以得到一个典型具有15到20个自由度的车辆行驶动力学模型(如图3所示)。
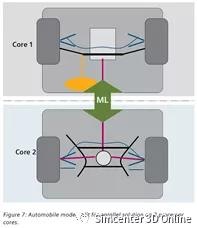
相对高精度的复杂模型,低精度的简化模型只需要较低的求解工作量,因此只能达到较低的求解精度。低精度简化模型只能提供可接受的约在5Hz以内仿真精度,在整车性能分析中只能覆盖典型的横摆、纵倾以及起伏模式(roll, pitch and heave modes)。高精度复杂模型可以将有效频段范围扩展到约30Hz。这个频率范围内能包含悬架的衬套有限刚度的动力学效应以及ADAS,ADAS在这样的动力学效应下会产生不一样的响应。在这种情况下,为了及时地发现和处理这类问题,高精度复杂车辆动力学模型的硬件在环测试时必需的。
实时应用的突破性解决方案
Simcenter 3D Motion 软件的实时求解平台,支持客户在实时仿真中能够直接使用高性能复杂多体系统模型。该解决方案的明显优势如下:
- 相同的高性能复杂模型,同时适用于离线仿真和实时仿真;
- 从离线仿真到实时仿真不会损失精度;
- 可以在实时仿真的模型中直接获取物理参数从而轻易实现“what-if”分析。
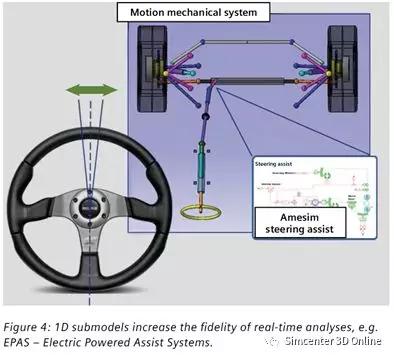
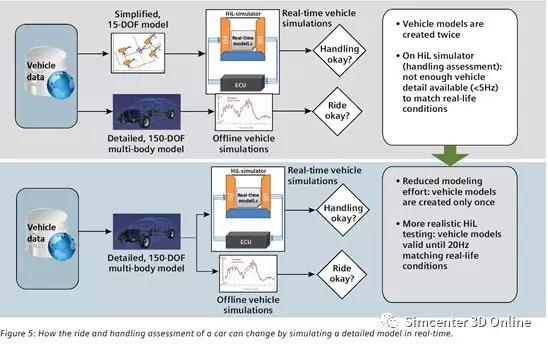
Simcenter 3D Motion实时求解主要特点包括定步长隐式求解、并行求解以及耦合电、液、气等子系统三个主要特点:
定步长隐式求解
在硬件在环仿真中,众所周知,任何一个时间步的周转时间(用来计算下一个离散时间点系统状态所需的时间)必须小于仿真时间步。换句话说,实时仿真必须是通过定步长来求解进行。
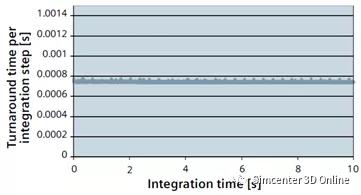
当前大多数实时求解都是显式的。这类求解只通过考虑当前(也有可能是过去)离散时间点的加速度来计算下一个时间步的系统状态。虽然显示方法可以保证确定性的计算载荷,但是内含的像衬套之类的柔性单元会产生数值刚度系统,在这种情况下,隐式求解法被认为是比较好的,因为其优秀的数值稳定性和精度。
由于像衬套、弹簧、阻尼器等力单元与约束之间多自由度的耦合,在多体动力学中使用多处理器来分割计算是一项不同凡响的工作。在隐式积分方法设置中,这个运动方程耦合的难点不仅仅局限于约束之间,在力单元之间也有。
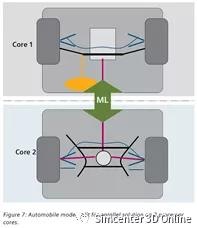
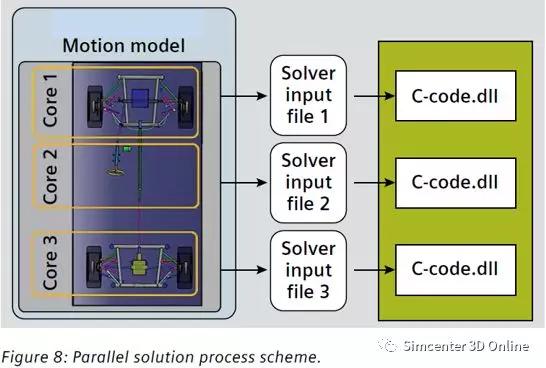
Simcenter 3D Motion实时求解能集成1D形式的车辆子系统进行耦合仿真。SimcenterAmesim软件提供大量的机械、电气、液压等系统详细模型库,同时为Simcenter3D Motion提供专用的接口以方便的进行1D与3D模型之间的交互。虽然在实时协同仿真的标准应用中,涉及的所有的子系统都要求相同的集成步长(典型的是1ms=1kHz),但是Simcenter3D Motion实时求解器功能已扩展至能进行多速率仿真,以便能满足高频子系统的特殊要求,例如在内燃机点火载荷仿真中,需要高达5kHz的频率才能达到所需的结果精度。
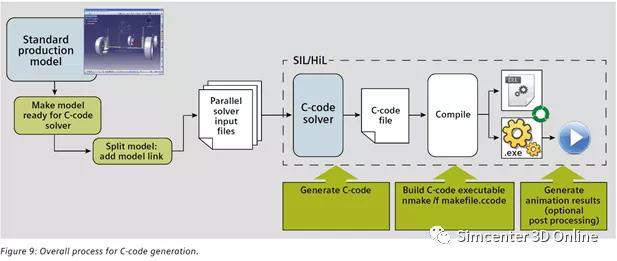
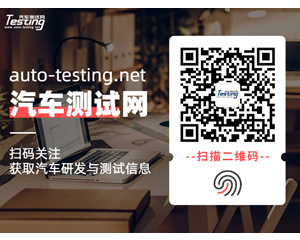
最新资讯
-
商用车及工程机械行业专场:NVH 及语音音频
2025-08-01 17:12
-
理想i8和重卡对撞测试引争议,东风柳汽发声
2025-08-01 15:52
-
艾德克斯IT-N2100 系列太阳能阵列模拟器
2025-08-01 15:43
-
ITECH重磅发布IT2705直流电源分析仪,重构
2025-08-01 15:34
-
现代汽车新一代混合动力系统:以技术革新引
2025-08-01 15:32