车用燃料电池耐久性的解决策略
车辆频繁变工况运行是引起燃料电池寿命降低的最主要原因。从物理方面看,车辆在动态运行过程中由于电流载荷的瞬态变化会引起反应气压力、温度、湿度等频繁波动,导致材料本身或部件结构的机械性损伤。从化学角度看,由于动态过程载荷的变化,引起电压波动,导致材料化学衰减,尤其在启动、停车、怠速以及带有高电位的动态循环过程中材料性能会加速衰减,如催化剂的溶解与聚集、聚合物膜降解等。
因此,实现商业化燃料电池的寿命指标,可从2个层次逐步进行:一方面,通过对系统与控制策略的优化,使之避开不利条件或减少不利条件存在的时间,达到延缓衰减的目的,但系统会相对复杂,需要加入必要的传感、执行元件与相应的控制单元等;另一方面,还要持续支持新材料的发展,当能抵抗车用苛刻工况新材料的技术成熟时,系统可以进一步简化,在新材料基础上实现车用燃料电池的寿命目标。
车用燃料电池系统控制策略
燃料电池运行过程中的反应气饥饿、动态电位循环及高电位是引起催化剂及其载体等材料衰减的主要原因。此外,一些极限条件如零度以下储存与启动、高污染环境也会造成燃料电池不可逆转的衰减。归纳起来这些衰减因素主要包括在以下几种车辆运行的典型工况中:1)动态循环工况;2)启动/停车过程;3)连续低载或怠速运行;4)低温贮存与启动过程。下面重点对四种工况下引起的衰减机理进行分析,并介绍可能采取的解决对策。
动态循环工况
动态循环工况是指车辆运行过程中由于路况不同燃料电池输出功率随载荷的变化过程。通常车用燃料电池系统是采用空压机或鼓风机供气。研究显示,燃料电池在加载瞬间,由于空压机或鼓风机的响应滞后于加载的电信号,会引起燃料电池出现短期饥饿现象,即反应气供应不能维持所需要的输出电流,造成电压瞬间过低。尤其是当燃料电池堆各单节阻力分配不完全均匀时,会造成阻力大的某一节或几节首先出现反极,在空气侧会产生氢气,造成局部热点,甚至失效。此外,动态载荷循环工况也会引起燃料电池电位在0.5~0.9 V之间频繁变化,在车辆5500h的运行寿命内,车用燃料电池要承受高达30万次电位动态循环,这种电位频繁变化,会使催化剂及炭载体加速衰减,因此需要针对动态工况采用一定的控制策略减缓衰减。
采用二次电池、超级电容器等储能装置与燃料电池构建电- 电混合动力,既可减小燃料电池输出功率变化速率,又可以避免燃料电池载荷的大幅度波动。这样使燃料电池在相对稳定工况下工作,避免了加载瞬间由于空气饥饿引起的电压波动,减缓由于运行过程中的频繁变载引起的电位扫描导致的催化剂的加速衰减。
为了防止动态加载时的空气饥饿现象,还可采用“前馈”控制策略,即在加载前预置一定量的反应气,可以减轻反应气饥饿现象。此外,在电堆的设计、加工、组装过程中保证各单电池阻力分配均匀,避免电池个别节在动态加载时出现过早的饥饿,也是预防衰减的重要控制因素。在动态加载时除了会发生空气饥饿外,氢气供应不足会发生燃料饥饿现象。瞬间的燃料饥饿会使阳极电位升高,导致碳氧化反应的发生;系统上采用氢气回流泵或喷射泵等部件可实现尾部氢气循环,是避免燃料饥饿的最有效途径。通过燃料氢气的循环,可提高气体流速,改善水管理;同时燃料循环也相当于提高了反应界面处燃料的化学计量比,有利于减少局部或个别节发生燃料饥饿的可能。
启动/停车工况
启动、停车也是车辆最常见的工况之一。研究发现车用燃料电池由于停车后环境空气的侵入,在启动或停车瞬间阳极侧易形成氢空界面,导致阴极高电位产生,瞬间局部电位可以达到1.5 V以上,引起炭载体氧化。根据美国城市道路工况统计,车辆在目标寿命5500 h 内,启动停车次数累计高达38500次,平均7次/h,若每次启动停车过程是10 s,则阴极暴露1.2 V以上时间可达100 h,而1.5 A/cm2下平均电压衰减率每次为1.5 mV。因此,在新载体材料没有重大突破的现阶段,需要通过系统策略来控制高电位的生成。研究结果表明,启动、停车过程采用系统控制策略后,装有常规膜电极组件 的寿命有了显著的提高,而材料改进的 MEA寿命提高得并不是很明显,由此可见系统控制策略的重要性。此外,碳腐蚀速率与进气速度密切相关,在启动过程中快速进气可以降低高电位停留时间,达到减少炭载体损失的目的。
连续低载或怠速运行
当低载运行或怠速时,燃料电池电压处于较高范围,阴极电位通常在0.85~0.9 V之间,在这个电位下的炭载体腐蚀与铂氧化也会直接导致燃料电池性能衰减。在整个车辆使用寿命周期内,怠速时间可达1000 h,因此怠速状态引起的材料衰减同样不可忽视。利用混合动力控制策略,在低载时通过给二次电池充电,提高电池的总功率输出,也可起到降低电位的目的。美国UTC公司在一专利中阐述了怠速限电位的方法,他们提出通过调小空气量同时循环尾排空气、降低氧浓度的办法,达到抑制电位过高目的。
低温贮存与启动
车辆运行在冬季要受到零下气候考验,由于燃料电池发电是水伴生的电化学反应,在零度以下反复水、冰相变引起的体积变化会对电池材料与结构产生影响。因此,要制定合理的零度以下贮存与启动策略,保证燃料电池在冬季使用的耐久性。低温贮存方面,通过研究电池内存水量对燃料电池材料与部件的影响,研究吹扫电池内残存水的方法,减小冰冻对燃料电池性能的危害,从而提出适宜的保存策略。加热法是低温启动时常采用的方法,可以通过车载蓄电池、催化燃烧氢等方法在启动时提供热量;自启动法是采用一定策略不依赖于外加能量的低温启动过程,这方面研究还在进行中。在启动过程中以低的能量损耗获得快速启动效果是追求的最终目标。
车用燃料电池关键材料
材料创新是取得燃料电池耐久性的最终解决方案。国内外主要从电催化剂及载体、聚合物膜、膜电极组件以及双极板等燃料电池关键材料入手,进行高耐久性材料的研究。
膜电极组件
膜电极组件(MEA)是燃料电池的核心部件,它的设计与制备对燃料电池性能与稳定性起着决定性作用。目前,国际上已经发展了三代MEA技术路线:一是把催化层制备到扩散层上,通常采用丝网印刷方法,其技术已经基本成熟;二是把催化层制备到膜上(Catalyst Coated Membrane, CCM),与第一种方法比较,在一定程度上提高了催化剂的利用率与耐久性;三是有序化的MEA,把催化剂如Pt制备到有序化的纳米结构上,使电极呈有序化结构,有利于降低大电流密度下的传质阻力,进一步提高燃料电池性能,降低催化剂用量。国内车用燃料电池大部分采用的是第一种传统制备方法,第二种方法还处于完善中。然而,要想实现低成本、高性能的目标,有序化的MEA是一个技术发展趋势,3M 公司研制的Pt担载量可降至0.15~0.25 mg/cm2的纳米结构薄膜 (nanostructured thin film, NSTF)MEA显示了较好的性能。
高稳定性催化剂
在高稳定性催化剂研究方面,主要从Pt/C催化剂的改进与新型催化剂研究两方面进行研究与探索。目前采用的Pt/C电催化剂稳定性欠佳,在燃料电池动电位扫描下会产生溶解、聚集、流失等现象,导致活性比表面积减少。
通过对制备方法的改进,进行形貌控制,可有效地提高其活性与稳定性。通过贵金属元素对Pt/C进行修饰,可提高催化剂的稳定性。如以Au cluster修饰Pt纳米粒子,提高了Pt的氧化电势,起到了抗 Pt溶解的作用,经过3万次循环伏安扫描,与Pt/C比较其稳定性有了大幅度提高。此外,加入Pd也可提高Pt的氧还原活性,并改善其抗氧化能力。研究表明,Pt3Pd/C与Pt/C相比较,在循环伏安扫描加速衰减实验中的抗衰减能力得到较大提高。
采用其他过渡金属与Pt形成的二元催化剂Pt-M/C,也是提高催化剂稳定性与降低成本的一个有效途径。利用过渡金属M与Pt之间的电子与几何效应,提高了Pt的稳定性及比活性,同时,降低了贵金属的用量,使催化剂成本也得到大幅度降低。如Pt-Co/C、Pt-Fe/C、Pt-Ni/C等二元催化剂,展示出了较好的活性与稳定性。
Pt-M1-M2/C三元核壳催化剂也是目前研究的热点课题,利用非贵金属为支撑核,表面贵金属为壳的结构,可降低Pt用量,提高质量比活性。如采用欠电位沉积方法制备的Pt-Pd-Co/C单层核壳催化剂总质量比活性是商业催化剂Pt/C的3倍,利用脱合金方法制备的Pt-Cu-Co/C核壳电催化剂,质量比活性可达Pt/C的4倍。催化剂除了需要工况循环下的稳定性以外,抗毒性也非常重要,如得到广泛研究的Pt-Ru/C催化剂具有较好的抗CO性能;对于其他杂质如硫化物、NH3等的抗毒催化剂,目前还处于研究阶段。空气中痕量的SO2,都会导致催化剂中毒,希望研制一种能够降低硫化物电化学氧化电位的非Pt金属与Pt形成的合金催化剂,在保证氧还原活性前提下,SO2能在正常电压范围0.6~0.7 V内就能氧化成SO3,并与电池内的水结合为硫酸,可降低硫化物对燃料电池的危害。总之,Pt基多元催化剂在提高性能、稳定性、抗毒物、降低成本方面均展示出一定的发展潜力,但一些研究成果尚需产品规模的验证,使替代催化剂尽早推向应用。
抗氧化催化剂载体
目前,广泛使用的催化剂载体为Vulcan XC 72碳黑,在燃料电池实际工况下会产生氧化腐蚀,从而导致其担载的贵金属催化剂的流失与聚集,表现为催化剂颗粒长大,活性比表面积减小。因此,需要研制抗氧化催化剂载体。综合近期研究成果,大体归纳为2方面:一是基于原载体材料的改性,二是研制新载体材料。在材料改性方面,可通过添加羰基(=CO)官能团的方法,提高催化剂的分散度,降低其聚集效应,提高稳定性。另外,对碳黑载体进行石墨化处理(如高温2000℃以上处理),可表现出一定程度的高耐腐蚀性。在新型催化剂载体材料方面,主要分为碳材料与金属化合物两大类。碳材料方面,研究人员在碳纳米管、碳纳米球、石墨纳米纤维、富勒烯C60、介孔碳、碳气凝胶等方面进行了有益的尝试。其中碳纳米管载体是研究得比较广泛的一种碳材料,它独特的管状结构和良好的导电性能使其非常适于用作催化剂的载体,而且研究表明,采用Pt/CNTs的稳定性明显好于Pt/C;另外,在碳纳米管中掺杂氮或硼可以进一步提高其稳定性。金属化合物作为催化剂载体材料,也得到越来越多的重视,如以WxCy、氧化铟锡等为代表的金属氧化物与金属碳化物等得到了关注。无论对炭载体材料的改性还是新型载体材料的创新,其技术挑战都来自于在提高抗氧化性的同时不损失其比表面积和降低其电子的传导性,另外低成本也是必须要考虑的因素。目前,满足性能、稳定性、成本三方面要求的催化剂载体,还正在探索之中。
质子膜改进
在车用燃料电池运行过程中,另一关键材料质子交换膜会产生物理或化学衰减,物理衰减主要是由于动态温湿及压力波动导致的膜机械损伤,化学衰减主要来自于反应过程中形成的氢氧自由基对膜结构的损害,这些均导致燃料电池性能不可逆转的衰减。研究人员从全氟磺酸膜的结构改进、全氟磺酸膜的改性、烃类膜及碱性膜等方面入手,寻找高稳定性、低成本膜的解决方案。
与目前采用的Nafion®膜比较,短侧链 (short side chain, SSC)的全氟磺酸膜其磺酸基团密度较高,质子传导率要高于 Nafion®膜,并表现出了良好的耐久性。典型的有美国陶氏 (DOW) 膜,还有Solvay Solexis公司开发的一种与DOW结构相同的Hyflon®Ion (EW=850~870) SSC膜,由于采用简单的合成路径,使成本得到大幅度降低。利用 Hyflon®Ion膜制备的MEA5000 h耐久性试验表明,该种类型的膜没有明显的针孔与膜减薄现象,透氢率也小于 Nafion®112。SSC膜的缺点是比较脆,可采用增强Nafion膜(后面有详细讨论)的思路,制备增强复合SSC膜,以进一步提高其机械性能。
有限的车辆空间使人们更加追求高功率密度的燃料电池,这促使膜趋于薄膜化。为了补偿均质薄膜的强度问题,研究人员研制的增强复合膜可有效地增加膜的机械性能,如采用多孔PTFE为基底浸渍全氟磺酸树脂制成的复合增强膜,在保证质子传导的同时,解决了薄膜的强度问题,同时尺寸稳定性也有大幅度的提高。美国Gore-select™复合膜是这种增强膜的典型代表,国内大连化物所刘富强等也研制成功了低成本、高强度的Nafion/PTFE复合增强膜,采用热台方法制备,结果表明这种复合膜尺寸稳定性明显优于 Nafion®膜,强度也有所提高,增强了抵抗变工况时膜的抗冲击能力,国内正在进行这种膜的小批量试制中。此外,研究人员还探索了多种纳米管增强复合膜等也展现了良好发展前景。
在膜中分散如SiO2、TiO2、杂多酸等无机/有机吸湿材料作为保水剂,储备电化学反应生成水,实现湿度的调节与缓冲,使膜提高了在低湿、高温(约为120℃)下的耐久性。制成的自增湿膜,利用吸湿材料的保水特性,在无外增湿的情况下使燃料电池保持了良好的性能。此外,把无机保水剂磺化再与 Nafion 复合,可以进一步提高膜的吸水率以及提供额外的酸位,使传导质子能力明显增强。通过添加自由基淬灭剂可以一定程度上缓解膜的化学衰减。
烃类膜以其低成本、结构调变性强等特点,一直是质子交换膜发展的重要方向,目前研究的烃类膜主要包括芳香烃类如离子化处理的聚苯撑氧、芳香聚酯、聚苯并咪唑(PBI)、聚酰亚胺(PI)、聚醚砜(PES)、聚醚醚酮(PEEK)等;此外,如咪唑、吡唑、苯并咪唑等含氮杂环类的膜也引起人们的关注。烃类膜与全氟磺酸膜的主要区别在于C-H键与C-F键的差别,C-H键键能(413 kJ/mol)小于C-F键键能(485.6 kJ/mol),导致C-H键较C-F 容易发生化学降解,因此,烃类膜的稳定性成为了实际应用中面临的焦点问题。下一步研究也可以尝试在烃类膜中加入自由基淬灭剂,提高烃类膜寿命,使膜的低成本与寿命问题同时得到解决。
碱性聚合物电解质膜与传统的碱性燃料电池KOH液态电解质不同,由于没有可移动的金属阳离子,因此不会产生碳酸盐沉淀与电解液流失,给车用燃料电池带来了新的契机,近年来得到广泛关注。固态聚合物OH-离子交换膜是碱性环境,与质子交换膜酸性环境相比,材料的腐蚀问题得到缓解;最重要的是碱性环境中的氧还原动力学快于酸性条件,催化剂可采用非贵金属,使燃料电池成本得到降低。目前,研制具有高离子传导性、高稳定性的碱性离子交换膜还存在技术难点,研究者大多采用季胺或季膦型聚合物膜,通过对电解质可溶性溶剂的选择,制备出了带有立体化三相界面的非贵金属催化剂膜电极,但聚合物膜的离子传导性与稳定性还有待于进一步提高。
双极板
双极板材料分为石墨、石墨金属复合及金属3类。纯石墨板是早期采用的双极板材料,现在有些企业还沿用这种材料,但由于其材料与制造成本很高,难于满足商业化的需求,正在被石墨粉与树脂的复合模压板技术取代。以Ballard公司为代表的填充膨胀石墨双极板,采用模压工艺,成本大幅度降低,已经在燃料电池示范车上得到了成功的应用。然而,石墨双极板材料的非致密性,会直接导致燃料电池发电效率的降低和潜在的安全问题;且随着双极板的减薄,给材料的致密性会带来更大的挑战,使比功率密度提高具有局限性;此外,在零度以下运行时,由于石墨板微孔内会有一定的水残存,水的冷冻与解冻会削弱材料的强度。以大连化学物理研究所为代表的石墨金属复合双极板,弥补了单一石墨双极板的不足,表现出了良好的工况适应性,其电堆已经用于国内示范燃料电池汽车与发电装置上。
车用燃料电池由于空间体积的限制,对燃料电池比功率要求越来越高,因此,薄金属双极板成为了研究的热点,GM公司开发的基于金属双极板技术的燃料电池电堆,其比功率已经达到3 kW/L、2 kW/kg。金属双极板主要的技术挑战是要满足导电、耐蚀性与低成本的兼容。研究表明特殊的高合金钢,可以满足燃料电池环境中耐腐蚀性要求,然而界面导电性还不够理想。因此,目前更多的研究集中在不锈钢材料表面改性上,如碳膜、Ti-N、Cr-C、Cr-N膜等均表现出具有良好的性能。金属双极板表面处理层的针孔是双极板材料目前普遍存在的问题。此外,金属阳离子污染导致电池性能下降也值得关注。
结论
寿命是制约车用燃料电池商业化的重要因素,车辆工况运行的复杂性导致了燃料电池的加速衰减,而启动、停车、怠速过程中的高电位和动态操作条件下电位扫描是引起催化剂及载体衰减的主要原因。需要从材料改进与创新、系统控制策略两方面着手制定解决对策。材料方面需要研究高稳定性的电催化剂、抗腐蚀的催化剂载体、抗氧化的质子交换膜、有序化膜电极组件 (MEA)、导电耐腐兼容的金属双极板等,研究人员已经进行了大量工作,取得了一些成果,但还需要一定应用前的试验验证及产品规模的探索。材料问题的解决是一项相对长期的工作,近期可采用控制策略优化等方式,避免燃料电池不利条件的停留时间,以期在现有材料的基础上提高燃料电池寿命,美国联合技术公司(UTC)取得的7000 h寿命是这方面的一个成功范例。控制策略的解决方案,会一定程度增加系统的复杂性,我们期待材料的创新,使系统实现简单—复杂—简单的循环上升过程,最终实现燃料电池汽车商业化的既定目标。
编辑:燃料电池博士
作者 : 衣宝廉,侯明
来源:汽车安全与节能学报《车用燃料电池耐久性的解决策略》
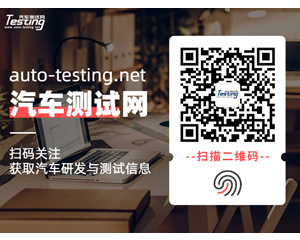
编辑推荐
最新资讯
-
商用车及工程机械行业专场:NVH 及语音音频
2025-08-01 17:12
-
理想i8和重卡对撞测试引争议,东风柳汽发声
2025-08-01 15:52
-
艾德克斯IT-N2100 系列太阳能阵列模拟器
2025-08-01 15:43
-
ITECH重磅发布IT2705直流电源分析仪,重构
2025-08-01 15:34
-
现代汽车新一代混合动力系统:以技术革新引
2025-08-01 15:32